Introduction
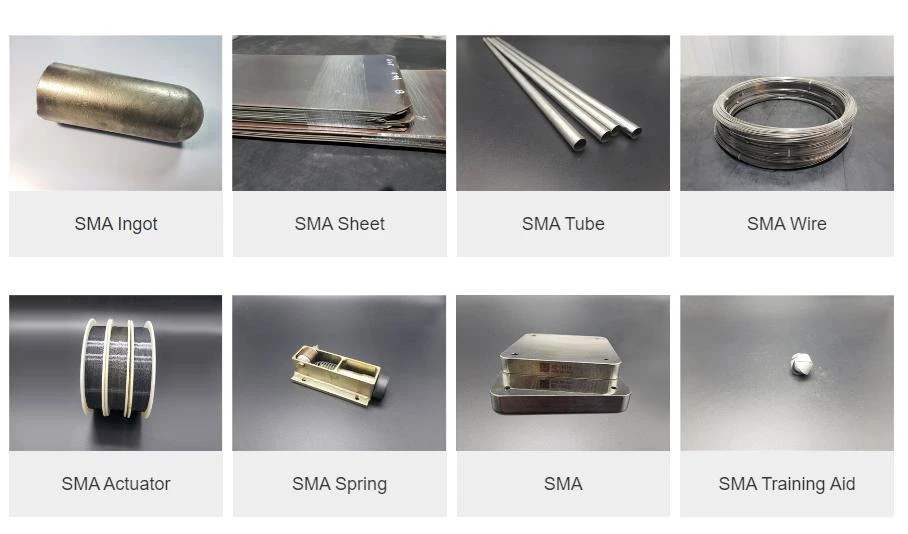
Nickel sheet metal is a highly versatile material that offers a wide range of applications across various industries. From aerospace to electronics, the use of nickel sheet in manufacturing processes has become increasingly popular due to its exceptional properties and characteristics. As a metal, nickel is known for its corrosion resistance, high thermal conductivity, and strength, making it an ideal choice for numerous industrial applications.
The Versatility of Nickel Sheet Metal
The versatility of nickel sheet metal lies in its ability to be easily formed, welded, and machined into complex shapes and structures. This makes it an essential material in the production of components for aircraft, electronic devices, and automotive parts. Its malleability and ductility also enable manufacturers to create intricate designs with precision and accuracy.
Advantages of Using Nickel Sheet in Manufacturing
The advantages of using nickel sheet in manufacturing are abundant. Its resistance to corrosion ensures longevity and durability in harsh environments, while its high thermal conductivity makes it suitable for heat exchangers and other thermal applications. Additionally, the superior electrical conductivity of nickel sheet makes it indispensable in the production of electronic components.
Exploring the Potential of Nickel Sheet Metal
Exploring the potential of nickel sheet metal opens up opportunities for innovation and advancement in various industries. With ongoing research and development, new applications for nickel sheet continue to emerge, further solidifying its position as a valuable material in modern manufacturing processes.
What is Nickel Sheet Metal?
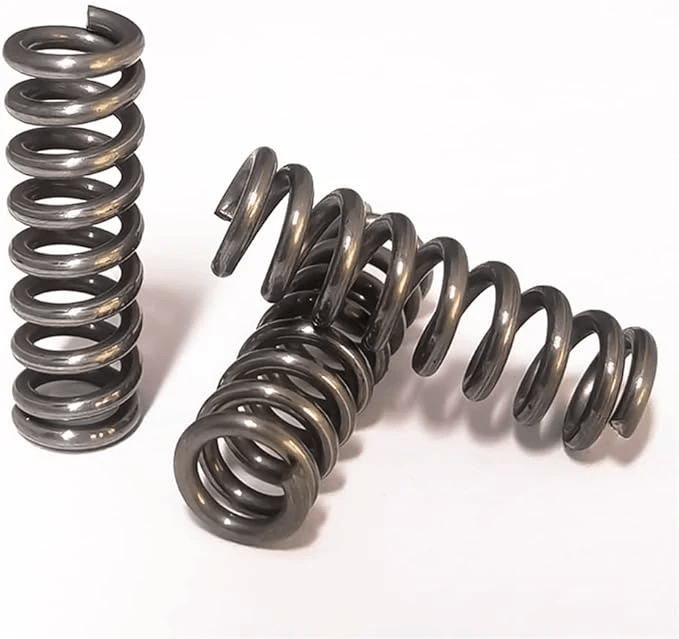
Nickel sheet metal is a versatile material known for its exceptional properties and characteristics. It is highly resistant to corrosion, making it an ideal choice for various industrial applications. Its malleability and ductility also make it easy to work with, allowing manufacturers to create intricate designs and shapes.
