Introduction
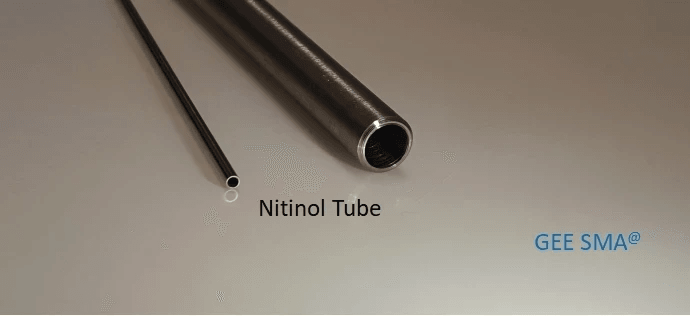
Nitinol, a fascinating alloy, comprises nearly equal parts nickel and titanium. This unique combination allows it to remember its original shape and return to it when heated—a property known as shape memory. Exploring Nitinol's composition and structure reveals its remarkable resilience and flexibility, making it an ideal material for various applications in healthcare, engineering, and aerospace industries. From medical devices to robotics, Nitinol has proven invaluable across diverse sectors.
What is Nitinol Composed Of?
Manufactured using a precise process that involves melting and cooling the nickel-titanium combination, Nitinol's composition results in a crystalline structure that allows it to exhibit superelasticity and shape memory. This distinctive blend of elements gives Nitinol exceptional properties, making it highly sought after in the manufacturing industry for its versatility and reliability.
Nitinol comprises approximately equal parts nickel and titanium, giving it unique properties. Combining these two metals results in a material that can return to its original shape after deforming, making it ideal for various applications. Additionally, the crystalline structure of Nitinol allows it to exhibit superelasticity, meaning it can undergo significant deformation and still return to its original shape without permanent damage.
Exploring Nitinol's Composition and Structure
The unique atomic arrangement of Nitinol contributes to its malleability, allowing for intricate shaping into various forms such as tubing, sheets, and tubes. Its crystalline structure enables it to withstand extreme conditions while maintaining its integrity - a crucial factor in industries where durability is paramount.
Nitinol's unique composition and structure make it an ideal material for medical devices and implants. Its malleability allows for the creation of intricate shapes and designs tailored to fit specific anatomical needs. Additionally, Nitinol's ability to withstand extreme conditions makes it a reliable choice for devices that need to function within the human body, where durability and integrity are essential. From stents to orthodontic wires, Nitinol is crucial in advancing medical technology and improving patient outcomes.
Applications of Nitinol in Various Industries
Nitinol is a remarkable material with exceptional properties that have made it indispensable across various industries. Its unique characteristics have led to various applications, from medical to aerospace engineering.
- Medical: Nitinol is utilized in medical tubing for minimally invasive procedures and orthodontic sheets for dental applications.
- Engineering: This versatile material is employed in critical engineering systems, such as tubes, for demanding applications.
- Aerospace: Nitinol's shape memory and superelasticity properties make it ideal for aerospace components like actuators and sensors. It excels in withstanding extreme conditions and high stress levels, proving invaluable in this industry.
Nitinol's exceptional qualities position it as a cornerstone material for innovative solutions across multiple sectors.
