Introduction
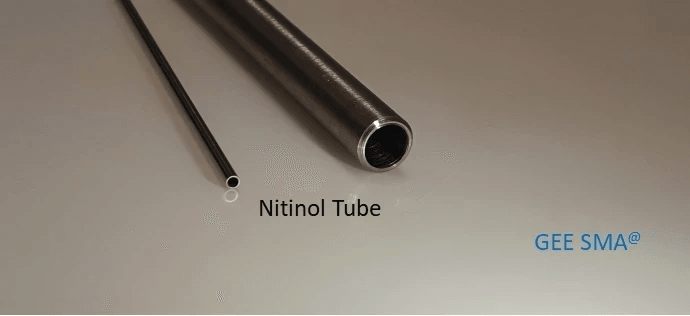
Nitinol, a unique alloy of nickel and titanium, has gained popularity for its remarkable properties and diverse applications across various industries. Understanding the process of nitinol electropolishing, exploring its distinct properties, and uncovering its wide-ranging applications is essential for harnessing its full potential.
Understanding Nitinol Electropolishing
Nitinol electropolishing is a specialized surface finishing process that enhances nitinol components' corrosion resistance and biocompatibility, making it ideal for medical devices and implants. This electrochemical technique removes surface imperfections and contaminants, resulting in a smooth, clean finish that improves the performance and longevity of nitinol products.
Exploring Nitinol Properties
Nitinol exhibits unique shape memory and superelasticity, allowing it to return to its original shape after deformation. With a melting point of around 1310°C, nitinol possesses exceptional thermal properties suitable for high-temperature applications. Its mechanical strength and corrosion resistance make it an attractive choice for various engineering solutions.
Applications of Nitinol in Various Industries
From medical devices like stents and guidewires to automotive components and consumer electronics, nitinol's versatility has led to widespread adoption across multiple industries. Its biocompatibility in medical implants, lightweight nature in aerospace engineering, and shape memory capabilities in actuators demonstrate its adaptability to diverse applications.
The Process of Nitinol Electropolishing
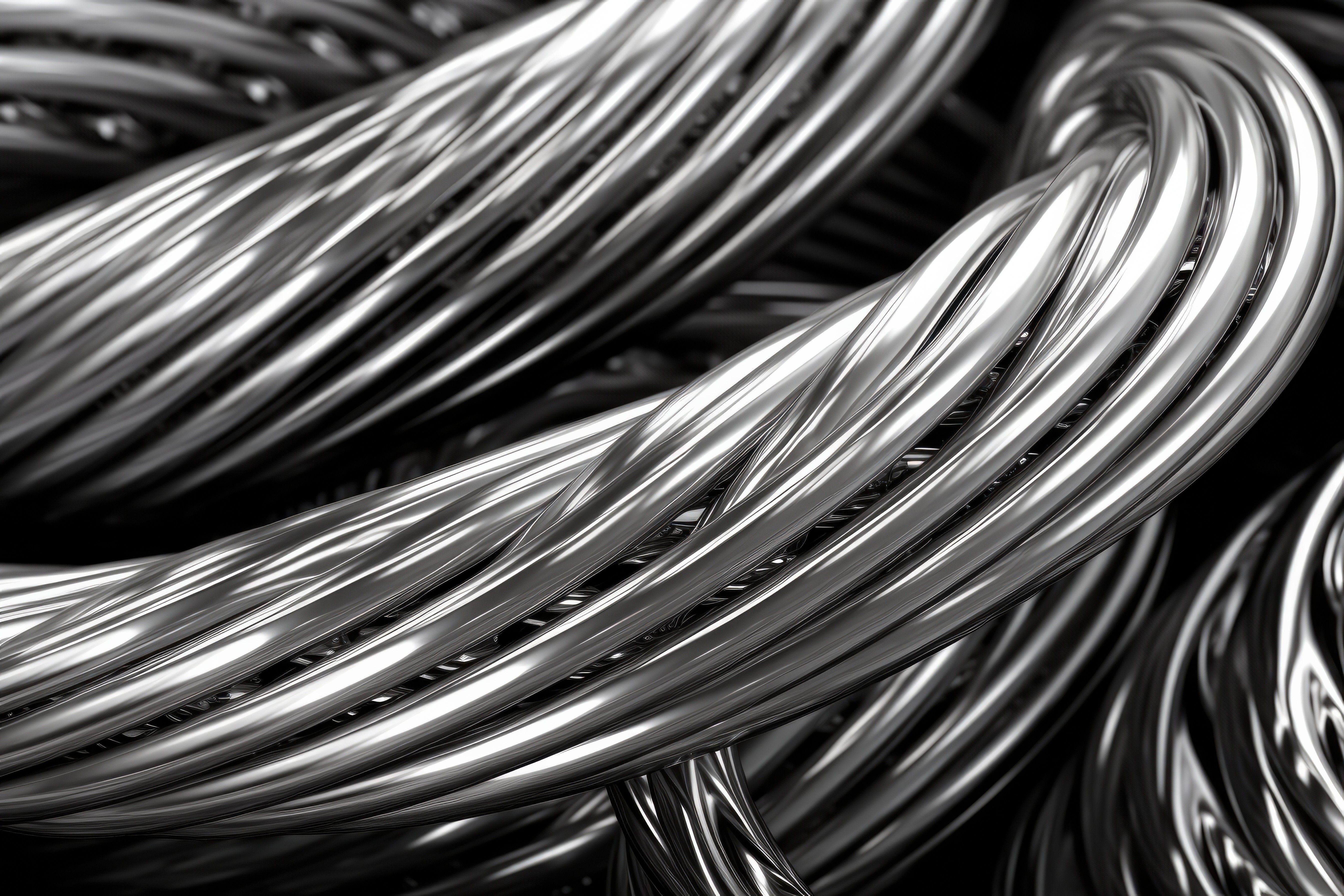
Nitinol electropolishing is a specialized surface-finishing process that enhances the properties of nitinol alloys. This method involves immersing the nitinol material in an electrolyte solution and applying an electric current to remove surface imperfections and contaminants, resulting in a smooth, polished finish.
What is Nitinol Electropolishing?
