Introduction
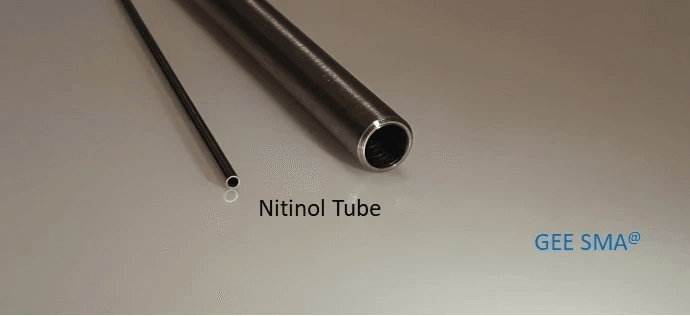
Nitinol is a remarkable alloy composed primarily of nickel and titanium, known for its unique properties that blend flexibility with strength. This fascinating material has found its way into various applications, from medical devices to robotics, thanks to its ability to return to a predetermined shape when heated. As we delve deeper into the world of Nitinol, we'll explore how products like the Nitinol Superelastic Sheet are revolutionizing industries and why they command such a high price tag.
What is Nitinol and Its Uses
At its core, Nitinol is celebrated for two standout characteristics: shape memory and superelasticity. These traits make it invaluable in numerous fields, particularly in medical technology where precision and reliability are paramount. From stents to guidewires, understanding what Nitinol can do opens up a world of possibilities—so what is the purpose of nitinol? Simply put, it's about enhancing performance where traditional materials fall short.
Understanding the Nitinol Superelastic Sheet
The Nitinol Superelastic Sheet exemplifies the incredible versatility of this alloy. When subjected to stress or deformation, it can revert back to its original shape without permanent changes—a feature that sets it apart from conventional materials. This unique property allows for innovative designs in applications ranging from aerospace components to advanced medical instruments.
The Significance of Nitinol in Modern Applications
In today's fast-paced technological landscape, the significance of Nitinol cannot be overstated. Its applications span various sectors including healthcare, automotive engineering, and consumer electronics—each benefiting from its lightweight yet durable nature. However, one might wonder: why is nitinol so expensive? The answer lies in its complex manufacturing process and the specialized knowledge required to harness its full potential effectively.
Flexibility and Shape Memory
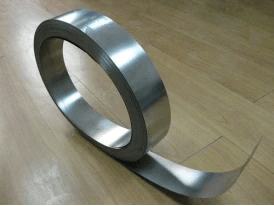
Nitinol, a remarkable alloy of nickel and titanium, is renowned for its unique flexibility and shape memory capabilities. This means that Nitinol strips can be deformed at one temperature but return to their original shape when heated above a certain threshold. This fascinating property makes Nitinol essential in various applications, particularly where adaptability and resilience are paramount.
How Nitinol Strips Retain Shape
The magic of Nitinol strips lies in their ability to undergo phase transformations between two distinct crystalline structures: the austenite phase (high-temperature) and the martensite phase (low-temperature). When a Nitinol strip is cooled, it becomes more malleable, allowing it to be bent or twisted into various shapes without permanent deformation. Once heated back to the austenite phase, the strip retains its original form, showcasing an impressive example of what is often referred to as shape memory.
This property is not just theoretical; it's practically applied in numerous industries. For instance, medical devices utilize this capability to create guidewires that can navigate through complex pathways in the body without losing their effectiveness or structural integrity. The versatility of these Nitinol Superelastic Sheets ensures that they can adapt seamlessly while maintaining reliability—an essential feature in high-stakes environments like healthcare.
Applications of Shape Memory Alloys
Shape memory alloys (SMAs), including Nitinol strips, have found their way into diverse fields due to their unique properties. One notable application is in orthodontics; braces made from SMAs can gently exert continuous pressure on teeth, promoting gradual movement over time while adapting to changes in oral conditions. Additionally, actuators made from Nitinol are increasingly used in robotics for precise movements that mimic natural motion.
