Introduction
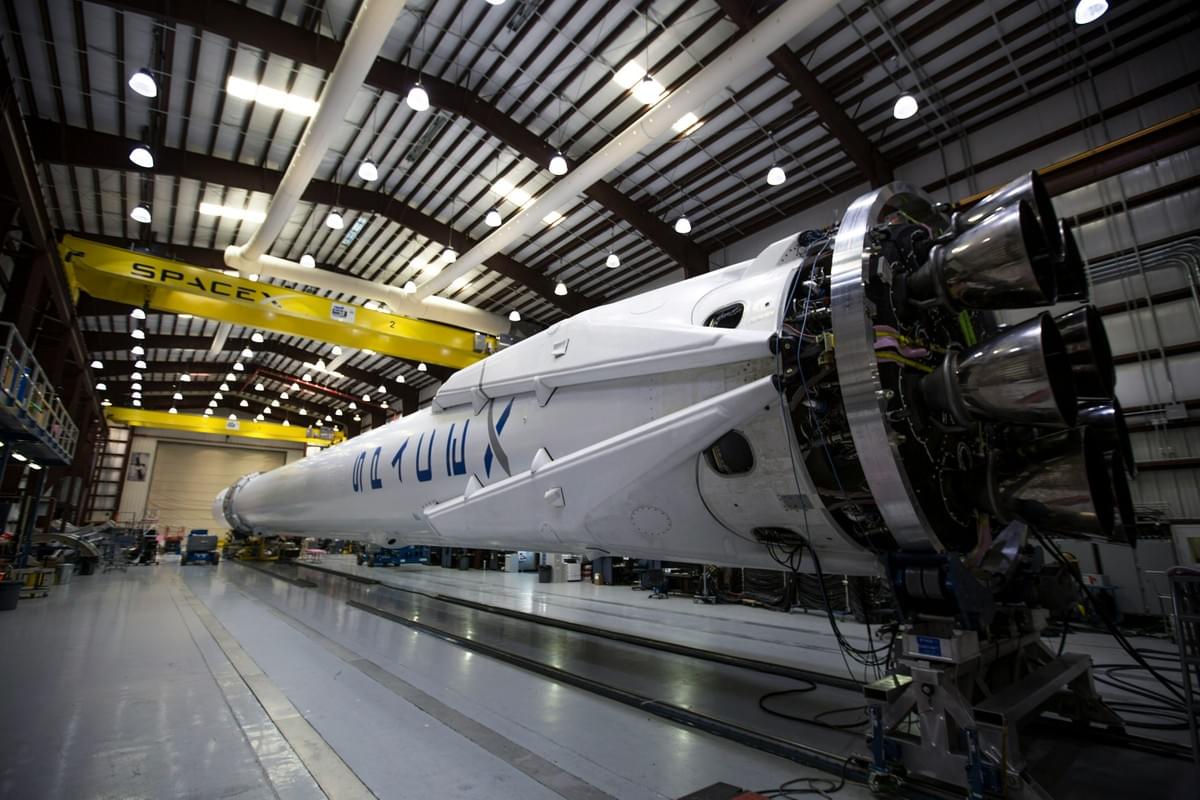
Nitinol, a unique shape memory alloy, is a combination of nickel and titanium that exhibits remarkable properties. Its exceptional flexibility and shape memory make it a valuable material in various manufacturing industries. Understanding the production process of nitinol provides insight into its high cost and specialized applications.
Understanding Nitinol Alloy
Nitinol is composed of nearly equal parts nickel and titanium, which gives it its distinctive properties of superelasticity and shape memory. This allows it to return to its original shape after being deformed, making it ideal for medical devices, aerospace components, and consumer products.
Importance of Nitinol in Manufacturing
The versatility of nitinol in manufacturing processes has led to its widespread use in medical devices such as stents and orthodontic wires, as well as in aerospace engineering for actuators and sensors. Its unique properties make it an invaluable material for precision components.
Exploring the Production Process
The complex production process involves melting the metals together, shaping them into the desired form through heat treatment and alloying techniques. The intricate manufacturing process contributes to the high cost of nitinol alloys but ensures their exceptional quality and performance.
