Introduction
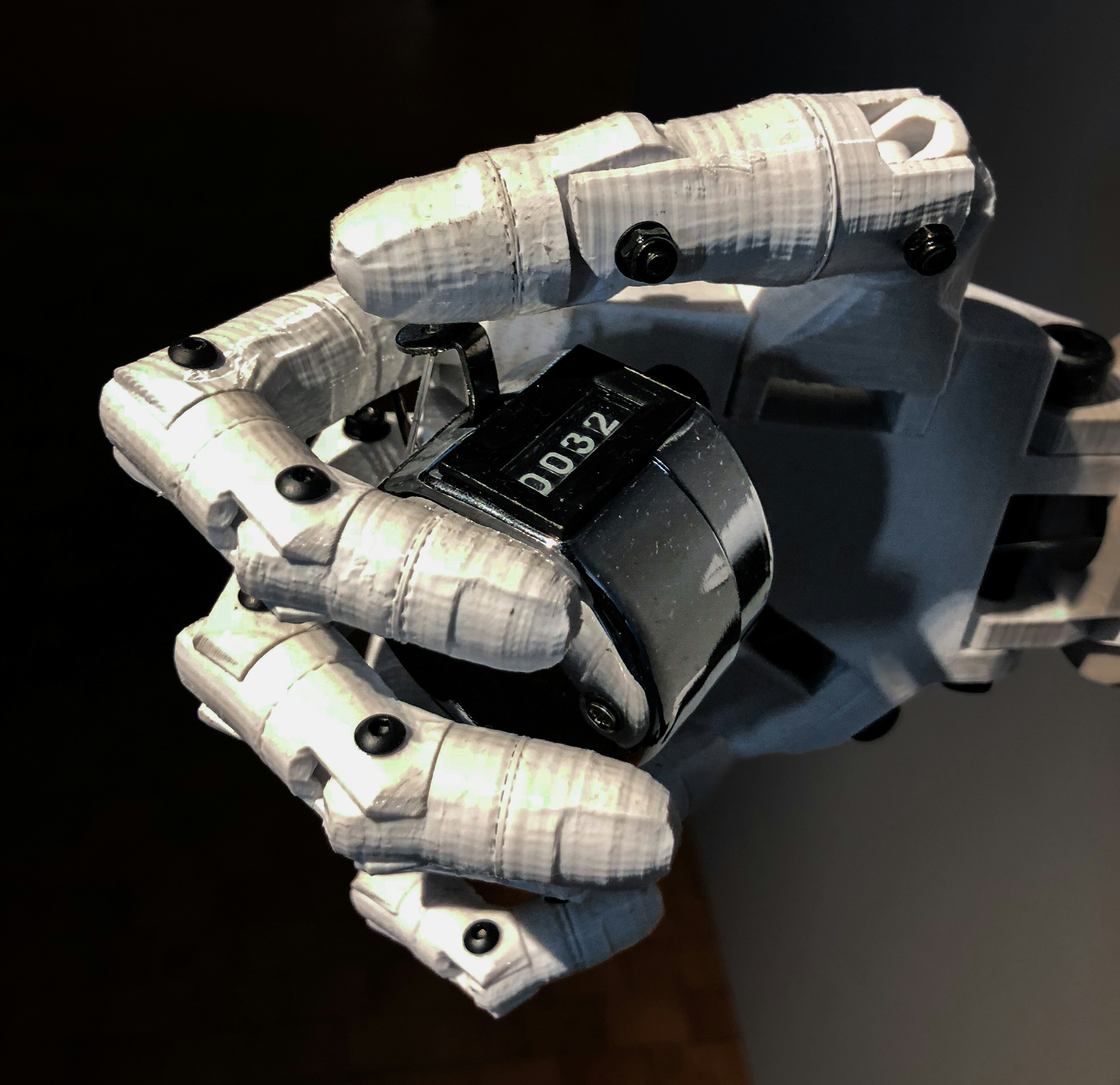
Are you familiar with the revolutionary technology of muscle wire actuators? These innovative systems are changing the game in the field of robotics and automation. By harnessing the unique properties of shape memory alloys like Nitinol, muscle wire actuators are providing unprecedented levels of precision and control in a wide range of applications.