Properties and Characteristics of Nickel Sheet
Nickel sheet metal boasts excellent thermal conductivity, making it suitable for use in high-temperature environments. It also exhibits superb electrical conductivity, making it a popular choice in the electronics industry. Additionally, nickel sheet has a high melting point and is highly resistant to oxidation, ensuring its durability even in harsh conditions.
Industrial Applications of Nickel Sheet
Nickel sheet metal finds extensive use in industries such as aerospace, automotive, and electronics manufacturing. It is commonly used in the production of aircraft components, electronic connectors, battery casings, and automotive exhaust systems due to its exceptional strength and resistance to corrosion.
Advantages of Nickel Sheet in Manufacturing Processes
The use of nickel sheet in manufacturing processes offers several advantages. Its ability to withstand extreme temperatures and harsh chemicals makes it an ideal material for demanding applications. Furthermore, its longevity and low maintenance requirements contribute to cost savings for manufacturers.
Nickel Sheet in Manufacturing
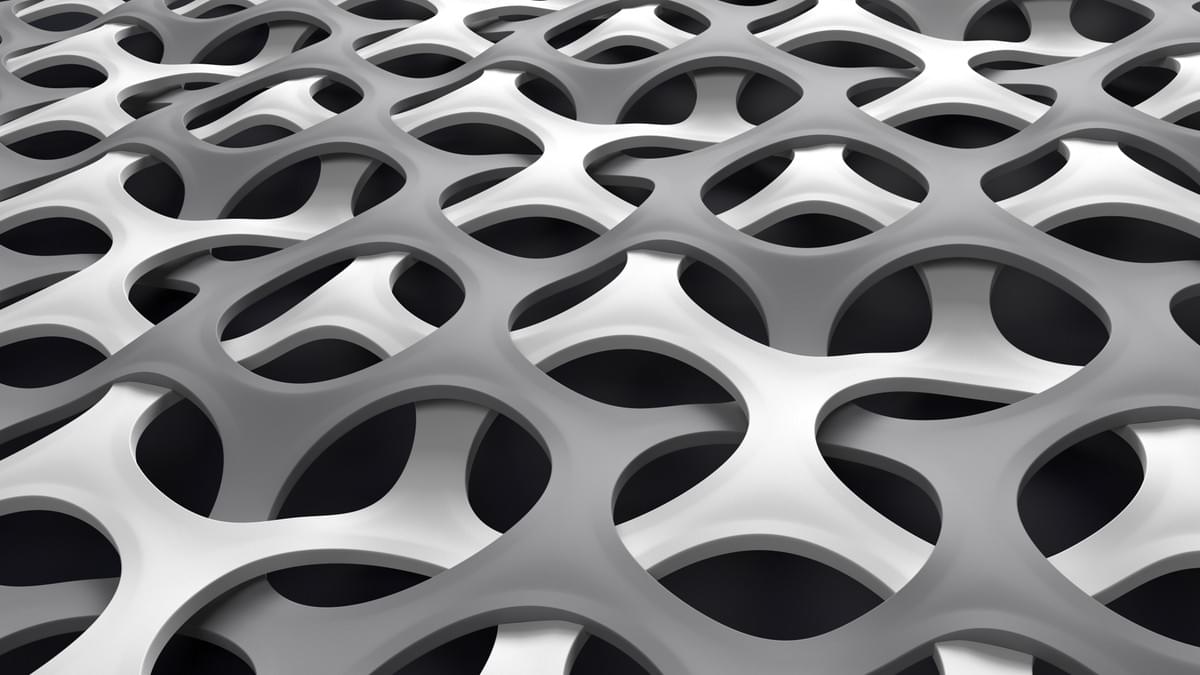
Nickel sheet metal is a crucial component in the aerospace industry, where its exceptional strength and resistance to corrosion make it an ideal material for aircraft components. From structural parts to engine components, nickel sheet is widely used in the production of aircraft, ensuring safety and reliability in the skies.
