Introduction
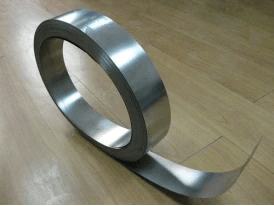
Nitinol strips, a fascinating blend of nickel and titanium, have garnered attention for their unique properties and versatile applications. Often referred to as shape memory alloys, these materials can remember their original shape after being deformed, leading many to ask: What is the purpose of nitinol? With an array of uses spanning various industries—from medical devices to robotics—nitinol strips are not just a scientific curiosity; they are a practical solution for modern engineering challenges.
Understanding Nitinol Strips
At its core, a nitinol strip is more than just a piece of metal; it embodies the remarkable characteristics of superelasticity and shape memory effects. These strips can undergo significant deformation and return to their original form when heated or subjected to specific conditions. This unique behavior raises questions about the broader implications of nitinol in technology and medicine, prompting inquiries such as: Is nitinol stronger than titanium? The answer lies in understanding how these materials interact under stress and strain.
The Unique Properties of Nitinol
The standout features of nitinol include its superelasticity—a property that allows it to endure large strains without permanent deformation—and its ability to revert to a predetermined shape upon heating. These characteristics make nitinol strips highly desirable in applications requiring flexibility and resilience, particularly in medical devices like guidewires. Yet, with all these advantages comes the question: Why is nitinol so expensive? The complex manufacturing processes involved in producing high-quality nitinol contribute significantly to its cost.
Applications Across Industries
Nitinol's adaptability has led it into diverse fields such as aerospace, automotive engineering, and especially medicine—where it plays a crucial role in devices like stents and guidewires. For instance, what is a nitinol guidewire? It’s an essential tool used during minimally invasive surgeries that benefits from the material's flexibility and strength. As industries continue exploring new ways to leverage super elastic nitinol strips, the future looks promising for this innovative alloy.
What is the Purpose of Nitinol?
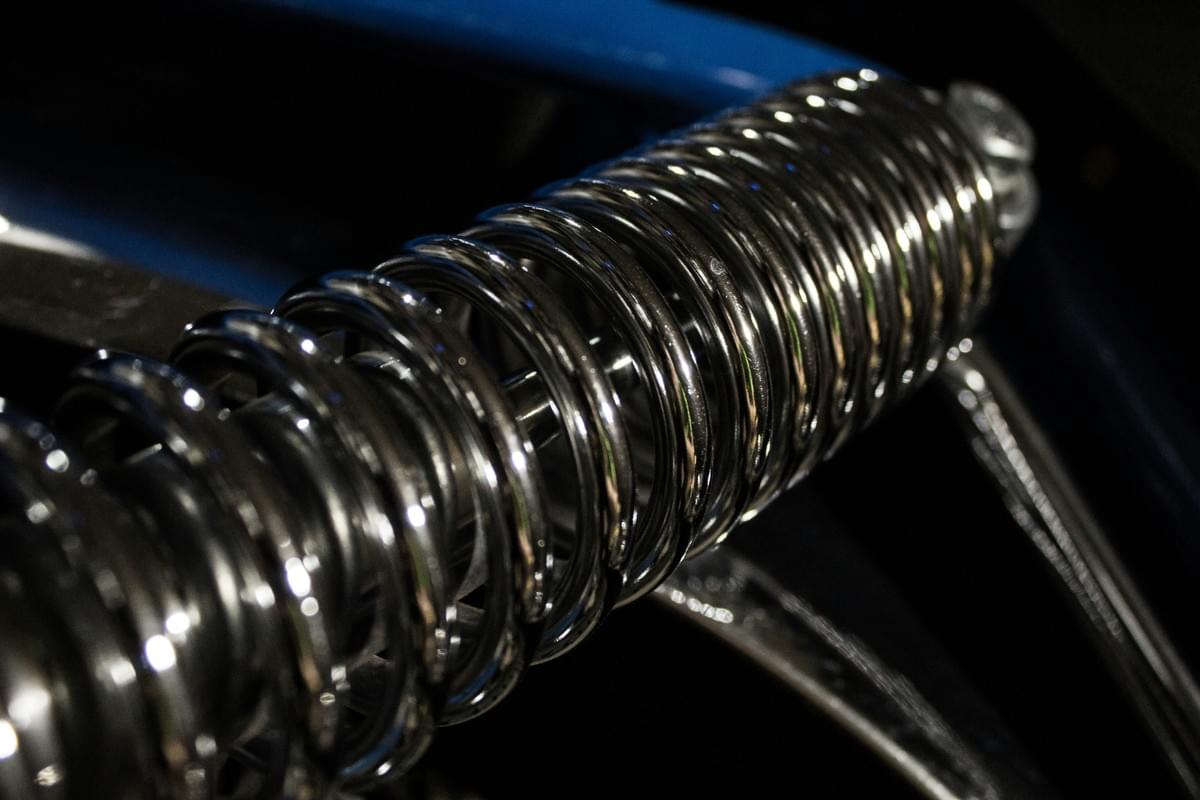
Nitinol, a remarkable alloy of nickel and titanium, has gained significant attention in various industries due to its unique properties. But what is the purpose of nitinol? Its ability to undergo phase transformations allows it to be used in applications ranging from medical devices to actuators in robotics, making it a versatile material.
