Introduction
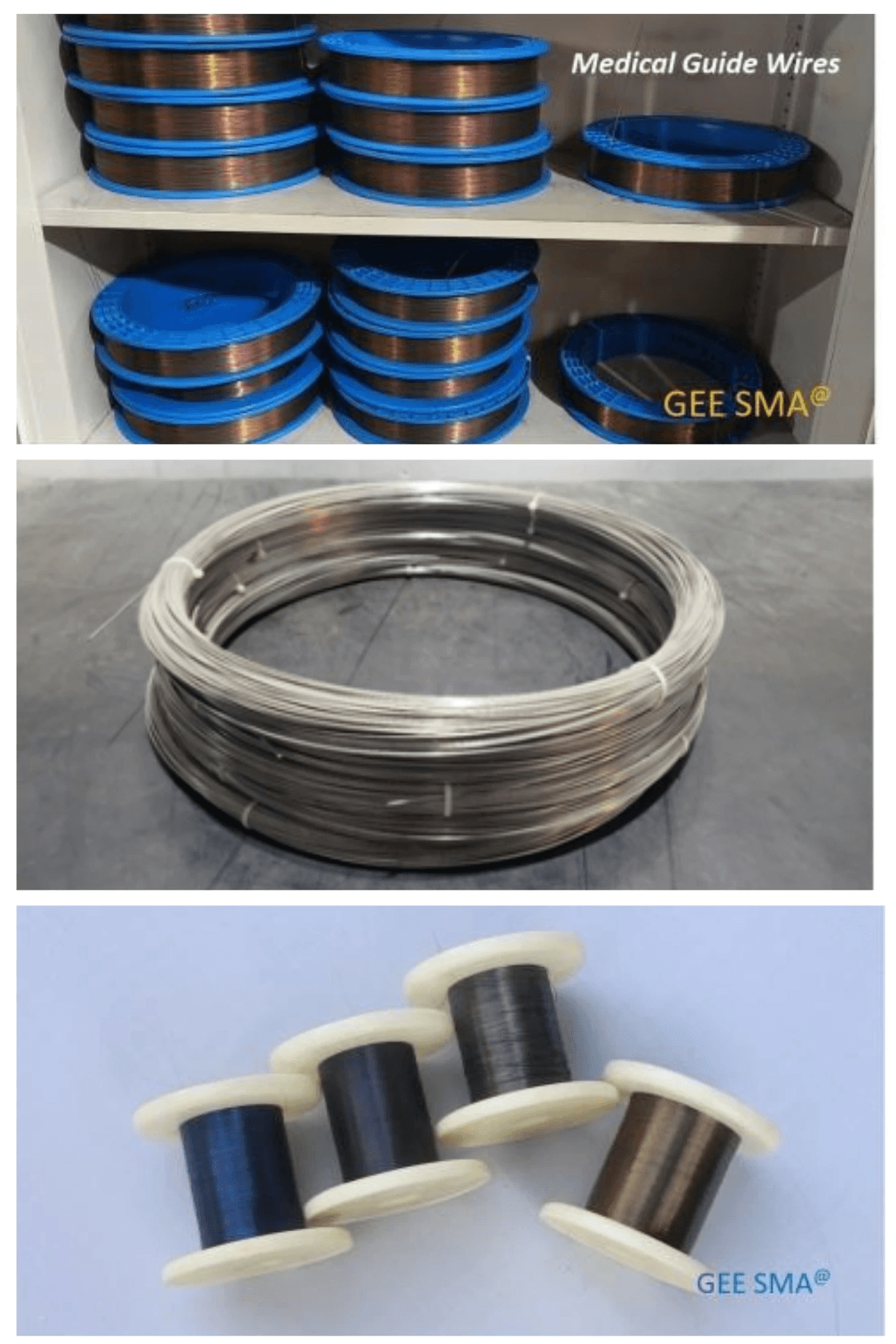
Nitinol, a unique alloy of nickel and titanium, possesses remarkable material properties that make it a versatile and valuable material in various industries. Its shape memory effect and superelasticity have revolutionized the design of medical devices, aerospace components, and consumer gadgets. With its exceptional tensile strength and durability, nitinol has become indispensable in modern technology, driving innovation and pushing the boundaries of what's possible.
Understanding Nitinol Material Properties
The material properties of nitinol are truly fascinating. It exhibits a shape memory effect, allowing it to return to its original shape after deforming at certain temperatures. Additionally, its superelasticity enables it to withstand significant strain without permanent deformation. These unique characteristics make nitinol an ideal choice for flexible and resilient applications.