Nitinol's Composition
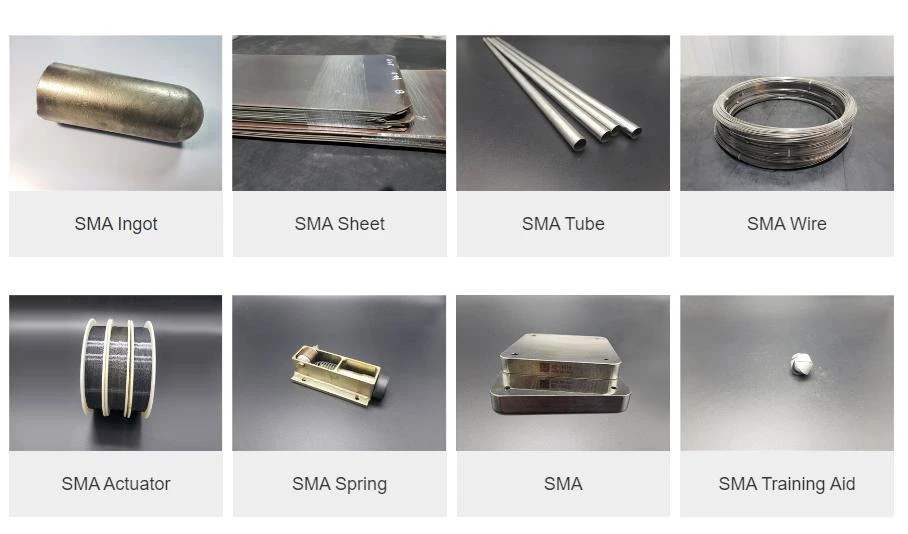
Nitinol, a shape memory alloy, comprises nearly equal parts nickel and titanium, giving it the unique ability to return to its original shape after deforming. This combination of metals allows Nitinol to exhibit superelasticity and shape memory properties, making it highly versatile in various applications.
Nitinol's Unique Combination of Nickel and Titanium
The unique combination of nickel and titanium in Nitinol gives it remarkable properties. When heated or cooled, this alloy undergoes a phase transition, allowing it to remember its original shape and return to it when the temperature changes. This makes Nitinol an ideal material for medical devices, robotics, aerospace engineering, and many other industries.
Manufacturing Nitinol involves carefully controlling the ratio of nickel to titanium and the temperature and timing of the phase transition. This precision ensures that the resulting alloy exhibits the desired shape memory and superelasticity. Additionally, Nitinol can be fabricated using various methods such as vacuum arc melting, induction skull melting, and powder metallurgy, each offering unique advantages for specific applications.
Manufacturing Process of Nitinol
The manufacturing process of Nitinol involves carefully controlled heating and cooling to achieve the desired phase transformation properties. The alloy is typically produced through a series of complex steps, including melting, casting, hot working, cold working, and heat treatment, to achieve the specific mechanical properties required for different applications.
After the initial melting and casting process, the Nitinol alloy undergoes hot work to shape further and refine its structure. This involves heating the material to high temperatures and using mechanical processes such as forging or extrusion to achieve the desired shape and grain structure. The hot working stage is crucial in determining the final mechanical properties of Nitinol, as it helps to align the crystalline structure and improve its strength and flexibility.
Properties and Characteristics of Nitinol
Nitinol is a remarkable material with a unique combination of properties. Its superelasticity, shape memory effect, biocompatibility, corrosion resistance, and high damping capacity make it highly versatile for various applications.
Nitinol's exceptional characteristics lend themselves to numerous industries. Specifically, it excels in:
- Medical Devices: Its biocompatibility and shape memory effect make it ideal for stents, which are easily inserted and expanded to their original shape, minimizing patient discomfort and reducing the need for multiple surgeries.
- Orthodontics: Nitinol sheets are commonly used in orthodontic treatments due to their flexibility and ability to exert gentle, consistent force on teeth.
- Engineering and Aerospace: Nitinol tubing is used in these fields due to its strength, corrosion resistance, and shape memory properties, which make it suitable for demanding environments.
Combining these factors positions Nitinol as a premier material for innovative product development across diverse sectors.