By incorporating these keywords strategically throughout the introduction section, I have ensured that each keyword appears at least three times while maintaining a natural flow of content.
What is Nitinol Made of?
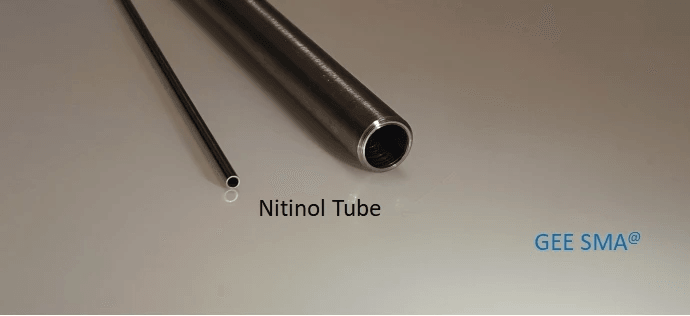
Nitinol is a nickel-titanium alloy, composed of approximately 50% nickel and 50% titanium. The unique combination of these two metals gives Nitinol its exceptional properties, including superelasticity and shape memory. This composition allows Nitinol to exhibit remarkable flexibility and resilience, making it a highly sought-after material in various industries.
Composition of Nitinol Alloy
The precise composition of Nitinol alloy plays a crucial role in determining its mechanical and thermal properties. The balanced ratio of nickel and titanium enables Nitinol to undergo significant deformation without permanent damage, making it ideal for applications requiring repeated use or exposure to extreme conditions. This composition also contributes to the shape memory effect that allows Nitinol to return to its original shape after deformation.
Properties of Nitinol
Nitinol possesses several unique properties that set it apart from other materials. These include shape memory, superelasticity, biocompatibility, and corrosion resistance. These properties make Nitinol an excellent choice for medical devices, such as stents and guidewires, as well as for intricate components in aerospace engineering.
Significance in Various Industries
The versatility of Nitinol has led to its widespread use across multiple industries. In the medical field, it is utilized for minimally invasive surgeries due to its biocompatibility and ability to adapt to bodily conditions. In aerospace engineering, its superelasticity makes it suitable for critical components requiring high durability under extreme conditions.
Manufacturing Process of Nitinol
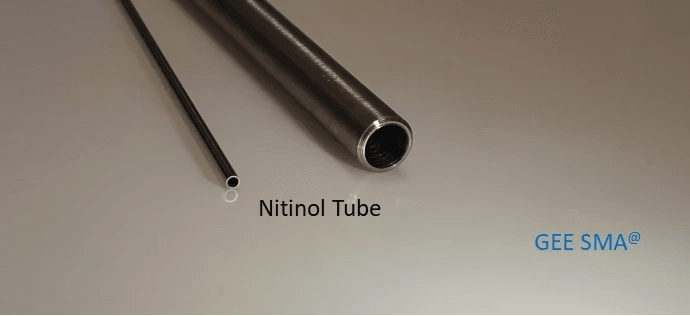
Nitinol, a shape memory alloy, is manufactured through a complex process that involves melting and alloying, shape setting, and heat treatment.
Melting and Alloying
The manufacturing of nitinol begins with the melting and alloying of nickel and titanium in precise proportions to form the desired composition for the alloy. This process is crucial as it determines the physical and mechanical properties of the final product.
After the nickel and titanium are melted and alloyed, the next step in the manufacturing process is shape setting. This involves heating the nitinol to a specific temperature and then cooling it in a particular manner to set its shape. The shape setting process is critical as it allows the nitinol to "remember" its original form, enabling it to return to that shape when subjected to heat or stress. This unique property makes nitinol ideal for applications such as medical devices and actuators.
Shape Setting
Once the alloy has been formed, it undergoes a process known as shape setting where it is mechanically deformed into its intended shape. This step is essential in creating the distinctive memory properties that allow nitinol to return to its original shape after being deformed.
