Introduction
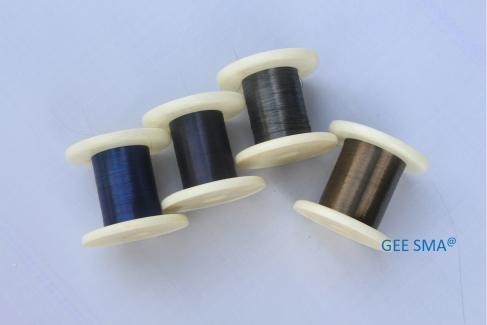
In engineering, the use of NiTiNb wires has become increasingly crucial. These nitinol wires are known for their unique properties and applications in various industries. As a leader in nitinol shape memory alloys, GEE SMA has been at the forefront of producing high-quality NiTiNb wires that have revolutionized the field of engineering.
Understanding Heat-Activated Prestressing
NiTiNb wires are often used in heat-activated prestressing, which allows for controlled deformation and recovery. This technique is essential in engineering, as it helps improve the strength and durability of structures and components.
Importance of NiTiNb Wires in Engineering
NiTiNb wires are a type of metal alloy wire valued for their unique properties, which make them highly desirable for various engineering applications.
Here are some of the critical benefits of NiTiNb wires:
- Exceptional Flexibility: NiTiNb wires can be bent and deformed significantly without breaking, making them ideal for applications requiring intricate shapes or tight spaces.
- Shape Memory Properties: These wires can be "trained" to remember a specific shape and return to it upon exposure to a certain temperature or external stimulus. This property makes them useful for applications like orthodontic braces and self-deploying stents.
- Superelasticity: NiTiNb wires exhibit superior elasticity, allowing them to recover from large deformations without permanent damage. This makes them ideal for applications requiring components that can withstand significant stress or impact.
NiTiNb wires offer a compelling combination of flexibility, shape memory, and superelasticity, making them a highly sought-after material for demanding engineering applications across various industries.
GEE SMA: Leader in Nitinol Shape Memory Alloys
As one of the leading nitinol wire manufacturers and suppliers, GEE SMA has provided top-notch materials to industries worldwide. Their expertise in producing high-quality NiTiNb rings and other nitinol products has solidified their reputation as an industry leader.
Exploring NiTiNb Wires

NiTiNb Wires are known for their exceptional properties and characteristics, making them highly versatile in various industries. These wires comprise nickel, titanium, and niobium, offering unique shape memory and superelasticity. With excellent corrosion resistance and biocompatibility, NiTiNb Wires are the top choice for medical devices, aerospace components, and automotive applications.
Properties and Characteristics of NiTiNb Wires
NiTiNb Wires exhibit remarkable properties such as shape memory effect, superelasticity, and high damping capacity. Their unique ability to return to a predetermined shape after deformation makes them ideal for minimally invasive surgical tools and orthodontic archwires. Additionally, their biocompatibility allows for safe use in medical implants without causing adverse reactions in the body.
In addition to their use in medical applications, NiTiNb wires also find their way into various other industries. Their unique combination of properties makes them ideal for aerospace, automotive, and robotics use. For example, their superelasticity allows them to withstand extreme forces and vibrations, making them suitable for use in aircraft components and automotive parts. Furthermore, their high damping capacity makes them valuable in reducing noise and vibrations in robotics and machinery.
Applications in Various Industries
Due to their diverse applications, nitinol wire manufacturers supply NiTiNb Wires to a wide range of industries. These wires are extensively used in medical devices like stents, guidewires, and endoscopic equipment. In the aerospace industry, they contribute to lightweight actuators and vibration control systems. Moreover, automotive engineers utilize NiTiNb Wires for precise control systems in engines and transmissions.
NiTiNb Wires are also utilized in the construction industry for their shape memory properties, making them ideal for innovative building materials. These wires can be integrated into concrete structures to provide self-healing capabilities, reducing maintenance costs and increasing the lifespan of infrastructure. The unique combination of flexibility and strength makes NiTiNb Wires a valuable asset in developing innovative construction solutions.
Advantages of Using NiTiNb Wires
NiTiNb wires offer a compelling combination of properties that make them valuable in various engineering applications.
- Exceptional Flexibility and Patient Comfort: NiTiNb wires are incredibly flexible, allowing for intricate designs in medical devices. This flexibility enables minimally invasive procedures, improving patient comfort and recovery times.