Understanding Muscle Wire Actuator Systems
Muscle wire actuators, also known as shape memory alloy actuators, are devices that convert electrical energy into mechanical motion through the use of a special type of wire composed of shape memory alloys like Nitinol. When subjected to an electrical current, these wires undergo a phase change that allows them to contract or expand, enabling precise and powerful movements.
Muscle wire actuators offer several advantages over traditional actuators, including their compact size and lightweight nature. This makes them ideal for applications where space is limited or weight is a concern, such as in robotics and aerospace. Additionally, muscle wire actuators are known for their high force-to-weight ratio, allowing them to generate a significant amount of force relative to their size. This makes them well-suited for tasks that require precise and powerful movements, such as in medical devices or industrial automation.
Benefits of Muscle Wire Actuators
The benefits of muscle wire actuators are numerous and impressive. Their compact size, lightweight nature, and high energy density make them ideal for applications where space is limited or weight is a concern. Additionally, their ability to produce large forces with minimal power input makes them highly efficient and cost-effective for various industries.
In addition, muscle wire actuators can operate in harsh environments, such as extreme temperatures or high levels of vibration, without losing performance. This durability and resilience make them suitable for a wide range of industrial applications, including aerospace, automotive, and robotics. Furthermore, their precise control and responsiveness allow for intricate movements and fine adjustments, making them valuable in fields such as medical devices and prosthetics.
Applications of Muscle Wire Actuators
From robotics to aerospace, muscle wire actuators have found diverse applications across different sectors. Whether it's in the development of advanced prosthetics, precision positioning systems, or even intricate surgical instruments, these actuators have proven their versatility and reliability time and time again. In the field of robotics, muscle wire actuators are being used to create more lifelike movements in robots, allowing for greater dexterity and flexibility in their actions. This has opened up new possibilities for robotic applications in industries such as manufacturing and healthcare.
Getting to Know Muscle Wire Actuators
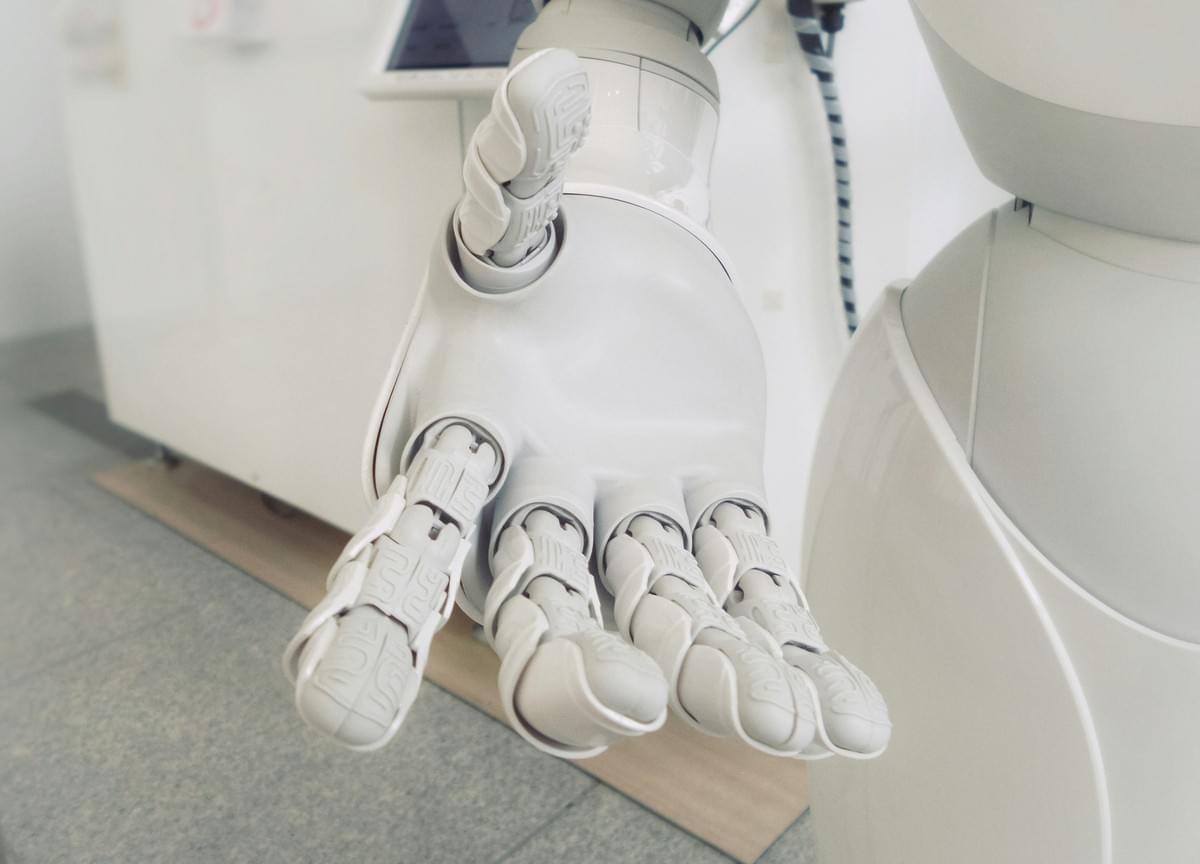
What is a Muscle Wire Actuator?
A muscle wire actuator, also known as a shape memory alloy actuator, is a type of actuator that uses the properties of shape memory alloys to produce motion. When an electrical current is passed through the wire, it contracts, allowing it to be used in various applications such as robotics and medical devices.
