Introduction

When it comes to innovative and high-quality springs, the Micromatic Nitinol Spring stands out as a top contender in the market. This unique type of spring is crafted from Nitinol, a shape memory alloy known for its exceptional properties and performance. Offering superior flexibility, durability, and resilience, the Micromatic Nitinol Spring is a game-changer in various industries.
What is Micromatic Nitinol Spring?
The Micromatic Nitinol Spring is a type of Nitinol spring that is designed to exhibit shape memory behavior, allowing it to return to its original shape after deformation. This remarkable feature makes it ideal for applications that require precise and consistent performance under varying conditions.
Advantages of using Micromatic Nitinol Spring
One of the key advantages of using the Micromatic Nitinol Spring is its ability to withstand repeated deformations without experiencing permanent damage or fatigue. Additionally, its superelasticity and biocompatibility make it suitable for a wide range of demanding applications.
Common applications of Micromatic Nitinol Spring
From medical devices and automotive components to aerospace technologies, the Micromatic Nitinol Spring finds extensive use across diverse industries due to its exceptional performance and reliability.
Understanding Micromatic Nitinol Spring
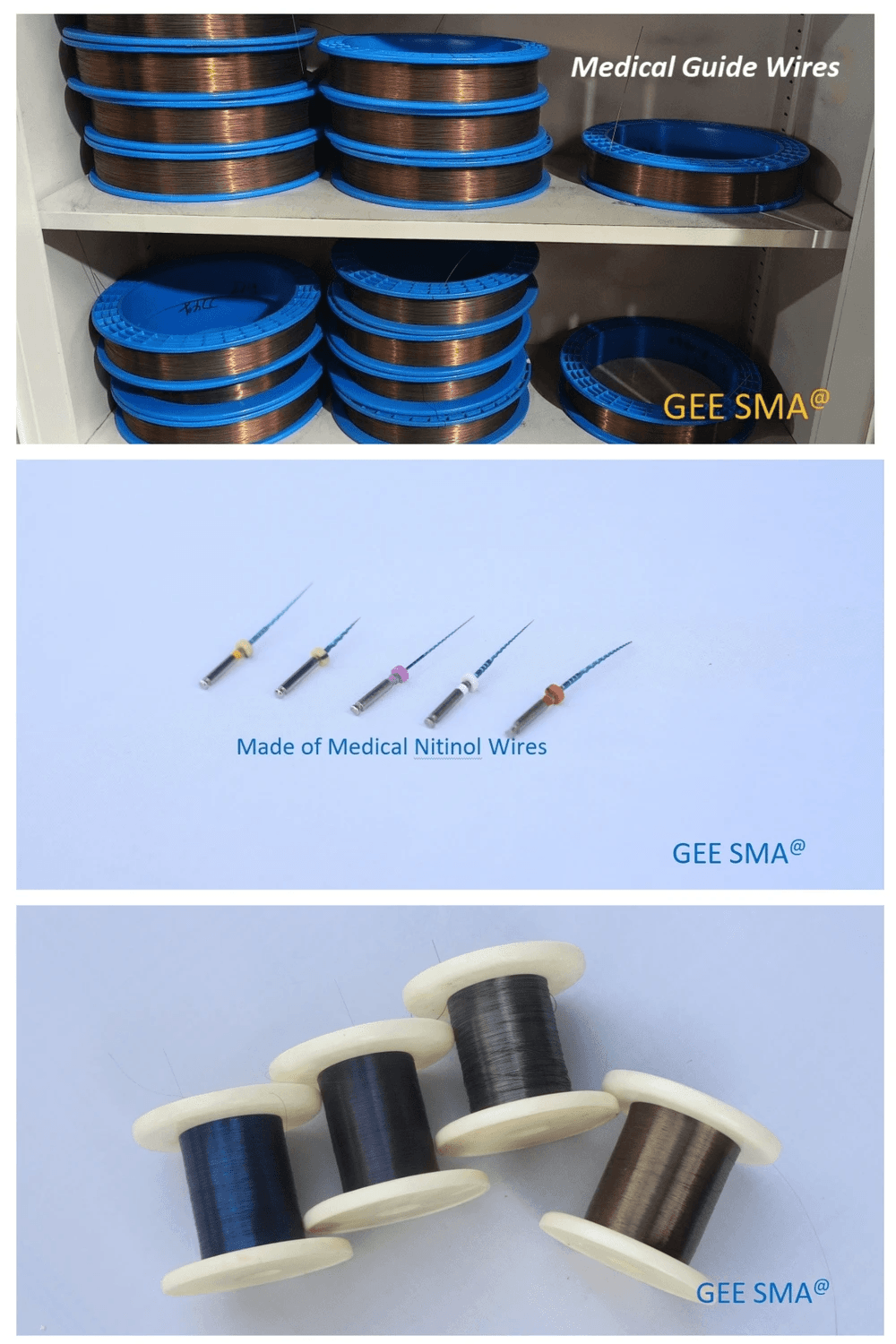
When it comes to understanding the Micromatic Nitinol Spring, it's essential to grasp its composition and properties. This remarkable spring is made from a nickel-titanium alloy, also known as Nitinol, which exhibits superelasticity and shape memory properties. This makes it an ideal material for applications requiring flexibility and resilience.
