Introduction
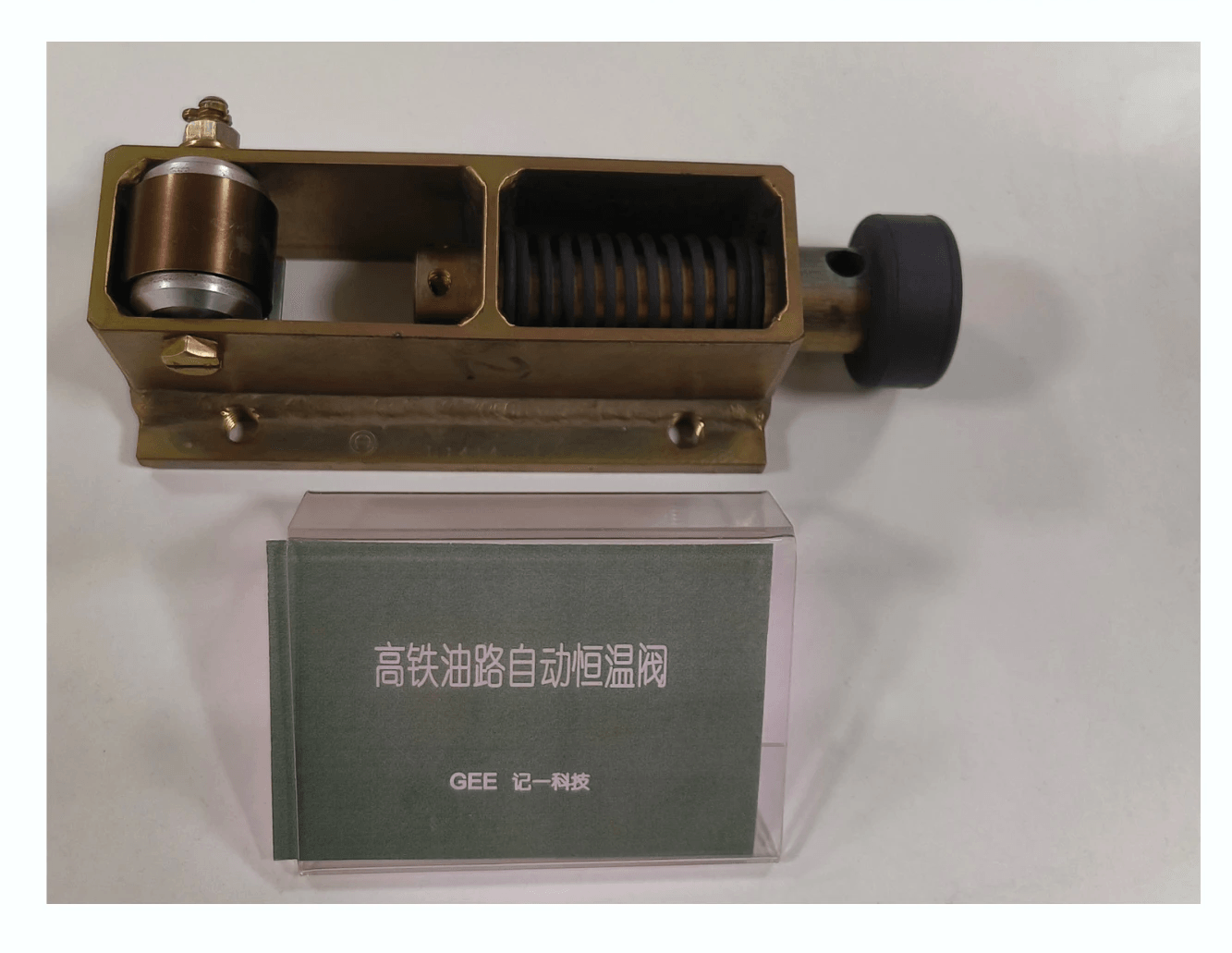
In the fast-paced world of micromanufacturing, Nitinol has emerged as a game-changer. With its unique properties and versatility, Nitinol offers endless possibilities for creating intricate components on a microscopic scale. From Nitinol Electropolishing to Nitinol 3D Laser Micro Machining, the techniques and applications are as diverse as they are innovative.