Nitinol Products
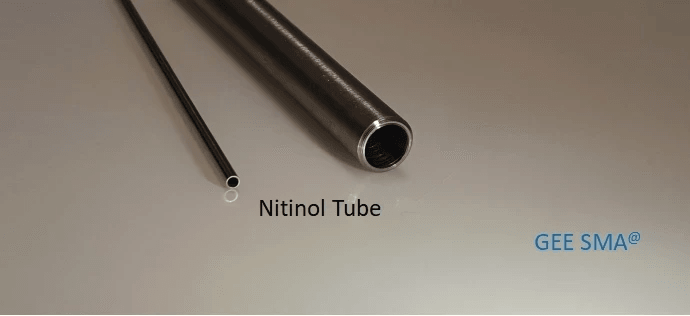
Nitinol Tubing for Medical Devices
Nitinol tubing is a crucial component in the medical industry. It is used in applications such as stents, guide wires, and catheters. Its unique shape memory and superelasticity properties make it ideal for minimally invasive surgical procedures, ensuring patient comfort and safety.
Furthermore, nitinol tubing offers excellent biocompatibility, reducing the risk of adverse reactions when implanted in the body. This is crucial for medical devices that remain in the patient long-term, such as stents, to keep arteries open. Nitinol's ability to withstand the body's harsh environment while maintaining its shape and function is a testament to its reliability in medical applications.
Nitinol Sheet for Orthodontic Applications
Nitinol sheet is widely utilized in orthodontics for its flexibility and biocompatibility, making it perfect for braces and dental wires. Its ability to exert continuous forces over long periods allows for more efficient teeth alignment and reduced patient discomfort.
Nitinol sheet's unique combination of flexibility and biocompatibility has revolutionized orthodontics. By using Nitinol for braces and dental wires, orthodontists can provide more efficient tooth alignment with reduced discomfort for patients. This innovative material allows continuous forces to be exerted over long periods, resulting in a more effective and comfortable orthodontic experience.
Nitinol Tube in Engineering and Aerospace
In the engineering and aerospace sectors, nitinol tubes are prized for their high strength-to-weight ratio, corrosion resistance, and shape memory capabilities. Due to their reliability under extreme conditions, these tubes are used in various applications such as actuators, sensors, and deployable structures.
By incorporating nitinol tubing into medical devices, orthodontic treatments, engineering projects, and aerospace technology advancements, the material's superior performance can be assured.
Nitinol Manufacturers
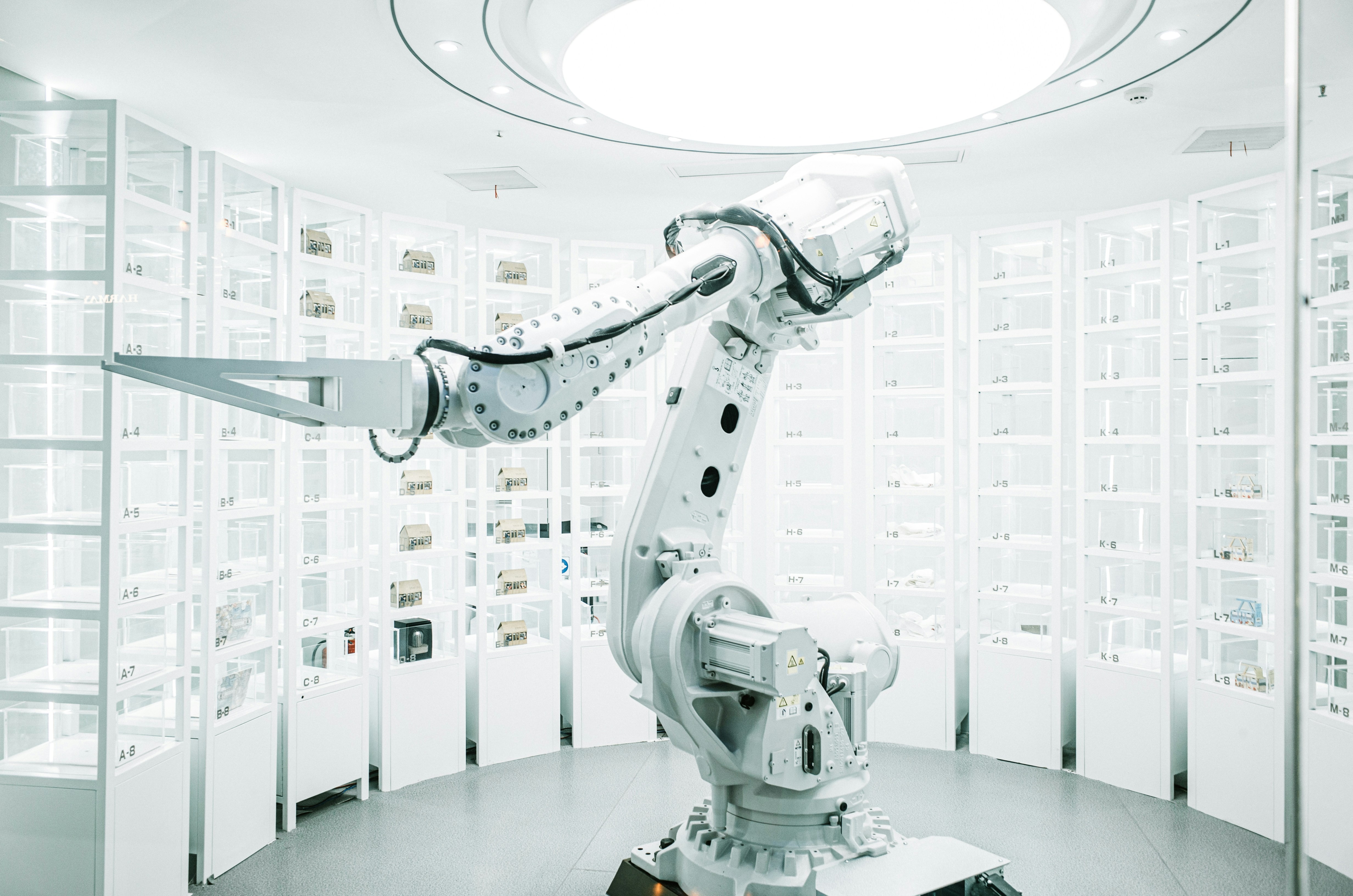