Nitinol electropolishing is a chemical process that removes a thin layer of material from the surface of nitinol components, resulting in improved surface finish and corrosion resistance. This method also helps eliminate microcracks and defects, enhancing mechanical properties and biocompatibility for medical applications. Additionally, nitinol electropolishing can improve the fatigue life of components by reducing stress concentrations and enhancing the overall performance of nitinol devices. Furthermore, the process can be tailored to achieve specific surface roughness or texture, allowing for customization based on the requirements of different applications.
Benefits of Nitinol Electropolishing
Nitinol electropolishing has numerous benefits, including improved fatigue life, reduced friction, and increased resistance to corrosion. Additionally, this process can enhance the biocompatibility of nitinol for medical implants and devices, making it an ideal choice for various healthcare applications.
In addition to the mechanical benefits, nitinol electropolishing also results in a smoother surface finish, which can be advantageous for applications where contact with other materials is necessary. The improved surface finish can reduce the risk of particulate generation and improve the overall performance of nitinol components in various medical and industrial settings. This makes nitinol electropolishing an attractive option for manufacturers looking to enhance the quality and reliability of their products.
Techniques and Equipment for Nitinol Electropolishing
The techniques and equipment used for nitinol electropolishing vary depending on the application's specific requirements. Common methods include manual polishing with abrasive materials or automated processes using specialized electrolytes and power supplies to achieve precise control over the finishing parameters.
Remember that when it comes to achieving optimal results with nitinol electropolishing, it's crucial to work with experienced professionals who understand the intricacies of this specialized process. Whether you're looking to enhance the performance of medical devices or improve the functionality of automotive components, partnering with experts in nitinol electropolishing can make all the difference in achieving superior results.