Overview of Shape Memory Alloys
Shape memory alloys (SMAs) are materials that can return to a predetermined shape when heated above a certain temperature. Nitinol is one of the most well-known SMAs, exhibiting both shape memory and superelasticity. This means that nitinol strips can be deformed at room temperature but will revert back to their original form upon heating, showcasing an extraordinary level of adaptability.
Benefits of Nitinol Strips
One major benefit of nitinol strips is their superelasticity, which allows them to absorb significant amounts of stress without permanent deformation. This property makes them ideal for applications where flexibility and resilience are paramount—think guidewires in medical procedures or components in robotic systems. Additionally, nitinol strips are biocompatible, making them suitable for use within the human body without adverse reactions.
Real-World Applications
The real-world applications for nitinol strips are vast and varied. In medicine, these strips are commonly utilized in devices such as stents and guidewires—what is a nitinol guidewire? It’s an essential tool that enhances navigation through blood vessels during surgical procedures due to its flexibility and strength. Beyond healthcare, industries like automotive and aerospace leverage the unique properties of nitinol for sensors and actuators that require reliable performance under extreme conditions.
How Do Super Elastic Nitinol Strips Work?
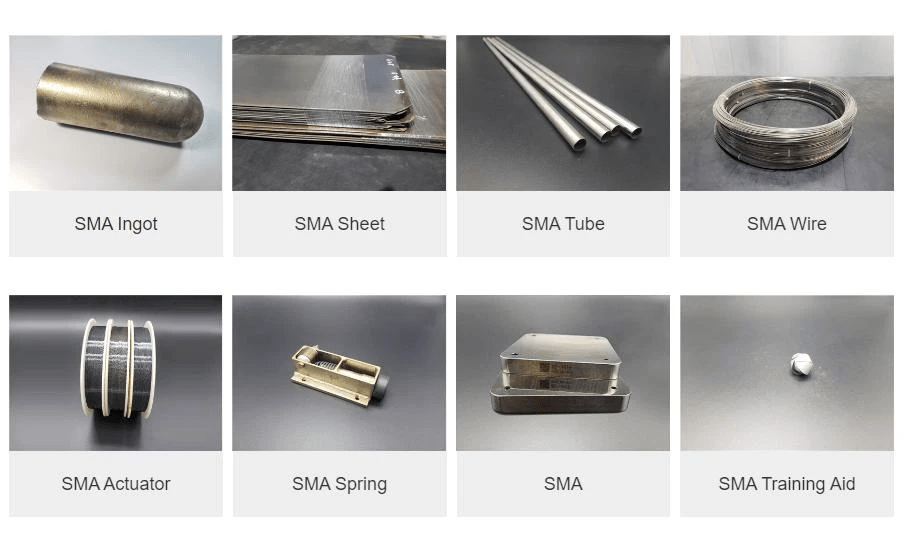
Super elastic nitinol strips are fascinating materials that combine unique properties with innovative applications. Understanding how these strips function can shed light on their purpose and advantages in various industries, particularly in medical devices. With their ability to return to a predetermined shape when heated, nitinol strips provide exceptional versatility and reliability.
The Science Behind Superelasticity
Superelasticity is a remarkable phenomenon exhibited by nitinol strips, allowing them to undergo significant deformation and return to their original shape without permanent changes. This occurs due to a phase transformation between the austenite and martensite structures of the nitinol alloy, triggered by stress rather than temperature changes alone. When subjected to stress, the material can stretch up to eight times its original length before returning to its initial form, making it an ideal candidate for applications requiring flexibility and resilience.