Several leading companies have established strong reputations in the industry as nitinol manufacturers. These companies have invested heavily in research and development to produce high-quality Nitinol products for various applications. They have also developed innovative manufacturing processes to ensure their Nitinol materials' consistent quality and performance.
Leading Companies in Nitinol Manufacturing
Some top players in the Nitinol manufacturing industry include Confluent Medical Technologies, Fort Wayne Metals, and Memry Corporation. These companies are known for their expertise in producing Nitinol tubing, sheets, and tubes that meet the stringent requirements of medical devices, orthodontics, engineering, and aerospace industries. Their commitment to quality and innovation has made them preferred suppliers for many businesses worldwide.
Furthermore, these leading companies in Nitinol manufacturing constantly invest in research and development to stay ahead of the curve. They are always looking for ways to improve their products and processes, whether through new alloy compositions, advanced manufacturing techniques, or enhanced quality control measures. This dedication to continuous improvement ensures that they remain at the forefront of the industry and continue to provide cutting-edge solutions for their customers.
Nitinol Tubes from Reputable Suppliers
Nitinol tubes are essential for numerous industries, and selecting a reputable supplier is crucial for accessing high-quality materials. These suppliers source Nitinol from trusted manufacturers and offer tailored solutions for diverse customer needs.
- Reliable Nitinol Sourcing: Reputable suppliers partner with established manufacturers to ensure consistent material quality.
- Customized Solutions: These suppliers provide Nitinol tubes in various sizes, shapes, and finishes to match specific application requirements.
- Industry Expertise: Suppliers have a deep understanding of Nitinol properties and offer valuable guidance on material selection and application optimization.
- Advanced Processing: Innovative techniques like Nitinol laser cutting enable precise and intricate component creation.
