Introduction
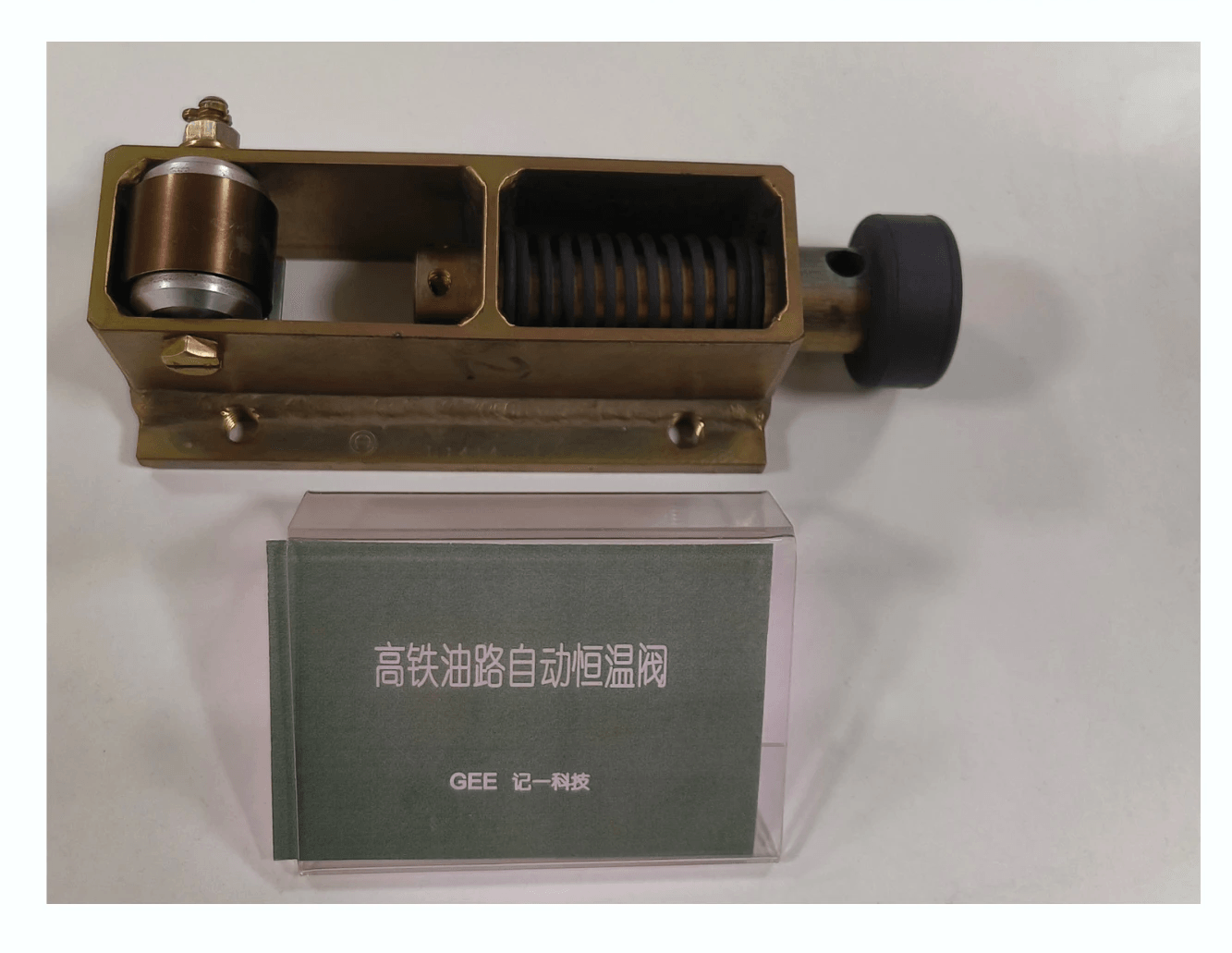
Nitinol actuators, also known as shape memory alloy wire actuators, are a fascinating innovation in the field of engineering and robotics. These actuators are built from Nitinol, a unique alloy with shape memory properties that allow it to return to a predetermined shape when subjected to the appropriate stimulus. Understanding the technical information behind Nitinol linear actuators is crucial for unlocking their full potential in various applications.