Composition and properties of Micromatic Nitinol Spring
The composition of the Micromatic Nitinol Spring typically consists of approximately 55% nickel and 45% titanium, giving it the unique ability to return to its original shape after deformation. This spring also boasts exceptional corrosion resistance, biocompatibility, and non-magnetic properties, making it suitable for a wide range of industries.
The unique composition of the Micromatic Nitinol Spring gives it a distinct advantage over traditional metal springs. With its high nickel and titanium content, this spring is able to withstand significant deformation and still return to its original shape, making it ideal for applications where repeated use is necessary. In addition, its exceptional corrosion resistance ensures a longer lifespan, while its biocompatibility makes it suitable for medical devices and implants. Its non-magnetic properties also make it a valuable component in industries where magnetic interference must be avoided.
Manufacturing process of Micromatic Nitinol Spring
The manufacturing process of the Micromatic Nitinol Spring involves several key steps, including alloy melting, hot or cold working, heat treatment, and shaping through various methods such as wire forming or laser cutting. This meticulous process ensures that the spring retains its desired shape memory and superelasticity characteristics.
Furthermore, the Micromatic Nitinol Spring undergoes rigorous quality control measures to ensure that it meets the highest standards of performance and reliability. This includes thorough testing for shape memory, superelasticity, and fatigue resistance to guarantee that the spring will maintain its functionality over countless cycles of use. These stringent quality checks are essential in delivering a product that consistently meets the demanding requirements of various industries.
Key features of Micromatic Nitinol Spring
One of the key features of the Micromatic Nitinol Spring is its ability to undergo significant deformation without permanent damage, making it highly durable for repetitive use. Additionally, its unique thermomechanical behavior allows for precise control over its shape recovery temperature, enabling tailored solutions for specific applications.
Furthermore, the Micromatic Nitinol Spring's exceptional fatigue resistance allows it to endure millions of cycles without compromising its performance, making it an ideal choice for high-demand applications in industries such as medical devices, aerospace, and automotive engineering. This durability and reliability make the Nitinol Spring a cost-effective solution for long-term use, reducing the need for frequent replacements and maintenance.
With a thorough understanding of the composition, manufacturing process, and key features of the Micromatic Nitinol Spring in mind, let's explore its diverse applications in various industries next!
Applications of Micromatic Nitinol Spring
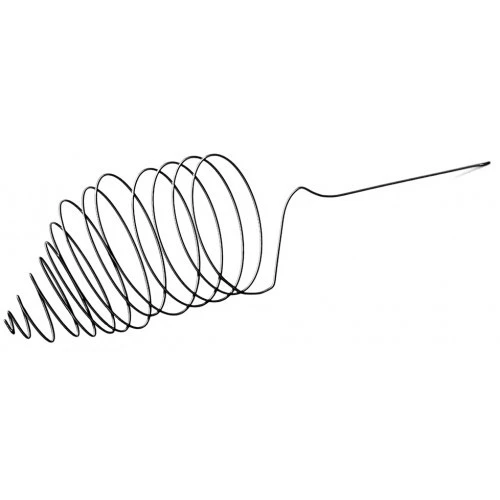
Medical industry applications
Micromatic Nitinol Spring is widely used in the medical industry for various applications such as orthodontic braces, stents, and catheter guide wires. Its superelasticity and shape memory properties make it ideal for minimally invasive medical procedures, providing patients with better comfort and faster recovery times.
Automotive industry applications
In the automotive industry, Micromatic Nitinol Spring is utilized in fuel injection systems, airbags, and seatbelt mechanisms. Its high fatigue resistance and corrosion resistance make it a reliable choice for critical automotive components, ensuring safety and longevity in vehicles.
Aerospace industry applications
Nitinol Micro-Springs are essential in the aerospace industry for applications like actuators, landing gear components, and satellite deployment mechanisms. The unique combination of lightweight construction and high strength-to-weight ratio makes them indispensable for space exploration and aircraft engineering.