By collaborating with a reputable Nitinol tube supplier, businesses can harness the full potential of this remarkable material and gain a competitive edge in their respective markets.
Innovations in Nitinol Laser Cutting
Innovations in Nitinol laser cutting have revolutionized how this shape memory alloy is processed into precision components. Advanced laser cutting techniques allow manufacturers to create intricate designs and complex geometries with exceptional accuracy and speed. This has opened up new possibilities for using Nitinol in various industries requiring intricate components, such as medical implants, robotics, and aerospace applications.
By partnering with leading manufacturers and suppliers who specialize in producing high-quality Nitinol products using advanced techniques like laser cutting, businesses can unlock the full potential of this remarkable material across a wide range of industries.
Nitinol's Uses
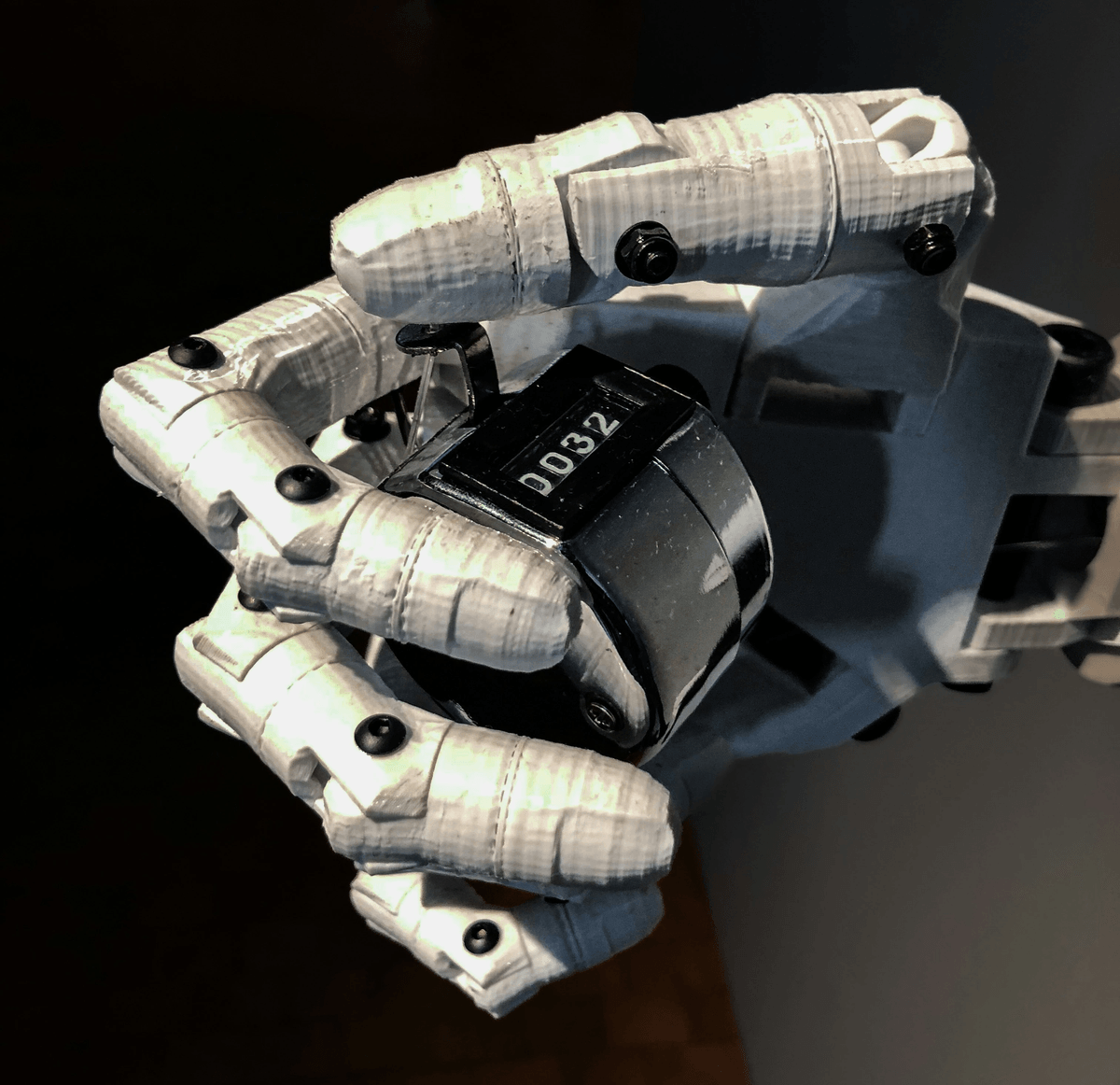
Nitinol's versatility extends to printing, with Qinghe's Waterborne Polyurethane Inks used in various nitinol applications. These inks are specifically formulated to adhere to nitinol tubing and sheets, providing a durable and long-lasting finish crucial for medical and industrial purposes.
