Introduction
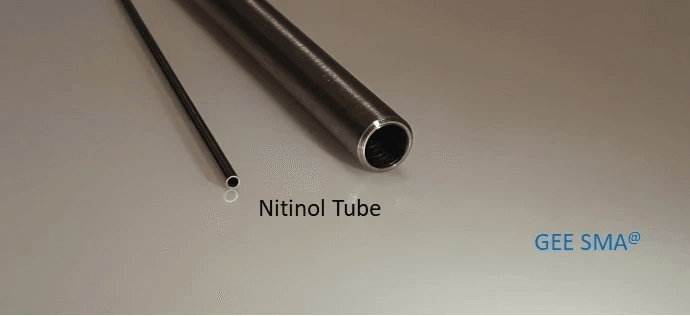
Nitinol, a remarkable nickel-titanium alloy, has captured the attention of various industries due to its unique properties such as shape memory and superelasticity. This material has found applications in fields ranging from medical devices to robotics, making nitinol processing an essential aspect of modern manufacturing. As we delve deeper into the world of nitinol, we will explore how to produce nitinol, its machining capabilities, and the intricacies involved in manufacturing components like stents.
Understanding Nitinol and its Applications
Nitinol stands out for its ability to return to a predetermined shape when heated above a certain temperature. This property opens doors for innovative applications, particularly in the medical sector where devices like stents require precision and reliability. By understanding these applications, we can appreciate why nitinol processing is crucial for ensuring that this versatile material meets the demands of various industries.
The Importance of Nitinol Processing
The processing of nitinol is not just about shaping the metal; it’s about unlocking its potential through careful manipulation of its properties. Effective nitinol processing techniques ensure that the desired characteristics—like strength and flexibility—are achieved without compromising integrity. Given that many products rely on these attributes, understanding how to produce nitinol efficiently becomes paramount in maintaining quality standards across applications.
Overview of Nitinol Processing Techniques
There are several techniques employed in nitinol processing that cater to different end-use requirements—from heat treatment methods that enhance performance to cold working techniques that improve formability. Additionally, surface modification approaches play a critical role in tailoring the material's interaction with other substances or environments it may encounter during use. With advancements in technology, exploring these diverse methods not only answers questions like “Can nitinol be machined?” but also highlights innovations in manufacturing practices.
The Basics of Nitinol Processing
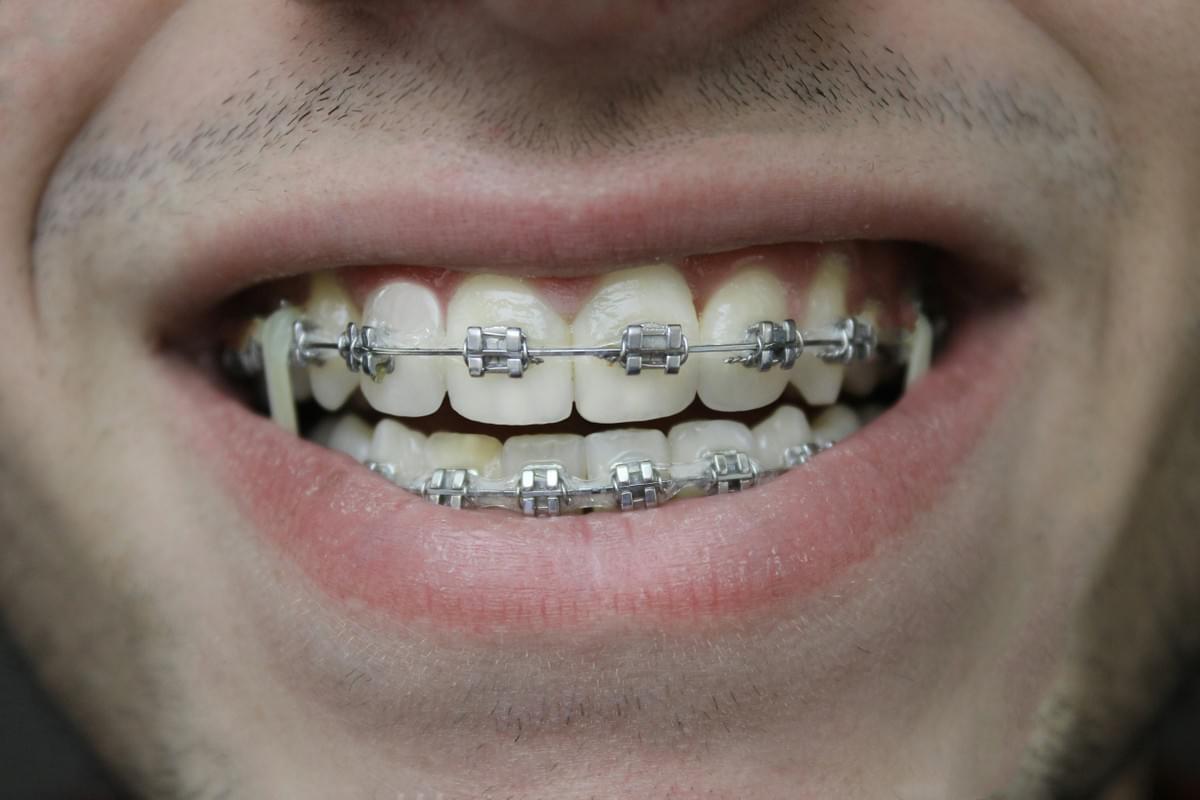