The question often arises: what is the purpose of nitinol? In many cases, it serves as an essential component in medical devices where precision and reliability are paramount. Its superelastic properties enable it to withstand extreme conditions while maintaining performance, highlighting why it's becoming increasingly popular across various sectors.
Comparison with Traditional Materials
When comparing super elastic nitinol strips with traditional materials like stainless steel or titanium, it's clear that nitinol offers distinct advantages. Traditional materials often lack the same degree of flexibility and shape memory capabilities that make nitinol so appealing for dynamic applications. While titanium is known for its strength—leading some to wonder if is nitinol stronger than titanium?—nitinol’s unique combination of strength and elasticity can outperform traditional options in specific contexts.
Additionally, traditional materials may not exhibit the same level of fatigue resistance over time as super elastic nitinol strips do. This durability translates into longer-lasting products that require less frequent replacement or repair—a crucial factor in industries like healthcare where performance directly impacts patient outcomes. Thus, understanding these comparisons helps clarify why many engineers opt for super elastic nitinol over conventional materials.
Use Cases in Medical Devices
The use cases for super elastic nitinol strips in medical devices are numerous and impactful. One standout application is within guidewires—what is a nitinol guidewire? Essentially, these specialized tools aid in navigating complex vascular pathways during procedures like angioplasty or stent placement. The inherent flexibility of super elastic nitinol allows these guidewires to maneuver through tight spaces without compromising structural integrity.
Moreover, other medical devices such as stents benefit from the properties of super elastic nitinol strips as well; they can expand upon deployment yet remain flexible enough not to cause damage during insertion or movement within the body. As healthcare continues evolving towards minimally invasive techniques that prioritize patient safety and comfort, innovations using super elastic nitinol will undoubtedly play a pivotal role moving forward.
What is a Nitinol Guidewire?
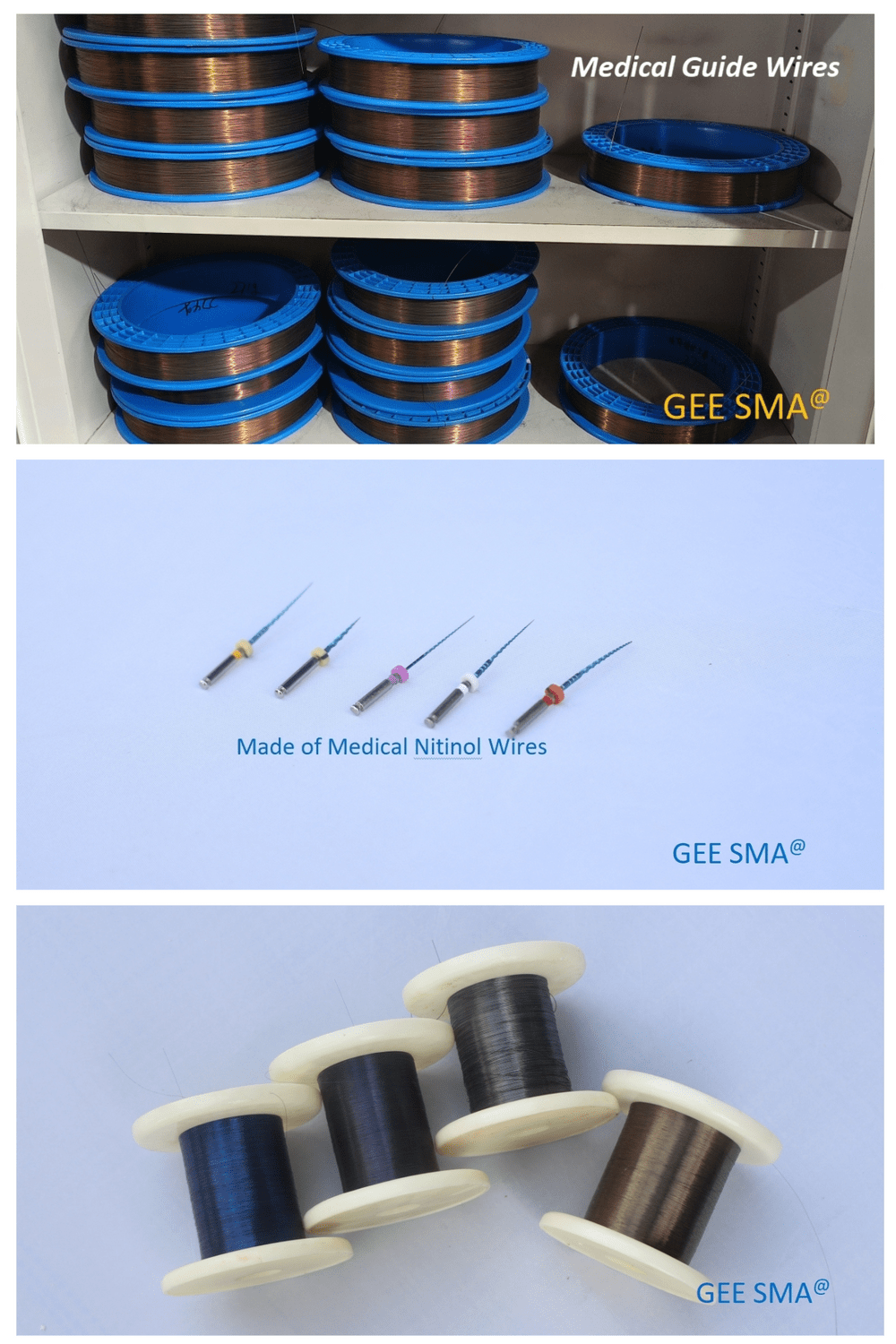
Nitinol guidewires are specialized medical devices made from nitinol, a unique alloy of nickel and titanium, known for its exceptional properties like superelasticity and shape memory. These guidewires play a crucial role in various minimally invasive procedures, allowing physicians to navigate complex anatomical pathways with precision. Understanding the functionality and importance of nitinol guidewires sheds light on their transformative impact on modern medicine.
Functionality and Importance