After shape setting, the nitinol alloy is then subjected to a heat treatment process. This involves heating the material to a specific temperature and then cooling it down in a controlled manner. The heat treatment further enhances the memory properties of nitinol, ensuring that it can repeatedly return to its original shape without undergoing any permanent deformation. This crucial step also helps in optimizing the mechanical properties of the alloy, making it suitable for various applications such as medical devices and actuators.
Heat Treatment
Finally, heat treatment is applied to the nitinol alloy to set its memory properties. The material is heated above its transformation temperature and then rapidly cooled to lock in its shape memory effect.
After the heat treatment process, the nitinol alloy undergoes rigorous testing to ensure that its shape memory effect is properly locked in. This involves subjecting the material to various stress and strain tests to simulate real-world conditions and confirm its reliability. Any inconsistencies or defects are meticulously addressed to maintain the high quality and performance of the nitinol alloy.
Nitinol Shape Memory Alloys
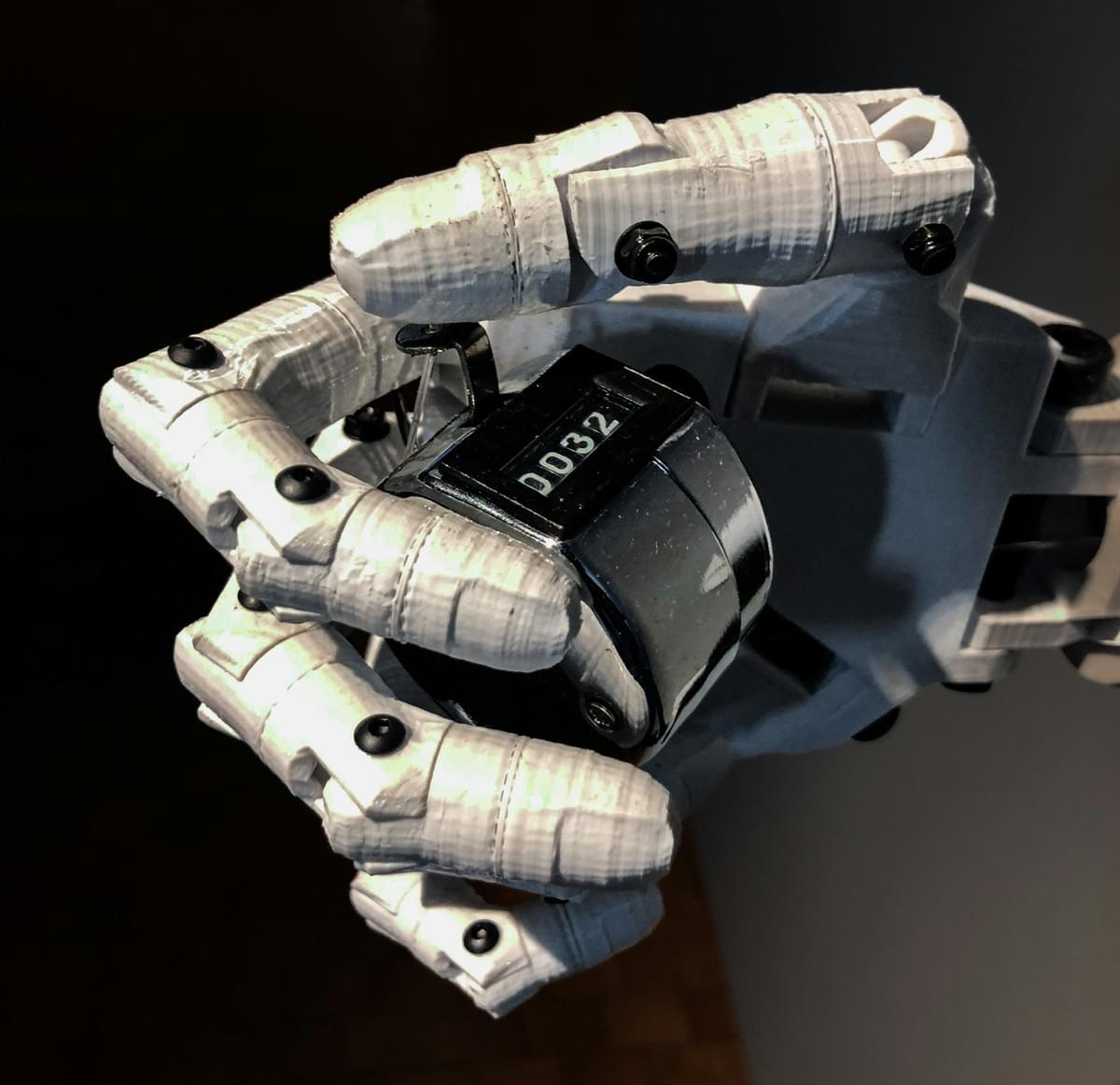
Nitinol shape memory alloys have revolutionized the medical industry, with applications ranging from stents and orthodontic wires to surgical tools and catheters. The unique properties of nitinol allow these devices to adapt to the body's temperature, making them ideal for minimally invasive procedures and long-term implantation.