Nitinol, a unique alloy of nickel and titanium, stands out due to its remarkable shape memory and superelastic properties. These attributes make it an ideal candidate for various applications, particularly in the medical field, where precision is paramount. Understanding nitinol processing is essential for harnessing these properties effectively.
What is Nitinol and Its Unique Properties
Nitinol’s defining characteristics are its ability to return to a predetermined shape when heated and its remarkable elasticity under stress. This means that nitinol can be deformed at room temperature but will revert back to its original form upon heating, making it invaluable in applications like stents and guidewires. Such unique properties stem from the specific crystalline structure of nitinol, which changes with temperature variations.
How to Produce Nitinol?
Producing nitinol involves several critical steps that ensure the alloy's unique properties are preserved throughout the process. Initially, nickel and titanium are combined in precise ratios before undergoing processes like melting, casting, and solidification. The subsequent heat treatment plays a vital role in determining the final characteristics of the material—this is where understanding how to produce nitinol becomes crucial for achieving desired performance standards.
The Role of GEE SMA in Nitinol Processing
GEE SMA (Shape Memory Alloys) technology enhances nitinol processing by improving control over the material's thermal and mechanical behavior during production. This advanced method allows manufacturers to fine-tune properties such as transformation temperatures and mechanical strength more effectively than traditional techniques. By integrating GEE SMA into nitinol processing workflows, manufacturers can achieve higher precision levels necessary for critical applications like how are nitinol stents manufactured?
Common Techniques in Nitinol Processing
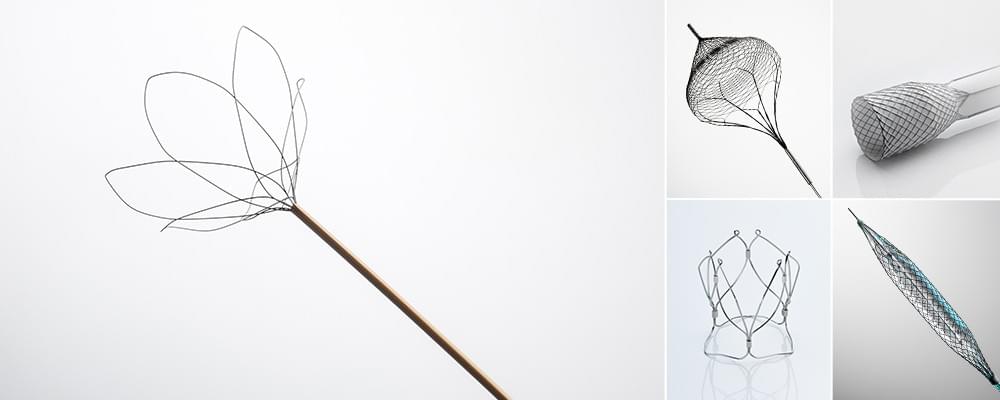
Nitinol processing involves a variety of techniques that help to optimize its unique properties for different applications. Understanding these methods is crucial for manufacturers looking to harness the full potential of this remarkable alloy. This section will explore some of the most common techniques, including heat treatment, cold working, and surface modification.