Exploring Real-World Applications
Nitinol's versatility has led to its widespread use across various industries. Due to its biocompatibility and shape memory properties, it is utilized in implants and surgical tools in the medical field. Aerospace and automotive applications benefit from nitinol's lightweight yet durable nature. Moreover, consumer electronics leverage its flexibility for innovative designs in gadgets such as eyeglass frames and smartphone antennas.
Importance of Nitinol in Modern Technology
Nitinol is a critical material driving innovation in modern technology. Its unique properties make it indispensable in various applications.
- Exceptional Tensile Strength: Allows for creating robust yet lightweight components, essential for advancing technological capabilities.
- Enhanced Corrosion Resistance and Biocompatibility: Electropolishing techniques render nitinol surfaces suitable for demanding environments and medical applications.
- Versatility in Manufacturing: The production of semi-finished parts through shape memory alloy (SMA) processes expands the potential applications of nitinol in cutting-edge technologies.
Nitinol's combination of properties positions it as a cornerstone material for future technological advancements.
The Versatility of Nitinol Material Properties
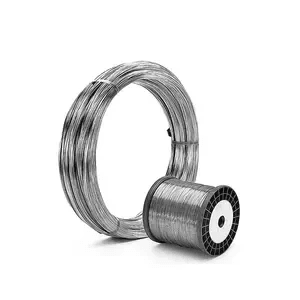
Nitinol material properties are known for their remarkable versatility, making them ideal for various applications. One of the most fascinating characteristics of nitinol is its shape memory effect, which allows the material to return to its original shape after being deformed. This unique property has led to innovative uses in medical devices, aerospace, and consumer electronics industries.
Shape Memory Effect in Nitinol
The shape memory effect in nitinol results from its ability to undergo a reversible phase transformation between the austenite and martensite phases. This means that nitinol can remember its original shape and return to it when subjected to the appropriate stimulus, such as heat or stress. This property has revolutionized the development of minimally invasive medical devices, allowing for the creation of self-expanding stents and guidewires that can navigate through complex anatomical structures with precision.
Superelasticity and Flexibility
In addition to its shape memory effect, nitinol exhibits superelasticity and flexibility, making it an ideal material for applications requiring resilience and durability. These properties allow nitinol components to withstand repeated deformation without permanent damage, making them well-suited for use in orthodontic braces, surgical instruments, and various mechanical systems where reliability is paramount.
In addition to its shape memory effect, nitinol's superelasticity and flexibility make it a standout material for various applications. Its ability to withstand repeated deformation without permanent damage is especially beneficial in the medical field, where orthodontic braces and surgical instruments must maintain their integrity under various stresses. Furthermore, in mechanical systems where reliability is paramount, nitinol's resilience and durability ensure optimal performance over extended periods of use.
Tensile Strength and Durability
Nitinol's impressive tensile strength and durability enhance its appeal for various applications. With a high fatigue and excellent corrosion resistance, nitinol components can endure demanding conditions without compromising their performance. This makes them invaluable in aerospace and automotive engineering industries, where safety and reliability are critical considerations.
Nitinol's exceptional tensile strength and durability make it a top choice for medical device applications. Its ability to withstand repeated bending and flexing without losing shape or structural integrity is crucial for devices such as stents, guidewires, and orthodontic wires. In addition, its biocompatibility and non-toxic nature make nitinol an ideal material for implants, ensuring patient safety and comfort. This unique combination of properties has revolutionized the field of medical technology, allowing for the development of innovative devices that can improve patient outcomes and quality of life.
What is Nitinol Used For?
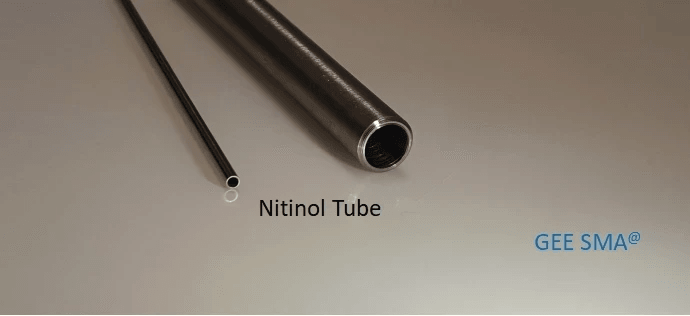
Medical Devices and Implants
Nitinol material properties make it an ideal choice for medical devices and implants due to its unique ability to return to its original shape after deformation. This makes it perfect for stents, orthopedic implants, and guidewires, providing flexibility and durability in the human body.