Understanding Nitinol Actuators
Actuators built from Nitinol are capable of producing mechanical motion through the application of heat, making them incredibly versatile for use in various industries. The ability of Nitinol to remember and return to its original shape allows for precise and controlled movement, making it an ideal choice for applications where accuracy is paramount.
Why Nitinol Actuators are Important
The unique properties of Nitinol make it an essential component in the development of advanced medical devices, robotics, and aerospace technology. The ability of Nitinol actuators to respond rapidly to external stimuli makes them invaluable for applications where speed and precision are critical.
Exploring the Response Time of Nitinol Actuators
One of the key factors that sets Nitinol actuators apart is their rapid response time. Understanding how fast a Nitinol actuator can react to changes in temperature or stress and strain is essential for optimizing its performance in real-world applications.
The Science Behind Nitinol Actuators

Actuators built from Nitinol, a nickel-titanium alloy, are known for their unique shape memory properties and superelasticity. The composition of Nitinol alloys typically consists of nearly equal parts of nickel and titanium, resulting in a material that can remember its original shape even after being deformed. This allows for the creation of Nitinol Linear Actuators (2 way) that can respond rapidly to changes in temperature or stress.
Composition of Nitinol Alloys
Nitinol actuator technical information reveals that the precise composition of Nitinol alloys can vary slightly depending on the specific application requirements, but the most common formulation is around 55% nickel and 45% titanium. This balanced combination gives Nitinol its unique properties, making it an ideal material for actuators in various industries.
Nitinol alloys are known for their shape memory properties, meaning they can return to a predetermined shape after being deformed, which is a crucial feature for actuators. This unique ability allows Nitinol actuators to be used in a wide range of applications, from medical devices to aerospace technology. The combination of nickel and titanium in the alloy also gives Nitinol high strength and corrosion resistance, making it a durable and reliable material for actuator components.
Shape Memory Properties
The Shape Memory Alloy Wire used in Nitinol actuators allows them to return to their original shape when heated after being deformed. This property makes them highly versatile and suitable for a wide range of applications where precise and rapid movement is required.
Transformation Temperatures
Nitinol actuator technical information also includes details about transformation temperatures, which refer to the specific temperatures at which the alloy undergoes phase transitions. Understanding these transformation temperatures is crucial for designing actuators with predictable response times and performance characteristics.