- High Fatigue Resistance for Durability: These wires boast exceptional fatigue resistance. This translates to long-lasting performance in aerospace components that endure constant stress, ensuring reliability and safety in demanding environments.
- Cost-Effective Choice: NiTiNb wires balance performance and affordability, making them an attractive option for various engineering applications.
- Excellent Biocompatibility for Medical Devices: NiTiNb wires excel in biocompatibility beyond their mechanical properties. This means they are well-tolerated by the human body, minimizing the risk of adverse reactions and ensuring patient safety in medical implants and instruments.
- Corrosion Resistance for Long-Term Use: NiTiNb wires also demonstrate impressive corrosion resistance. This translates to reliable performance in long-term implants and surgical instruments, providing medical professionals and patients peace of mind.
NiTiNb wires stand out for their unique combination of flexibility, strength, biocompatibility, and cost-effectiveness. These qualities make them a versatile material for applications across various engineering disciplines, particularly in the medical and aerospace fields.
Heat Activation Process
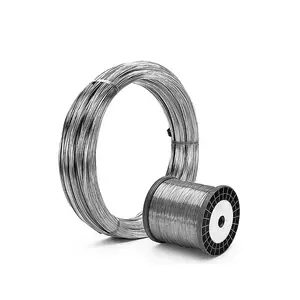
NiTiNb Wires, known as nitinol wires, are renowned for their unique heat-activated properties. When subjected to a specific temperature, these wires showcase remarkable shape memory and superelasticity. This phenomenon is rooted in the science of martensitic phase transformation, where the material's crystalline structure undergoes reversible changes upon heating or cooling.
The Science Behind Heat Activation
The principles of solid-state phase transformation govern the heat activation of NiTiNb Wires. At lower temperatures, the wire retains its deformed shape due to the presence of the martensite phase. After heating above its transition temperature, it reverts to its original austenite phase, restoring its pre-deformation shape. This unique behavior makes NiTiNb Wires ideal for engineering applications requiring precise control over material properties.
Best Practices for Activating NiTiNb Wires
Adhering to best practices when activating NiTiNb Wires is crucial to ensuring optimal performance. This involves carefully calibrating the heating process to achieve the desired transformation temperature without causing structural damage or degradation. Additionally, it's essential to employ accurate temperature monitoring and control mechanisms to guarantee consistent and reliable activation across all wire components.
Factors Affecting Heat Activation
NiTiNb wires, known for their unique shape memory properties, are crucial components in various engineering applications. However, achieving consistent performance and reliability from these wires requires understanding the factors influencing their heat activation process.
Here's a breakdown of the key factors affecting NiTiNb wire heat activation:
- Compositional Variations: Slight changes in the alloy's composition can significantly impact its activation temperature.
- Surface Finish Quality: The wire's surface finish quality can influence heat transfer and activation consistency.
- Thermal Treatment History: The wire's prior heat treatment plays a role in determining its activation behavior.
- External Conditions: Ambient temperature and mechanical stress during activation can also affect the wire's response.
By mastering the science behind heat activation and carefully considering these influencing factors, engineers can unlock the full potential of NiTiNb wires and ensure their reliable performance in diverse industrial settings.