In aerospace engineering, engineers leverage the flexibility of Nitinol for components that require both strength and adaptability under varying temperatures and pressures. These applications highlight not only what is the purpose of nitinol but also why industries are willing to invest significantly—because having materials that adapt while maintaining performance can save costs and improve safety.
The Role of GEE SMA in Nitinol Innovation
GEE SMA has been at the forefront of developing innovative solutions using super elastic nitinol technology. Their advancements include creating specialized forms like NT0402 Nitinol Foil which enhances functionality across different applications—from medical devices like stents and guidewires to consumer products requiring durable yet flexible materials.
What sets GEE SMA apart is its commitment to pushing the boundaries of what these alloys can achieve; they continually explore how variations in composition affect performance characteristics such as elasticity and strength compared to traditional materials like titanium—often leading many users to ask: Is nitinol stronger than titanium? The answer often leans towards yes when considering specific applications where flexibility coupled with strength is crucial.
Superelastic Properties Explained
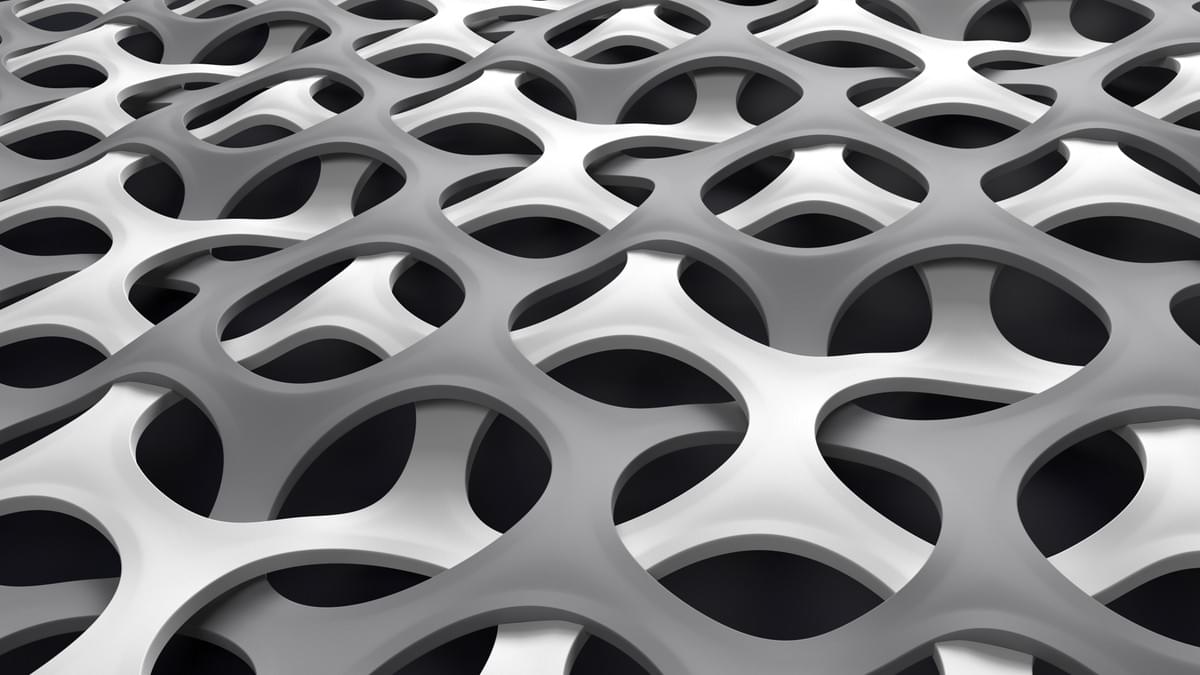
Nitinol, a remarkable alloy of nickel and titanium, possesses unique superelastic properties that set it apart from traditional metals. This superelasticity allows Nitinol strips and sheets to undergo significant deformation while returning to their original shape when the stress is removed. The ability of a Nitinol Superelastic Sheet to absorb energy and revert to its pre-deformed state makes it invaluable in various applications, particularly where flexibility and resilience are crucial.