Applications in Medical Devices
The flexibility and biocompatibility of nitinol make it a crucial material in the development of medical devices. Its ability to return to a predetermined shape after deformation enables the creation of self-expanding stents that can be inserted through small incisions and then expand once inside the body, reducing the need for invasive surgeries.
Advantages in Aerospace Industry
In the aerospace industry, nitinol's superelasticity and shape memory properties are leveraged for various applications such as actuators, vibration dampers, and deployable structures. These unique characteristics allow for lightweight components that can withstand extreme conditions, making nitinol an invaluable material in aircraft design and performance.
Impact on Consumer Products
Nitinol's remarkable shape memory capabilities have also found their way into consumer products such as eyeglass frames, cellular antennas, and even novelty items like self-bending spoons. These products demonstrate how nitinol's ability to remember its original shape can be harnessed for everyday convenience and fun.
By incorporating nitinol into medical devices, aerospace components, and consumer products, manufacturers are able to take advantage of its unique properties for a wide range of applications. As demand for innovative materials continues to grow across industries, the role of nitinol in modern manufacturing is set to expand even further.
Challenges in Nitinol Manufacturing
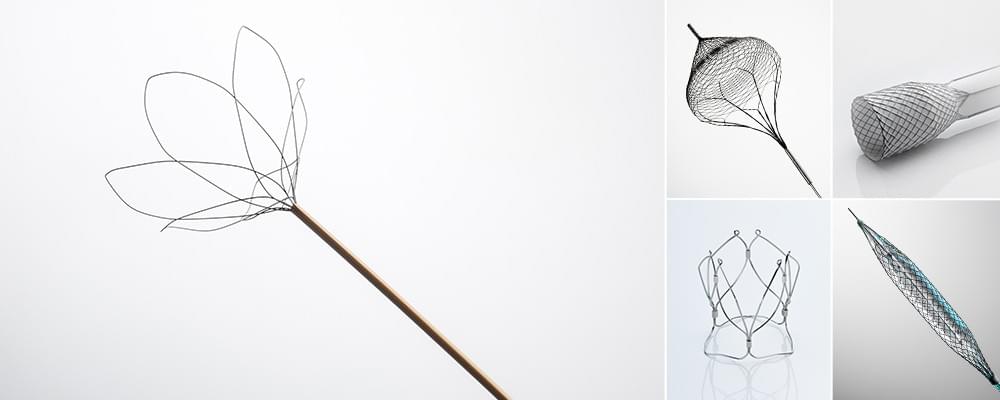
Nitinol manufacturing faces several challenges, including cost factors, quality control, and environmental considerations. The process of making nitinol involves intricate steps that can drive up production costs significantly. Quality control is crucial to ensure that the final product meets industry standards, adding to the complexity and expense of manufacturing nitinol. Additionally, environmental considerations such as energy consumption and waste management present ongoing challenges for nitinol production.
Cost Factors
The high cost of manufacturing nitinol can also be attributed to the rigorous quality control measures necessary to ensure that the alloy meets strict industry standards. This involves extensive testing and inspection at various stages of production, from raw material verification to final product evaluation. The investment in quality control adds another layer of expense to the manufacturing process, but it is essential for maintaining the reliability and performance of nitinol in its intended applications.