Understanding Nitinol Micro Manufacturing Techniques
Nitinol micro-manufacturing techniques encompass various processes to manipulate this shape memory alloy into finely detailed components. From Nitinol Oxide Removal to Nitinol Braiding, each technique plays a crucial role in harnessing the full potential of this remarkable material.
Exploring the Potential of Nitinol in Micro Manufacturing
The potential of Nitinol in micromanufacturing is truly boundless. Its shape-setting capabilities allow for precise control over the final form of components, making it ideal for applications requiring intricate shapes and sizes indispensable for.
The Significance of Nitinol Electropolishing
Nitinol electropolishing is a critical process in enhancing components' surface quality and performance. It's a vital step in ensuring products meet the rigorous demands of various industries.
- Enhanced Surface Finish: Nitinol electropolishing produces a smooth, mirror-like finish on the component's surface, improving its aesthetic appeal and reducing surface imperfections that can lead to premature wear or failure.
- Improved Corrosion Resistance: The process creates a passive oxide layer on the surface, which acts as a barrier against corrosive agents, enhancing the component's durability and lifespan.
- Enhanced Biocompatibility: For medical applications, nitinol electropolishing can improve the material's biocompatibility, reducing the risk of adverse reactions or infections.
- Improved Fatigue Resistance: A smooth surface and reduced surface defects can help improve the fatigue resistance of nitinol components, making them more resistant to failure under cyclic loading.
Nitinol electropolishing is a valuable process that offers numerous advantages regarding surface quality, corrosion resistance, and overall component performance. By incorporating this step into manufacturing processes, industries can ensure that their products meet the highest standards of quality and reliability.
Nitinol Shape Memory Alloys (SMA)
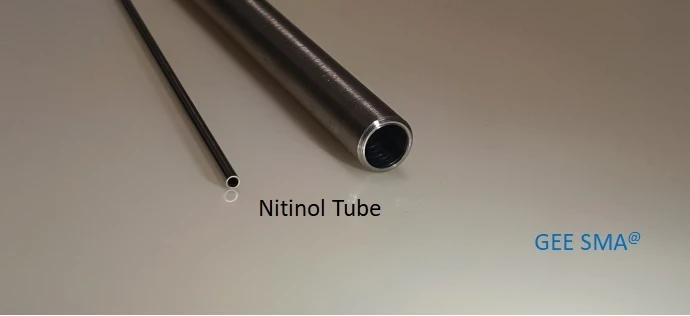
GEE SMA's Expertise in Nitinol Shape Memory Alloys
At GEE SMA, we have honed our expertise in working with Nitinol Shape Memory Alloys (SMA) to deliver high-quality components for micro-manufacturing applications. Our team of skilled engineers and technicians is well-versed in the unique properties of Nitinol, allowing us to create precision-engineered products that meet our clients' most demanding requirements.
Our expertise in Nitinol Shape Memory Alloys extends to our knowledge of effective oxide removal techniques. We understand the importance of maintaining the integrity and functionality of Nitinol components, which is why we have developed specialized methods for removing oxides from the material. By utilizing state-of-the-art processes, we ensure that our Nitinol products are free from any surface contaminants, resulting in superior performance and longevity.
Nitinol Oxide Removal Techniques
One key challenge in working with Nitinol is the presence of oxides on its surface, which can compromise its performance. We have developed advanced techniques for effectively removing these oxides, ensuring that our Nitinol components are free from impurities and exhibit superior mechanical properties essential for micromanufacturing applications.
Our advanced techniques for removing Nitinol oxide from the surface ensure the purity and superior mechanical properties of our components and contribute to their longevity and reliability. By effectively removing oxides from the surface, we prevent potential issues such as corrosion and degradation, which are crucial for maintaining the performance of Nitinol in micromanufacturing applications. This attention to detail sets our products apart in quality and durability.