Aerospace and Automotive Applications
Nitinol's high tensile strength and superelasticity are highly valued in the aerospace and automotive industries. It is used in actuators, sensors, and components that require lightweight yet strong materials. Its ability to withstand extreme conditions makes it indispensable in these sectors.
Consumer Electronics and Gadgets
Nitinol's shape memory effect is harnessed in consumer electronics such as mobile phones, eyeglass frames, and headphones. Its flexibility allows for innovative designs while maintaining structural integrity. From smart gadgets to everyday appliances, nitinol enhances user experience.
Enhancing Nitinol Material Properties
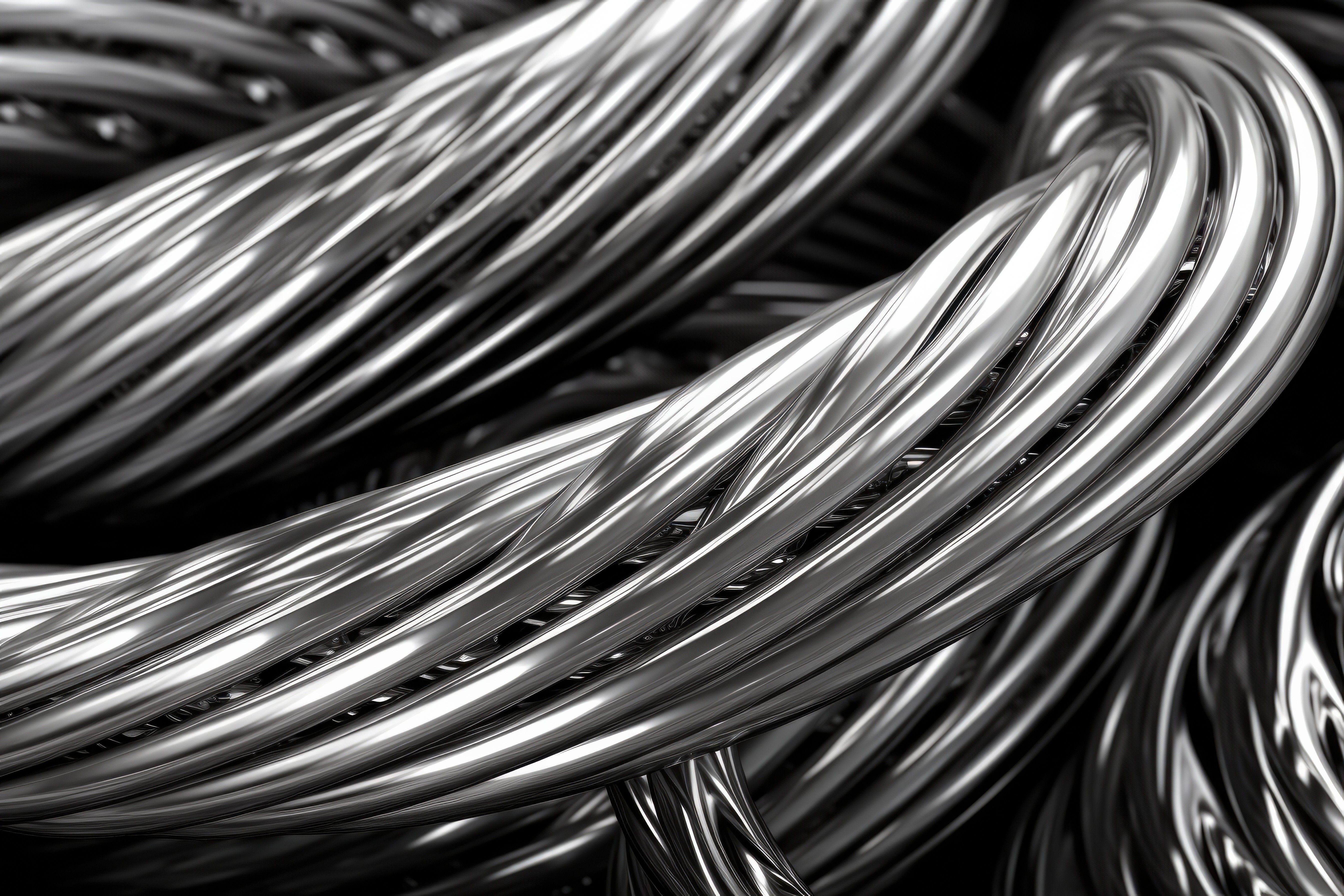
Nitinol material properties can be further improved through electropolishing techniques, which involve using an electrolyte solution and an electrical current to remove surface imperfections and enhance the finish of nitinol components. This process improves nitinol parts' aesthetic appeal and ensures better corrosion resistance and biocompatibility, making it ideal for medical and aerospace applications.