By choosing Micromatic Nitinol Spring for your specific needs, you can benefit from its versatility across various industries while ensuring top-notch performance and reliability. Whether it's in the medical field, automotive sector, or aerospace domain, this innovative material offers unmatched advantages that cater to diverse application requirements. Remember to partner with GEE SMA for tailored solutions that meet your exact specifications.
NiTi Coil Spring: The Ultimate Guide
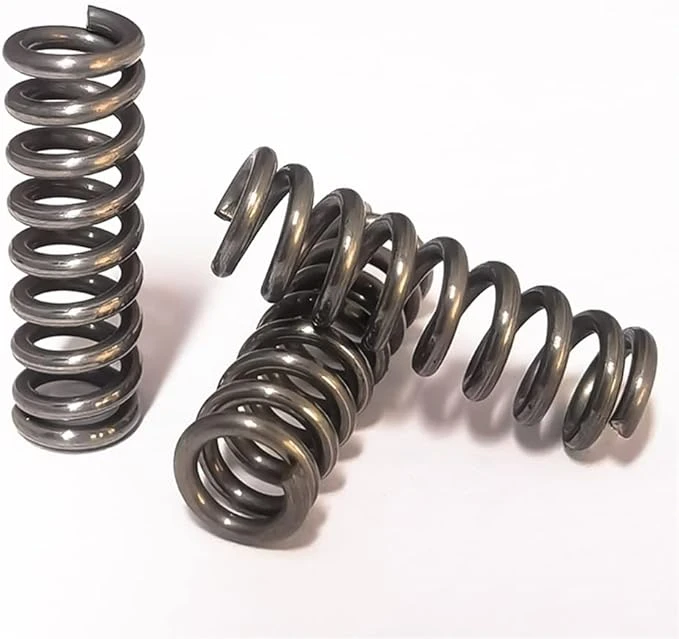
Characteristics of NiTi Coil Spring
NiTi Coil Spring, also known as Nitinol Micro-Springs, is a type of Nitinol SMA Shape Memory Spring that exhibits remarkable shape memory and superelasticity properties. These springs are composed of a nickel-titanium alloy, offering excellent corrosion resistance and biocompatibility, making them ideal for medical applications.
Advantages of using NiTi Coil Spring
The use of NiTi Coil Spring offers numerous advantages, including high fatigue resistance, precise control over force and displacement, and the ability to withstand extreme temperatures without losing functionality. Additionally, these springs provide unmatched durability and reliability in various demanding environments.
NiTi Coil Spring in various industries
NiTi Coil Springs find extensive use across diverse industries such as medical devices, automotive components, aerospace technology, and consumer electronics. Their unique combination of flexibility and resilience makes them indispensable for applications requiring consistent performance under varying conditions.
Remember to strategically incorporate these keywords into your content to enhance its visibility on search engines!
NiTi Adjustable Force Preformed Closed Coil Spring: A Comprehensive Overview
Features of NiTi Adjustable Force Preformed Closed Coil Spring
The NiTi Adjustable Force Preformed Closed Coil Spring is a versatile and reliable spring that offers adjustable force capabilities, making it suitable for a wide range of applications. With its unique design, this spring provides consistent and controlled force over a specified range, ensuring precision and efficiency in various systems.
Benefits of using NiTi Adjustable Force Preformed Closed Coil Spring
One of the key benefits of the NiTi Adjustable Force Preformed Closed Coil Spring is its ability to maintain constant force levels even under changing conditions, making it ideal for applications where precision and reliability are crucial. Additionally, its adjustable force feature allows for customization based on specific requirements, providing flexibility and performance optimization.
Diverse applications of NiTi Adjustable Force Preformed Closed Coil Spring
The NiTi Adjustable Force Preformed Closed Coil Spring finds extensive use in industries such as medical devices, automotive systems, aerospace technology, and more. Its adaptability to varying force requirements makes it an essential component in devices like stents, actuators, valves, and other intricate mechanisms where consistent force delivery is essential for optimal functionality.
