Introduction
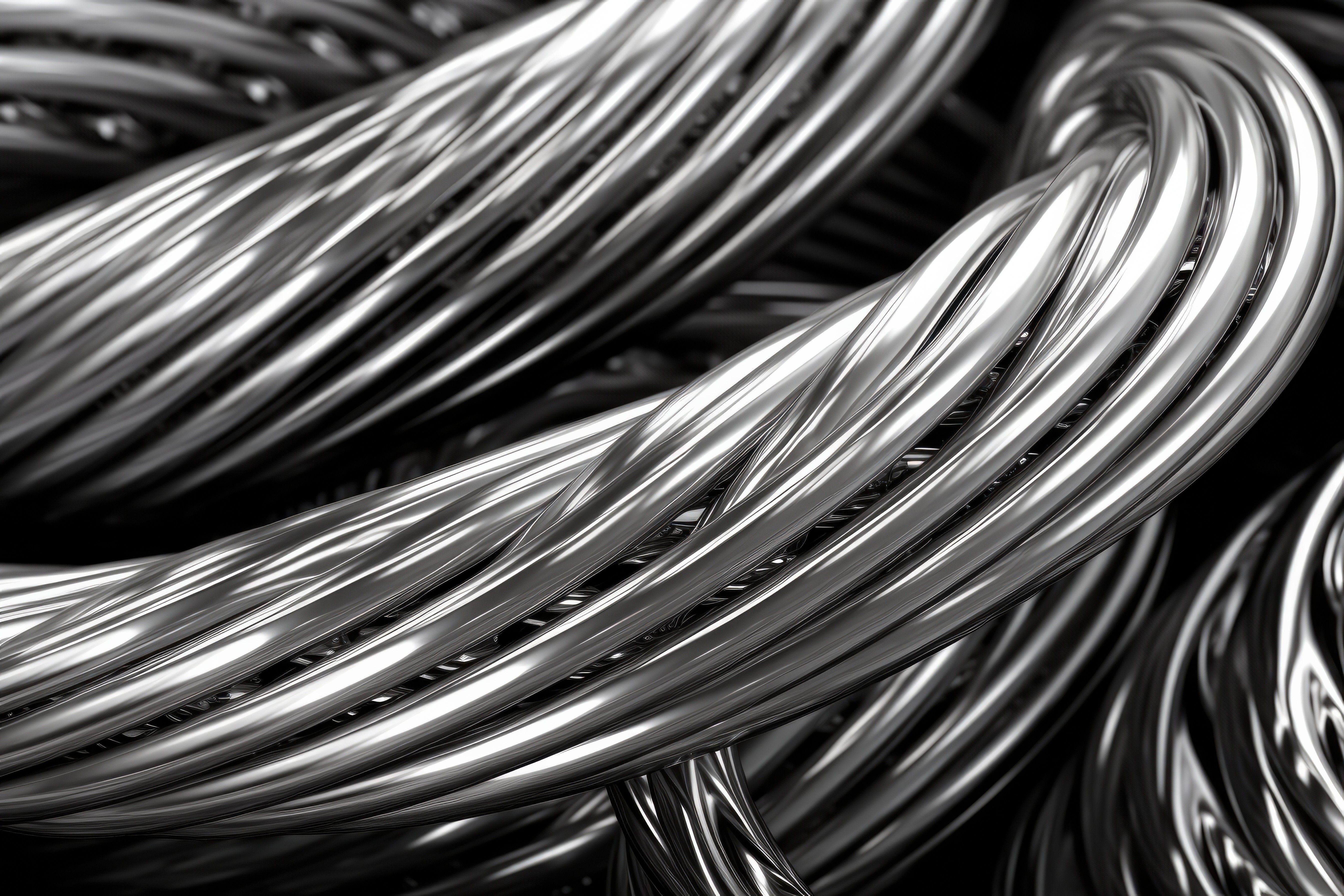
In advanced materials, super elastic nitinol wire has emerged as a game-changer. This unique alloy, known as nitinol nickel titanium, possesses remarkable properties, making it a sought-after choice in various industries. From its shape memory alloy (SMA) capabilities to its high flexibility and resilience, nitinol wire has proven versatile and valuable.