What Makes a Nitinol Superelastic Sheet Unique
What truly makes a Nitinol Superelastic Sheet unique is its ability to exhibit both shape memory and superelastic behavior under different conditions. When heated above its transformation temperature, the material can return to a predetermined shape after being deformed—this is the essence of shape memory alloys. Conversely, at room temperature, the Nitinol strip can be stretched or compressed significantly without permanent deformation; this phenomenon is what we call superelasticity.
The unique atomic structure of Nitinol allows it to undergo phase transformations between martensite and austenite phases with minimal energy loss. This property enables applications that require components to withstand extreme conditions while maintaining functionality—think guidewires in medical devices! Understanding what is the purpose of nitinol goes beyond just its mechanical properties; it's about leveraging these extraordinary characteristics for innovative solutions.
Real-World Applications of Superelasticity
The real-world applications of superelasticity are as diverse as they are fascinating! One prominent example includes medical devices like stents and guidewires—what is a nitinol guidewire? It's a flexible yet strong tool used in minimally invasive surgeries that can navigate through complex anatomy without losing its structural integrity thanks to its superelastic nature.
Additionally, industries such as robotics and automotive engineering have begun incorporating Nitinol strips due to their ability to absorb shock and restore original shapes after deformation, enhancing durability without adding excess weight. These applications showcase how the versatility of super elastic nitinol extends beyond medicine into everyday technology.
Why is Nitinol So Expensive?
You might be wondering: why is nitinol so expensive? The answer lies in several factors including raw material costs, complex manufacturing processes, and stringent quality control measures required for producing high-performance alloys like NT0402 Nitinol Foil. The alloying process itself demands precise control over composition ratios between nickel and titanium, which adds both time and cost.
