Introduction
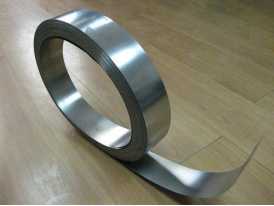
Nickel alloys microfoil is a versatile material that offers a wide range of benefits in precision engineering. From its exceptional strength to its ability to withstand extreme temperatures, nickel alloys microfoil is a go-to choice for many manufacturing applications. Additionally, the importance of heat treatment in nickel alloys cannot be overstated, as it plays a crucial role in enhancing their properties and performance.
Understanding the Benefits of Nickel Alloys Microfoil
Nickel alloys microfoil is good for a variety of applications due to its excellent corrosion resistance, high-temperature strength, and exceptional electrical conductivity. Its thin and flexible nature also makes it ideal for intricate manufacturing processes, providing precision and accuracy in the final product.
Nickel alloys microfoil's exceptional electrical conductivity also makes it a top choice for electronic components and devices. Its ability to conduct electricity with minimal resistance ensures optimal performance and reliability in various electronic applications. Whether used in circuit boards, sensors, or other electronic equipment, nickel alloys microfoil delivers the conductivity needed for efficient operation.
Exploring the Strength and Versatility of Nickel Alloys
The strongest nickel alloy is often determined by its composition and intended use. However, some of the strongest nickel alloys include Inconel 718, Hastelloy X, and Waspaloy, each offering unique properties that cater to specific engineering requirements.
Nickel alloys are known for their exceptional strength and versatility, making them indispensable in a wide range of industries. Inconel 718, for example, is renowned for its high tensile strength and excellent creep-rupture properties, making it ideal for applications in the aerospace and gas turbine industries. On the other hand, Hastelloy X offers superior oxidation resistance at high temperatures, making it a top choice for furnace components and chemical processing equipment. Waspaloy, with its exceptional strength and thermal stability, is often used in gas turbine engines and industrial heating applications. Each of these nickel alloys brings something unique to the table, allowing engineers to tailor their material selection to specific performance requirements.
The Importance of Heat Treatment in Nickel Alloys
Heat treatment of nickel alloys involves controlled heating and cooling processes to alter their mechanical properties such as hardness, strength, and ductility. This treatment method is crucial in optimizing the performance and durability of nickel alloys for various industrial applications.
Nickel alloys are a group of metals composed primarily of nickel, as well as other elements such as copper, chromium, and iron. These alloys are known for their exceptional corrosion resistance, high-temperature strength, and excellent mechanical properties. They are widely used in industries such as aerospace, chemical processing, and marine engineering due to their ability to withstand harsh environments and extreme conditions.
What Are Nickel Alloys and Their Applications?
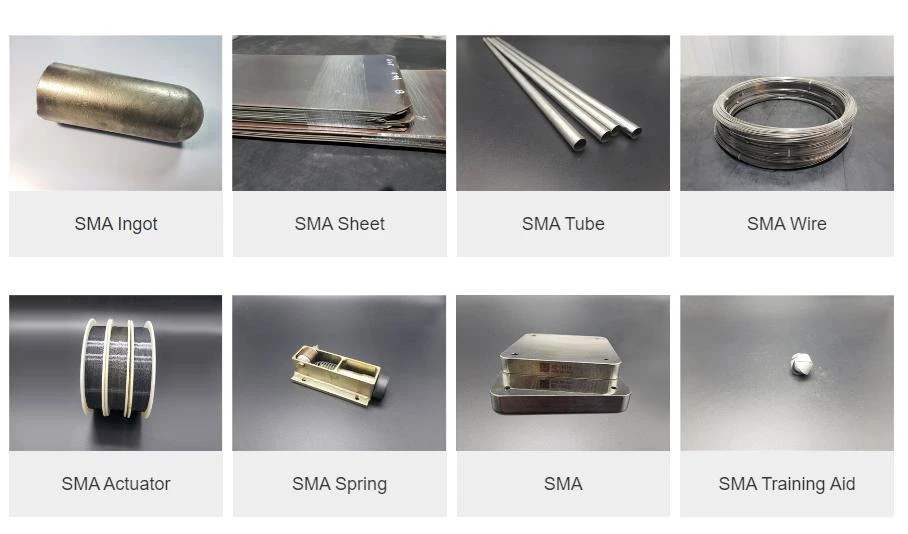
Nickel alloys are a group of metals that offer exceptional corrosion resistance, high strength, and excellent heat resistance. These alloys are known for their ability to withstand extreme temperatures and harsh environments, making them ideal for a wide range of applications in various industries.