The Importance of Nitinol Shape Setting
Shape setting is a fundamental aspect of fabricating Nitinol components, as it enables the material to "remember" a desired shape and return to it upon application of specific stimuli. This unique property makes Nitinol invaluable in various fields, including micromanufacturing, where precise and repeatable movements are essential.
Here's a numbered list highlighting the key benefits of shape setting in Nitinol components:
- Programmable Shape Memory: Nitinol can be programmed to remember a specific shape, allowing for precise and controlled movements in applications such as medical devices and actuators.
- Enhanced Durability: Shape setting helps to minimize the risk of deformation in Nitinol components, ensuring their long-term durability and reliability even under demanding conditions.
- Repeatability: Nitinol's ability to consistently return to its programmed shape provides excellent repeatability and precision in various applications.
- Wide Range of Applications: Shape setting in Nitinol components is utilized in diverse fields, including medical devices, aerospace, robotics, and more.
Shape setting is a critical process that unlocks the full potential of Nitinol components. By programming the material to remember a specific shape, we can create precise, durable, and reliable products that meet the stringent requirements of demanding applications.
Nitinol 3D Laser Micro Machining
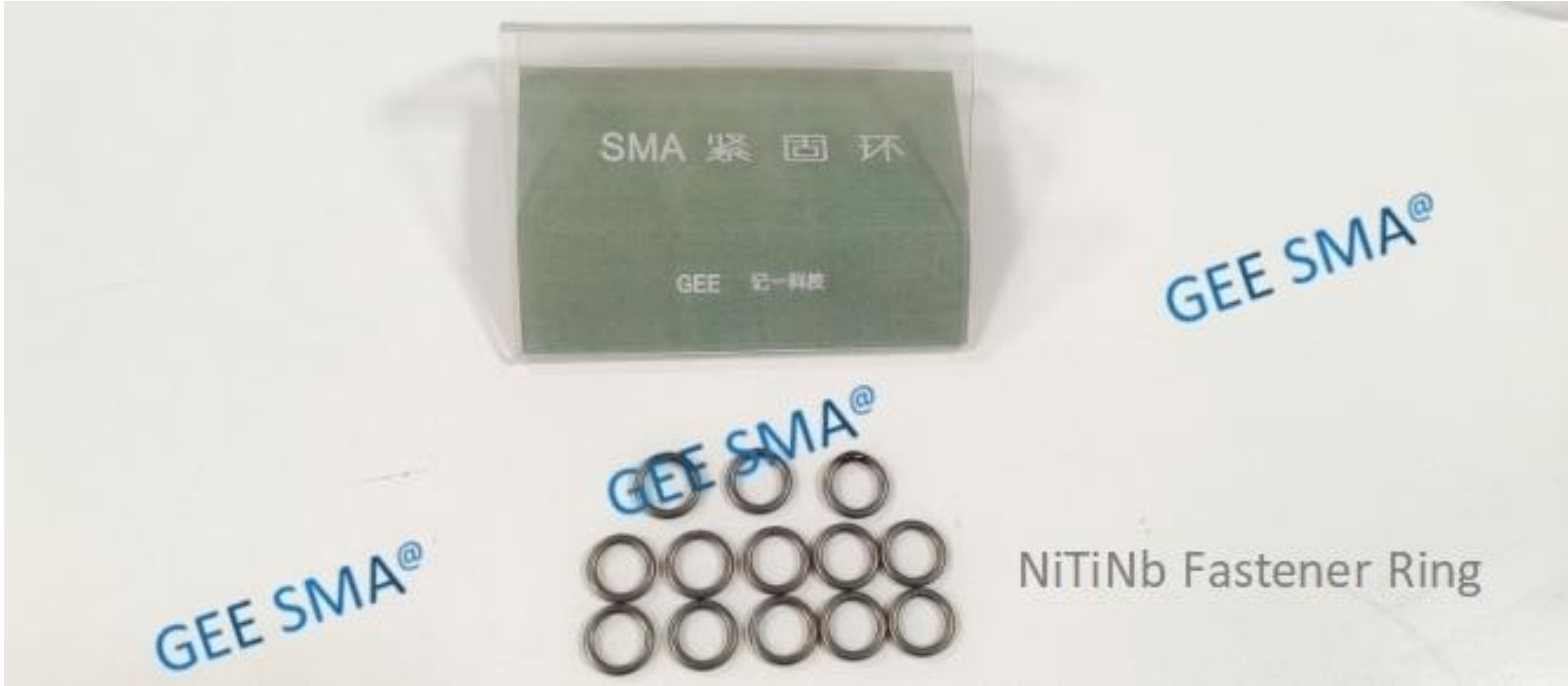
Nitinol 3D laser micromachining offers unparalleled precision and efficiency in producing intricate Nitinol components for various micromanufacturing applications. Advanced laser technology allows for the creation of complex shapes and designs with exceptional accuracy, meeting the demands of even the most challenging projects.