Electropolishing Techniques
Semi-finished parts play a crucial role in shaping the final form of nitinol components, especially in shape memory alloy (SMA) manufacturing. These semi-finished parts are carefully processed to achieve specific shapes and dimensions, allowing for precise customization according to the requirements of different industries. Nitinol can be transformed into intricate shapes through advanced manufacturing techniques while maintaining its unique material properties.
Electropolishing techniques are commonly used in the finishing process of nitinol components, especially in SMA manufacturing. This process involves the removal of surface material through an electrochemical reaction, resulting in a smooth and shiny surface finish. By using this technique, manufacturers can improve nitinol components' corrosion resistance and biocompatibility, making them suitable for a wide range of medical and industrial applications. Additionally, electropolishing allows for the precise removal of surface imperfections, ensuring that the final nitinol parts meet stringent quality standards.
Semi-Finished Parts and SMA Manufacturing
Quality control and testing processes are essential for ensuring the reliability and performance of nitinol materials. Rigorous testing methods such as tensile strength tests, fatigue tests, and thermal cycling tests are conducted to validate nitinol components' mechanical properties and durability. By adhering to strict quality control standards, manufacturers can guarantee that nitinol products meet the highest industry standards for safety and efficiency.
Semi-finished parts play a crucial role in the manufacturing of nitinol components. These parts undergo rigorous testing to meet shape memory alloy (SMA) manufacturing specifications. By conducting thorough quality control checks on semi-finished parts, manufacturers can identify any potential issues early in the production process, thereby minimizing waste and ensuring the overall quality of the final product. This attention to detail at every manufacturing stage is essential for producing reliable and high-performance nitinol materials.
Quality Control and Testing Processes
By implementing these advanced techniques and processes, nitinol can be used in various real-world applications, from medical devices to aerospace components. The enhanced material properties allow for greater flexibility, durability, and resistance to corrosion, making it an ideal choice for industries with demanding requirements. With the ability to meet various industrial demands, nitinol has become a go-to material for engineers and manufacturers looking for high-performance solutions.
Nitinol in Action: Real-World Applications

Nitinol Wire Properties in Surgical Tools
Nitinol wire's properties make it an ideal material for surgical tools. It offers flexibility and a shape memory effect that allows for minimally invasive procedures. Nitinol's superelasticity and durability ensure that surgical tools can withstand repeated use, making them a reliable choice for medical professionals.
Nitinol's unique properties also make it an excellent choice for orthodontic braces. The flexibility and shape memory effect of nitinol wire allows the braces to apply gentle, continuous pressure to shift teeth into their proper position without causing discomfort to the patient. Additionally, the superelasticity and durability of nitinol ensure that the braces can withstand the forces exerted during orthodontic treatment, providing a reliable and long-lasting solution for patients seeking to improve their dental alignment.
Nitinol Alloys in Orthodontic Braces
The use of nitinol alloys in orthodontic braces has revolutionized dentistry, providing patients with a more comfortable and efficient treatment option. Nitinol's unique properties, such as its flexibility and shape memory effect, allow for the gradual realignment of teeth without the need for frequent adjustments, leading to faster results and improved patient satisfaction.
Nitinol Components in Engineered Systems
Due to their exceptional material properties, Nitinol components are increasingly used in diverse industries. This versatile metal is prized for its tensile strength, flexibility, and shape memory effect, making it ideal for creating innovative and reliable solutions.
Nitinol's applications span a wide range, including:
- Robotics: Actuators and sensors benefit from nitinol's precise movement and responsiveness.
- Aerospace: Intricate components rely on nitinol's strength and durability in demanding environments.
- Medical devices: Stents and guidewires leverage nitinol's flexibility and shape memory for minimally invasive procedures.
The biocompatibility of nitinol further enhances its suitability for medical applications, ensuring patient safety and recovery.
Nitinol'sa unique combination of properties has made it a cornerstone material in modern engineering and healthcare.