Heat Treatment Methods
Heat treatment is a fundamental technique in nitinol processing that significantly influences its transformation characteristics and mechanical properties. By carefully controlling temperature and time, manufacturers can induce phase changes in nitinol, allowing it to exhibit its shape memory effect and superelasticity. This process not only enhances performance but also tailors the material for specific applications, such as medical devices like stents.
Different heat treatment methods exist, including solution annealing and aging processes. Each method serves a particular purpose; for instance, solution annealing helps dissolve unwanted phases while aging strengthens the material by precipitating fine particles within it. Understanding how to produce nitinol with optimal properties through these heat treatments is essential for manufacturers aiming to meet stringent industry standards.
Cold Working Techniques
Cold working techniques are another vital component of nitinol processing that allow for enhanced strength and improved dimensional control without compromising the material's unique characteristics. These methods involve deforming the material at room temperature, which introduces dislocations that increase strength through strain hardening while still maintaining some degree of superelasticity.
Common cold working processes include rolling, drawing, and bending—each offering distinct advantages depending on the desired final shape or application. However, one must be cautious; excessive cold work can lead to brittleness or loss of functionality in certain contexts. Thus, understanding how to balance cold working with other processing methods is key in producing high-quality nitinol components.
Surface Modification Approaches
Surface modification approaches play an essential role in enhancing the performance and longevity of nitinol products across various applications. Techniques such as coating or texturing can improve biocompatibility when manufacturing medical devices like stents or enhance corrosion resistance for use in harsh environments.
By modifying surfaces at a microscopic level, manufacturers can tailor attributes such as friction coefficient or wear resistance—a critical consideration when addressing how are nitinol stents manufactured? The right surface modifications not only extend product life but also ensure optimal functionality during operation.
Furthermore, advancements in nanotechnology have opened new avenues for surface treatments that provide even more significant improvements over traditional methods. As innovations continue to emerge within this field, understanding effective surface modification strategies will remain paramount for those involved in nitinol processing.
Machining Nitinol: Is It Possible?
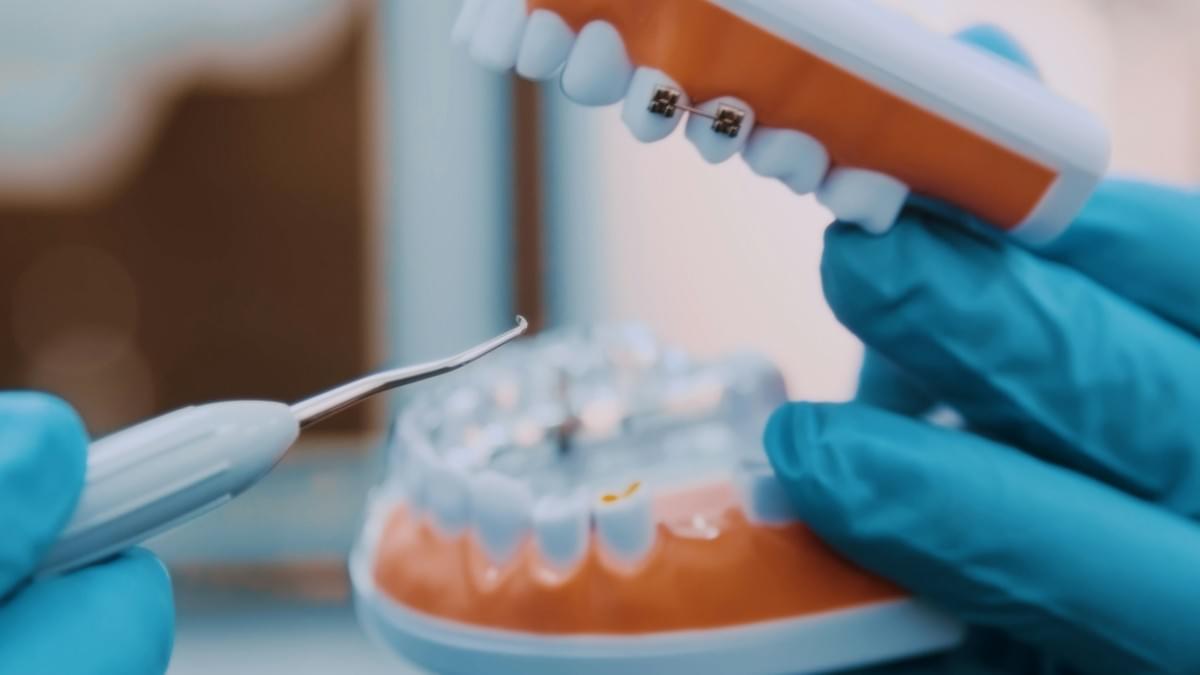
When it comes to machining nitinol, the answer is a bit of a mixed bag. Nitinol, known for its unique shape memory and superelastic properties, poses distinct challenges compared to traditional metals. However, with the right techniques and tools, machining nitinol can indeed be accomplished effectively.