Muscle wire actuators have the advantage of being lightweight and compact, making them ideal for small-scale applications where space is limited. Their ability to produce high force and large displacements relative to their size makes them a popular choice in robotics, where precise and powerful motion is required. Additionally, muscle wire actuators are known for their durability and low maintenance requirements, making them a cost-effective solution for long-term use in various industries.
Advantages of Muscle Wire Actuators
One of the main advantages of muscle wire actuators is their ability to produce large forces and displacements in a compact space. They are also lightweight and have low power consumption, making them ideal for portable devices and applications where weight and energy efficiency are crucial. Additionally, muscle wires offer precise control over motion, making them suitable for intricate tasks.
In addition, muscle wire actuators are highly durable and can withstand a high number of cycles without experiencing wear and tear. This makes them ideal for applications that require repetitive movements over an extended period of time, such as in robotics or medical devices. Their reliability and long lifespan make muscle wire actuators a cost-effective choice for industries looking for low-maintenance solutions.
Limitations of Muscle Wire Actuators
Despite their many benefits, muscle wire actuators do have some limitations. They can be relatively slow compared to other types of actuators, which may not be suitable for high-speed applications. Additionally, they can be sensitive to temperature changes, which may affect their performance in certain environments.
Furthermore, muscle wire actuators may also have limited force output compared to other types of actuators, which could restrict their use in applications requiring higher levels of force. This limitation may make them unsuitable for certain industrial or heavy-duty tasks where greater force is necessary for operation. In such cases, alternative actuator options with higher force capabilities may be more appropriate.
Implementing Muscle Wire Actuator Systems

Design Considerations for Muscle Wire Actuators
When designing muscle wire actuators, it's crucial to consider factors such as the required force, stroke length, and response time. The shape memory alloy used in muscle wires allows for compact designs and efficient energy usage. Additionally, the temperature at which the actuator will operate must be taken into account to ensure optimal performance.
Furthermore, the durability and longevity of the muscle wire actuators should be considered in the design process. This includes assessing the potential wear and tear that the actuator may experience over time, as well as any environmental factors that could impact its lifespan. By prioritizing durability, engineers can ensure that the actuators will have a longer operational life and require less frequent maintenance.