Understanding these transformation temperatures is crucial for designing actuators with predictable response times and performance characteristics. By knowing the specific temperatures at which Nitinol undergoes phase transitions, engineers can tailor the alloy's properties to suit the requirements of different applications. This level of control allows for the creation of Nitinol actuators that are not only reliable but also highly efficient in their operation, providing a competitive edge in industries such as aerospace, automotive, and medical devices.
Applications of Nitinol Actuators
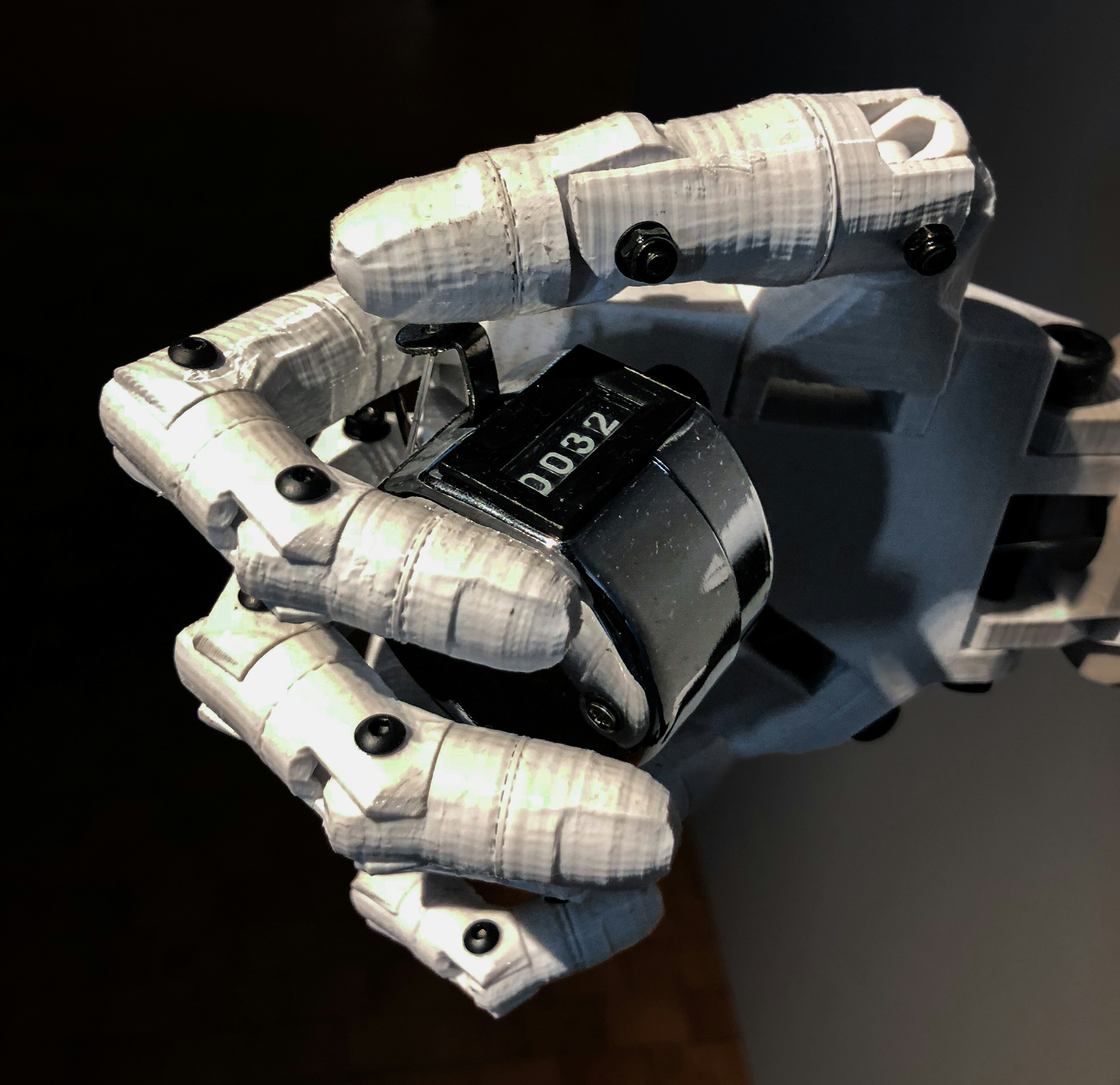
Nitinol actuators are revolutionizing various industries with their remarkable capabilities. Actuators built from Nitinol are finding extensive use in medical devices, robotics, and the aerospace industry due to their exceptional response time and durability.
Medical Devices
In the medical field, Nitinol linear actuators (2-way) are being used in a wide range of applications such as minimally invasive surgical tools, stents, and orthodontic braces. The shape memory alloy wire in these actuators allows for precise and reliable movement, making them ideal for intricate medical procedures.
In addition to the aforementioned applications, Nitinol linear actuators are also being utilized in advanced robotic surgical systems. These actuators provide the precise and controlled movement necessary for robotic arms to perform delicate procedures with a high level of accuracy. With the shape memory alloy wire, these actuators can withstand the repetitive movements required in robotic surgery, making them an essential component in this cutting-edge technology.
Robotics
Robotic systems are benefitting from the use of Nitinol actuator wire to achieve rapid and accurate movements. These actuators offer high force capabilities and can be designed to fit into compact spaces, making them perfect for powering robotic arms, grippers, and exoskeletons.
In addition to their compact size and high force capabilities, Nitinol actuator wire also offers the benefit of precise control, allowing robotic systems to perform delicate tasks with accuracy. This level of control is essential for applications such as surgical robots, where the ability to make precise movements is critical. Additionally, the durability of Nitinol ensures that these actuators can withstand the repetitive motions required in robotic applications without experiencing degradation in performance.
Aerospace Industry
In the aerospace industry, where precision and reliability are crucial, Nitinol actuator technical information is highly sought after. Actuators made from Nitinol alloys are being used in aircraft components like wing flaps and landing gear mechanisms due to their ability to withstand extreme conditions while delivering fast response times.