Can Nitinol Be Machined?
Yes, nitinol can be machined, but it requires specialized knowledge and equipment due to its unique characteristics. The alloy's high strength and toughness make it resistant to conventional machining methods, which can lead to tool wear and poor surface finishes if not managed properly. Understanding how to produce nitinol with optimal properties is crucial for successful machining; improper processing can result in undesirable outcomes during fabrication.
Best Practices for Machining Nitinol
To achieve the best results when machining nitinol, certain best practices should be followed. First off, using sharp cutting tools made from materials like carbide or ceramic will help minimize wear and improve precision during the process. Additionally, implementing proper cooling techniques—such as using a water-soluble coolant—can mitigate heat buildup that may affect the material’s properties during machining.
Another key aspect is to maintain slow feed rates while machining nitinol; this helps reduce stress on both the tool and the workpiece. It's also advisable to conduct regular inspections of both tools and parts throughout the process to ensure quality control—especially important when considering how nitinol stents are manufactured where precision is paramount.
Challenges in Nitinol Machining
Despite its machinable nature, several challenges arise when working with nitinol that manufacturers must navigate carefully. One major hurdle is its tendency for work hardening; as you machine it, the material becomes harder and more difficult to cut efficiently over time. This characteristic can lead to increased tool wear rates and potential failures if not addressed properly.
Moreover, achieving tight tolerances while working with nitinol requires meticulous attention since any deviations could compromise functionality in applications like medical devices or stents—after all, understanding why nitinol is so expensive often comes down to these stringent manufacturing requirements. Lastly, operators need extensive training in handling this complex alloy; without proper knowledge of how to produce nitinol correctly from start to finish, even experienced machinists may struggle with this fascinating material.
Manufacturing Nitinol Stents
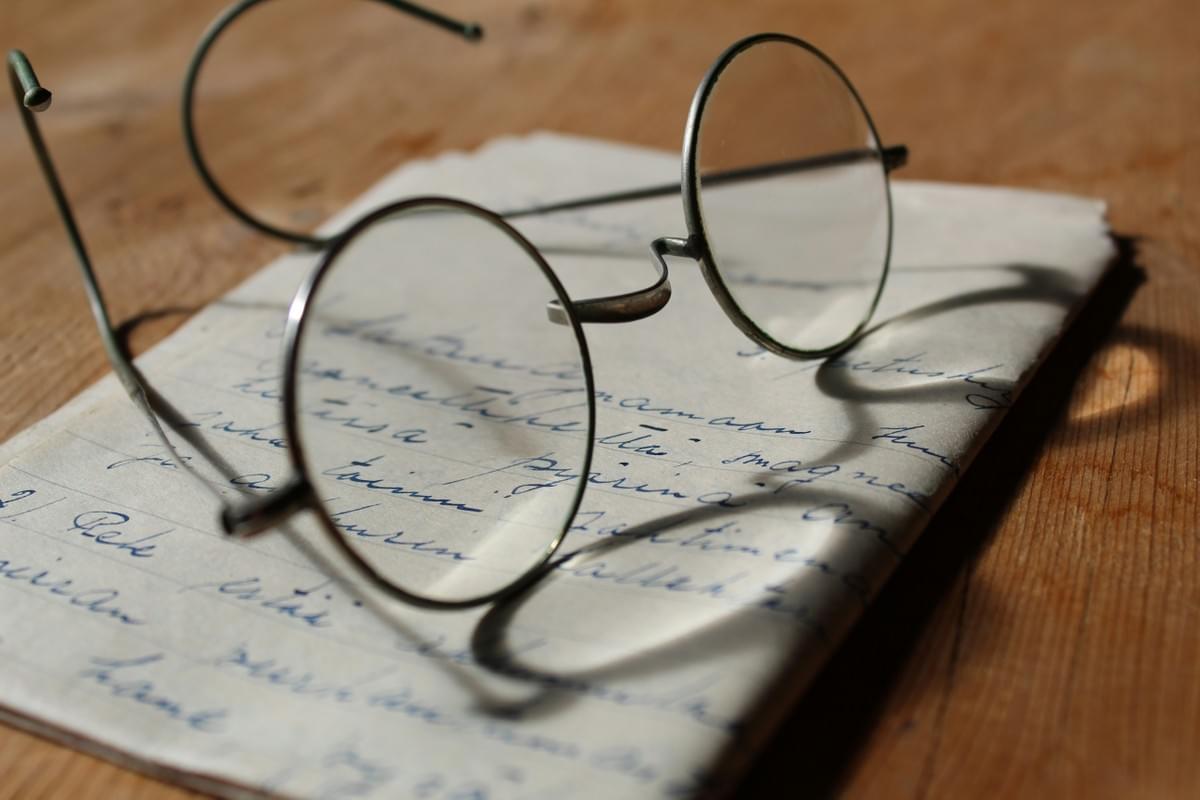
Nitinol stents are marvels of modern medical engineering, combining the unique properties of nitinol with advanced manufacturing techniques. Understanding how these stents are manufactured is crucial for ensuring their performance in the body. The process involves meticulous steps that transform raw nitinol into life-saving devices used in various medical applications.
How Are Nitinol Stents Manufactured?