Understanding Super Elastic Nitinol Wire
Nitinol wire is a shape memory alloy that can return to its original shape after deforming, earning it the nickname memory metal. This remarkable property allows for innovative medical devices, automotive engineering, and consumer electronics applications.
Benefits of Nitinol Shape Memory Alloys
Superelastic nitinol wire is a remarkable material prized for its unique properties, making it a highly versatile choice across various applications. Here are some of its key attributes:
- Superelasticity: Nitinol can undergo significant deformation (up to 8% strain) and return to its original shape upon unloading. This property allows for intricate designs and precise movements in medical devices.
- High Resilience: Nitinol can withstand repeated bending and flexing without permanent deformation, making it ideal for applications requiring durability and reliability.
- Biocompatibility: Nitinol is non-toxic and compatible with the human body, making it a safe choice for medical implants and devices.
Superelastic nitinol wire's exceptional flexibility, resilience, and biocompatibility make it an invaluable material for the medical field and beyond.
Applications of Nitinol Wire
From minimally invasive surgical tools to orthodontic braces, nitinol wire finds extensive use in the medical industry due to its biocompatibility and shape memory capabilities. Beyond healthcare, this versatile material is also utilized in automotive and aerospace engineering for components requiring high strength-to-weight ratios.
Properties of Super Elastic Nitinol Wire
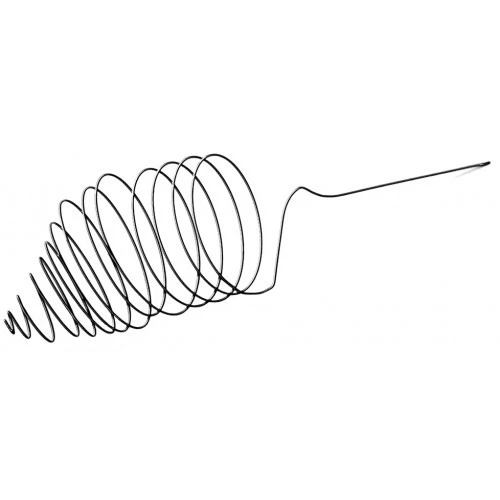
Super elastic nitinol wire, also known as nitinol nickel titanium, possesses remarkable properties that make it highly sought after in various industries. Its unique composition of nickel and titanium results in a shape memory alloy (SMA) that exhibits exceptional flexibility and resilience.
High Flexibility and Resilience
The super elastic nitinol wire can undergo substantial deformation while still returning to its original shape when the external force is removed. This property makes it ideal for applications requiring repetitive bending or twisting, such as medical devices and robotics.
The high flexibility and resilience of superelastic nitinol wire also make it an excellent choice for orthodontic braces. The wire can withstand the repeated bending and twisting required to adjust the position of teeth, providing a more comfortable experience for the wearer. Additionally, its biocompatibility ensures that it is safe to be in constant contact with the inside of the mouth, making it a reliable and durable option for orthodontic treatment.
Biocompatibility in Medical Devices
Nitinol's biocompatibility with the human body has revolutionized the medical device industry, allowing for the development of advanced stents, guidewires, and orthodontic wires that can be safely implanted within the body. This remarkable material's ability to resist corrosion and degradation in the harsh conditions of the body ensures that these devices remain effective and reliable over extended periods. As a result, patients can benefit from improved outcomes and reduced risks associated with medical procedures involving these innovative devices.
Corrosion Resistance
Nitinol wire exhibits excellent corrosion resistance due to its oxide layer, which forms naturally on its surface. This property maintains its integrity even when exposed to harsh environmental conditions, making it suitable for aerospace engineering and marine applications.