At its core, the purpose of a nitinol guidewire is to facilitate the delivery of other medical instruments through the vascular system or other bodily pathways. By providing an initial point of access, these guidewires enable the safe navigation through tight spaces, curvatures, and challenging environments within the body. The importance of nitinol guidewires cannot be overstated; they are vital in procedures such as angioplasty, stent placement, and catheterization.
In addition to their primary function, nitinol guidewires enhance procedural efficiency by reducing complications associated with traditional methods. Their flexibility allows them to conform to the anatomy without causing trauma or injury to surrounding tissues. Thus, understanding what is the purpose of nitinol becomes clearer: it’s about improving patient outcomes while minimizing risks during intricate medical interventions.
How Nitinol Enhances Performance
The performance enhancement provided by nitinol in guidewires stems from its unique superelastic properties which allow it to return to its original shape after deformation. This characteristic enables these wires to navigate around bends and curves without breaking or kinking—an essential feature when maneuvering through complex vascular structures. Compared to traditional materials like stainless steel or even titanium, which can be rigid and prone to fracture under stress, nitinol strips demonstrate remarkable resilience.
Furthermore, the temperature-responsive nature of nitinol means that these guidewires can change their stiffness based on body temperature—becoming more flexible when heated and returning to a more rigid state when cooled down after use. This adaptability not only improves handling during procedures but also contributes significantly to patient safety by reducing potential injuries during insertion or removal processes. When considering if nitinol is stronger than titanium for specific applications like this one, it’s clear that strength isn’t just about raw power; it’s also about how materials behave under different conditions.
Common Applications in Medicine
Nitinol guidewires find widespread use across various medical specialties due to their versatility and effectiveness in enhancing procedural outcomes. In cardiology, they are crucial for guiding catheters into coronary arteries during angioplasty procedures—helping open blocked vessels safely and effectively while minimizing damage to surrounding tissues. Similarly, in gastroenterology and urology fields, these wires assist in navigating complex anatomical structures for interventions such as stone retrieval or stent placement.
Beyond just cardiovascular applications, you’ll find that nitinol strips are equally valuable in orthopedic surgeries where precise navigation is paramount for achieving successful outcomes with minimal invasiveness. The ability of these guides not only streamlines surgical processes but also significantly reduces recovery times for patients—a win-win scenario! As we explore why is nitinol so expensive compared to other materials used in similar applications later on, consider how its superior performance justifies its cost across diverse medical uses.
Is Nitinol Stronger Than Titanium?