The manufacturing of nitinol stents begins with the production of nitinol itself, which raises the question: how to produce nitinol? Typically, this involves a series of alloying processes that create a shape memory alloy with specific properties. Once the nitinol is produced, it undergoes a series of heat treatments and cold working techniques to achieve the desired mechanical characteristics before being shaped into stent forms through laser cutting or other precise methods.
After shaping, the stents often require additional processing to enhance their surface properties and ensure biocompatibility. This can include surface modification approaches like passivation or coating to prevent corrosion and promote healing post-implantation. The final stage involves rigorous testing and quality control measures to ensure that each stent meets stringent medical standards before it can be used in patients.
The Importance of Precision in Manufacturing
Precision in manufacturing nitinol stents cannot be overstated; even minor deviations can lead to catastrophic failures when implanted in patients. The unique properties of nitinol—such as its superelasticity—demand exacting tolerances throughout every stage of production. This precision ensures that when deployed within blood vessels, these stents expand correctly and maintain their structural integrity under physiological conditions.
Moreover, given that many applications for these devices involve delicate procedures such as angioplasty, any errors during manufacturing could compromise patient safety or treatment efficacy. Therefore, manufacturers invest heavily in advanced technologies and skilled labor to achieve high levels of accuracy throughout the entire process—from how are nitinol stents manufactured to final inspections before distribution.
Innovations in Nitinol Stent Production
The field of nitinol processing is continually evolving, with innovations aimed at improving both performance and cost-effectiveness for manufacturers and healthcare providers alike. Recent advancements include 3D printing techniques which allow for more complex designs tailored specifically for individual patient anatomies—a significant leap forward from traditional methods. These innovations not only enhance patient outcomes but also address questions like why is nitinol so expensive by potentially lowering costs through streamlined production processes.
Additionally, researchers are exploring new alloys and treatments that could further enhance the mechanical properties of nitinol while reducing its price tag over time. With ongoing research into bioresorbable materials combined with traditional nitinol structures, future iterations may offer even greater benefits without compromising safety or efficacy. As we look ahead at trends shaping this industry, one thing remains clear: advancements in how we manufacture these critical devices will continue to revolutionize patient care.