Properties of Nitinol
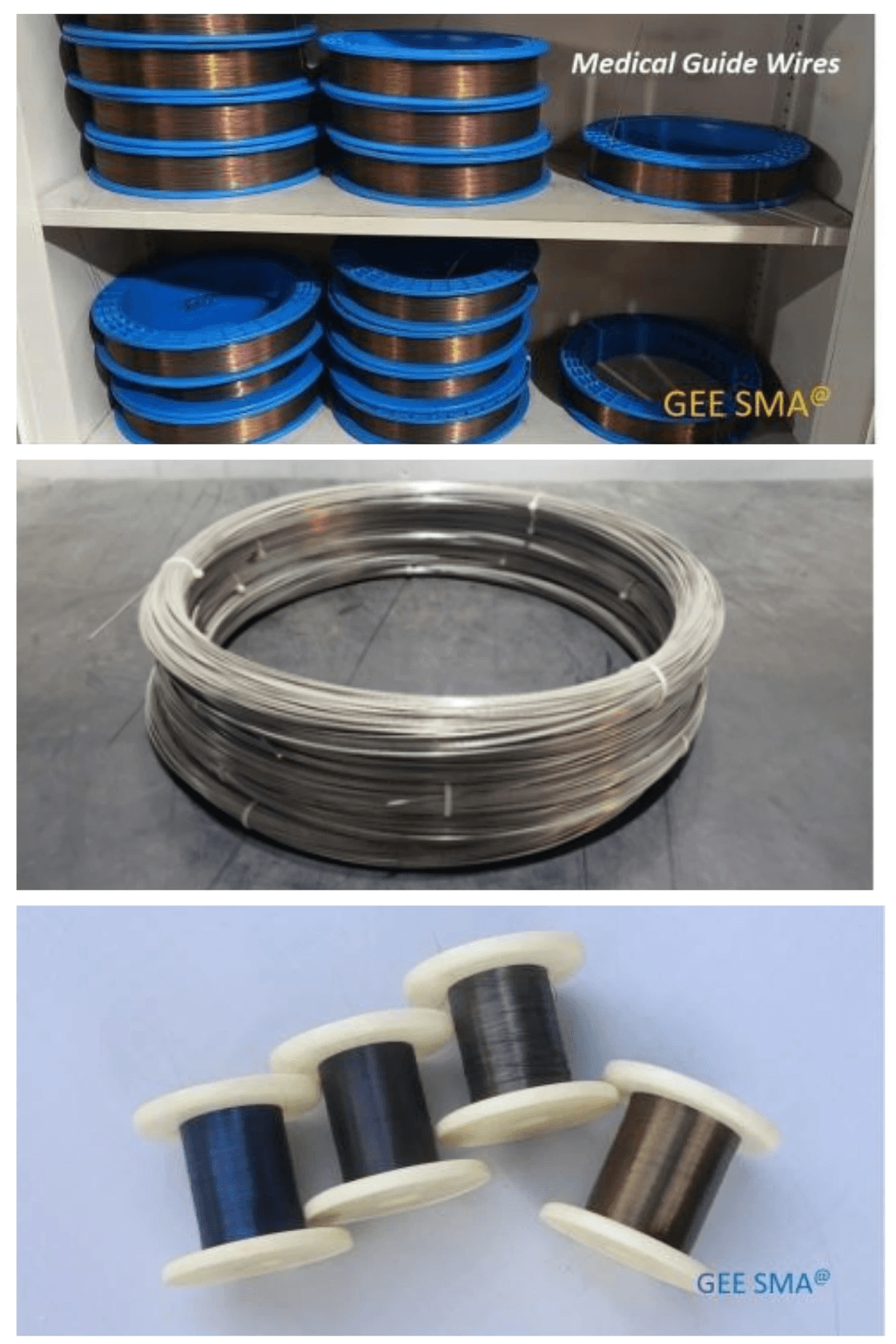
Nitinol, a nickel-titanium alloy, possesses remarkable properties that make it highly versatile and sought after in various industries. One of its most fascinating characteristics is its shape memory and superelasticity, allowing it to return to its original shape after deformation. This makes it ideal for applications such as stents and orthodontic wires in the medical field, where flexibility and resilience are crucial.
Nitinol also boasts a high melting point and exceptional thermal properties, making it suitable for extreme temperatures. Its ability to withstand harsh conditions without losing its structural integrity makes it a top choice for aerospace and automotive components, where reliability is paramount.
In addition, Nitinol exhibits impressive mechanical strength and corrosion resistance, ensuring longevity and durability in diverse applications. This makes it an excellent material for manufacturing surgical tools, engine components, and consumer electronics that require strength and resistance to environmental factors.
With its unique combination of properties, Nitinol continues to revolutionize numerous industries by enabling the creation of innovative products with exceptional performance and reliability.
Applications of Nitinol
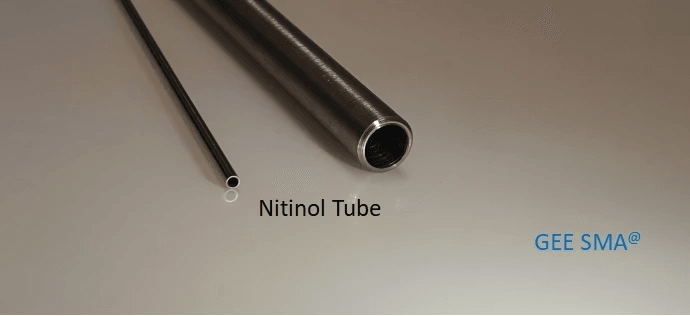
Nitinol, a unique shape memory alloy, has found diverse applications across various industries due to its exceptional properties. From medical devices to automotive components, its versatility makes it a sought-after material for numerous applications.