Nitinol actuators have revolutionized the aerospace industry by providing a level of precision and reliability never before seen. Their ability to withstand extreme conditions while delivering fast response times has made them an integral part of aircraft components like wing flaps and landing gear mechanisms. As a result, the use of Nitinol actuators has led to enhanced performance and efficiency across various aerospace applications.
Factors Affecting Nitinol Actuator Response Time

When it comes to understanding the response time of actuators built from Nitinol, several factors come into play. First and foremost is the impact of temperature on the speed at which these shape memory alloy wire actuators can actuate. This is due to the unique properties of Nitinol alloys, which exhibit a rapid response time when subjected to specific temperature changes. The relationship between temperature and the speed at which a Nitinol linear actuator (2 way) operates is crucial in determining its overall performance.
Temperature
The response time of Nitinol actuators is highly dependent on temperature fluctuations, with higher temperatures typically resulting in faster actuation speeds. The Shape Memory Alloy Wire used in these actuators undergoes a phase transformation when heated or cooled, enabling them to quickly change shape and respond to external stimuli. Understanding how different temperatures affect the speed at which these actuators operate is essential for optimizing their performance in various applications.
In addition to temperature, stress and strain also play a crucial role in the performance of Nitinol actuators. The amount of stress applied to the Shape Memory Alloy Wire can affect its response time and actuation speed. Similarly, the level of strain experienced by the wire during operation can impact its ability to change shape and function effectively. Therefore, it is important to consider not only temperature fluctuations but also stress and strain factors when optimizing the performance of these actuators for different applications.
Stress and Strain
Another key factor that affects the response time of Nitinol actuators is the level of stress and strain they are subjected to during operation. Actuator wire made from Nitinol alloys exhibits unique mechanical properties, including superelasticity and shape memory effects, which can influence their responsiveness under different levels of stress and strain. By carefully managing these mechanical forces, it is possible to enhance the speed and reliability of Nitinol actuators in real-world applications.
Material Quality
The quality of the Nitinol alloy used in actuator manufacturing also plays a significant role in determining their response time. High-quality materials with precise composition and manufacturing processes can result in more consistent and reliable performance, leading to faster actuation speeds and longer operational lifespans. Understanding how material quality impacts the response time of Nitinol actuators is crucial for ensuring their effectiveness across various industries.
High-quality Nitinol alloys are essential for ensuring the reliable and consistent performance of actuators. These materials undergo precise composition and manufacturing processes to achieve the desired properties, resulting in faster actuation speeds and longer operational lifespans. By using high-quality Nitinol alloys, industries can benefit from improved efficiency and durability in their various applications.
Testing and Measuring Nitinol Actuator Response Time
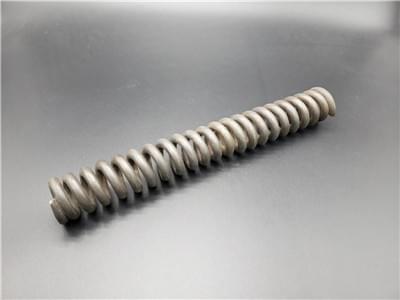
Laboratory Experiments
To determine how fast a Nitinol actuator responds, extensive laboratory experiments are conducted using actuators built from Nitinol. These experiments involve subjecting the Nitinol linear actuator (2 way) to varying stress levels and temperatures to gather technical information on its response time. The Shape Memory Alloy Wire is carefully monitored for its speed and efficiency in different conditions.
Real-world Applications
In real-world applications, the response time of Nitinol actuators is put to the test in practical settings. Engineers and researchers analyze how long does nitinol last under constant use and stress, as well as its performance in different environments. This hands-on approach provides valuable insights into the durability and reliability of actuator wire made from Nitinol.
Case Studies
Case studies play a crucial role in testing and measuring the response time of Nitinol actuators. These studies involve detailed examinations of actual scenarios where Nitinol actuators are utilized, providing concrete examples of their speed and effectiveness in various applications. By analyzing these case studies, researchers can gain a deeper understanding of how fast a Nitinol actuator can respond in practical situations.
(Note: The image shows a laboratory setting with scientists conducting experiments on a Nitinol actuator, representing the testing process described in this section.)