Precision and Efficiency in Nitinol 3D Laser Micro Machining
3D laser micromachining ensures that Nitinol components are manufactured precisely, producing high-quality products that meet strict industry standards. This cutting-edge technology enables manufacturers to achieve intricate details and fine features on Nitinol parts, making it an ideal choice for micro-manufacturing applications where precision is paramount.
The precision and efficiency of 3D laser micromachining in manufacturing Nitinol components also contribute to cost-effectiveness and reduced material waste. By utilizing this advanced technology, manufacturers can minimize the need for secondary operations and manual finishing, ultimately streamlining the production process and reducing overall production costs. This makes 3D laser micromachining a smart investment for companies looking to optimize their manufacturing processes and remain competitive.
Enhancing Nitinol Micro Manufacturing through Laser Technology
By harnessing the power of laser technology, Nitinol micro-manufacturing processes are significantly enhanced, allowing for greater flexibility and adaptability in producing custom-designed components. The versatility of 3D laser micromachining empowers manufacturers to explore innovative design possibilities and optimize production efficiency, ultimately leading to cost-effective solutions for various industry needs.
Furthermore, the precision and accuracy of 3D laser micromachining enable manufacturers to create intricate Nitinol components with minimal material waste, leading to more sustainable and environmentally friendly production processes. This technology also allows for producing complex geometries and fine features that are difficult to achieve with traditional manufacturing methods, opening up new possibilities for medical devices, aerospace components, and other critical applications. With the ability to work with Nitinol in its superelastic or shape memory state, 3D laser machining offers unparalleled versatility in producing components that meet the specific needs of diverse industries.
Crafting High-Quality Nitinol Components with 3D Laser Machining
Using 3D laser machining elevates the quality of Nitinol components by enabling the fabrication of intricate geometries and precise features that traditional methods may struggle to achieve. This advanced manufacturing technique ensures that each component is meticulously crafted accurately, resulting in superior performance and reliability in diverse micro-manufacturing applications.
Furthermore, 3D laser machining allows for producing Nitinol components with minimal material waste, making it a cost-effective and environmentally friendly manufacturing solution. This technology also offers the flexibility to easily create customized designs and prototypes, reducing lead times and accelerating product development. As a result, companies can stay ahead of the competition by quickly bringing innovative Nitinol components to market, meeting the demands of various industries such as medical devices, aerospace, and consumer electronics.