GEE SMA: Crafting High-Quality Nitinol Springs
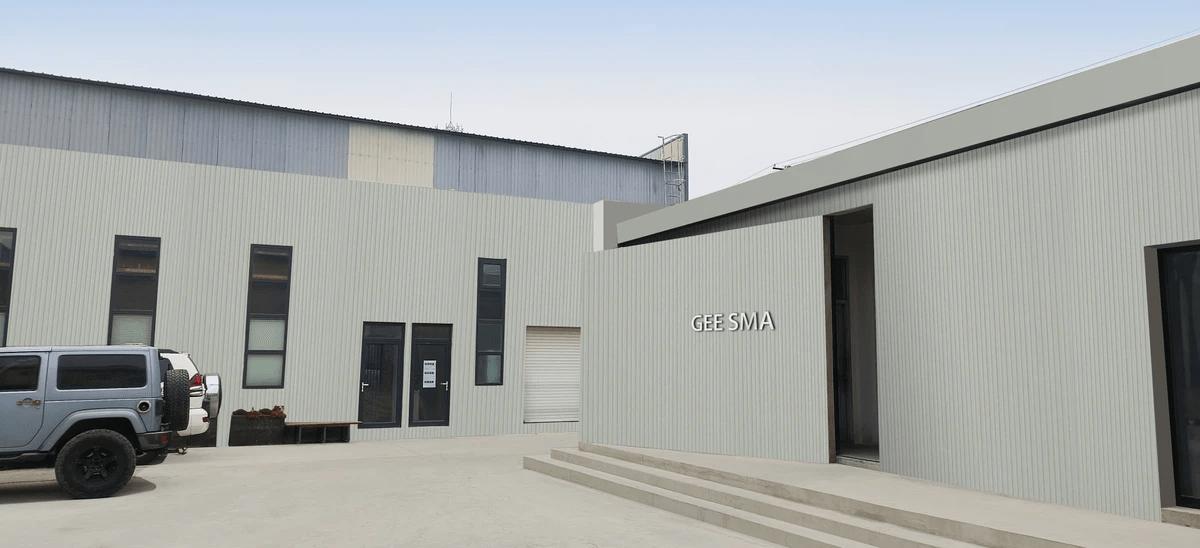
GEE SMA is a leading manufacturer of high-quality Nitinol springs, including Micromatic Nitinol Spring, NiTi Coil Spring, and NiTi Adjustable Force Preformed Closed Coil Spring. With decades of experience in the industry, GEE SMA has established itself as a trusted provider of advanced Nitinol spring solutions.
About GEE SMA
GEE SMA specializes in the production of Nitinol Shape Memory Alloys (SMA) and functional materials. Their team of experts is dedicated to delivering innovative and reliable Nitinol springs that meet the unique requirements of their customers across various industries.
Production of Nitinol Shape Memory Alloys
GEE SMA utilizes state-of-the-art manufacturing processes to produce high-quality Nitinol Shape Memory Alloys. Their advanced production facilities ensure precision and consistency in the creation of Nitinol springs, resulting in superior performance and durability.
Tailoring Nitinol functional materials to meet customer requirements
At GEE SMA, customization is key. They work closely with their clients to tailor Nitinol functional materials to meet specific design and performance needs. Whether it's for medical devices, automotive components, or aerospace applications, GEE SMA can provide tailored solutions for any project.
Conclusion
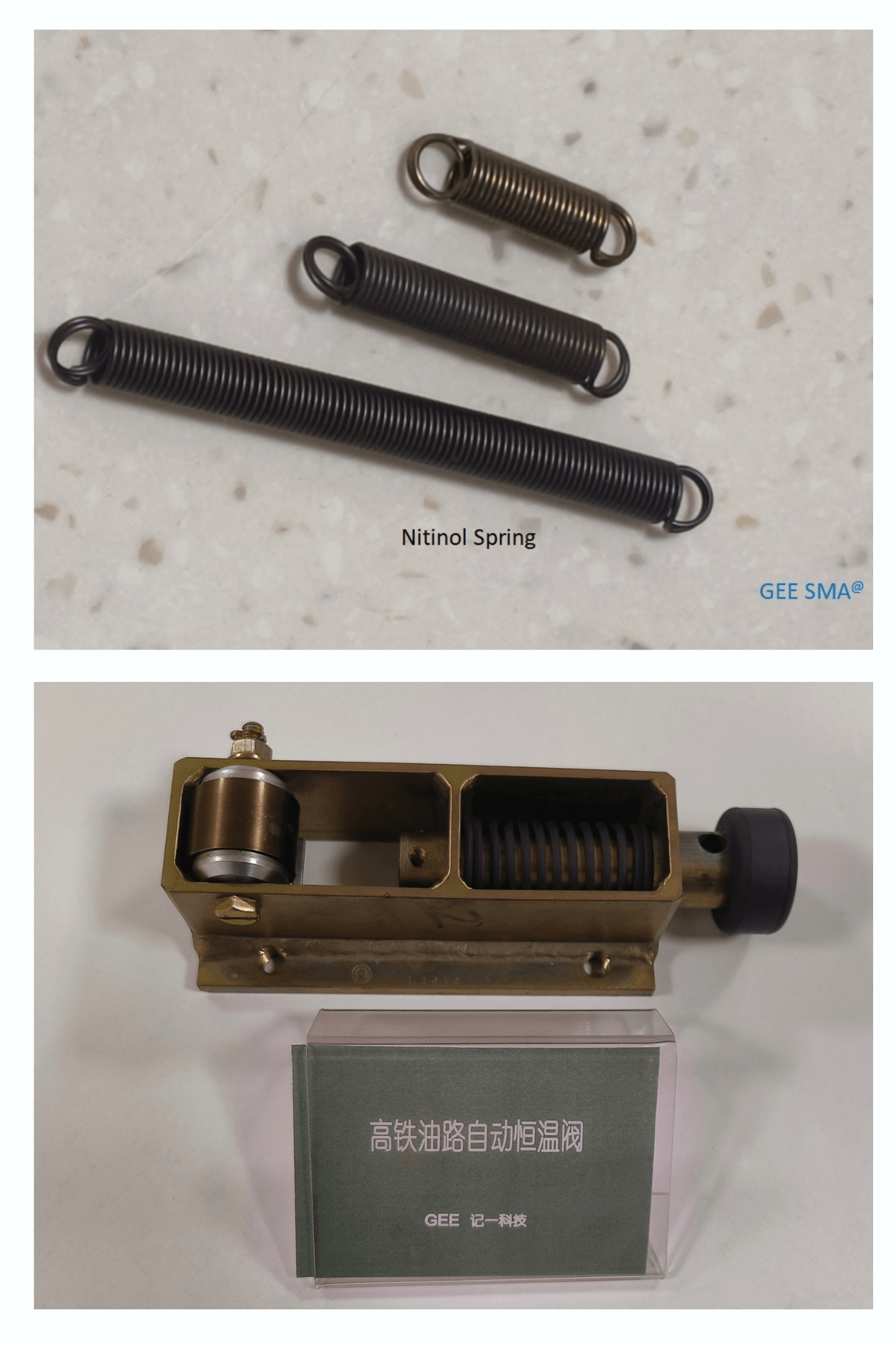
When it comes to choosing the right Nitinol spring for your specific needs, it's crucial to consider factors such as size, shape, and desired properties. Whether you require the flexibility of Nitinol Micro-Springs or the resilience of NiTi Coil Spring, understanding your application is key.
Choosing the right Nitinol spring for your specific needs
Consider the unique requirements of your project and select a Nitinol spring that aligns with those needs. If you need a compact and durable solution, a Micromatic Nitinol Spring might be the perfect fit. For applications where adjustable force is necessary, the NiTi Adjustable Force Preformed Closed Coil Spring could be ideal.