Prestressing Techniques
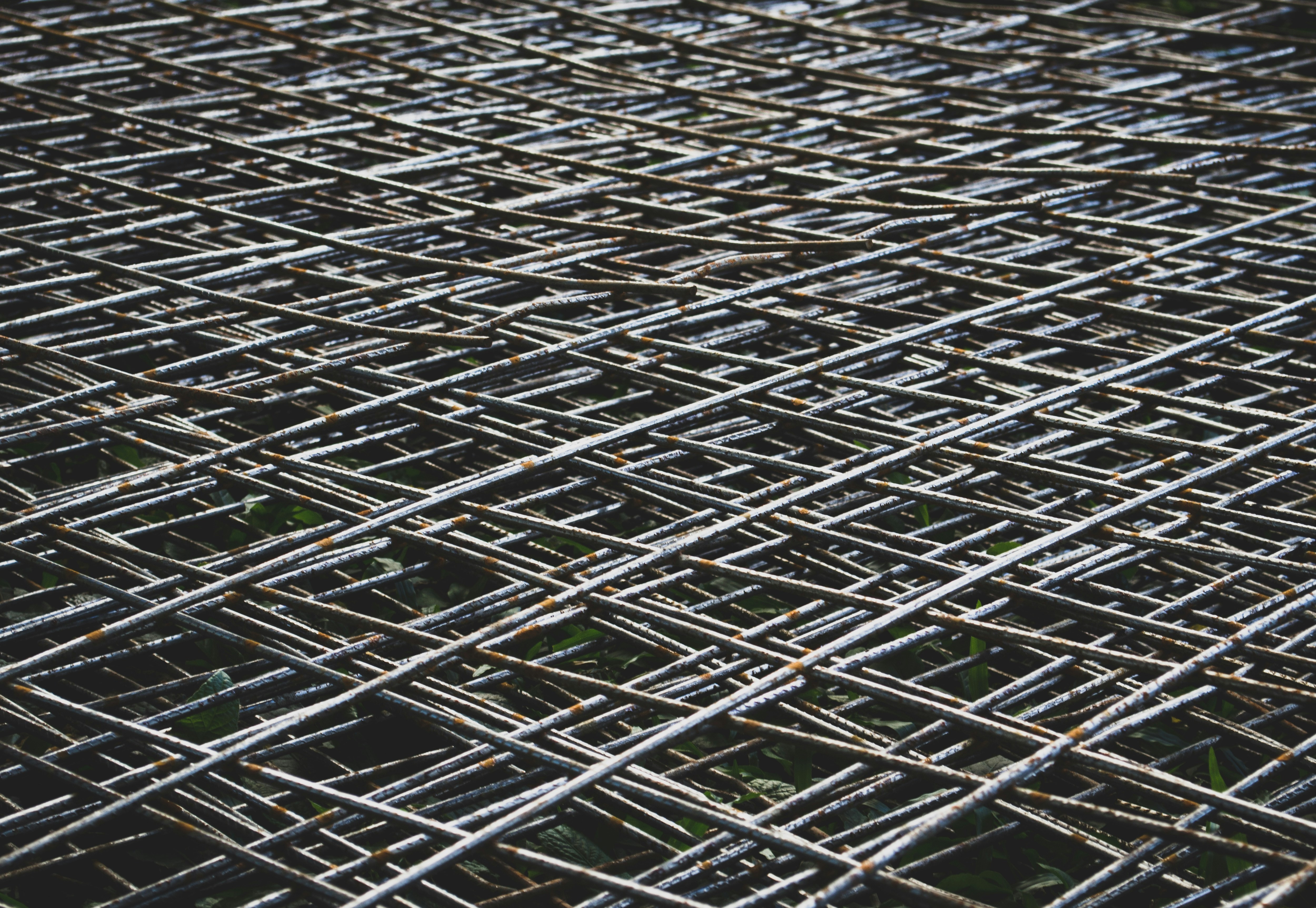
NiTiNb wires are renowned for their unique ability to return to their original shape after deforming, making them ideal for prestressing applications. Methods such as pre-tensioning and post-tensioning are commonly employed to maximize the material's capabilities and ensure structural integrity in effective prestressing.
Methods for Effective Prestressing
Pre-tensioning involves applying a load to the NiTiNb wires before casting concrete, allowing them to counteract the tensile stresses that occur when the concrete is subjected to external forces. On the other hand, post-tensioning involves inserting the NiTiNb wires into ducts within the concrete structure and then tensioning them after the concrete has hardened, providing additional strength and flexibility.
Importance of Proper Prestressing
Proper prestressing is crucial in ensuring that NiTiNb wires effectively enhance the structural performance of various applications. By carefully controlling the amount of stress applied during prestressing, engineers can optimize the material's shape memory effect and its ability to withstand dynamic loads, ultimately improving safety and durability in engineering projects.
GEE SMA's Quality Prestressing Solutions
As one of the leading nitinol wire manufacturers and suppliers, GEE SMA offers high-quality NiTiNb wires designed explicitly for prestressing applications. Focusing on precision engineering and advanced manufacturing techniques, GEE SMA provides tailored solutions that meet industry standards while offering competitive nitinol sheet prices and superior performance in various industries.