Nitinol Braiding
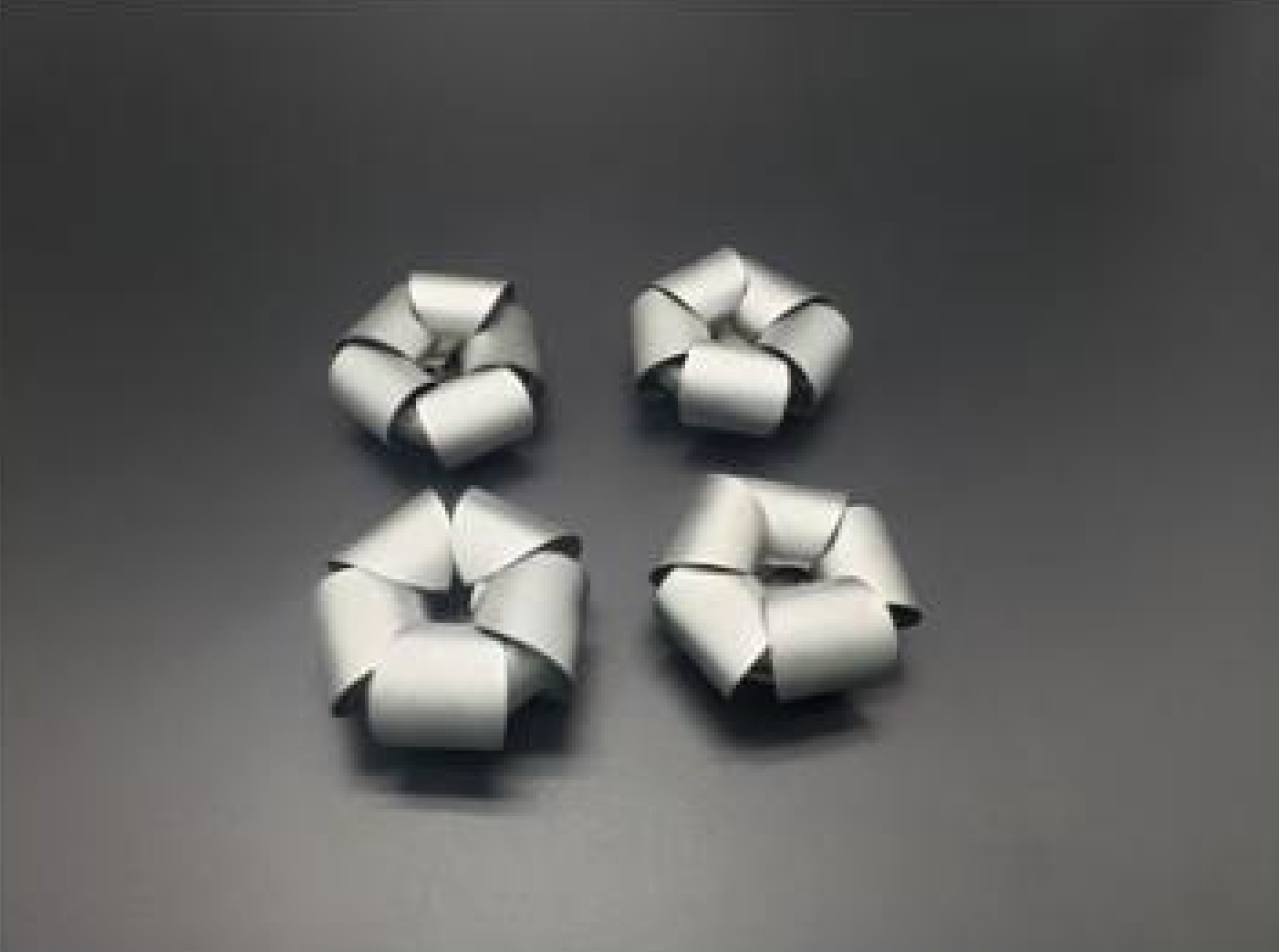
Nitinol braiding is a cutting-edge micromanufacturing technique involving weaving Nitinol wires into intricate patterns to create durable and flexible components. This innovative method produces complex, custom-designed Nitinol structures ideal for various applications, from medical devices to aerospace technology.
Innovative Techniques in Nitinol Braiding
Innovative techniques in Nitinol braiding involve advanced machinery and specialized processes to weave Nitinol wires intricately into precise patterns. This allows for creating highly customizable components with exceptional strength, flexibility, and shape memory properties. The result is a versatile material that can be tailored to meet the unique requirements of various industries, making it an invaluable asset in micromanufacturing.
Advancing Nitinol Micro Manufacturing through Braiding Methods
Braiding methods have significantly advanced Nitinol micromanufacturing by enabling the production of intricate and durable components with unparalleled precision and reliability. Advanced braiding technology has revolutionized the way Nitinol materials are utilized, allowing for the creation of complex structures that were previously unattainable through traditional manufacturing methods.