If your project requires a Nitinol spring that can withstand extreme temperatures, the Micromatic Nitinol Spring is an excellent choice due to its high-temperature resistance and durability. Additionally, if you need a spring that offers precise and consistent performance, the NiTi Adjustable Force Preformed Closed Coil Spring is designed to provide adjustable force for a wide range of applications. Both options offer unique benefits that cater to specific project requirements, ensuring optimal performance and reliability.
Key considerations when selecting Micromatic Nitinol Spring
When evaluating Micromatic Nitinol Spring options, take into account factors such as temperature range, fatigue resistance, and shape memory characteristics. Understanding these key considerations will help you make an informed decision and ensure that you choose the most suitable spring for your application. Additionally, it's important to consider the manufacturing process and quality control measures in place for the Nitinol springs. Partnering with a reputable supplier like GEE SMA ensures that you receive top-notch Nitinol spring solutions that meet the highest industry standards for performance and reliability.
Partnering with GEE SMA for top-notch Nitinol spring solutions
For top-notch Nitinol spring solutions tailored to your specific requirements, partnering with GEE SMA is an excellent choice. With their expertise in crafting high-quality Nitinol springs and their ability to tailor materials to meet customer needs, GEE SMA is a trusted partner for innovative solutions.
Partnering with GEE SMA for top-notch Nitinol spring solutions means gaining access to a team that is dedicated to delivering exceptional customer service. From the initial consultation to the final product delivery, GEE SMA prioritizes open communication and collaboration to ensure that every client's unique needs are met. This commitment to personalized attention sets them apart as a reliable and responsive partner in the field of Nitinol spring solutions.