Characteristics and Properties of Nickel Alloys
Nickel alloys exhibit a unique combination of properties, including high temperature strength, exceptional corrosion resistance, and excellent mechanical properties. These alloys can be easily fabricated into different shapes and forms, making them highly versatile for use in diverse engineering applications.
Nickel alloys are also known for their exceptional resistance to oxidation and sulfidation at high temperatures, making them ideal for use in applications such as gas turbines, aerospace components, and chemical processing equipment. Additionally, these alloys have a low thermal expansion coefficient, which allows them to maintain their shape and mechanical properties even at elevated temperatures. This makes nickel alloys a top choice for precision engineering in industries where high temperature stability and resistance to thermal fatigue are crucial.
Applications of Nickel Alloys in Precision Engineering
The exceptional properties of nickel alloys make them invaluable in precision engineering applications such as aerospace components, gas turbines, nuclear reactors, and chemical processing equipment. Their ability to maintain strength at high temperatures and resist corrosion makes them essential for critical components in demanding environments.
Nickel alloys are also highly resistant to oxidation and sulfidation, making them ideal for use in high-temperature and high-pressure environments. This resistance to corrosion ensures the longevity and reliability of components, reducing the need for frequent maintenance or replacement. In addition, nickel alloys exhibit excellent mechanical properties, including high tensile strength and toughness, further enhancing their suitability for precision engineering applications.
Advantages of Using Nickel Alloys Microfoil in Manufacturing
Nickel alloys microfoil offers several advantages in manufacturing processes due to its thinness and flexibility. It allows for precise shaping and forming of intricate components with minimal material waste. The microfoil's high strength and corrosion resistance make it an ideal choice for producing intricate parts with tight tolerances.
Additionally, nickel alloys microfoil is known for its excellent electrical and thermal conductivity, making it an ideal material for manufacturing electronic components and heat exchangers. Its ability to withstand high temperatures and harsh environments further expands its application in various industries, including aerospace, automotive, and medical equipment. The thinness of the microfoil also allows for efficient heat dissipation, contributing to the overall performance and reliability of the final products.
The Strongest Nickel Alloys for Precision Engineering
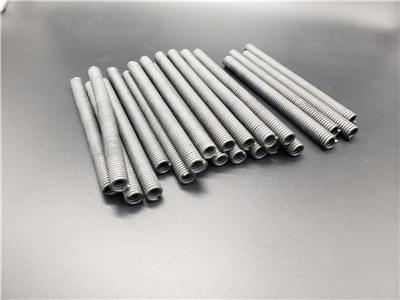
Identifying the Strongest Nickel Alloys
When looking for the strongest nickel alloys for precision engineering, it's important to consider factors such as tensile strength, corrosion resistance, and thermal stability. Some of the top contenders in this category include Inconel 718, Hastelloy X, and Waspaloy, known for their exceptional mechanical properties and high temperature capabilities.
Properties and Strength of GEE SMA Nickel Alloys
GEE SMA nickel alloys are renowned for their exceptional strength and durability, making them ideal for precision engineering applications where reliability is crucial. These alloys exhibit superior resistance to oxidation and corrosion, along with excellent thermal stability, making them a top choice for demanding environments.
GEE SMA nickel alloys are renowned for their exceptional strength and durability, making them ideal for precision engineering applications where reliability is crucial. These alloys exhibit superior resistance to oxidation and corrosion, along with excellent thermal stability, making them a top choice for demanding environments. In addition to their impressive physical properties, GEE SMA nickel alloys also offer high electrical conductivity, further expanding their potential applications in various industries. This combination of strength, durability, and conductivity sets these alloys apart from other nickel-based materials.