Integration of Muscle Wires for Robotics
Muscle wires are increasingly being integrated into robotics due to their lightweight and high force-to-weight ratio. Their ability to mimic human muscle movements makes them ideal for applications such as prosthetics and exoskeletons. When integrating muscle wires into robotics, precise control systems must be implemented to ensure accurate and repeatable movements.
Additionally, the flexibility of muscle wires allows for a wide range of motion, making them suitable for intricate and delicate tasks in robotics. This makes them particularly useful in applications such as surgical robots, where precise and controlled movements are essential. The ability of muscle wires to contract and expand quickly also enables rapid response times in robotic systems, enhancing their overall performance and efficiency.
Choosing the Right Size Wire for Actuators
The size of the wire used in muscle wire actuators depends on the specific application and desired performance characteristics. Thinner wires provide faster response times but may have lower force output, while thicker wires can generate greater force but may have slower response times. It's essential to carefully select the right size wire based on the requirements of the actuator system.
Once you have determined the required force output and response time for your muscle wire actuator, it's important to consider the environmental factors that may impact the performance of the wire. Factors such as temperature, humidity, and vibration can all affect the behavior of muscle wire actuators. Thicker wires may be more suitable for applications in harsh environments where greater force output is needed, while thinner wires may be better suited for applications that require a faster response time in more controlled environments.
Now that we've covered implementing muscle wire actuator systems, let's delve into optimizing their performance for various applications.
Optimizing Performance of Muscle Wire Actuators
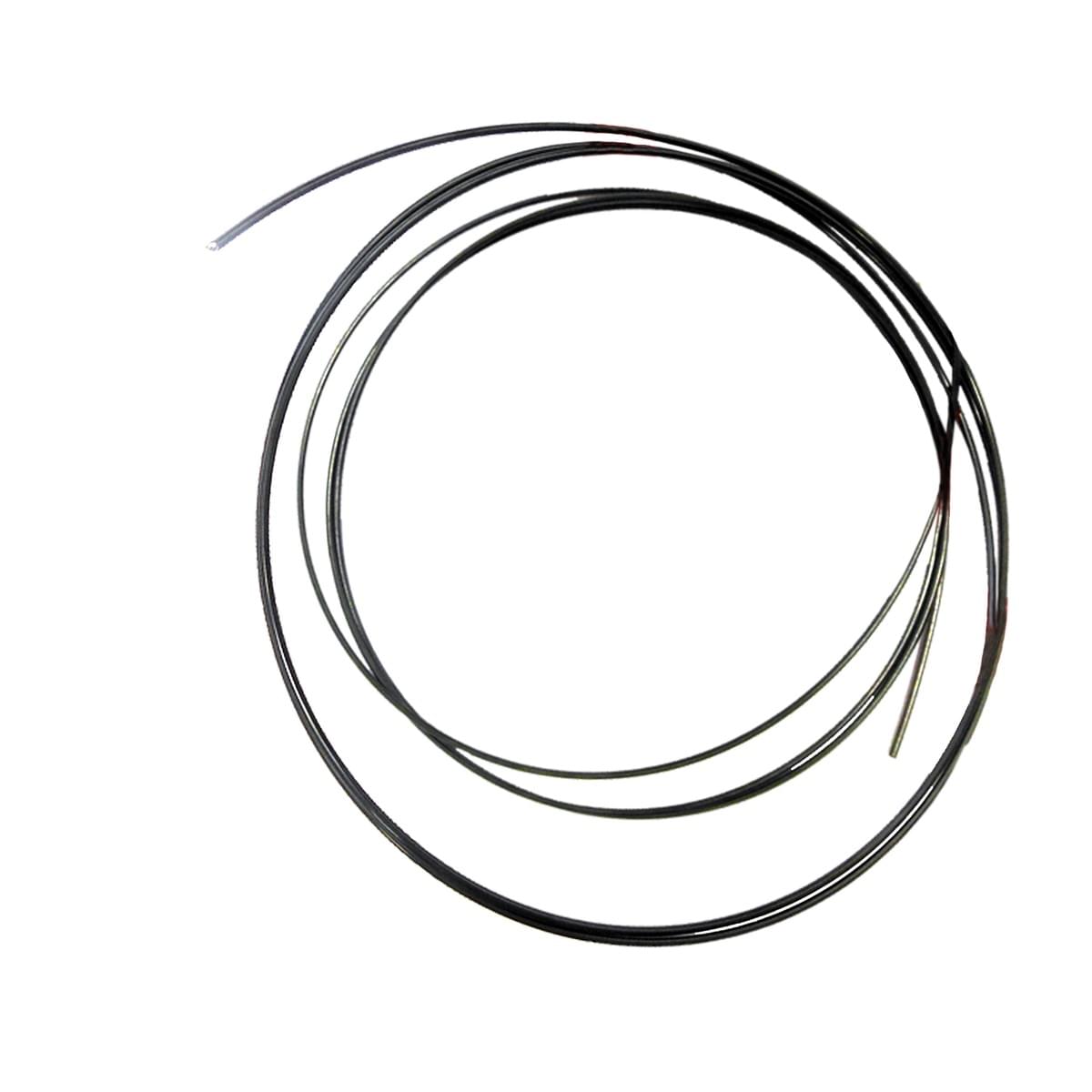
When it comes to optimizing the performance of muscle wire actuators, one key component to consider is the use of shape memory alloy. This unique material allows muscle wires to return to their original shape after being deformed, providing a reliable and repeatable actuation process for various applications. By harnessing the properties of shape memory alloy, muscle wire actuators can deliver precise and efficient movement, making them an ideal choice for robotics and automation.
Shape Memory Alloy in Muscle Wire Actuators