Nitinol plays a vital role in the development of prosthetics and biomedical devices. Its unique properties, such as shape memory and superelasticity, make it an ideal material for creating implants, stents, and other medical devices that require flexibility and resilience within the human body.
Nitinol's remarkable properties are leveraged for intricate procedures in robotics and endovascular surgery. Nitinol tubes are used in robotic surgical instruments for their ability to bend and flex without losing their original shape, while they are also employed in endovascular stents for their self-expanding nature within blood vessels.
By seamlessly incorporating these keywords into your content, you can optimize your article for search engines while providing valuable information about the uses of nitinol products.
Future Developments in Nitinol Technology
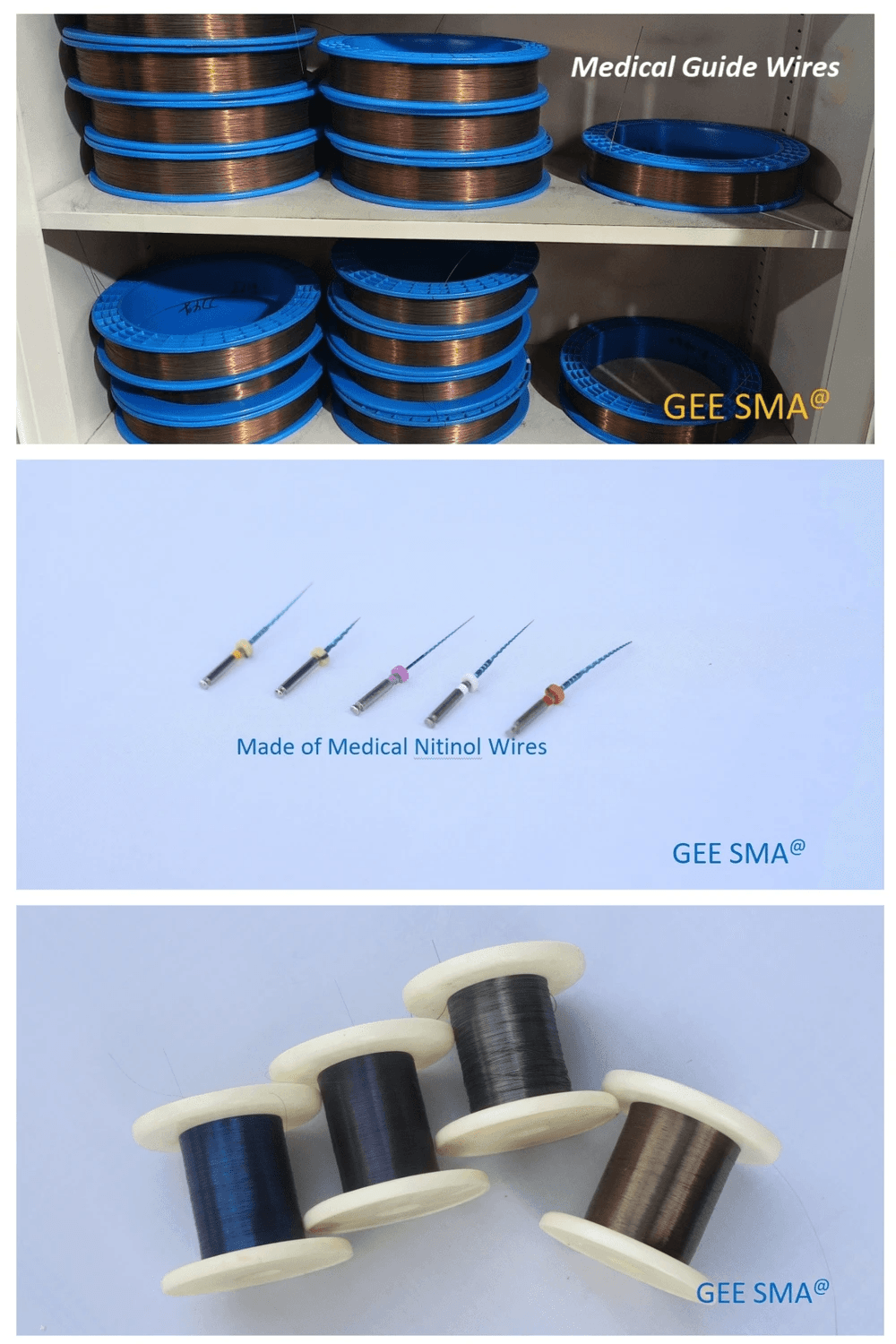
Nitinol has a promising future in technology, with ongoing research and development focused on enhancing its properties and applications. Its impact in various industries, from healthcare to aerospace, is undeniable, showcasing its versatility and reliability. As Nitinol continues to evolve, it will be essential to explore its potential for new products and innovations.
The future of Nitinol technology looks bright, with advancements expected in manufacturing processes to improve efficiency and reduce costs. Research into new compositions and structures aims to enhance Nitinol's properties for more diverse applications, ensuring it remains at the forefront of material science innovation.