Nickel Sheet in Aerospace Industry
The aerospace industry heavily relies on nickel sheet metal for its high-temperature performance and ability to withstand extreme conditions. Whether it's for manufacturing engine components, such as turbine blades and exhaust systems, or for producing structural parts like landing gear and fasteners, nickel sheet plays a vital role in ensuring the safety and efficiency of aircraft.
Nickel sheet metal is also essential in the electronics manufacturing industry, where its high conductivity and corrosion resistance make it a valuable material for producing electronic components. From connectors and lead frames to battery casings and heat sinks, nickel sheet plays a crucial role in ensuring the reliability and longevity of electronic devices. Its ability to be easily formed into intricate shapes also makes it ideal for creating custom components that meet the specific requirements of electronic applications.
Nickel Sheet in Electronics Manufacturing
In electronics manufacturing, nickel sheet metal is used for various applications such as battery casings, connectors, and lead frames due to its excellent electrical conductivity and corrosion resistance. Its ability to be easily plated with other metals also makes it a popular choice for electronic components.
In addition to its use in electronic components, nickel sheet metal is also commonly used for shielding purposes in electronics manufacturing. Due to its high magnetic permeability, nickel sheets are ideal for creating protective barriers that can block electromagnetic interference and prevent signal distortion. This makes them essential for ensuring the proper functioning of sensitive electronic devices in various applications.
Nickel Sheet in Automotive Manufacturing
Nickel sheet metal is also used in the production of automotive heat exchangers and radiator tubes due to its excellent thermal conductivity and resistance to corrosion. This ensures that the vehicle's cooling system operates efficiently and effectively, preventing overheating and potential engine damage. Additionally, nickel sheet is utilized in the manufacturing of electrical connectors and wiring harnesses, where its high electrical conductivity and durability are crucial for maintaining reliable electrical systems in vehicles. As automotive technology continues to advance, the demand for nickel sheet metal in manufacturing is expected to grow, reinforcing its significance in the automotive industry.
Nickel Alloy and Its Uses
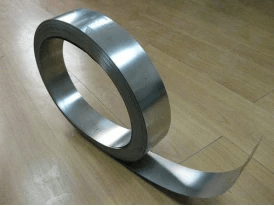
Nickel alloys are widely utilized in various industries due to their exceptional properties and versatility. From aerospace to medical equipment, nickel alloys play a vital role in enhancing product performance and durability.
Diverse Applications of Nickel Alloys
Nickel alloys are extensively used in the aerospace industry for manufacturing aircraft components, such as turbine engines, due to their high-temperature resistance and corrosion protection. In the medical field, nickel alloys are used in orthopedic implants and surgical instruments for their biocompatibility and strength.
Unique Properties of Nickel Alloys
Nickel alloys exhibit remarkable characteristics, including excellent thermal conductivity, high tensile strength, and resistance to oxidation and corrosion. These properties make nickel alloys ideal for applications that require durability under extreme conditions.
Importance of Nickel Alloys in Various Industries
The significance of nickel alloys is evident across a wide range of industries, including chemical processing, marine engineering, and electronics manufacturing. With their ability to withstand harsh environments and maintain structural integrity, nickel alloys contribute significantly to the reliability and performance of diverse products.
By understanding the diverse applications and unique properties of nickel alloys, it becomes clear why they are indispensable in various industries. Trusted manufacturers play a crucial role in ensuring the quality and reliability of nickel sheet products for continued innovation and advancement.
Reliability of Nickel Sheet Manufacturers
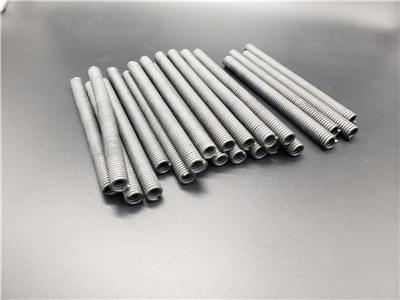
When it comes to sourcing high-quality nickel sheet metal, it's crucial to partner with leading manufacturers known for their expertise and reliability. These manufacturers have a proven track record of producing top-notch nickel sheet products that meet industry standards and specifications, making them the go-to choice for businesses in various sectors.