Tailoring Nitinol Materials for Diverse Applications
Nitinol braiding offers a versatile and customizable approach to material fabrication, finding applications in various industries.
- Medical Implants: Nitinol's shape memory and biocompatibility make it ideal for creating intricate medical implants, such as stents, catheters, and orthopedic devices.
- Aerospace Components: Nitinol's high strength-to-weight ratio and corrosion resistance make it suitable for aerospace components like actuators, sensors, and heat exchangers.
- Electronics: Nitinol's shape memory and electrical conductivity can be utilized in electronic components, such as microactuators and sensors.
- Energy Storage: Nitinol's shape memory can be harnessed for energy storage applications, such as shape memory alloy batteries and thermal actuators.
Nitinol braiding's ability to create tailored structures with unique properties makes it a valuable tool for advanced manufacturing across various industries.
Nitinol Electrical Discharge Machining (EDM)
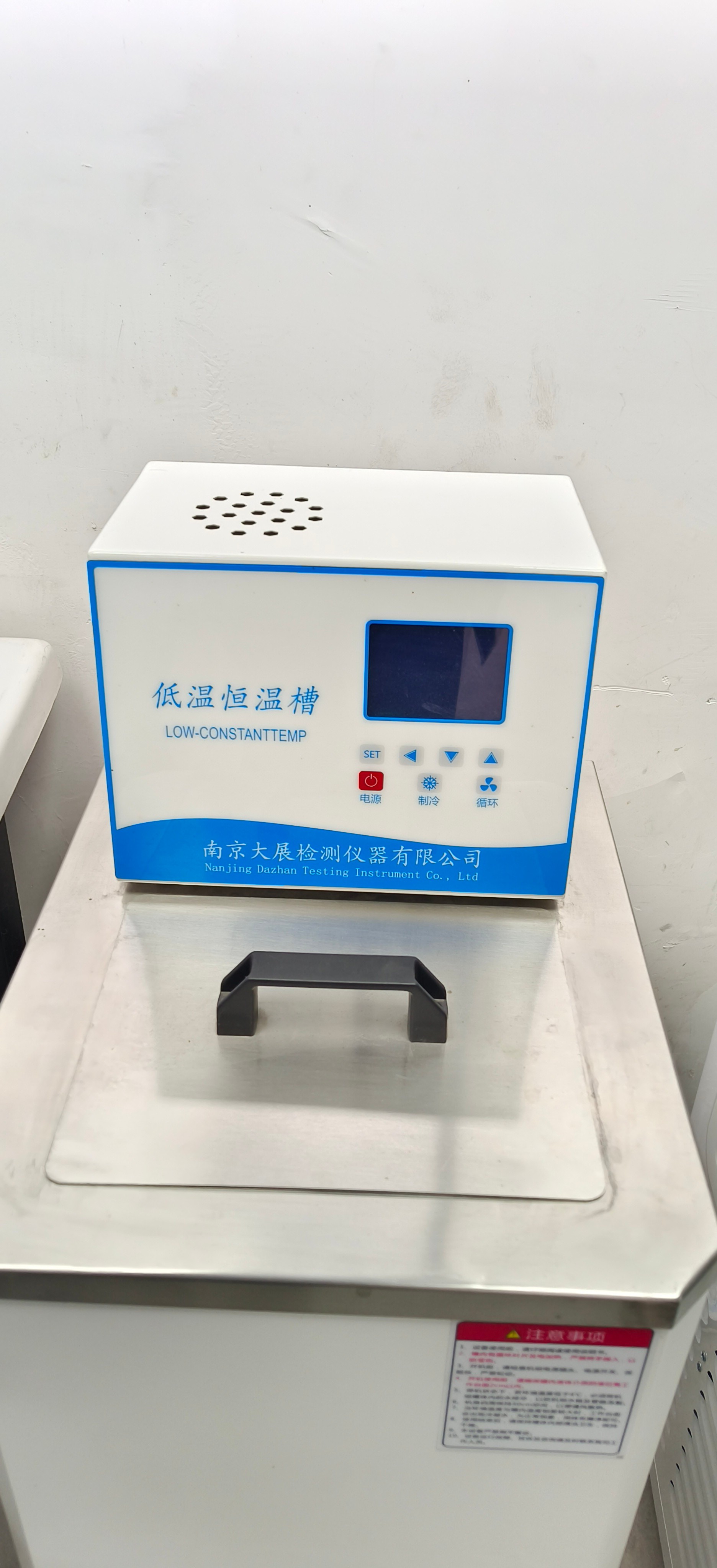
Nitinol micro manufacturing reaches new heights with the optimization of EDM technology. This cutting-edge method allows for the precise shaping and machining of Nitinol components, ensuring superior quality and accuracy in production. By harnessing the power of EDM, manufacturers can easily meet the intricate demands of micromanufacturing.