Moreover, the specialized equipment needed for processing Nitinol into usable forms—such as sheets or strips—adds another layer of expense that manufacturers must account for. Despite these costs, industries continue investing in this remarkable material due to its unparalleled performance advantages over conventional materials; after all, when you need something stronger than titanium but just as lightweight, you turn towards Nitinol!
Nitinol in Medical Devices
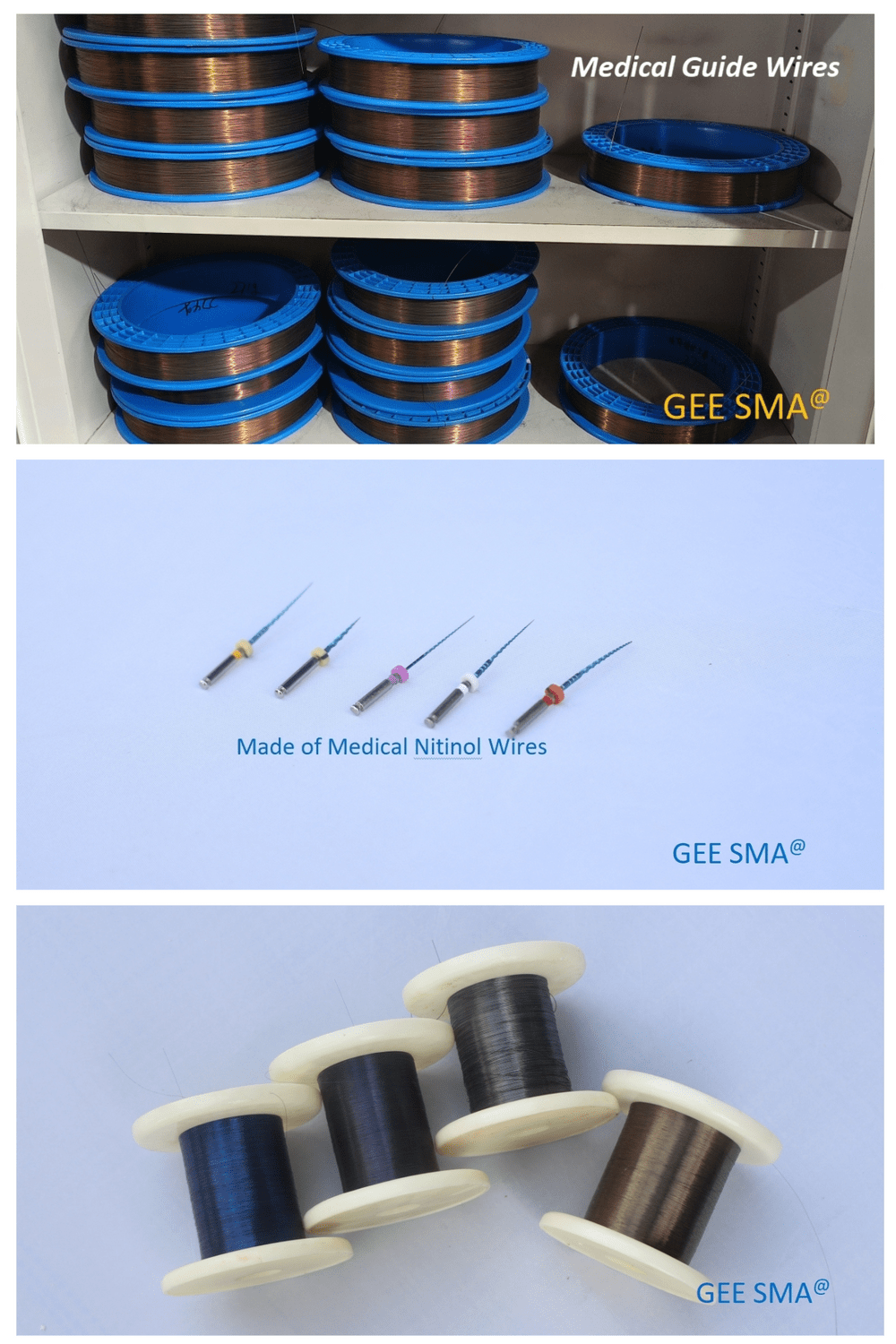
Nitinol has carved out a significant niche in the medical device industry, thanks to its unique properties that blend flexibility and strength. One of the most notable applications is the Nitinol guidewire, which plays an essential role in various minimally invasive procedures. Understanding what makes Nitinol so valuable can shed light on its purpose and advantages in healthcare.
What is a Nitinol Guidewire?
A Nitinol guidewire is a thin, flexible wire made from a special alloy of nickel and titanium, known for its superelastic properties. These wires are designed to navigate through complex vascular pathways during medical procedures, making them indispensable tools for interventional cardiology and radiology. By using a Nitinol guidewire, doctors can easily maneuver around obstructions while minimizing trauma to the surrounding tissues.
Advantages of Nitinol in Medical Applications
The advantages of using Nitinol in medical applications are numerous and compelling. First off, the superelasticity of the Nitinol strip allows it to return to its original shape after being bent or twisted, providing exceptional control during delicate procedures. Additionally, because it's biocompatible and resistant to corrosion, Nitinol is ideal for long-term implantation within the human body—making it not only effective but also safe.
Moreover, one might ponder: why is nitinol so expensive? The answer lies in its unique manufacturing process and material composition; producing high-quality Nitinol requires advanced technology and rigorous quality control measures that contribute to its higher cost compared to traditional metals like stainless steel or titanium.
NT0402 Nitinol Foil and its Uses
NT0402 Nitinol foil is another innovative application of this remarkable alloy that showcases its versatility beyond guidewires. This thin sheet can be used in various medical devices such as stents or orthopedic implants due to its ability to adapt under stress while maintaining structural integrity. The flexibility offered by NT0402 allows for easier deployment within the body while ensuring that devices remain functional over time.