Medical Applications of Nitinol
In the medical field, nitinol is widely used for manufacturing stents, guidewires, and orthodontic wires due to its superelasticity and biocompatibility. Its ability to return to its original shape after deformation makes it ideal for minimally invasive surgical procedures and long-term implantation in the human body.
In addition to its use in medical devices, nitinol is also finding applications in the automotive and aerospace industries. Its unique combination of strength and flexibility makes it an ideal material for components such as actuators, sensors, and valves in these high-performance environments. Nitinol's ability to withstand extreme temperatures and pressures further enhances its appeal for use in critical automotive and aerospace systems.
Automotive and Aerospace Applications
Nitinol is a valuable material for the automotive and aerospace industries due to its lightweight, durable, and unique properties. Its applications span various components, including actuators, sensors, and engine parts.
Nitinol's key advantages for these sectors include:
- High fatigue resistance: It can withstand repeated stress without breaking or deforming.
- Thermal stability: It maintains its properties under varying temperature conditions.
- Shape memory effect: It returns to its original shape after deforming, making it ideal for components subjected to repeated stress.
This shape memory property is particularly advantageous for components like springs, valves, and fasteners, enhancing their performance and reliability in demanding environments.
By harnessing nitinol's potential, these industries can develop innovative solutions that improve vehicle and aircraft efficiency, safety, and performance.
Consumer and Industrial Applications of Nitinol
Due to its flexibility and resilience in consumer electronics, nitinol is utilized in products like eyeglass frames, mobile phone antennas, and headphone wires. Additionally, industrial applications include valves, couplings, and actuators, where nitinol's shape memory properties are harnessed for precise control and automation. Nitinol wire is a shape memory alloy that can "remember" its original shape and return to it when heated. This unique property makes it ideal for applications requiring precise control and movement, such as in medical devices like stents and guidewires.
What is Nitinol Wire
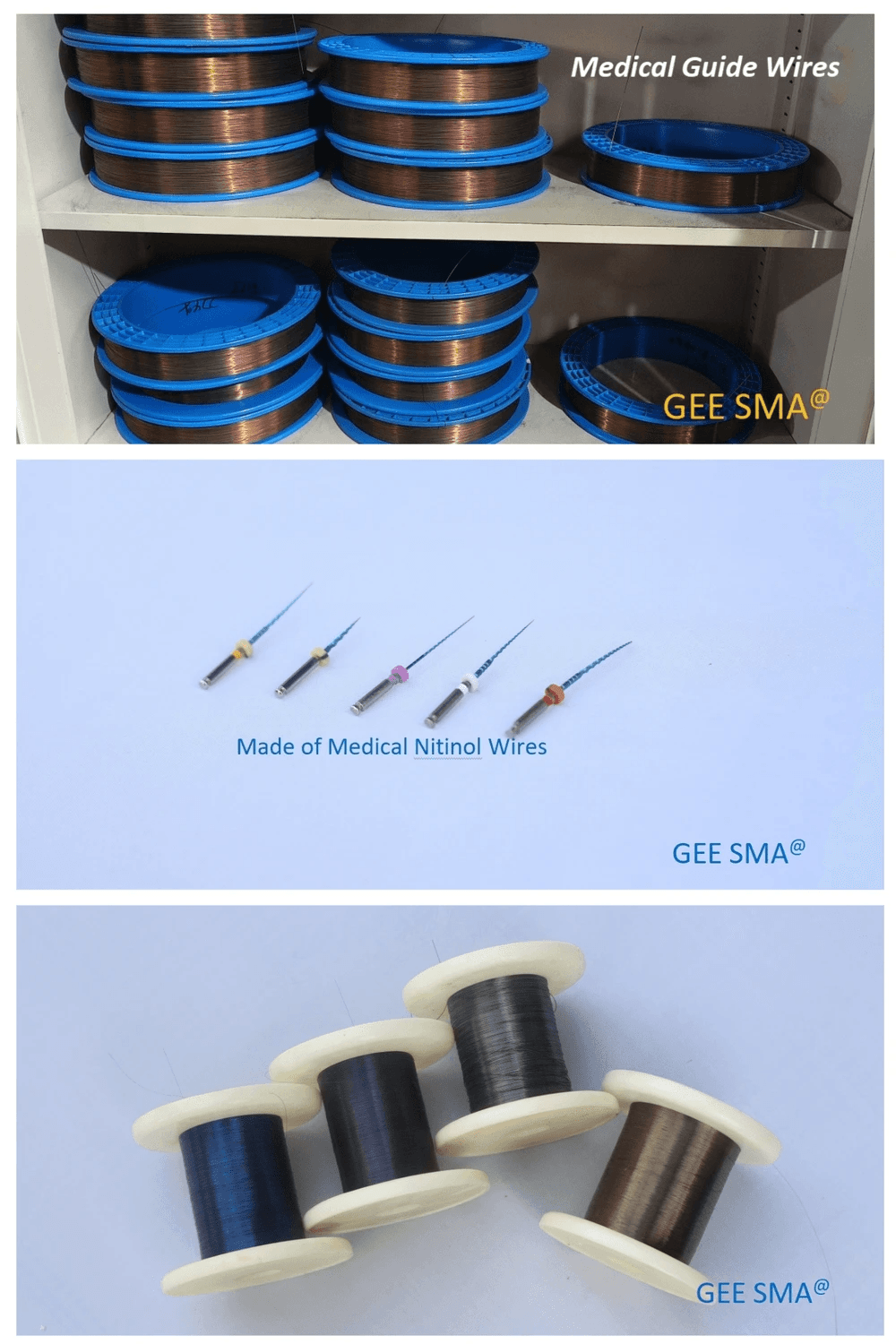
Nitinol wire is a unique alloy of nickel and titanium, known for its shape memory and superelasticity. It is typically manufactured in various diameters and lengths to suit different applications, making it a versatile material in industries such as medical, automotive, and aerospace.
Characteristics and Composition of Nitinol Wire
Nitinol wire is a remarkable material renowned for its exceptional flexibility and resilience. Composed of approximately 50% nickel and 50% titanium, this unique alloy exhibits extraordinary properties.