Working with NiTiNb Wires
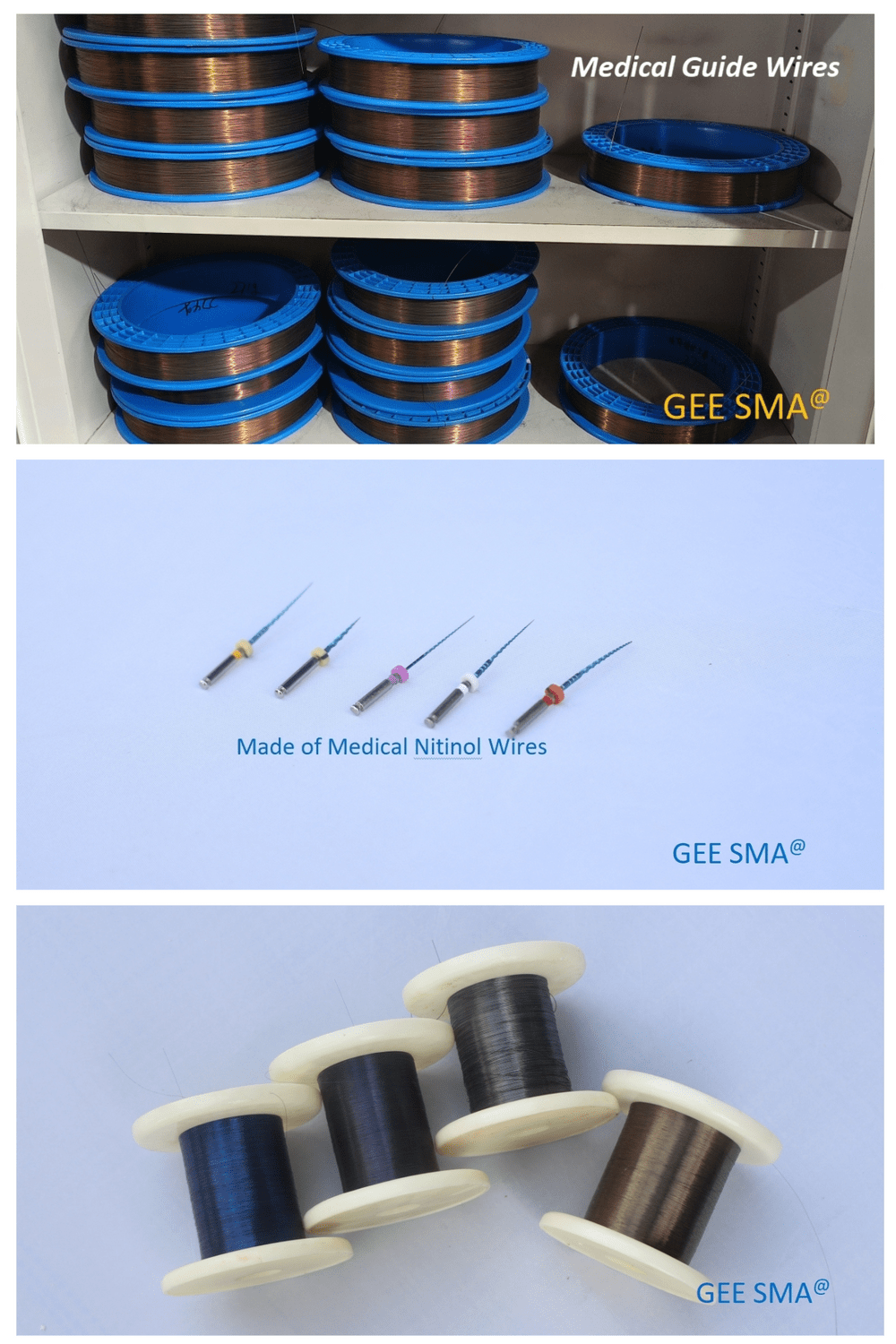
NiTiNb wires are incredibly versatile and can be used in various applications. When handling NiTiNb wires, wearing protective gloves is essential to prevent any potential injuries from sharp edges. Also, NiTiNb wires should always be stored in a dry and cool environment to prevent oxidation or corrosion.
Tips for Handling NiTiNb Wires
When working with NiTiNb wires, using the right tools for cutting and shaping is essential. Ensure the tools are designed to work with nitinol materials to avoid damaging the wires. Handling NiTiNb wires with care is also crucial, as they can be delicate and easily deformed if mishandled.