In addition to these uses, NT0402 also demonstrates how far we've come with materials like Super Elastic Nitinol; it's not just about strength but about adaptability too! As we explore further into what is the purpose of nitinol?, we see that it aims at improving patient outcomes through minimally invasive techniques while reducing recovery times significantly.
Strength Comparison
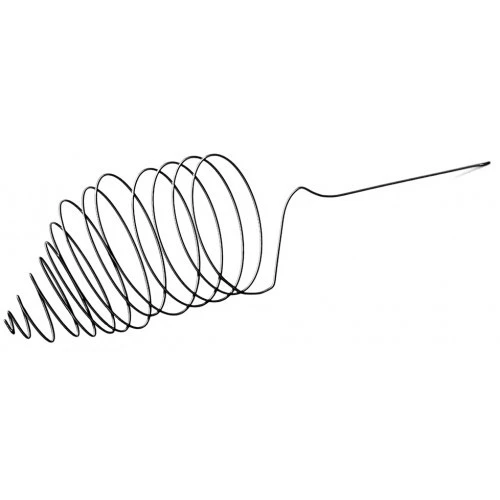
Is Nitinol Stronger Than Titanium?
At first glance, one might wonder, Is Nitinol stronger than titanium? The answer isn't straightforward because strength can be measured in various ways: tensile strength, yield strength, and fatigue resistance are just a few metrics to consider. While titanium typically boasts higher tensile strength than a Nitinol strip, the superelastic properties of Nitinol allow it to absorb significant amounts of energy without permanent deformation, making it exceptionally resilient in dynamic environments.
Moreover, when dealing with applications requiring flexibility alongside strength—such as medical devices like a nitinol guidewire—Nitinol often emerges as the preferred choice despite its lower inherent tensile strength. So while titanium might take the crown in raw power contests, Nitinol's unique capabilities make it invaluable in situations where flexibility and adaptability are paramount.
Comparative Analysis of Metal Alloys
In comparing metal alloys like Nitinol and titanium, it's crucial to look at more than just their mechanical properties; we must also consider their practical applications and costs. Why is Nitinol so expensive? Its complex manufacturing process involves precise heat treatments and alloying elements that contribute to its distinctive superelastic characteristics. This intricate production method elevates its price point but also enhances its functionality across various industries.
When examining other metal alloys in conjunction with Nitinol Superelastic Sheets or NT0402 Nitinol Foil, we find that each material has strengths tailored for specific uses. For instance, stainless steel may offer better corrosion resistance but lacks the shape memory capabilities inherent to shape memory alloys like Nitinol. Thus, while comparing these materials provides insights into their strengths and weaknesses, it's essential to align them with intended purposes to make informed decisions.
Applications Requiring Superior Strength
The quest for superior strength leads engineers and designers to evaluate numerous materials based on their unique properties. In industries such as aerospace or automotive engineering—where weight savings are critical—a combination of lightweight yet strong materials becomes vital; this is where both titanium and super elastic nitinol come into play effectively. While some applications may lean towards traditional metals like titanium due to their sheer toughness under stress conditions, others benefit from the adaptability offered by Nitinol strips.
For example, in the medical field where precision instruments like nitinol guidewires are utilized during minimally invasive procedures, having a material that can withstand bending without breaking is crucial—this showcases how certain applications require not only raw power but also resilience under dynamic conditions provided by advanced alloys such as NT0402 Nitinol Foil or other forms of superelastic nitinol products.