Nitinol wire offers several key advantages:
- Shape Memory Effect: When heated, it can be deformed and then return to its original shape.
- Superelasticity: It can undergo large deformations and spring back to its original shape without permanent damage.
- High Strength and Durability: It is resistant to wear and tear, making it suitable for demanding applications.
- Excellent Corrosion Resistance: It is highly corrosion-resistant, ensuring long-lasting performance.
- Biocompatibility: It is safe for use in medical implants.
Beyond its shape-changing abilities, Nitinol wire also excels in withstanding extreme temperatures. This characteristic makes it an ideal choice for aerospace, medicine, and robotics industries, where components must function reliably in harsh conditions.
From the precision of medical procedures to the rigors of space exploration, Nitinol wire consistently delivers outstanding performance. Its flexibility, resilience, and heat resistance make it a versatile and indispensable material in modern technology.
Manufacturing Process of Nitinol Wire
The manufacturing process of nitinol wire involves carefully blending the nickel and titanium in precise proportions before subjecting the alloy to extreme heat treatment. This process helps achieve the desired shape memory properties and superelasticity, ensuring that the nitinol wire meets the stringent quality standards required for various industrial applications.
In addition to its shape memory and superelastic properties, nitinol wire offers excellent corrosion resistance, making it ideal for applications in harsh environments. This corrosion resistance ensures that the nitinol wire maintains its integrity and performance over time, even when exposed to moisture, chemicals, or other corrosive elements. As a result, industries such as medical devices, aerospace, and automotive rely on nitinol wire for critical components that require long-term durability.
Advantages of Using Nitinol Wire in Various Applications
Nitinol wire is a versatile material with numerous applications across various industries. Its unique properties make it an ideal choice for various products and components.
Here are some of the key advantages of nitinol wire:
- Shape Memory and Superelasticity: Nitinol wire can return to its original shape after deforming, making it ideal for medical implants, actuators, and other applications requiring precise and consistent performance.
- Biocompatibility: Nitinol is widely used in medical procedures, including minimally invasive surgeries, due to its excellent biocompatibility and ability to interact safely with human tissue.
- Durability and Corrosion Resistance: Nitinol wire is highly resistant to corrosion and fatigue, making it suitable for demanding environments in automotive, aerospace, and industrial applications.
By understanding the full potential of nitinol wire, businesses can leverage this remarkable material to create innovative and high-performance products.