Enhancing Nitinol Actuator Response Time
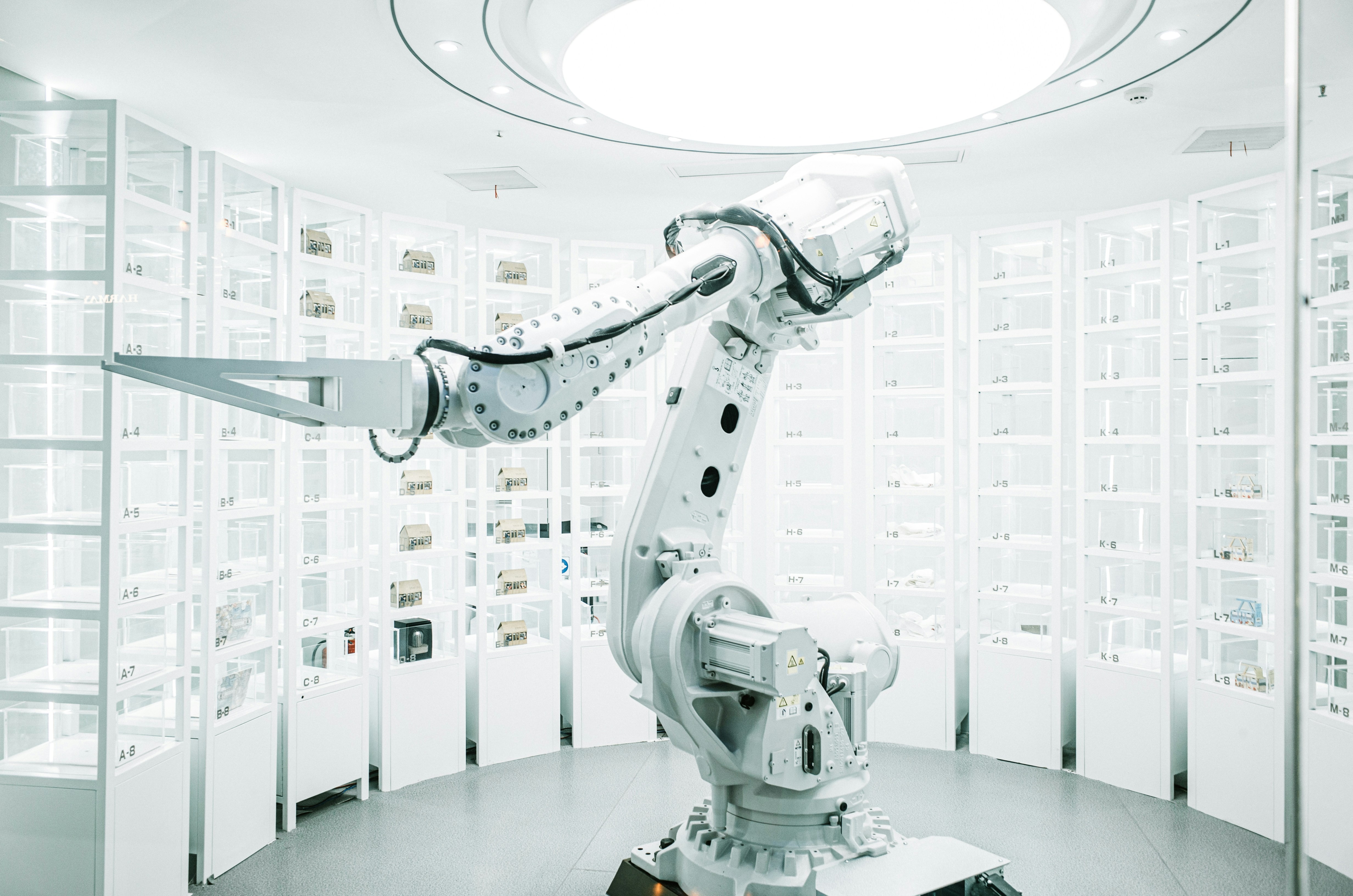
When it comes to enhancing the response time of actuators built from Nitinol, GEE SMA has been at the forefront of innovation. By developing advanced techniques and technologies, GEE SMA has significantly improved the speed at which Nitinol actuators operate. Their cutting-edge solutions have revolutionized industries such as medical devices, robotics, and aerospace by providing faster and more efficient actuation.