Nitinol wire is produced through a complex process involving precisely combining nickel and titanium in specific proportions. This alloy is subjected to heat treatments and mechanical processing to achieve the desired shape and properties. The result is a high-quality wire with exceptional corrosion resistance, making it an ideal choice for demanding applications in aerospace engineering and marine environments.
Production Process of Nitinol Wire
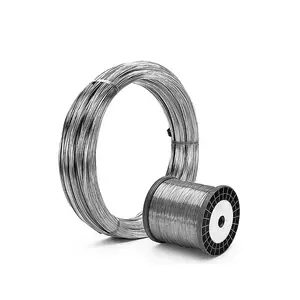
Nickel and Titanium Alloy Composition
The production of superelastic nitinol wire begins with the combination of nickel and titanium, forming a unique shape memory alloy (SMA) known for its remarkable flexibility and resilience. The precise ratio of nickel and titanium in the alloy composition determines the specific properties of the nitinol wire, making it suitable for various applications in different industries.
After the nickel and titanium are combined, the nitinol wire undergoes a unique heat treatment to set its shape memory properties. This involves heating the alloy to a specific temperature and then cooling it in a controlled manner. As a result, the nitinol wire can "remember" its original shape and return to it after being deformed, which is a key characteristic that makes it ideal for various applications. This transformation process also enhances the superelastic properties of the nitinol wire, allowing it to withstand repeated bending and flexing without permanent deformation.
Shape Memory Alloy Transformation
Once the nickel and titanium are combined, the shape memory alloy undergoes a transformation process that allows it to remember its original shape even after deforming. This unique characteristic gives nitinol wire its remarkable super elasticity, making it an ideal material for medical devices, robotics, and other innovative applications that require flexibility and durability.
After the transformation process, the nitinol wire can be further enhanced through heat treatment and wire drawing. Heat treatment involves subjecting the alloy to specific temperatures to optimize its superelastic properties, while wire drawing involves pulling the material through progressively smaller dies to achieve the desired diameter and surface finish. These additional steps contribute to nitinol wire's overall quality and performance, making it even more suitable for demanding applications in various industries.
Heat Treatment and Wire Drawing
After the transformation process, the nitinol alloy is subjected to heat treatment to enhance its properties further, such as biocompatibility in medical devices and corrosion resistance in harsh environments. The alloy is then carefully drawn into wires with precise dimensions to meet the specific requirements of different applications, ensuring consistent quality and performance.
By understanding the intricate production process of superelastic nitinol wire, manufacturers can ensure they are sourcing high-quality materials that meet industry standards and performance expectations. This knowledge also empowers businesses to explore innovative solutions across various industries by harnessing the unique capabilities of nitinol alloys.
Quality Standards for Nitinol Wire

GEE SMA implements stringent quality control measures throughout the production process to ensure the highest quality of superelastic nitinol wire. From raw material inspection to final product testing, every step is meticulously monitored to guarantee the reliability and performance of the nitinol nickel-titanium alloy.
GEE SMA's Quality Control Measures
GEE SMA employs advanced testing equipment and techniques to assess their nitinol products' mechanical properties, dimensional accuracy, and surface integrity. This commitment to quality control allows them to deliver shape memory alloys that meet the most demanding specifications and standards across various industries.
In addition to utilizing advanced testing equipment and techniques, GEE SMA's quality control measures include rigorous inspection processes at every production stage. This ensures that each nitinol product undergoes thorough scrutiny for potential defects or irregularities, guaranteeing the highest quality and reliability. By implementing such comprehensive quality control measures, GEE SMA maintains its reputation as a trusted provider of shape memory alloys that consistently meet and exceed industry standards.
ASTM International Standards
In line with industry best practices, GEE SMA adheres to the rigorous standards set by ASTM International for nitinol nickel-titanium alloys. These comprehensive guidelines cover everything from chemical composition and mechanical properties to manufacturing processes, ensuring that all nitinol wire products meet the highest levels of quality and performance.