Crafting High-Quality Nitinol with GEE SMA
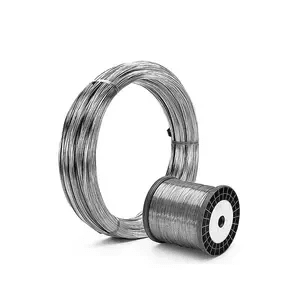
GEE SMA is dedicated to providing top-notch nitinol products tailored to various industries' unique needs. Our mission is to deliver innovative solutions that harness the full potential of nitinol while upholding the values of integrity, quality, and customer satisfaction.
Mission and Values of GEE SMA
At GEE SMA, we are committed to tailoring nitinol functional materials that exceed industry standards. Our expertise in nitinol electropolishing and advanced manufacturing techniques ensure that our products offer exceptional performance and reliability for a wide range of applications. Our dedication to innovation drives us to continuously push the boundaries of what is possible with nitinol, allowing us to develop cutting-edge solutions for our customers' most demanding challenges. By staying at the forefront of technological advancements and investing in research and development, we guarantee that our nitinol functional materials are always at the leading edge of quality and performance.
Tailoring Nitinol Functional Materials
Our team at GEE SMA takes pride in our ability to swiftly address customer requirements by tailoring nitinol functional materials to meet specific needs. Whether adjusting the composition of nitinol wire or fine-tuning the thermal properties of alloy foils, we have the expertise to deliver custom solutions that exceed expectations. By understanding the unique demands of each application, we can ensure that our nitinol products meet and surpass customer requirements.
Swiftly Addressing Customer Requirements
At GEE SMA, we take pride in our ability to address customer requirements for nitinol products swiftly. Whether developing prototypes or scaling up production for large orders, we are dedicated to providing responsive support and delivering exceptional results on time. Our team of experienced engineers and technicians works tirelessly to ensure every project is executed precisely and efficiently, allowing us to meet even the most demanding specifications. With our state-of-the-art facilities and commitment to innovation, we can tackle complex challenges and deliver cutting-edge solutions that exceed expectations.
By partnering with GEE SMA, you can trust that you will receive unparalleled expertise in crafting high-quality nitinol products tailored to your needs.
Conclusion
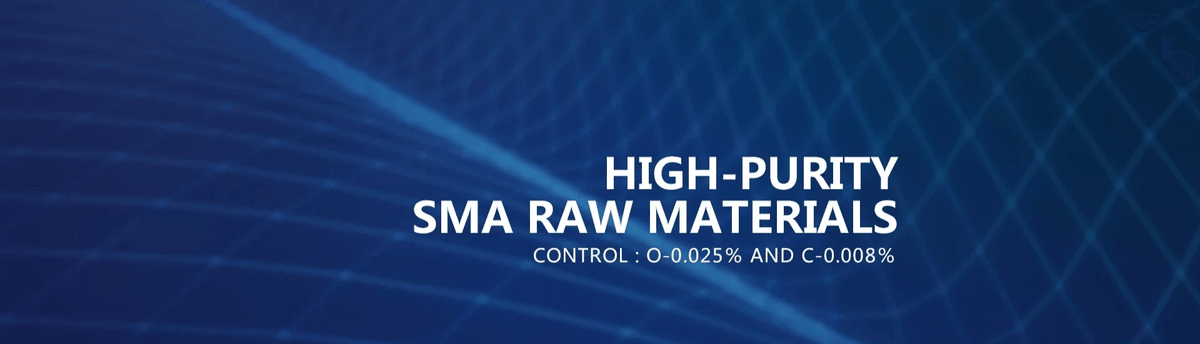
Nitinol electropolishing is a crucial process for enhancing Nitinol components' surface finish and corrosion resistance. By advancing Nitinol electropolishing techniques, we can ensure the production of high-quality Nitinol materials that meet the stringent requirements of various industries.
Harnessing the power of Nitinol in diverse industries is essential for driving innovation and creating cutting-edge products. With its unique properties, such as shape memory and superelasticity, Nitinol offers unparalleled versatility in medical, automotive, aerospace, consumer, and industrial applications.
GEE SMA is your trusted partner for custom Nitinol solutions. With a commitment to tailoring Nitinol functional materials and swiftly addressing customer requirements, GEE SMA stands out as a reliable source of high-quality Nitinol products that meet your needs.
Remember: For top-notch results in your next project that requires nitinol alloy foil or any other nitinol product, count on GEE SMA to deliver exceptional custom solutions tailored to your unique specifications.