Comparing the Strength of Different Nickel Alloys
When comparing the strength of different nickel alloys, it's essential to assess their performance under various conditions such as high temperatures, extreme pressures, and corrosive environments. While some nickel alloys excel in specific areas like creep resistance or fatigue strength, others may offer a more balanced combination of properties suitable for a wide range of applications.
It's also important to consider the cost-effectiveness of different nickel alloys, as some may offer superior strength but at a higher price point. Balancing performance with cost is crucial for many industries, especially when considering large-scale applications where material expenses can significantly impact the overall project budget. Additionally, the availability and ease of fabrication of nickel alloys should be taken into account, as these factors can influence the feasibility and practicality of using a particular alloy in a given application.
Heat Treatment Techniques for Nickel Alloys Microfoil
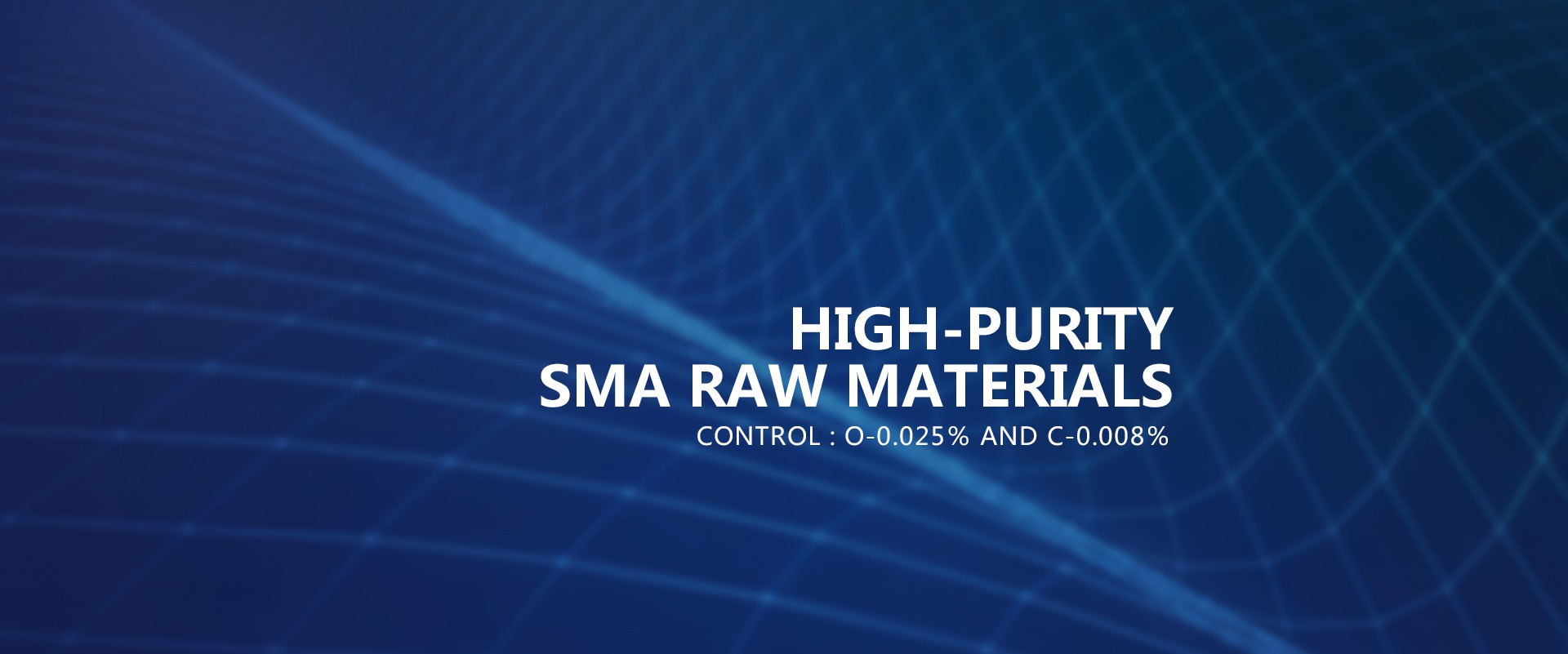
Understanding the Heat Treatment Process
Heat treatment of nickel alloys microfoil involves a series of controlled heating and cooling processes to alter the material's properties. This can include annealing, quenching, and tempering to improve strength, hardness, and ductility. By carefully manipulating the microstructure, the heat treatment process enhances the performance of nickel alloys microfoil in precision engineering applications.