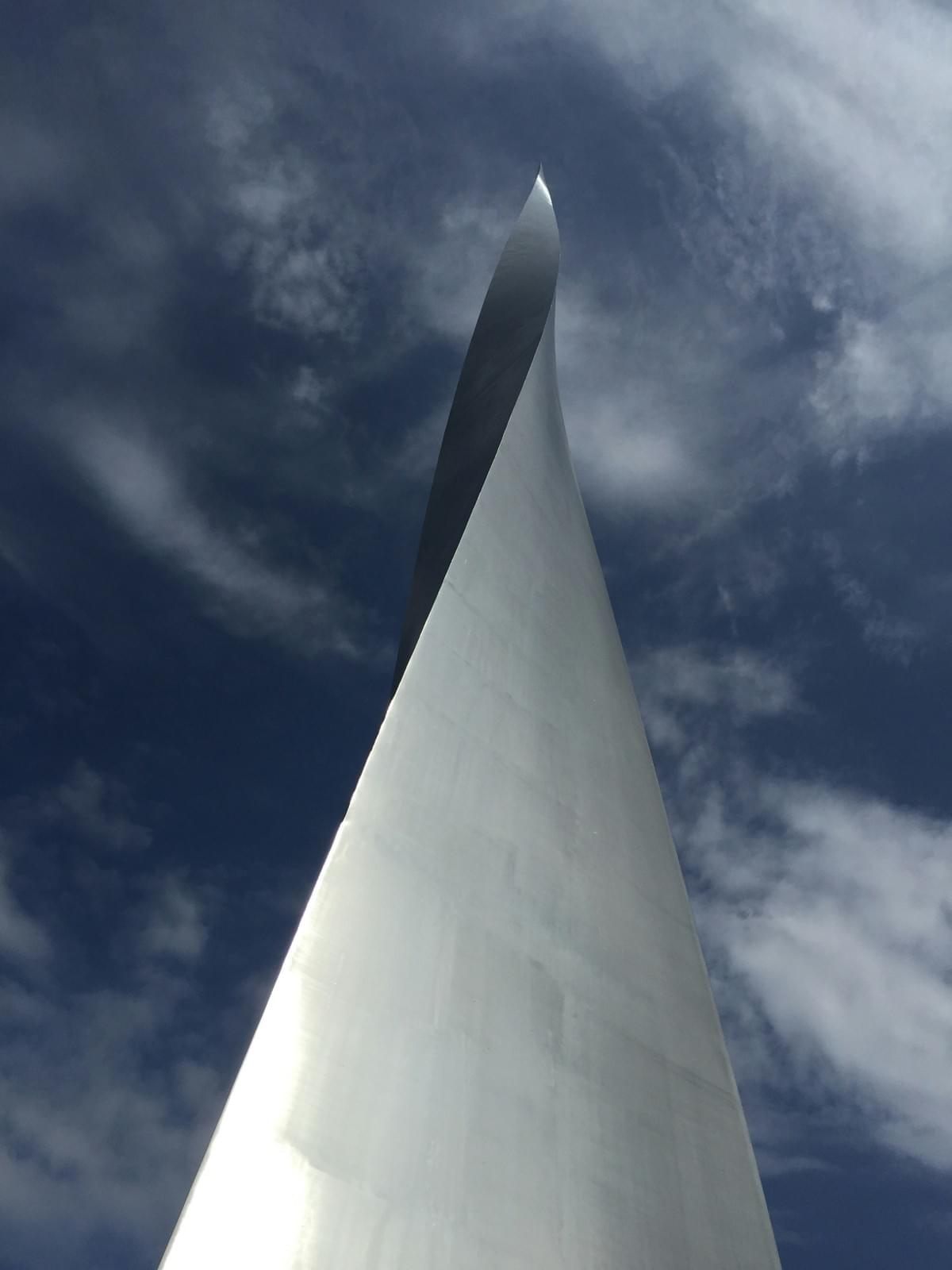
When comparing materials in engineering and medical applications, the debate often arises: is nitinol stronger than titanium? Both materials have unique properties that make them suitable for various uses, but their strengths lie in different areas. Understanding how a nitinol strip or plate measures up against titanium can illuminate their respective advantages and limitations.
Material Properties Comparison
Nitinol is a nickel-titanium alloy known for its shape memory and superelastic properties, while titanium is renowned for its high strength-to-weight ratio and corrosion resistance. In terms of tensile strength, titanium generally outperforms nitinol; however, nitinol’s superelasticity allows it to undergo significant deformation without permanent damage. This means that while a nitinol strip may not be as strong as titanium in raw strength tests, its ability to return to its original shape after being deformed gives it an edge in specific applications.