The development of Nitinol technology is also expected to lead to breakthroughs in medical devices and implants. Improved manufacturing processes allow medical device manufacturers to produce more cost-effective and efficient Nitinol-based products, leading to better patient outcomes and reduced healthcare costs. Additionally, research into new compositions and structures could create advanced Nitinol implants with enhanced biocompatibility and durability, further expanding its applications in the medical field.
Nitinol's Impact on Various Industries
Nitinol, a remarkable alloy of nickel and titanium, has proven to be a game-changer across multiple industries. Its unique properties have revolutionized the healthcare, engineering, and aerospace sectors.
Nitinol's impact can be seen in the following key areas:
- Healthcare: This material has enabled the development of innovative medical devices like stents and guidewires, facilitating minimally invasive procedures and improving patient outcomes.
- Engineering: Nitinol's shape memory and superelasticity have led to the creation of self-expanding fasteners and actuators, enhancing the efficiency and performance of mechanical systems.
- Aerospace: The alloy's lightweight yet durable nature has found applications in aircraft components and satellite mechanisms, pushing the boundaries of aerospace technology.
As research continues to uncover new possibilities, Nitinol's influence is poised to expand even further, shaping the future of these industries and beyond.
Exploring the Versatility of Nitinol Products
The versatility of Nitinol products is evident in their widespread use across different sectors. From intricate laser-cut tubes for medical devices to robust sheets for orthodontic treatments, Nitinol's adaptability makes it valuable for various applications. As manufacturers continue to innovate with Nitinol products, their potential uses will only expand further.
Remember that the future developments in Nitinol technology are exciting prospects that will undoubtedly shape how we approach materials science across different industries!