In addition to adhering to ASTM International standards, GEE SMA also conducts regular internal and third-party testing to ensure the quality and performance of our nitinol wire products. This commitment to ongoing testing and certification procedures ensures product integrity and customer satisfaction. By staying proactive in our approach to quality control, we can confidently stand behind the reliability of our nitinol nickel-titanium alloys.
Certification and Testing Procedures
Before being released into the market, GEE SMA's nitinol wire undergoes extensive certification and testing procedures to validate its conformance with industry standards. This includes fatigue testing, tensile strength evaluation, and corrosion resistance assessments, providing customers with peace of mind regarding the reliability of their nitinol shape memory alloy solutions.
After the nitinol wire passes the rigorous certification and testing procedures, GEE SMA ensures that it meets all necessary industry standards before being released into the market. This commitment to quality and reliability gives customers confidence in the performance of their nitinol shape memory alloy solutions, knowing that they have been thoroughly vetted and tested. By prioritizing certification and testing, GEE SMA demonstrates its dedication to providing high-quality products that meet the needs of various industries.
Applications of Nitinol Wire in Various Industries
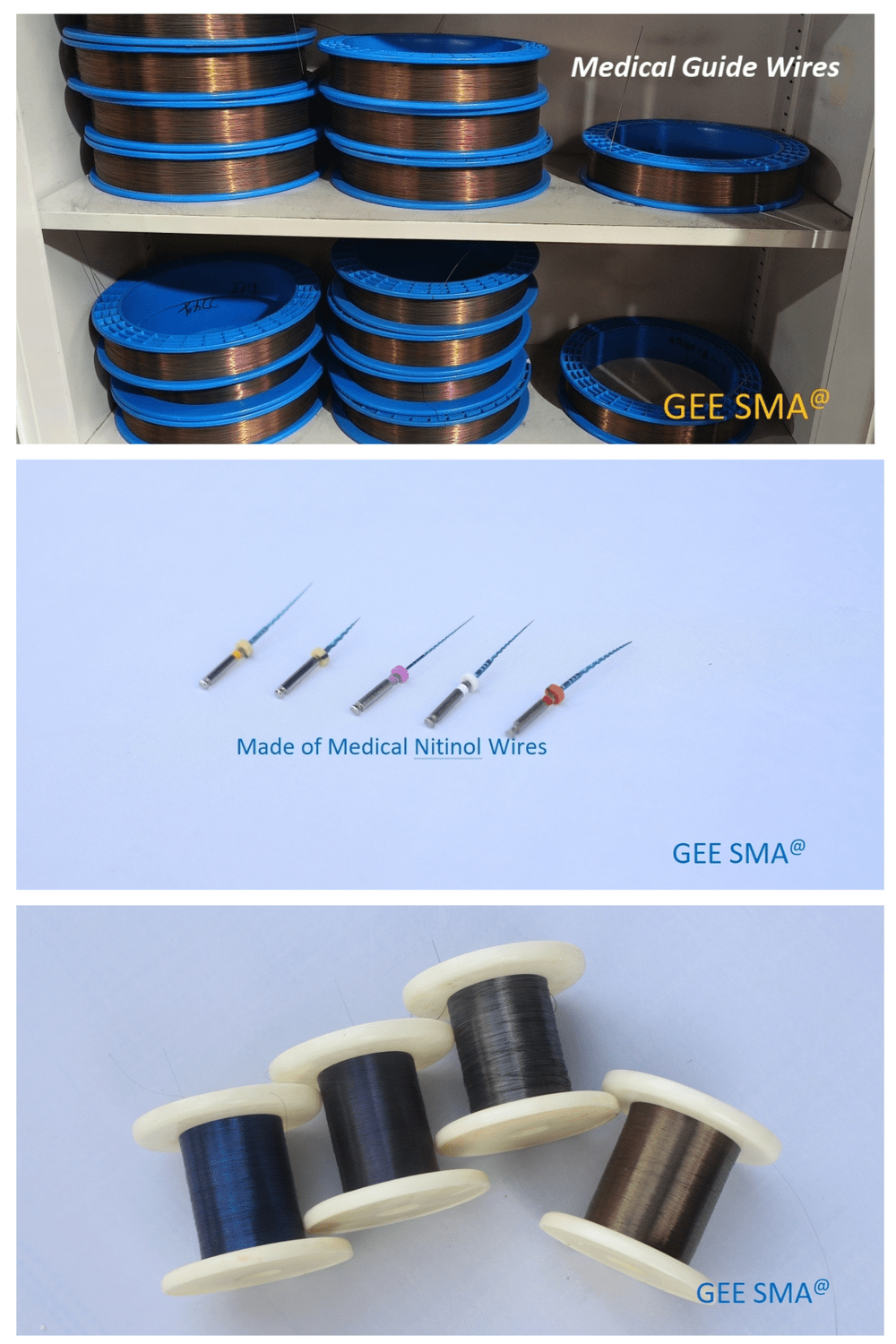
Nitinol wire, also known as super elastic nitinol wire, is a versatile material with unique properties that find applications in a wide range of industries. From medical devices to consumer electronics, the use of nitinol nickel-titanium shape memory alloys continues to expand, offering innovative solutions and driving technological advancements.
Medical Devices and Equipment
Nitinol wire has become a staple in the medical field due to its unique combination of biocompatibility and superelasticity. Here's how it benefits various medical applications:
- Minimally Invasive Surgery: Nitinol's shape memory allows it to be compressed into a smaller form for insertion through catheters. Once in place, it returns to its original shape, providing support and navigation within blood vessels without causing damage. Guide wires and stents are prime examples of this application.