Optimizing Nitinol Micro Manufacturing with EDM
EDM technology revolutionizes Nitinol micro manufacturing by offering unparalleled precision and efficiency in shaping Nitinol components. This advanced method enables manufacturers to produce intricate designs and complex geometries with utmost accuracy, meeting the specifications for micro-manufacturing applications.
Furthermore, EDM technology also allows for the creation of Nitinol components with minimal material waste, making it a cost-effective solution for micromanufacturing. The precision and efficiency of EDM ensure that manufacturers can optimize their production processes, reducing lead times and increasing overall productivity. With the ability to produce intricate designs and complex geometries at such high accuracy, EDM has become an indispensable tool for achieving superior precision in Nitinol micromanufacturing.
Achieving Superior Precision with Nitinol EDM Techniques
The use of EDM techniques elevates the precision of Nitinol micro-manufacturing to a whole new level. With its ability to create intricate patterns and detailed features, EDM ensures that every Nitinol component is crafted impeccably, meeting the highest quality standards in micro-manufacturing. This level of precision is essential in meeting the increasing demands for smaller, more complex Nitinol components used in medical devices and other cutting-edge technologies. By utilizing EDM technology, manufacturers can confidently address these customer requirements and deliver products that exceed expectations.
Addressing Customer Requirements through EDM Technology
Nitinol EDM technology empowers manufacturers to address diverse customer requirements easily. Whether it's creating custom-designed Nitinol components or meeting specific dimensional tolerances, EDM offers a versatile solution that caters to a wide range of customer needs in micro-manufacturing.