The Future of Nitinol Technology
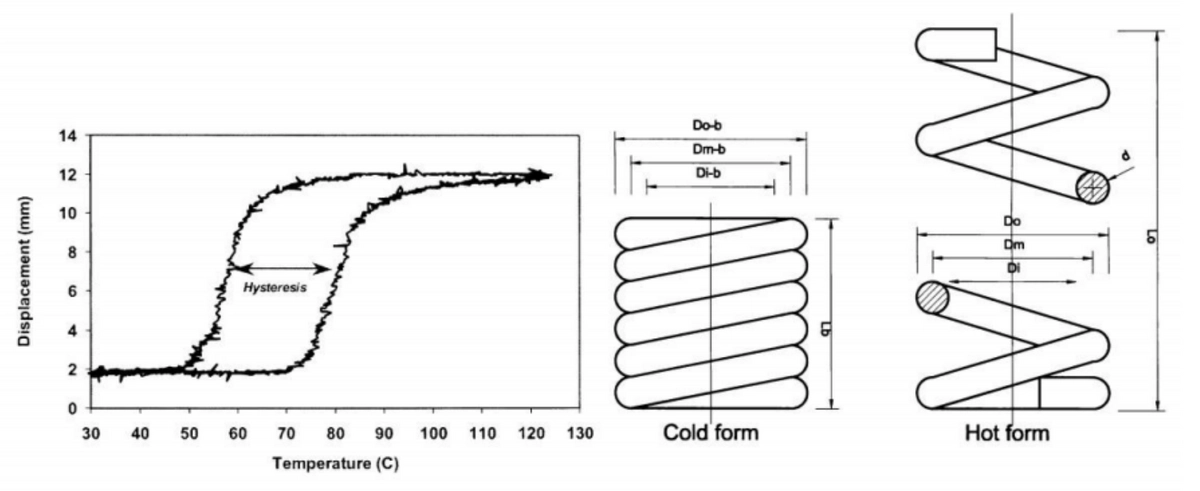
As we peer into the crystal ball of Nitinol technology, it’s clear that this remarkable material is on the brink of some exciting advancements. From the development of more versatile Nitinol strips to enhanced manufacturing processes, researchers are constantly exploring new horizons. These innovations promise to expand the applications of Nitinol Superelastic Sheets in various industries, making them an integral part of future technological solutions.
Emerging Trends in Nitinol Development
The landscape of Nitinol development is evolving rapidly, with emerging trends that aim to maximize its unique properties. One significant trend is the exploration of hybrid materials that combine Nitinol with other alloys to enhance performance while reducing costs—an answer to the question, Why is nitinol so expensive? Moreover, advances in additive manufacturing techniques are allowing for more complex shapes and configurations, paving the way for bespoke solutions tailored to specific needs. As researchers delve deeper into these developments, they are likely to uncover even more applications for this versatile alloy.
Innovations from GEE SMA
GEE SMA has been at the forefront of pushing boundaries in Nitinol technology. Their commitment to innovation has led to breakthroughs such as advanced processing techniques that ensure greater consistency and reliability in products like NT0402 Nitinol Foil and Super Elastic Nitinol sheets. With a focus on sustainability and efficiency, GEE SMA is not only enhancing product performance but also addressing environmental concerns associated with metal production—truly a win-win scenario.
What is the Purpose of Nitinol?
So what exactly is the purpose of nitinol? At its core, this extraordinary alloy serves multiple functions across various sectors—from medical devices like a nitinol guidewire that offers flexibility and precision during procedures to aerospace components requiring lightweight yet strong materials. Its ability to return to a predetermined shape after deformation makes it invaluable for applications where reliability and resilience are paramount; thus solidifying its place in both current technologies and future innovations.