- Orthodontics: The superelasticity of nitinol makes it ideal for orthodontic braces. It can exert gentle and consistent pressure on teeth, promoting gradual movement.
- Implantable Devices: Nitinol's biocompatibility and flexibility suit various implantable devices. Its ability to withstand repeated stress makes it a reliable choice for long-term use within the body.
Nitinol wire's remarkable properties are revolutionizing minimally invasive surgery, orthodontics, and implantable devices, offering patients improved treatment options with less risk and discomfort.
Automotive and Aerospace Engineering
Nitinol nickel-titanium alloys are increasingly incorporated into automotive and aerospace applications due to their high strength-to-weight ratio and resilience. In these industries, nitinol wire is used for actuators in engine components, adaptive wing structures, and various sensors that require precise movement or shape retention under extreme conditions.
Consumer Electronics and Robotics
The unique properties of superelastic nitinol wire make it an attractive choice for consumer electronics and robotics. It is commonly used in small-scale actuators for smart devices, such as mobile phones and wearable technology, where space constraints demand compact yet powerful components. Additionally, robotics engineers utilize nitinol wire to mimic muscle movement in soft robotic systems.
Nitinol wire is used in consumer electronics and robotics and medical devices. Its superelasticity makes it ideal for use in minimally invasive surgical tools such as catheters and guidewires. The ability of nitinol wire to return to its original shape after deformation allows for precise control and maneuverability within the human body, making it a valuable asset in the healthcare industry.
With its remarkable adaptability across diverse sectors, the demand for high-quality nitinol wire continues to grow as industries seek innovative solutions that leverage the unique capabilities of shape memory metals like nitinol nickel-titanium alloys.