Nitinol EDM technology not only allows manufacturers to meet specific dimensional tolerances and create custom-designed components but also enables them to do so with exceptional precision and accuracy. This level of precision is crucial in the realm of micro-manufacturing, where even the smallest deviation can significantly impact the final product. By leveraging EDM technology, manufacturers can ensure they deliver high-quality Nitinol components that meet or exceed their customers' expectations.
The Future of Nitinol in Micro Manufacturing
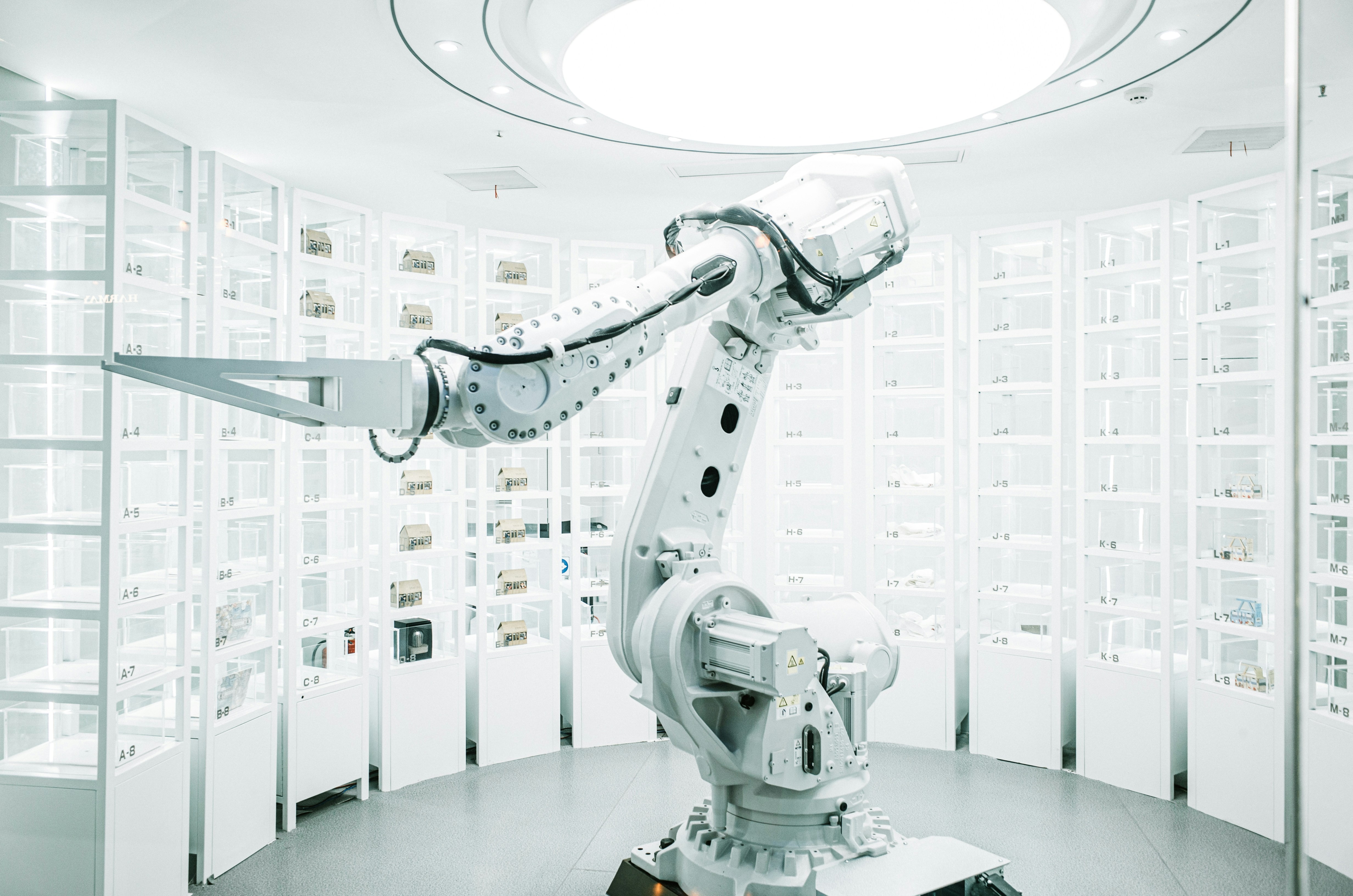
In conclusion, using Nitinol in micromanufacturing has opened up a world of possibilities. With techniques such as Nitinol Electropolishing, Nitinol Oxide Removal, and Nitinol Shape Setting, we can maximize the potential of this shape memory alloy. By meeting unique customer needs with tailored Nitinol components through methods like Nitinol 3D Laser Micro Machining, Nitinol Braiding, and Nitinol Electrical Discharge Machining (EDM), we can ensure that every project succeeds. The future of Nitinol in micromanufacturing looks bright, with endless opportunities for innovation and growth.
Maximizing Nitinol Micro Manufacturing Potential
We have only scratched the surface of what is possible with Nitinol in micromanufacturing. Through advanced techniques such as 3D Laser Micro Machining and EDM technology, we can continue to push the boundaries of precision and efficiency. By constantly improving our methods for shaping and refining Nitinol components, we can unlock even greater potential for this remarkable material.
Meeting Unique Customer Needs with Tailored Nitinol Components
Every customer has unique requirements for micro-manufacturing, and our ability to craft tailored solutions using techniques like Braiding and Shape Setting sets us apart. Whether it's creating intricate medical devices or high-performance aerospace components, we are committed to delivering exactly what our customers need.
As technology advances, so will the capabilities of micromanufacturing with Nitinol. With ongoing research into new methods and materials, the future promises even greater precision, efficiency, and customization options for various applications.