Strength and Flexibility Analysis
The flexibility of super elastic nitinol strips makes them particularly appealing for medical devices like guidewires, where maneuverability is key. While titanium boasts impressive rigidity and durability under stress, it lacks the same level of flexibility that allows a nitinol strip to bend and twist without breaking. Thus, the choice between these materials often depends on the application; for instance, when designing a device that requires both strength and flexibility—like a nitinol guidewire—nitinol may prove more advantageous despite not being outright stronger than titanium.
Implications for Engineering
The implications of choosing between nitinol and titanium are vast in engineering contexts. Engineers must consider factors like cost (hint: why is nitinol so expensive?), intended use, and performance requirements when selecting materials for their projects. The unique properties of both materials allow them to shine in different scenarios—while some applications may benefit from the tensile strength of titanium, others will thrive on the superelasticity of a nitinol strip or plate.
Why is Nitinol So Expensive?
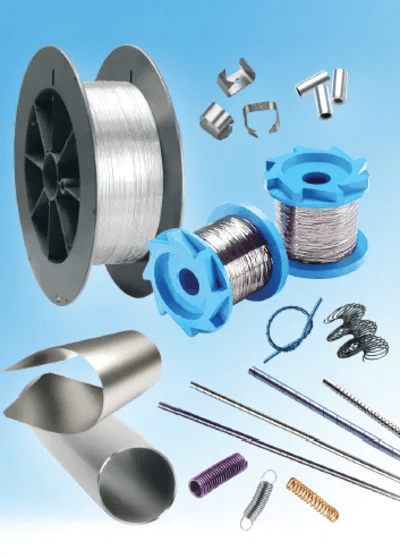
Nitinol, a remarkable alloy known for its unique properties, comes with a price tag that often raises eyebrows. The cost of nitinol strips and other forms, such as nitinol plates, can be attributed to several key factors ranging from manufacturing challenges to economic influences. Understanding why nitinol is so expensive helps clarify its value in applications like medical devices and beyond.
Manufacturing Challenges
Producing high-quality nitinol strips involves intricate processes that require precision and expertise. The manufacturing of super elastic nitinol strips demands stringent temperature control and specific alloy compositions to achieve the desired shape memory characteristics. This complexity not only adds to the production time but also necessitates specialized equipment, which further drives up costs.
Moreover, the process of fabricating nitinol guidewires is particularly challenging due to their need for flexibility and strength while maintaining their unique properties. Each step in creating these components must be meticulously monitored to ensure consistency and performance, which can lead to increased labor costs. Consequently, these manufacturing hurdles contribute significantly to the overall expense associated with nitinol products.
Material Sourcing and Quality Control
The sourcing of raw materials for creating nitinol strips is another factor that impacts pricing. The primary elements used in producing this alloy—nickel and titanium—can fluctuate in market value based on global supply chains and demand dynamics. This variability means manufacturers must navigate an unpredictable landscape when procuring materials necessary for high-quality nitinol production.
In addition to sourcing challenges, maintaining rigorous quality control standards plays a crucial role in driving up costs. Manufacturers must conduct extensive testing on every batch of nitinol strip or plate produced to ensure they meet stringent industry regulations—especially in critical applications like medical devices where reliability is paramount. This commitment to quality not only safeguards end-users but also adds layers of expense throughout the production process.
Economic Factors Affecting Pricing
Economic conditions significantly influence the pricing structure for various materials, including nitinol strips and guidewires. Factors such as tariffs on imported metals or changes in trade policies can create additional financial burdens for manufacturers who rely on international suppliers for raw materials essential in producing super elastic nitinol strips. These economic pressures inevitably trickle down into consumer prices.
Furthermore, as demand grows across industries—from healthcare innovations using nitinol guidewires to aerospace applications—the competition among manufacturers intensifies, leading companies to invest more heavily in research and development (R&D). While this investment is crucial for advancing technology related to what is the purpose of nitinol?, it also contributes indirectly to higher costs passed onto consumers seeking these advanced solutions. Ultimately, understanding why nitinol is so expensive reveals a complex interplay of factors that underscore its value across various applications.