GEE SMA's Innovations
GEE SMA's innovations in Nitinol actuator technology have resulted in remarkable advancements in response time. Through extensive research and development, they have optimized the design and composition of Nitinol alloys to achieve faster actuation speeds. Their expertise in shape memory properties and transformation temperatures has allowed them to create Nitinol linear actuators (2 way) that exhibit rapid response times, setting a new standard in the industry.
Industry Best Practices
In addition to GEE SMA's innovations, there are industry best practices that can further enhance the response time of Nitinol actuators. Utilizing high-quality shape memory alloy wire and implementing precise manufacturing processes are essential for achieving optimal performance. By adhering to these best practices, companies can ensure that their Nitinol actuators deliver exceptional speed and reliability in various applications.
Future Developments
Looking ahead, the future of Nitinol actuator technology holds even more exciting prospects for enhancing response time. Ongoing research into material quality, stress and strain factors, as well as temperature optimization will continue to drive improvements in actuation speed. With a focus on continuous innovation, the development of next-generation Nitinol actuators is poised to further push the boundaries of how fast a Nitinol actuator can operate.
Remember that when it comes to achieving rapid response with nitinol actuators, staying updated on the latest advancements from industry leaders like GEE SMA is crucial for realizing their full potential.
Conclusion
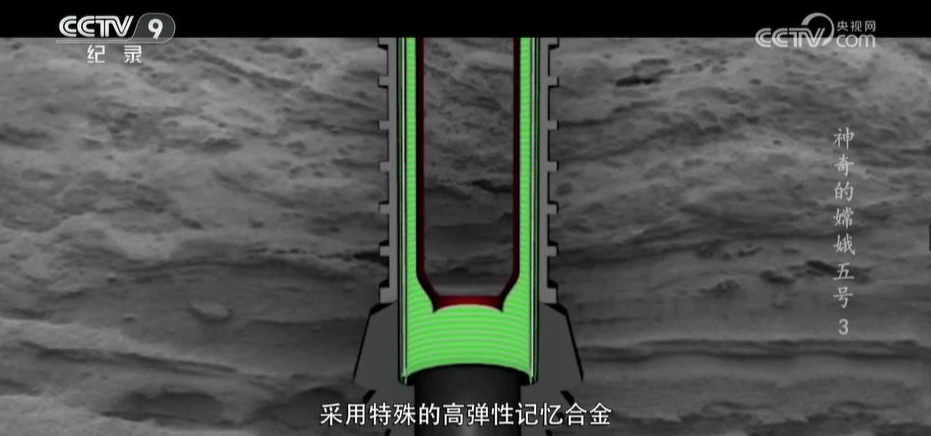
Nitinol actuators are revolutionizing the field of robotics and medical devices with their rapid response time and shape memory properties. Actuators built from Nitinol offer unparalleled performance, making them a popular choice in various industries. GEE SMA is committed to quality and innovation, ensuring that Nitinol actuators continue to push boundaries and realize their full potential.
Achieving Rapid Response with Nitinol Actuators
The technical information on Nitinol linear actuators (2 way) reveals that they can respond at impressive speeds, making them ideal for applications where quick, precise movements are required. The shape memory alloy wire used in these actuators allows them to return to their original shape when heated, resulting in fast and efficient performance. How fast is a Nitinol actuator? With Nitinol actuators, speed is not an issue.
Realizing the Potential of Nitinol Alloys
Actuator wire made from Nitinol alloys has proven to be durable and long-lasting, withstanding the rigors of demanding applications without compromising its performance. The transformation temperatures of Nitinol alloys ensure that these actuators maintain their shape memory properties over extended periods, making them a reliable choice for various industries.
GEE SMA's Commitment to Quality and Innovation
GEE SMA's dedication to quality is evident in their continuous efforts to enhance the response time of Nitinol actuators through innovative solutions and industry best practices. Their commitment to pushing the boundaries of what is possible with Nitinol alloys sets them apart as leaders in the field, ensuring that the full potential of these remarkable materials is realized.