Impact of Heat Treatment on Nickel Alloys
The heat treatment process is crucial for achieving the desired mechanical properties in nickel alloys microfoil. By carefully controlling the temperature and cooling rate during heat treatment, it is possible to enhance the tensile strength and yield strength of the material, making it suitable for demanding applications in precision engineering. Additionally, the resistance to corrosion and oxidation can be significantly improved through proper heat treatment, ensuring that components made from nickel alloys microfoil have a long service life in harsh operating environments.
Heat Treatment Best Practices for Precision Engineering
In precision engineering, it's crucial to adhere to best practices when performing heat treatment on nickel alloys microfoil. This includes precise temperature control, uniform heating and cooling rates, and proper selection of heat treatment cycles based on specific alloy compositions. Additionally, post-heat treatment processes such as stress relieving or aging may be necessary to further optimize the performance of nickel alloys microfoil in demanding applications.
To ensure the highest quality and performance of nickel alloys microfoil, it's essential to pay close attention to the post-heat treatment processes. Stress relieving, for example, can help to eliminate internal stresses that may have developed during the heat treatment process, resulting in improved dimensional stability and reduced risk of distortion. Additionally, aging can be used to enhance the strength and hardness of the microfoil, making it better suited for withstanding extreme conditions in precision engineering applications.
Nickel Strip & Nickel Foil & Nickel Alloys: A Comparative Analysis
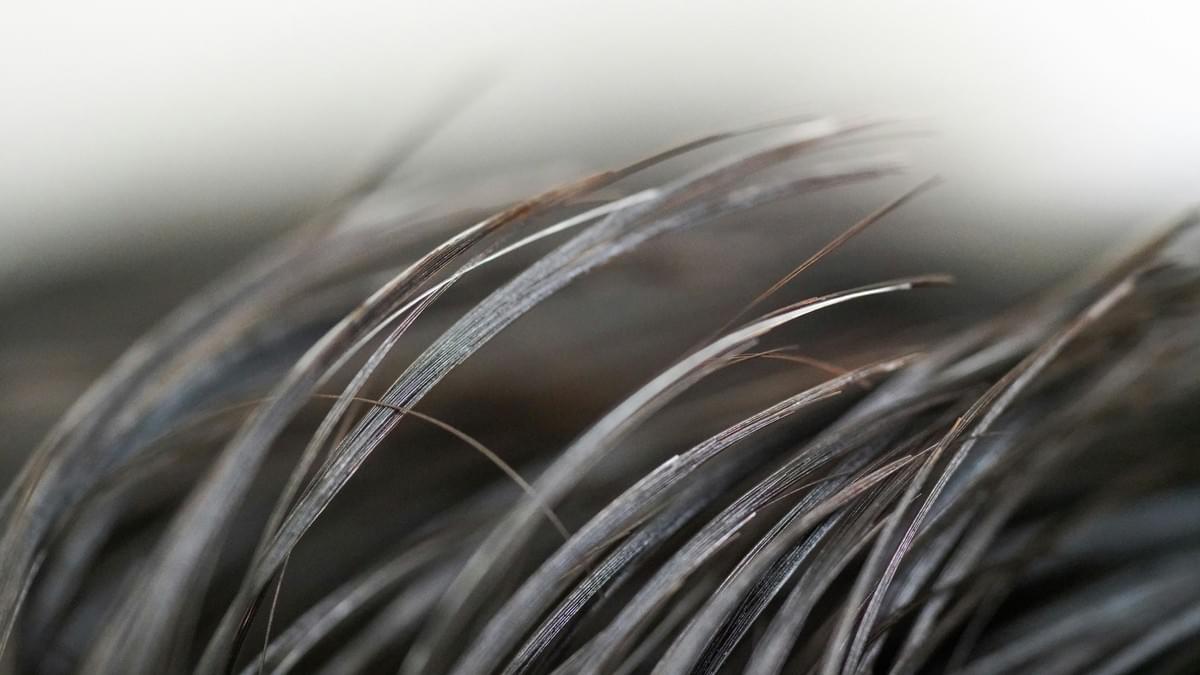
Nickel Strip, Nickel Foil, and Nickel Alloys are all essential materials in precision engineering. Each type of nickel material has its own unique properties and applications, making them indispensable in various industries. When it comes to choosing the right nickel material for precision engineering, it's important to understand the differences and benefits of each.