Common Mistakes to Avoid
One common mistake when working with NiTiNb wires is using excessive force during bending or shaping, which can lead to structural damage. Another mistake is not properly securing the wire during processing, which can result in uneven stress distribution and compromised performance. It's essential to avoid these mistakes to ensure the integrity of the NiTiNb wires.
GEE SMA's Expertise in NiTiNb Wire Production
As one of the leading nitinol wire manufacturers, GEE SMA has extensive expertise in producing high-quality NiTiNb wires. With state-of-the-art manufacturing facilities and a team of experienced professionals, GEE SMA ensures that its NiTiNb wires meet the highest industry standards for quality and performance.
By following these tips for handling NiTiNb wires and avoiding common mistakes, you can ensure that your nitinol materials are used effectively without compromising their properties.
Industry Standards and Innovations
As the demand for advanced materials grows, industry standards for NiTiNb wires continue evolving. Nitinol wire manufacturers and suppliers constantly refine their production processes to meet the highest quality standards and ensure consistent application performance. The industry is focused on enhancing the mechanical properties, corrosion resistance, and biocompatibility of NiTiNb wires to expand their use in diverse industries.
Current Industry Standards for NiTiNb Wires
The current industry standards for NiTiNb wires encompass various specifications related to material composition, mechanical properties, manufacturing processes, and quality control measures. These standards are essential for ensuring the reliability and safety of NiTiNb wires in critical applications such as medical devices, aerospace components, and automotive systems. Nitinol wire manufacturers adhere to these standards to deliver products that meet or exceed their customers' requirements.
Recent Developments and Innovations
Recent developments in nitinol wire technology have led to significant innovations in producing NiTiNb wires. Advanced manufacturing techniques like laser cutting and shape setting have enabled nitinol wire suppliers to create intricate designs with precise dimensional control. Furthermore, ongoing research into new alloy compositions and surface treatments has expanded the capabilities of NiTiNb wires, opening up opportunities for novel applications in emerging industries.
GEE SMA's Commitment to Industry Standards
GEE SMA is dedicated to upholding the highest industry standards for NiTiNb wires through its state-of-the-art manufacturing facilities and rigorous quality assurance protocols. As a leading nitinol wire manufacturer, GEE SMA prioritizes continuous improvement and innovation to meet the evolving needs of its customers across various sectors. By investing in research and development, GEE SMA remains at the forefront of advancements in nitinol materials while maintaining a steadfast commitment to industry best practices.
Future Trends in NiTiNb Wire Applications
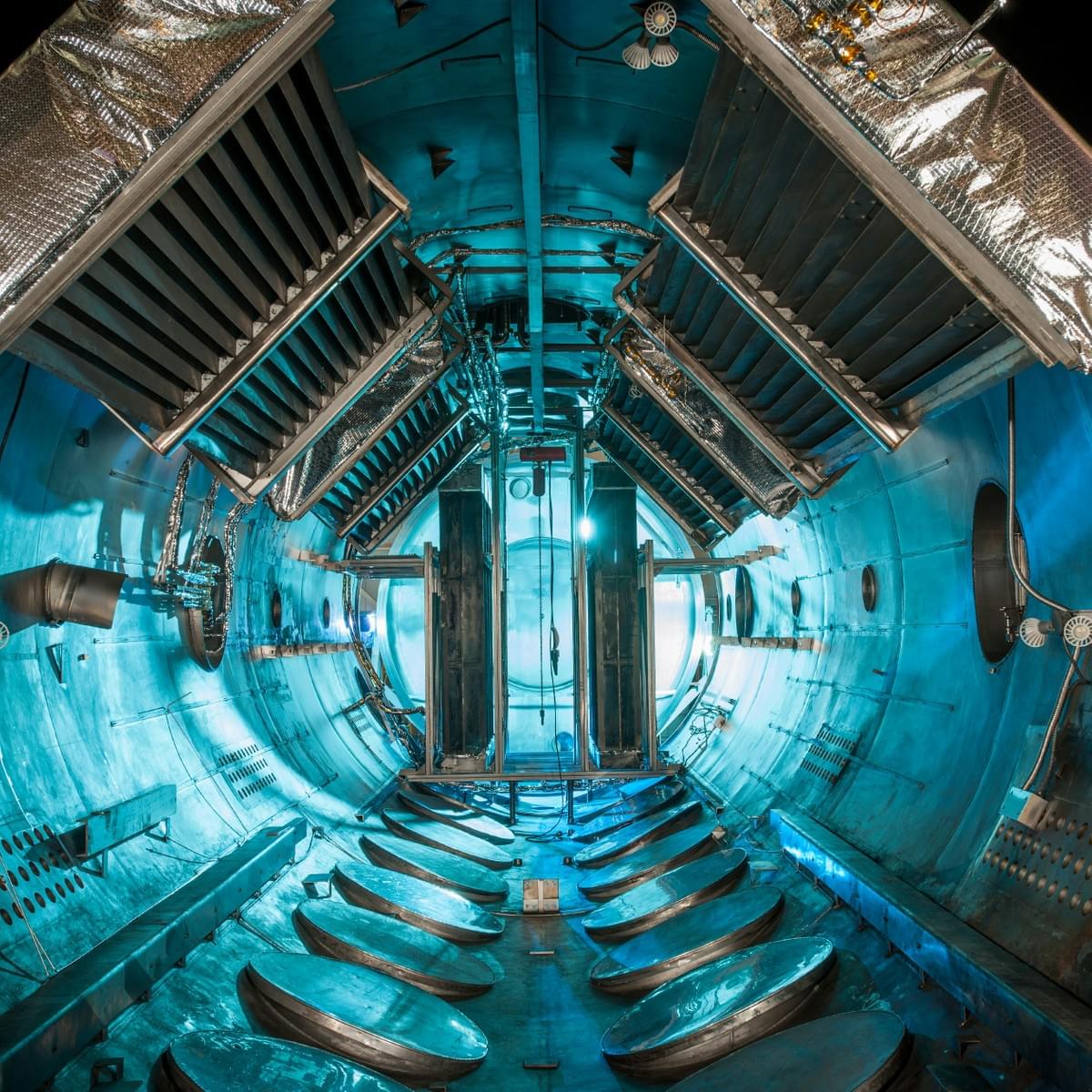