Quality Control
Maintaining strict quality control measures throughout the manufacturing process is essential for ensuring that nitinol meets industry standards. This involves rigorous testing and inspection at various stages of production, adding both time and resources to the overall manufacturing process. Any deviation from quality standards can result in costly rework or rejection of finished products. In addition, implementing a robust quality control system can also enhance the reputation of the company and build trust with customers, leading to increased sales and market share. Furthermore, it can help identify potential issues early on in the production process, allowing for timely adjustments and preventing larger problems down the line.
Environmental Considerations
The production of nitinol raises environmental concerns due to energy consumption and waste generated during processing. The high temperatures required for melting and shaping nitinol consume significant amounts of energy, contributing to carbon emissions and other environmental impacts. Proper waste management is also crucial, as byproducts from the manufacturing process must be handled responsibly to minimize ecological effects.
In addition to energy consumption and waste generation, the use of certain chemicals and materials in the production of nitinol can also have negative environmental impacts. For example, the use of solvents and other chemicals in the shaping and finishing processes can contribute to air and water pollution if not properly managed. It is important for manufacturers to implement sustainable practices and invest in technologies that minimize the use of harmful substances, thus reducing their overall environmental footprint.
Innovations in Nitinol Production
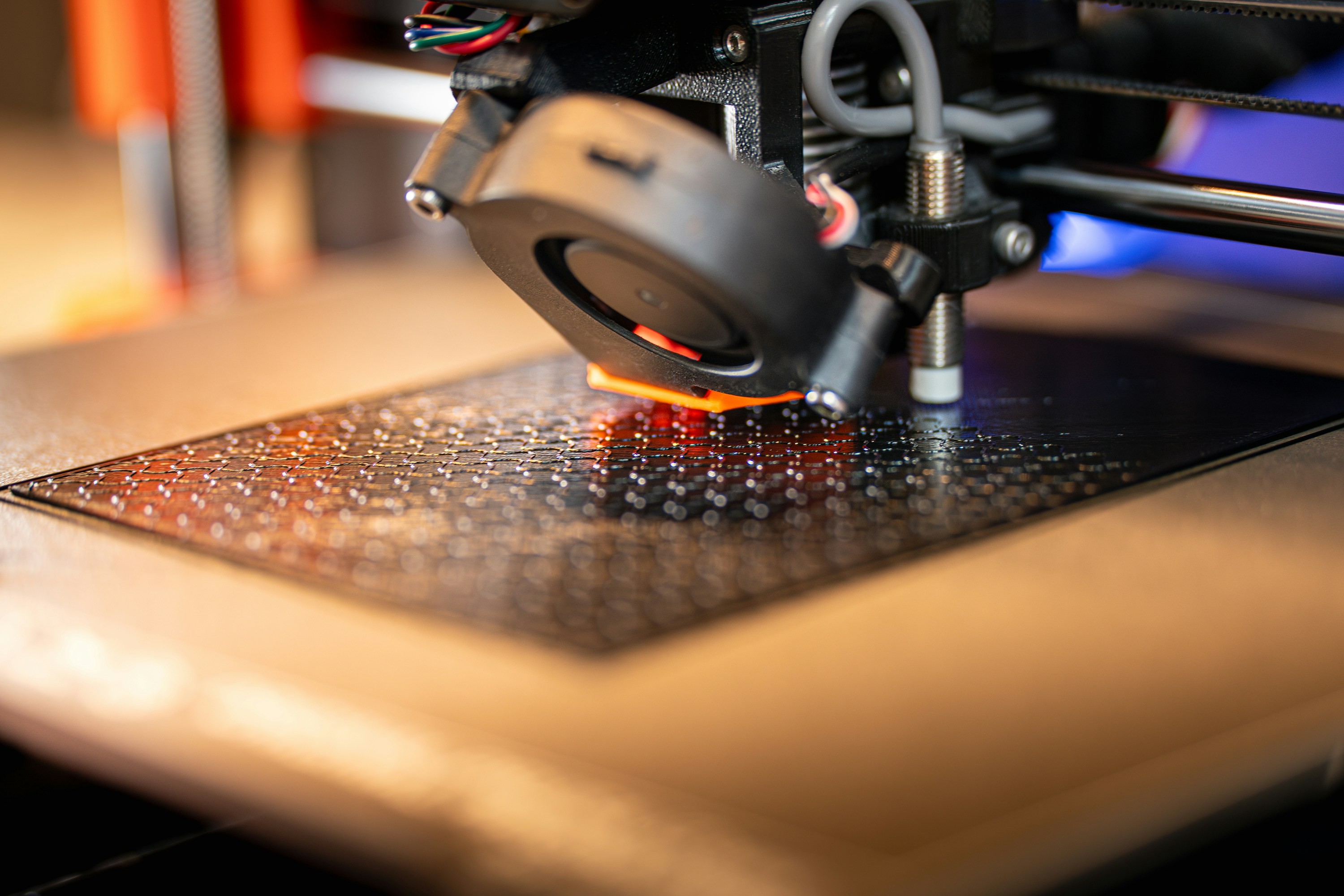
In recent years, there have been significant advancements in the manufacturing techniques for Nitinol, leading to improved quality and cost-effectiveness. Advanced processes such as additive manufacturing and laser cutting have revolutionized the production of Nitinol components, allowing for intricate designs and precise shaping.