Conclusion
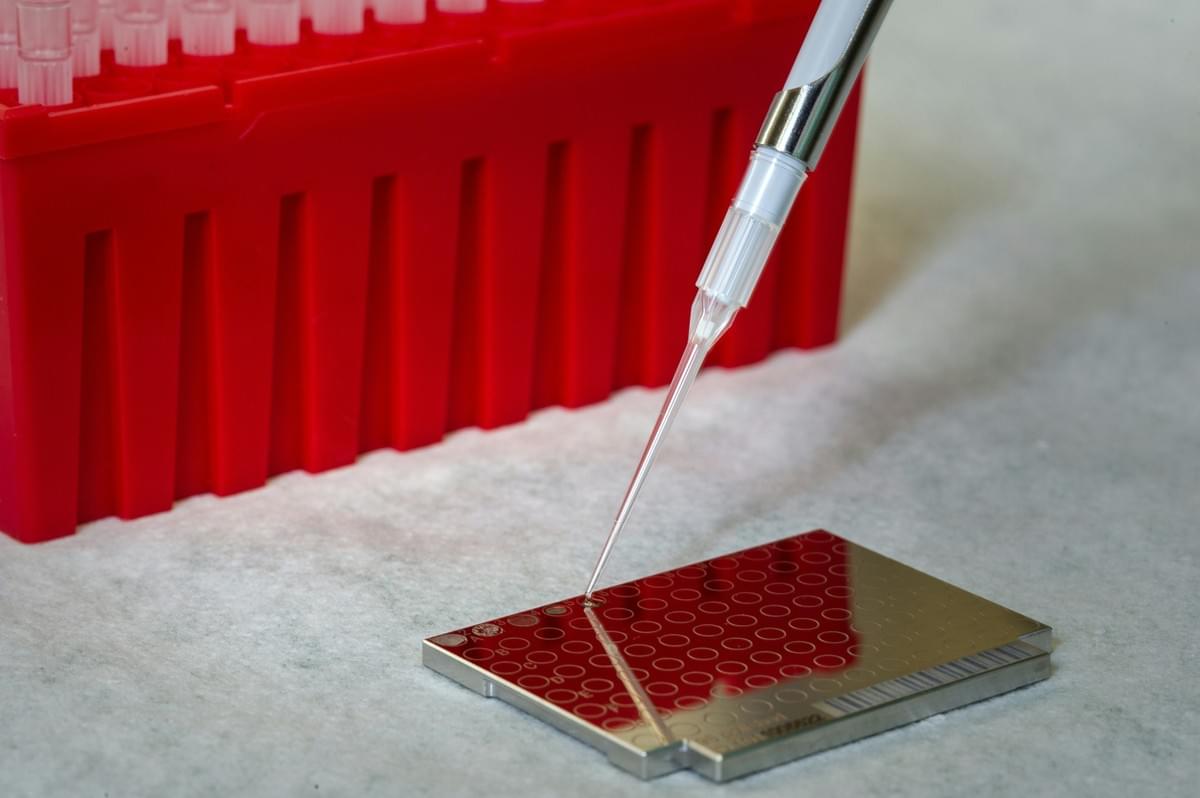
Nitinol strips have revolutionized various industries with their unique properties, paving the way for innovative applications that were once thought impossible. As we look to the future, the demand for these versatile materials is expected to grow, driven by advancements in technology and an increasing understanding of their capabilities. From medical devices to aerospace engineering, nitinol's adaptability will continue to inspire new solutions and applications.
The Future of Nitinol Strips
The future of nitinol strips seems bright, as researchers are continually exploring new functionalities and enhancements. With ongoing studies into improving their performance and reducing costs, we may soon see even more widespread use in critical sectors such as healthcare and robotics. Additionally, the integration of smart technologies with nitinol strips could lead to groundbreaking innovations that further expand their potential.
GEE SMA's Innovations in Nitinol
GEE SMA has been at the forefront of advancing nitinol technology by developing high-quality nitinol strips and plates tailored for specific applications. Their commitment to innovation ensures that they stay ahead in a competitive market while addressing common questions like What is the purpose of nitinol? and Why is nitinol so expensive? By focusing on research and development, GEE SMA continues to enhance the performance characteristics of super elastic nitinol strips, making them indispensable across various industries.
Final Thoughts on Nitinol Applications
In summary, understanding what a nitinol guidewire is or whether is nitinol stronger than titanium? opens up a world of possibilities for engineers and designers alike. The combination of strength, flexibility, and unique properties makes nitinol strips essential in many high-performance applications. As we continue to explore these fascinating materials' potential uses, it's clear that they will play a pivotal role in shaping the future landscape across multiple fields.