Future Innovations and Trends in Nitinol Applications
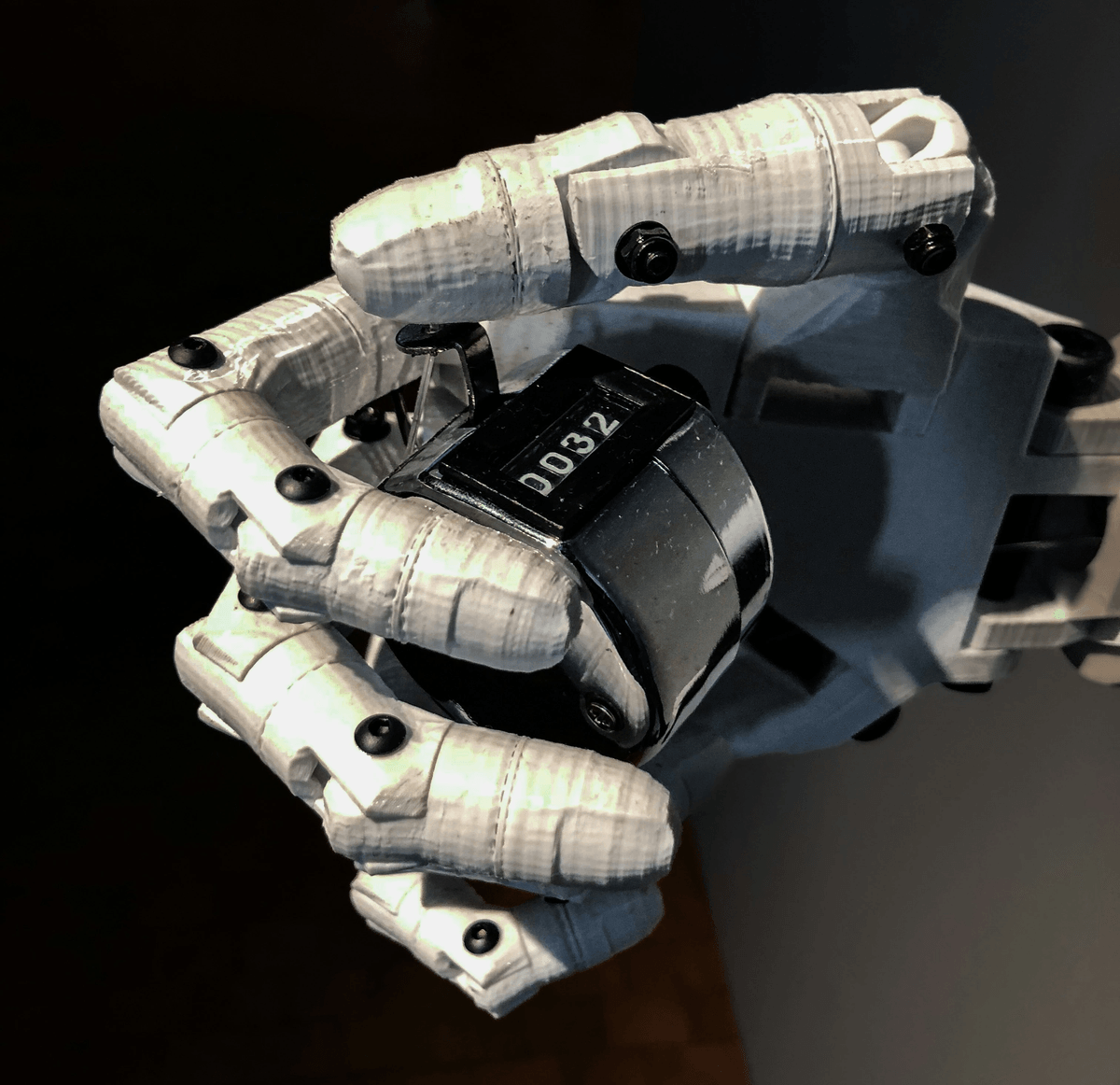
Advancements in Biomedical Engineering
As the demand for minimally invasive medical procedures continues to grow, nitinol material properties are at the forefront of advancements in biomedical engineering. Nitinol's unique shape memory effect and superelasticity make it an ideal material for developing innovative medical devices and implants, such as stents and guidewires. These applications benefit from nitinol's ability to adapt to various shapes and sizes within the human body, providing patients with improved treatment options.