Conclusion
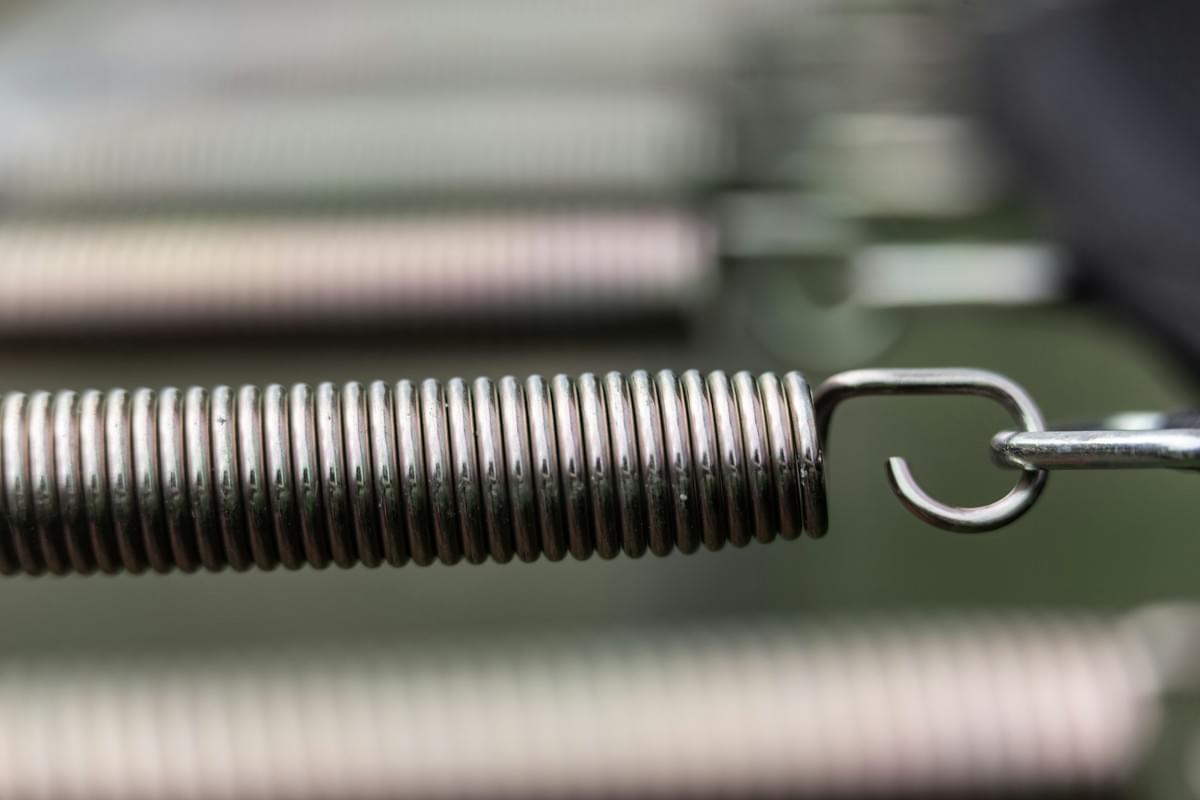
In summary, Nitinol strips represent a remarkable fusion of flexibility and strength, making them invaluable across various industries. Their unique properties, such as superelasticity and shape memory, allow for innovative applications that were once thought impossible. As we delve deeper into the potential of Nitinol Superelastic Sheets, it becomes evident that this material is not just a passing trend but a cornerstone of modern engineering and design.
The Versatility of Nitinol Strips
Nitinol strips are incredibly versatile, finding applications in fields ranging from medical devices to robotics. These strips can easily revert to their original shape after deformation, showcasing their impressive shape memory capabilities. Furthermore, the adaptability of Nitinol allows engineers to create solutions tailored to specific challenges—whether it's in delicate surgical procedures or innovative consumer products.
Important Applications of Nitinol Superelastic Sheet
The Nitinol Superelastic Sheet has transformed numerous industries with its ability to absorb shock and return to its original form under stress. One notable application is within the realm of medical devices; for instance, what is a nitinol guidewire? It’s an essential tool used in minimally invasive surgeries due to its flexibility and resilience. Beyond medicine, these sheets are also employed in aerospace and automotive sectors where lightweight yet strong materials are paramount.
Embracing Nitinol in Future Innovations
As we look toward the future, embracing advancements in Nitinol technology could lead to groundbreaking innovations that enhance everyday life. Emerging trends suggest that the demand for super elastic Nitinol will only increase as industries seek lighter and stronger materials—after all, why is nitinol so expensive? The investment pays off when considering its unparalleled performance compared to traditional metals like titanium; is nitinol stronger than titanium? In many cases, yes! With ongoing research into products like NT0402 Nitinol Foil, we can anticipate even more exciting developments on the horizon.