The use of shape memory alloy in muscle wire actuators is essential for achieving consistent and reliable performance. This innovative material enables muscle wires to undergo reversible phase transformations, allowing them to recover their original shape when heated after being deformed. This unique property makes shape memory alloy a valuable component in muscle wire actuators, ensuring precise and repeatable motion control in various robotic systems.
Additionally, the use of nitinol actuator wire has been shown to enhance the efficiency of muscle wire actuators. Nitinol, a type of shape memory alloy, offers superior flexibility and durability, allowing for smoother and more precise motion control in robotic systems. This advanced material also provides a higher level of responsiveness, enabling muscle wires to quickly adapt to changing environmental conditions and perform with increased accuracy.
Enhancing Efficiency with Nitinol Actuator Wire
Nitinol actuator wire, a type of shape memory alloy composed of nickel and titanium, has been widely used to enhance the efficiency of muscle wire actuators. With its exceptional flexibility and superelasticity, Nitinol actuator wire allows for seamless integration into complex robotic designs, providing high force output and rapid response times. By leveraging the unique properties of Nitinol actuator wire, engineers can optimize the performance of muscle wire actuators for a wide range of applications.
Furthermore, the use of Nitinol actuator wire can also help in overcoming common challenges in implementation, such as space constraints and weight limitations. Its compact size and lightweight nature make it an ideal choice for applications where size and weight are critical factors. This allows engineers to design more efficient and agile robotic systems without compromising on performance or durability.
Overcoming Common Challenges in Implementation
While muscle wire actuators offer numerous advantages, there are common challenges that engineers may encounter during implementation. These challenges include heat dissipation issues, mechanical fatigue, and control system complexities. However, by employing advanced thermal management techniques, fatigue-resistant materials, and sophisticated control algorithms, these challenges can be effectively addressed to maximize the performance and longevity of muscle wire actuator systems.
To further address heat dissipation issues, engineers can explore the use of passive and active cooling techniques to effectively manage the temperature of muscle wire actuators. Passive cooling methods such as heat sinks and thermal insulation can help dissipate excess heat, while active cooling methods like fans or liquid cooling systems can provide additional support in maintaining optimal operating temperatures. By implementing a combination of these techniques, engineers can ensure that heat-related challenges are mitigated, leading to improved performance and reliability of muscle wire actuator systems.