Leading Manufacturers of Nickel Sheet
Nickel sheet manufacturers such as ABC Metals and XYZ Alloys have established themselves as industry leaders in the production of nickel sheet/plate. Their state-of-the-art facilities and cutting-edge technology enable them to consistently deliver premium quality nickel sheet products that cater to the diverse needs of their clients across aerospace, electronics, automotive, and other industries.
High-Quality Standards in Nickel Sheet Production
These reputable manufacturers adhere to stringent quality control measures throughout the production process, ensuring that each nickel sheet meets the highest standards for strength, durability, and corrosion resistance. By employing advanced manufacturing techniques and rigorous testing protocols, they guarantee that their nickel sheet products are reliable and perform optimally in various applications.
Furthermore, these trusted nickel sheet suppliers offer personalized customer service and technical support to assist clients in choosing the right nickel sheet for their specific needs. Whether it's for aerospace, automotive, or chemical processing applications, their knowledgeable staff can provide expert guidance and recommendations to ensure that customers get the most suitable product for their requirements. This level of personalized attention sets them apart from other suppliers and ensures a seamless and satisfying experience for their clients.
Benefits of Partnering with Trusted Nickel Sheet Suppliers
Businesses can reap numerous benefits by partnering with trusted nickel sheet suppliers. Not only do they gain access to a wide range of high-quality nickel sheet options tailored to their specific requirements, but they also benefit from expert technical support, timely delivery, and competitive pricing. This strategic partnership empowers companies to enhance their manufacturing processes while maintaining a competitive edge in the market.
In addition to the benefits mentioned above, partnering with trusted nickel sheet suppliers also allows businesses to stay updated on the latest industry trends and advancements. With their finger on the pulse of the market, these suppliers can provide valuable insights and recommendations for optimizing production processes and improving product quality. By staying informed and leveraging the expertise of their suppliers, companies can stay ahead of the curve and adapt to changing market demands more effectively.
The Future of Nickel Sheet Metal
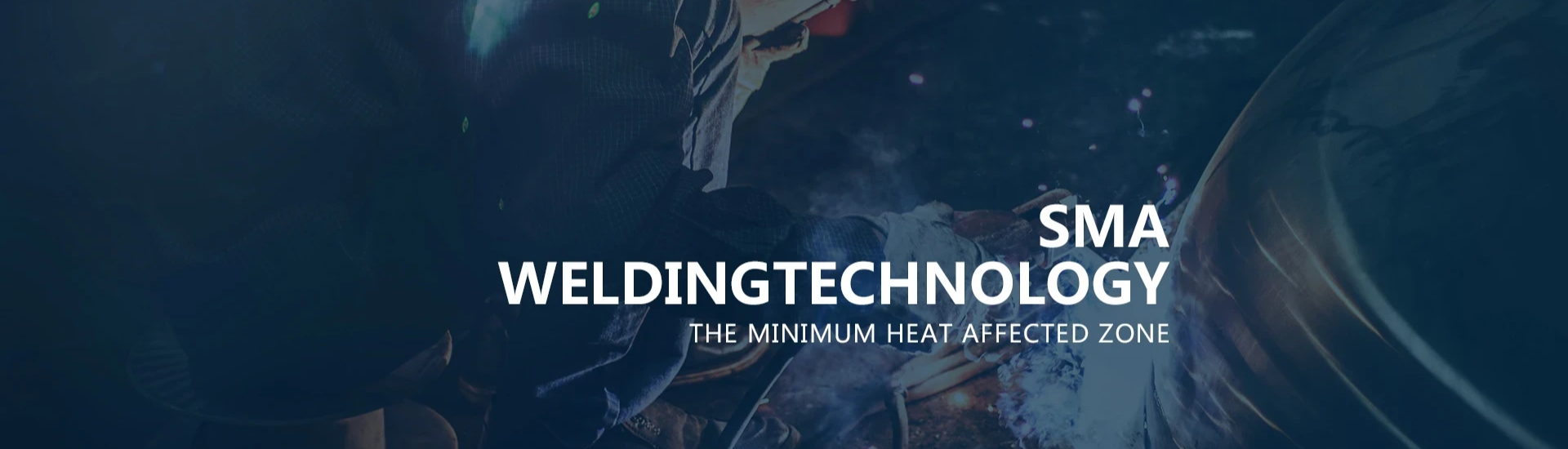
Innovations in Nickel Sheet Technology
Innovations in nickel sheet technology are revolutionizing manufacturing processes across industries. Advanced techniques such as electroforming and superplastic forming are enhancing the precision and durability of nickel sheet metal, making it an indispensable material for cutting-edge applications.