Different Types of Nickel Materials
Nickel Strip is a thin, flat metal that is commonly used in battery production, electrical components, and automotive applications. It offers excellent corrosion resistance and high thermal conductivity, making it ideal for a wide range of industrial uses. On the other hand, Nickel Foil is even thinner than strip and is often used in electronics, aerospace, and medical devices due to its flexibility and durability. Meanwhile, Nickel Alloys are mixtures of nickel with other metals such as copper, chromium, or iron to enhance their properties like strength or corrosion resistance.
Applications and Benefits of Nickel Strip, Nickel Foil, and Nickel Alloys
Nickel Strip is widely used in battery tabs for electric vehicles and energy storage systems due to its ability to withstand high temperatures without deformation or degradation. Meanwhile, Nickel Foil is commonly found in capacitors for electronic devices because of its excellent electrical conductivity and reliability under extreme conditions. On the other hand,Nickel Alloys Microfoil are utilized in aerospace components for their exceptional strength-to-weight ratio and resistance to high temperatures.
In addition to these applications, Nickel Strip is also commonly used in the production of solar panels due to its corrosion resistance and long-term durability in outdoor environments. This makes it an ideal material for connecting solar cells and ensuring efficient energy transfer. Similarly, Nickel Foil is utilized in the automotive industry for its ability to withstand vibrations and high temperatures, making it a reliable choice for electronic components in vehicles. Additionally, Nickel Alloys Microfoil finds its place in the medical field, where it is used in surgical instruments and implants for its biocompatibility and resistance to corrosion within the human body.
Choosing the Right Nickel Material for Precision Engineering
When selecting a nickel material for precision engineering applications,it's crucial to consider factors such as mechanical properties,cost-effectiveness,and environmental sustainability.Nickel Strip may be the best choice for battery connectors due to its low electrical resistance.Nickel Foil can be ideal for flexible circuits in electronics because of its malleability.Finally,Nickel Alloys Microfoil would be suitable for manufacturing turbine engine components given their superior strength at elevated temperatures.
In addition to mechanical properties, cost-effectiveness, and environmental sustainability, it's also important to consider the corrosion resistance of nickel materials when making a selection. Nickel alloys such as Inconel are highly resistant to corrosion and oxidation, making them suitable for applications in harsh environments such as chemical processing plants and marine equipment. This added durability can extend the lifespan of precision-engineered components, reducing maintenance costs and downtime.