Sourcing High-Quality Nitinol Wire
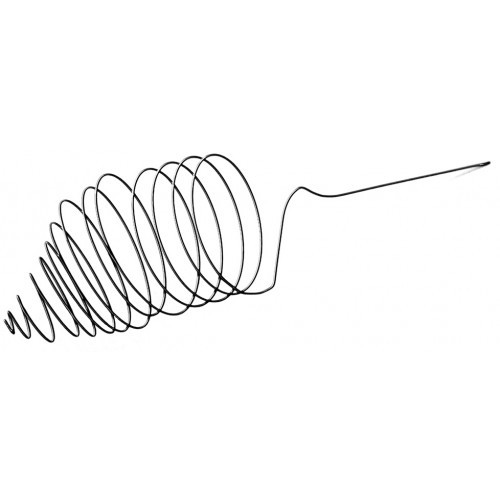
Partnering with reliable manufacturers is crucial when sourcing high-quality, super-elastic nitinol wire. Look for companies with a proven track record in producing top-notch nitinol nickel-titanium alloys. By collaborating with trusted suppliers, you can ensure the quality and consistency of your nitinol wire for various applications.
Partnering with Reliable Manufacturers
Seek manufacturers specializing in nickel and titanium alloys, particularly shape memory alloys (SMAs) like nitinol wire. These experts understand the intricacies of creating high-quality super-elastic nitinol wire and can provide valuable insights into its production and properties. By working closely with reputable manufacturers, you can access a reliable supply of nitinol wire tailored to your specific needs.
Understanding Material Specifications
To make informed decisions about sourcing nitinol wire, it's essential to understand the material specifications involved in its production. This includes knowledge of shape memory metals, SMA alloys, and the unique properties of superelastic nitinol wire. With a clear understanding of these specifications, you can effectively communicate your requirements to manufacturers and ensure that the product meets your expectations.
GEE SMA's Customization Capabilities
Consider partnering with GEE SMA for your nitinol wire needs. They offer customization capabilities that cater to diverse industry requirements. Whether you need specialized dimensions, surface finishes, or performance characteristics for your super elastic nitinol wire, GEE SMA can deliver tailored solutions to your specifications. Their expertise in shaping shape memory alloy products makes them a valuable partner in unlocking the full potential of nitinol alloys.
Unlock Innovative Solutions with Nitinol Wire
When choosing the right nitinol supplier, it's crucial to prioritize quality, reliability, and customization capabilities. Partnering with a reputable manufacturer like GEE SMA ensures access to high-quality, super-elastic nitinol wire that meets stringent industry standards. By harnessing the potential of nitinol alloys, industries can unlock innovative solutions that leverage the unique properties of nickel and titanium shape memory metals.
Choosing the Right Nitinol Supplier
Selecting a nitinol supplier is a critical decision. Here are some key factors to consider when choosing a supplier:
- Quality Control Measures: Ensure the manufacturer prioritizes strict quality control procedures to guarantee consistent material properties. Nitinol's unique properties are susceptible to its composition and processing, so consistent quality is essential.
- ASTM International Standards: Verify the supplier adheres to ASTM International standards for nitinol nickel titanium. These standards ensure the material meets specific mechanical and physical properties, guaranteeing material reliability for your application.
- Certification and Testing: Look for a supplier implementing rigorous certification and testing procedures for its nitinol products. To meet industry standards, reputable suppliers will have their materials certified by third-party organizations.
By partnering with a supplier that prioritizes these factors, you can be confident you are sourcing top-notch shape memory alloy materials that will perform consistently and reliably in your applications.
Harnessing the Potential of Nitinol Alloys
The versatility of SMa alloys opens up a world of possibilities across various industries, from medical devices and equipment to automotive and aerospace engineering, consumer electronics, and robotics. The unique properties of superelastic nitinol wire make it an invaluable material for innovative solutions requiring high flexibility, resilience, biocompatibility, and corrosion resistance.
By leveraging the remarkable capabilities of nitinol wire, businesses can push the boundaries of what's possible in product design and development. Whether designing minimally invasive medical devices or enhancing the performance of automotive components, nitinol's shape memory alloy transformation offers unparalleled opportunities for creating cutting-edge solutions that meet the demands of today's rapidly evolving industries.