The Cost of Nitinol: Understanding the Price Tag
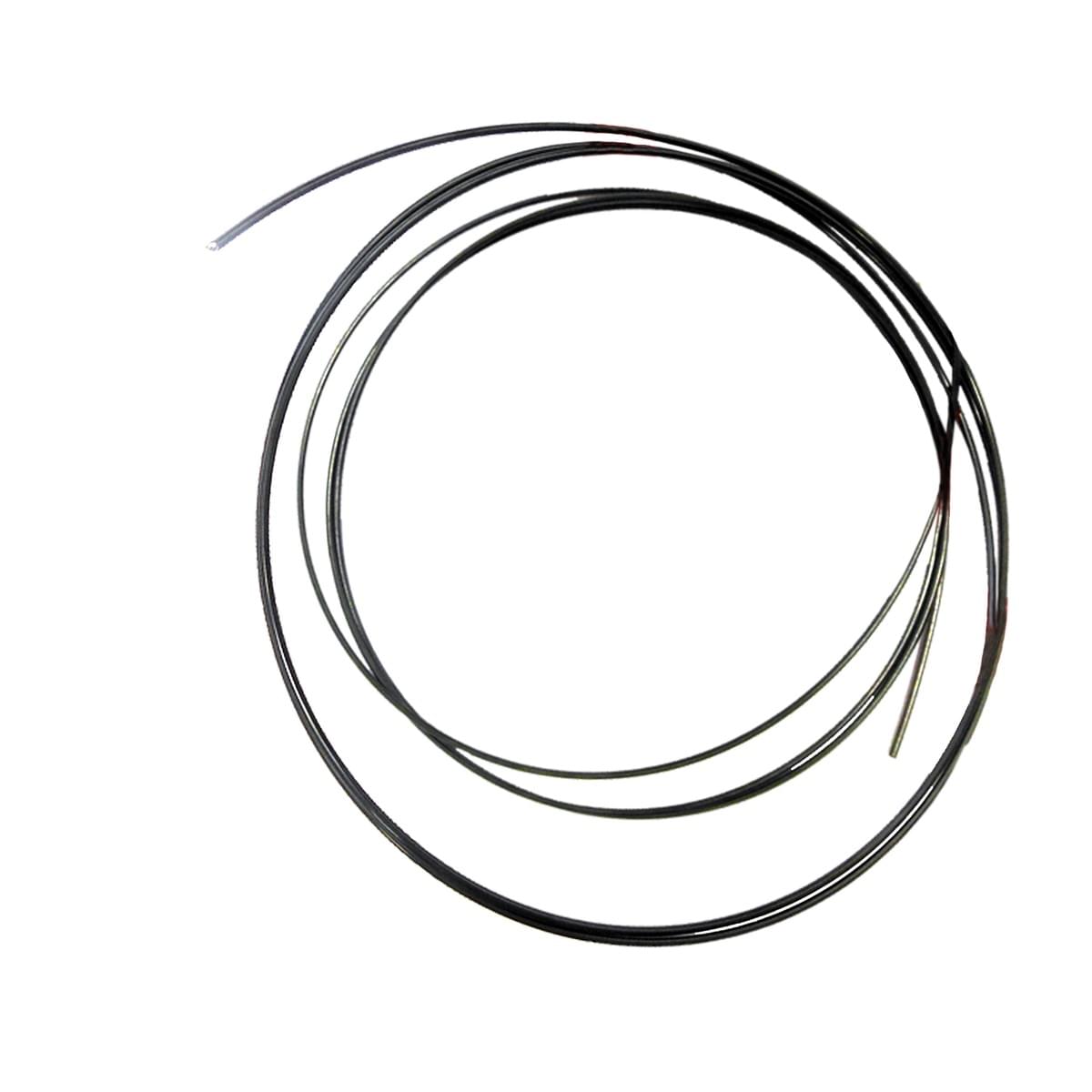
Nitinol, a remarkable alloy of nickel and titanium, is renowned for its unique properties such as shape memory and superelasticity. However, this innovation comes at a cost, leading many to ponder: why is nitinol so expensive? Understanding the reasons behind its high price tag is crucial for manufacturers and end-users alike, especially when considering applications in medical devices like stents.
Why Is Nitinol So Expensive?
The high cost of nitinol can be attributed to several factors, starting with its complex production process. To answer the question of how to produce nitinol?, manufacturers must engage in intricate metallurgical processes that require specialized equipment and skilled labor. Additionally, the raw materials—nickel and titanium—are themselves costly commodities that fluctuate in price based on market conditions.