Conclusion
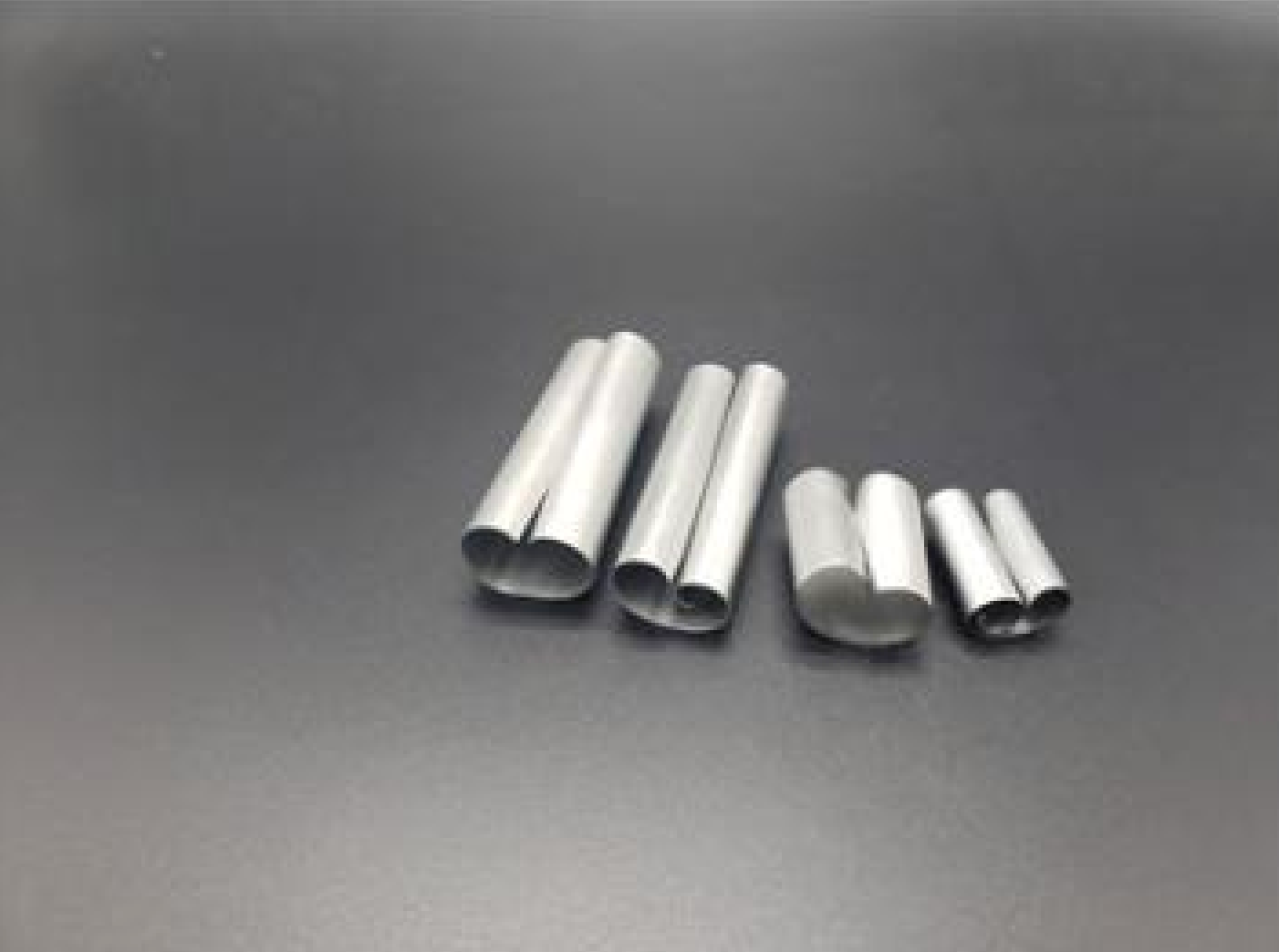
Nickel alloys microfoil offer unparalleled strength and versatility for precision engineering applications. With the ability to withstand extreme temperatures and corrosive environments, nickel alloys are good for a wide range of industries, including aerospace, medical, and automotive. The strongest nickel alloy, GEE SMA, boasts exceptional properties that make it ideal for demanding engineering projects.
Maximizing performance with high-quality nickel alloys microfoil is crucial for achieving superior results in precision engineering. The heat treatment of nickel alloys is a critical process that enhances their mechanical properties, making them more durable and resistant to wear and tear. By unlocking the potential of nickel alloys through precision engineering, manufacturers can create innovative solutions that push the boundaries of what's possible.