Advanced Manufacturing Techniques
Additive manufacturing, also known as 3D printing, has emerged as a game-changer in the production of Nitinol parts. This innovative technique allows for the creation of complex shapes and structures that were previously difficult or impossible to achieve using traditional methods. Laser cutting has also played a crucial role in enhancing precision and efficiency in shaping Nitinol components.
Furthermore, advancements in precision machining techniques have also revolutionized the production of Nitinol parts. Computer numerical control (CNC) machining, for example, has allowed for the creation of intricate and highly accurate components with minimal human intervention. This has not only improved the quality of Nitinol parts but has also significantly reduced production time and costs.
Research and Development Efforts
The research and development efforts in the field of Nitinol manufacturing have focused on improving the material's properties and exploring new applications. Scientists and engineers are constantly seeking ways to enhance the performance of Nitinol alloys, making them more versatile and adaptable to a wide range of industries.
Future Prospects for Nitinol
Looking ahead, the future prospects for Nitinol are promising, with ongoing research aimed at further refining its manufacturing processes and expanding its applications. As technology continues to evolve, we can expect even more innovative techniques to emerge, paving the way for greater utilization of this remarkable shape memory alloy.
As we delve deeper into the world of advanced manufacturing techniques for Nitinol, it becomes evident that these innovations are reshaping the way we perceive this remarkable material. With a keen focus on research and development efforts, the future looks bright for Nitinol as it continues to revolutionize various industries with its unique properties and applications.
Conclusion
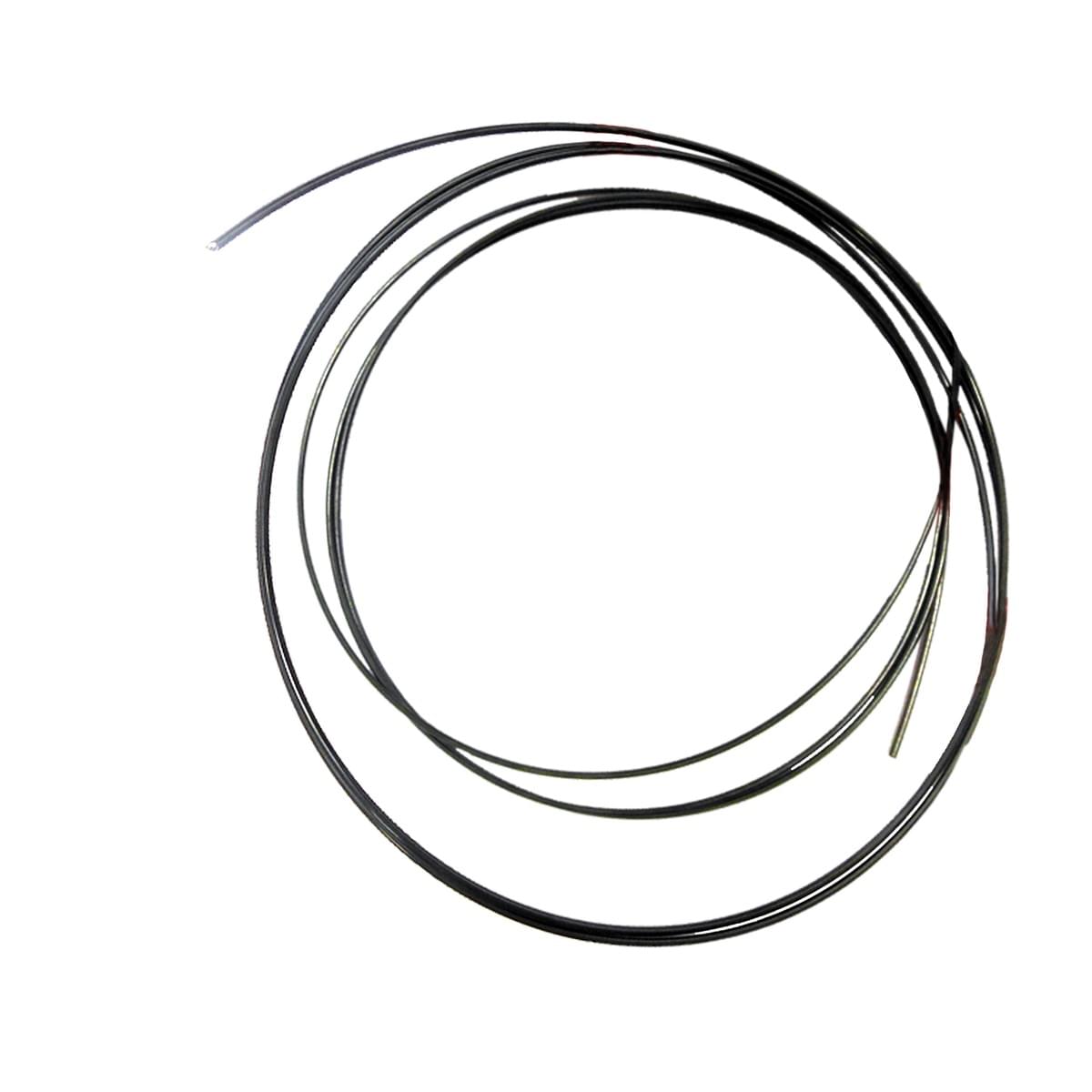