Another reason contributing to nitinol's steep price is the stringent quality control measures required during manufacturing. Given its critical applications in areas like medical devices, especially how are nitinol stents manufactured?, ensuring consistency and reliability is non-negotiable. This rigorous testing adds another layer of expense that ultimately gets passed down to consumers.
Lastly, the relatively low volume of nitinol produced compared to other metals leads to economies of scale not being fully realized. With limited production runs focused on niche markets like medical technology or aerospace applications, costs remain elevated. Thus, when asking why is nitinol so expensive?, it becomes clear that both material science intricacies and market dynamics play significant roles.
Factors Affecting Nitinol Pricing
Several key factors influence the pricing structure of nitinol beyond just production costs. For instance, demand fluctuations in sectors such as healthcare significantly affect pricing strategies for manufacturers who specialize in nitinol processing. The growing usage of nitinol in advanced medical devices means that as more companies enter this market space, competition may either drive prices up or down depending on supply chain efficiencies.
Another factor is regulatory compliance costs associated with producing biocompatible materials like nitinol for use in human bodies—think about how are nitinol stents manufactured? These regulations ensure safety but add an additional financial burden on producers who must navigate complex legal waters while maintaining product quality standards.
Lastly, technological advancements can also impact pricing by either reducing production costs or creating new applications that drive demand higher than supply can meet. As research continues into better ways to process this unique material—such as exploring whether can nitinol be machined?—the industry may see shifts in both availability and cost structures over time.
Cost-Effective Solutions for Nitinol Sourcing
While understanding why nitrionl is so expensive provides insight into its market dynamics, finding cost-effective solutions for sourcing remains essential for many businesses involved in its application. One approach involves establishing long-term relationships with reliable suppliers who can offer bulk purchasing options at discounted rates—this strategy often leads to lower per-unit costs while ensuring consistent quality throughout various batches.
Another solution lies within innovative processing techniques aimed at minimizing waste during production cycles related to how to produce nitinol?. By optimizing these processes through advanced manufacturing technologies or lean methodologies, companies can significantly reduce their overall expenses without compromising product integrity or performance characteristics.
Finally, exploring alternative materials that mimic some properties of nitinol could provide additional avenues for cost savings while still achieving desired outcomes within specific applications such as stent manufacturing processes mentioned earlier. While these alternatives might not replicate every feature found within true shape-memory alloys like Nitinol itself; they could serve as viable substitutes under certain conditions where budget constraints prevail.
Conclusion
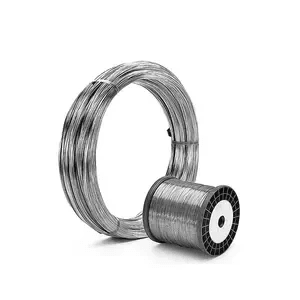
In summary, the world of nitinol processing is as fascinating as it is complex. From understanding how to produce nitinol to exploring its unique properties, this material continues to revolutionize various industries, particularly in medical applications like stents. As we move forward, the importance of refining these processes cannot be overstated, especially with the rising demand for high-quality nitinol products.
Key Takeaways on Nitinol Processing
Nitinol processing involves several techniques that enhance its unique properties and make it suitable for various applications. A crucial aspect is understanding how to produce nitinol effectively; mastering this process ensures a consistent supply of this remarkable alloy. Additionally, exploring whether can nitinol be machined reveals both challenges and innovative solutions that are essential for manufacturers looking to leverage this material.
Future Trends in Nitinol Applications
The future of nitinol applications looks promising, with advancements in technology paving the way for new innovations. Industries are increasingly recognizing the potential benefits of using nitinol beyond traditional uses—think robotics and aerospace! As research continues into optimizing how are nitinol stents manufactured, we can expect even more tailored solutions that cater to specific needs across various sectors.
Enhancing Nitinol Processing with GEE SMA
One exciting development in enhancing nitinol processing comes from GEE SMA technology, which offers new avenues for improving production efficiency and product quality. By integrating GEE SMA into existing processes, manufacturers can address questions like why is nitinol so expensive? The result could potentially lower costs while maintaining high standards for performance and reliability across all applications of nitinol.