Now that we've explored how shape memory alloy and Nitinol actuator wire play crucial roles in optimizing the performance of muscle wire actuators, let's delve into best practices for maintenance and care to ensure their long-term reliability.
Best Practices for Maintenance and Care
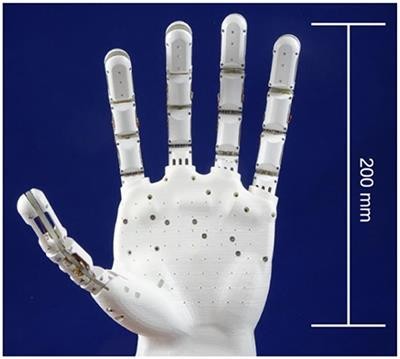
Extending the Lifespan of Muscle Wire Actuators
To extend the lifespan of muscle wire actuators, regular maintenance is key. Keep the actuator clean and free from debris to prevent corrosion and ensure smooth operation. Additionally, regularly inspect the wires for any signs of wear or damage to address issues early on.
Preventing Wear and Tear
Preventing wear and tear on muscle wire actuators involves proper handling and usage. Avoid subjecting the actuators to excessive force or overloading them beyond their capacity. Implementing protective measures such as using appropriate lubricants can also help reduce friction and minimize wear on the wires.
Troubleshooting Common Issues
When troubleshooting common issues with muscle wire actuators, start by checking for loose connections or misalignments in the actuator system. It's also important to verify that the power source is functioning correctly and that there are no obstructions hindering the actuator's movement. In case of persistent issues, consult a professional for further assistance.
Conclusion
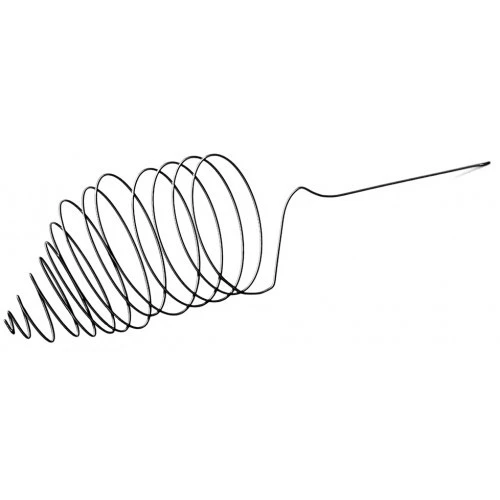
Harnessing the Potential of Muscle Wire Actuators
Muscle wire actuators have revolutionized the field of robotics with their unique ability to mimic human muscle movement. These actuators have opened up a world of possibilities in terms of creating more lifelike and efficient robotic systems, making them an invaluable tool for various industries.
The potential for muscle wire actuators is still largely untapped, and ongoing research and development in this field promise even more exciting innovations. As engineers continue to refine the technology, we can expect to see advancements in terms of strength, speed, and precision. These improvements will not only enhance the capabilities of robotic systems but also expand their applications across a wide range of industries, from manufacturing to healthcare.
Future Innovations in Muscle Wire Technology
As technology continues to advance, so does the potential for muscle wire actuators. The future holds exciting innovations in the development of more advanced and versatile muscle wire technology, paving the way for even greater applications across industries such as healthcare, aerospace, and beyond. One exciting area of innovation is the miniaturization of muscle wire actuators, allowing for their integration into smaller devices and equipment. This opens up possibilities for use in wearable medical devices and compact aerospace components, enhancing their functionality and performance.
Leveraging GEE SMA's Expertise in Nitinol Alloys
For those looking to harness the full potential of muscle wire actuators, leveraging GEE SMA's expertise in nitinol alloys is crucial. With their extensive knowledge and experience in shape memory alloy technology, GEE SMA is at the forefront of developing cutting-edge solutions for optimizing muscle wire actuator performance.