NiTiNb wires are revolutionizing the engineering industry with their exceptional properties and versatility. NiTiNb wires are increasingly used in various applications, from medical devices to aerospace engineering, as a cost-effective and reliable solution. With their shape memory and superelasticity, the future trends in NiTiNb wire applications are promising, offering endless possibilities for innovation and advancement in different industries. Partnering with GEE SMA is the intelligent choice for superior nitinol materials for unmatched quality and expertise in nitinol wire production.
Harnessing the Potential of NiTiNb Wires
The potential of NiTiNb wires lies in their unique ability to return to a predetermined shape when subjected to heat, making them ideal for a wide range of applications. From medical implants to robotics, these wires offer unparalleled performance and reliability, and harnessing their potential can lead to groundbreaking advancements in various industries.
NiTiNb wires are also known for their high fatigue resistance and biocompatibility, making them an excellent choice for medical devices such as stents, guide wires, and orthodontic appliances. Their ability to withstand repetitive bending and twisting without losing shape or strength makes them invaluable in the healthcare industry. Moreover, their biocompatibility ensures minimal risk of adverse reactions when implanted in the human body, setting a new standard for medical device materials.
The future trends in NiTiNb wire applications point towards innovative solutions that will further expand their usage across different sectors. With ongoing research and development, we can expect to see advancements in areas such as minimally invasive surgery, automotive engineering, and consumer electronics as new applications for NiTiNb wires emerge.
The potential for NiTiNb wire applications in minimally invasive surgery is fascinating, as these wires can be used to create advanced medical devices that are smaller, more flexible, and less invasive than ever before. This could lead to significant advancements in medical treatments, allowing for more precise procedures and faster patient recovery times. Additionally, using NiTiNb wires in automotive engineering holds promise for developing lighter and more robust components, leading to improved fuel efficiency and overall vehicle performance.
Partnering with GEE SMA for Superior Nitinol Materials
When sourcing high-quality nitinol materials such as NiTiNb wires, partnering with GEE SMA ensures access to top-notch products that meet industry standards. As one of the leading nitinol wire manufacturers and suppliers, GEE SMA's commitment to excellence guarantees superior materials tailored to specific requirements, providing unmatched reliability and performance.
In addition to providing top-notch nitinol materials, GEE SMA offers exceptional customer service and support. Their team of experts is dedicated to understanding each client's unique needs and providing tailored solutions that exceed expectations. With GEE SMA as a partner, customers can expect superior products and a collaborative and responsive approach to fulfilling their nitinol material requirements.