In addition to enhancing precision and durability, innovations in nickel sheet technology are also leading to improvements in surface finish quality. This allows for smoother and more aesthetically pleasing final products, making nickel sheet metal an attractive choice for a wide range of consumer goods and high-end applications. As a result, manufacturers are increasingly turning to nickel sheet technology to meet the growing demand for superior quality products in the market.
Emerging Trends in Nickel Sheet Applications
The emerging trend of incorporating nickel sheet in 3D printing is opening up new possibilities for complex and customized designs in aerospace, automotive, and electronics manufacturing. Additionally, the use of nickel sheet as a substrate for flexible electronics is gaining traction due to its exceptional conductivity and resilience.
Furthermore, the use of nickel sheet in battery manufacturing is gaining attention due to its high energy density and long-term durability. This trend is particularly significant in the growing electric vehicle market, where the demand for reliable and efficient battery technology is on the rise. As a result, nickel sheet suppliers are investing in research and development to optimize the material's performance in battery applications, driving innovation in energy storage solutions.
Sustainable Practices in Nickel Sheet Manufacturing
Sustainable practices in nickel sheet manufacturing are becoming increasingly important as environmental awareness grows. Manufacturers are investing in eco-friendly production methods and recycling initiatives to minimize waste and reduce the carbon footprint of nickel sheet metal production.
As environmental regulations become more stringent, manufacturers are also exploring new ways to reduce the environmental impact of nickel sheet production. This includes investing in energy-efficient technologies and implementing sustainable sourcing practices for raw materials. By adopting these measures, manufacturers can not only reduce their carbon footprint but also improve the overall sustainability of their operations.
Conclusion
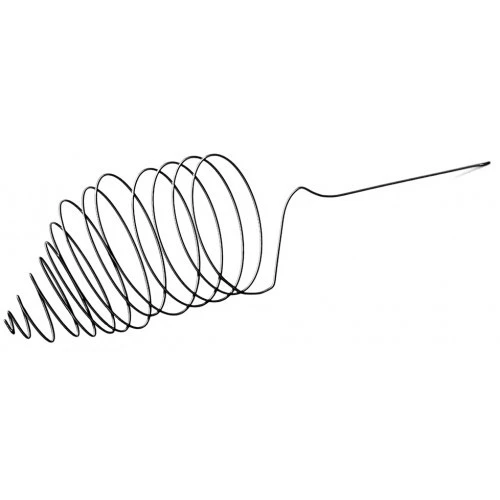
Maximizing Potential with Nickel Sheet Metal
Nickel sheet metal offers endless possibilities for innovation and excellence in manufacturing. Its exceptional properties make it an ideal material for various applications, from aerospace to electronics and automotive industries. By maximizing the potential of nickel sheet metal, manufacturers can achieve unparalleled precision and durability in their products.
Unleashing the Power of Nickel Alloy
The use of nickel alloy opens up a world of opportunities in diverse industrial sectors. With its unique properties and exceptional resilience, nickel alloy is indispensable in creating high-performance components for critical applications. Unleashing the power of nickel alloy enables manufacturers to push the boundaries of what is achievable, leading to groundbreaking advancements in technology and engineering.
Embracing the Versatility of Nickel Sheet
As a trusted resource for countless industries, nickel sheet has proven its worth as a reliable and adaptable material. Embracing the versatility of nickel sheet allows manufacturers to explore new frontiers in design and functionality, ensuring that their products meet the highest standards of quality and performance.