Nitinol in Robotics and Automation
In robotics and automation, nitinol's flexibility and durability are driving significant innovation. Nitinol wire properties in robotic actuators allow for precise and efficient movement, making it an essential component in developing advanced robotic systems. Additionally, nitinol's superelasticity enables robots to perform complex tasks with enhanced agility, paving the way for groundbreaking advancements in automation technology.
Nitinol's impact on robotics and automation extends beyond just performance benefits. Its lightweight nature and corrosion resistance make it a sustainable choice for long-term use in robotic applications. By utilizing nitinol in robotic systems, engineers can contribute to reducing the environmental impact of automation technology, aligning with the growing demand for eco-friendly solutions in various industries. As the focus on sustainability grows, nitinol's role in robotics and automation will be crucial in meeting these environmental objectives.
Sustainable Solutions and Environmental Impact
Nitinol, a shape-memory alloy, is increasingly recognized as a sustainable material due to its exceptional properties. Its longevity and recyclability make it a valuable asset in various industries, contributing to a more circular economy.
Nitinol's positive environmental impact is evident in several key areas:
- Reduced waste: Its durability and recyclability minimize the material sent to landfills.
- Eco-friendly manufacturing: Ongoing research into sustainable production processes enhances nitinol's environmental profile.
- Healthcare sustainability: Its application in medical devices can reduce the frequency of replacements, thereby decreasing medical waste.
By harnessing the potential of nitinol, we can develop innovative solutions that protect our planet while advancing technology.
Nitinol's Role in Driving Technological Advancements
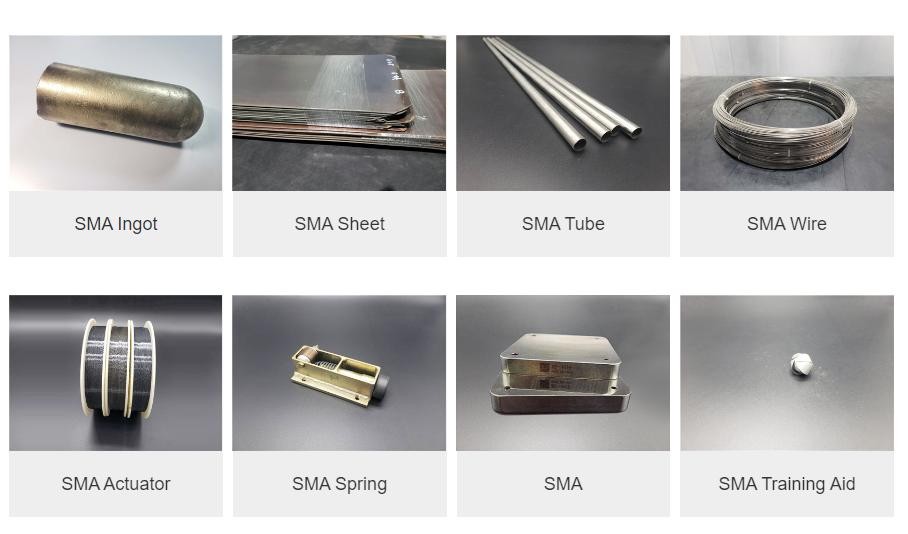
Nitinol material properties offer various applications, from biomedical devices to aerospace engineering, showcasing its incredible versatility and potential. The unique shape memory effect, superelasticity, and high tensile strength make nitinol a game-changer in various industries.
Harnessing the Power of Nitinol Material Properties
Nitinol's exceptional properties enable the creation of innovative medical devices and implants, such as stents and guidewires, revolutionizing patient care and treatment outcomes. Its shape memory effect allows for minimally invasive procedures, enhancing patient comfort and recovery.
Using nitinol in robotics and automation has opened up new possibilities for precise and efficient movement systems, leading to manufacturing and industrial automation advancements. Its flexibility and durability make it an ideal material for next-generation technologies.
Building a Sustainable Future with Nitinol Applications
By utilizing nitinol's unique properties in sustainable solutions, such as energy-efficient actuators and environmentally friendly manufacturing processes, we can contribute to a more eco-friendly future. With proper quality control measures and testing processes, nitinol applications can be optimized for minimal environmental impact.
In conclusion, the remarkable characteristics of nitinol material properties have paved the way for groundbreaking innovations in technology and healthcare. As we explore its potential in diverse fields, nitinol will undoubtedly play a crucial role in shaping our future advancements and sustainability efforts.