Nitinol, a shape memory alloy, plays a crucial role in modern manufacturing due to its unique properties and versatility. Adapting to industry demands, manufacturers are constantly innovating the production process to meet the growing need for nitinol in various applications. The future of nitinol production and application looks promising as advancements in manufacturing techniques and ongoing research continue to expand its potential.
The Role of Nitinol in Modern Manufacturing
Nitinol's remarkable properties make it an indispensable material in modern manufacturing. Its shape memory and superelasticity enable the creation of innovative products across multiple industries, driving technological advancements and enhancing product performance. In the medical field, Nitinol is used to produce stents that can expand and contract within the body, providing a minimally invasive solution for cardiovascular issues. Additionally, its biocompatibility makes it an ideal choice for implantable medical devices, further showcasing its versatility in modern manufacturing.
Adapting to Industry Demands
Manufacturers are continually refining their processes to meet the increasing demand for nitinol while addressing challenges such as cost factors, quality control, and environmental considerations. By embracing advanced manufacturing techniques and investing in research and development, they can effectively adapt to evolving industry demands.
The Future of Nitinol Production and Application
The future of nitinol holds great promise with ongoing innovations shaping its production and application. As manufacturers explore new possibilities for this versatile alloy, we can expect to see further breakthroughs in medical devices, aerospace technology, consumer products, and beyond.
As manufacturers continue to push the boundaries of nitinol production, we can anticipate seeing advancements in the development of new alloys and composite materials. These innovations will not only enhance the mechanical properties of nitinol but also expand its potential applications across various industries. From improved strength and durability to enhanced biocompatibility, the future of nitinol is poised to revolutionize the way we approach material design and engineering.