Introduction
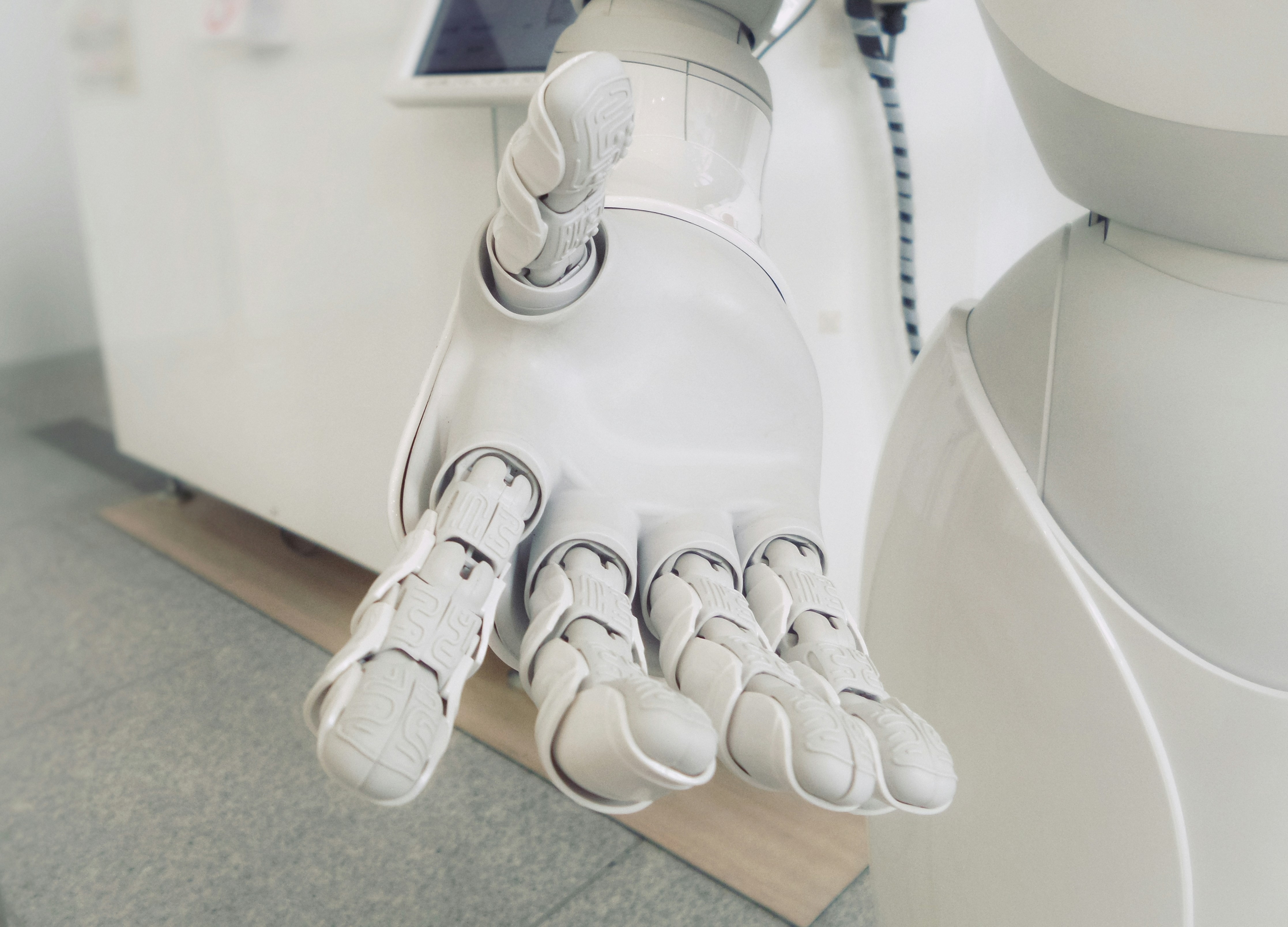
In the ever-evolving landscape of technology, robotics stands out as a field that continually pushes the boundaries of innovation. From the early mechanical automata to today's sophisticated machines, robotics has undergone significant transformation. Central to this evolution is the integration of advanced materials like shape memory alloys, which have revolutionized how we think about actuation in robotic systems.
The Evolution of Robotics
The journey of robotics began with simple mechanical devices designed for repetitive tasks, but it has rapidly progressed into a realm where robots can learn, adapt, and perform complex functions. This evolution has been fueled by advancements in materials science and engineering, leading to the development of more efficient and responsive actuators. Among these breakthroughs are shape memory alloy linear actuators that utilize unique properties to enhance robotic movement and functionality.
What are Shape Memory Alloys?
Shape memory alloys (SMAs) are remarkable materials capable of returning to a predetermined shape when subjected to specific temperatures or stimuli. These alloys exhibit a fascinating phenomenon known as the shape memory effect, which enables them to transform between two distinct shapes—one at lower temperatures and another at higher temperatures. In robotic applications, SMAs are often utilized in various forms such as shape memory alloy wire or nitinol linear actuators, providing unparalleled versatility in design and function.
Applications of Shape Memory Actuators
Shape Memory Actuators have found their way into numerous applications across different industries due to their lightweight nature and efficient performance. From aerospace engineering to medical devices, these actuators enable precise movements that were once deemed impossible with traditional mechanisms. The use of muscle wire actuators exemplifies this trend; they offer innovative solutions for soft robotics and prosthetics by mimicking natural muscle movements while remaining compact and energy-efficient.
Understanding Shape Memory Alloy Linear Actuators
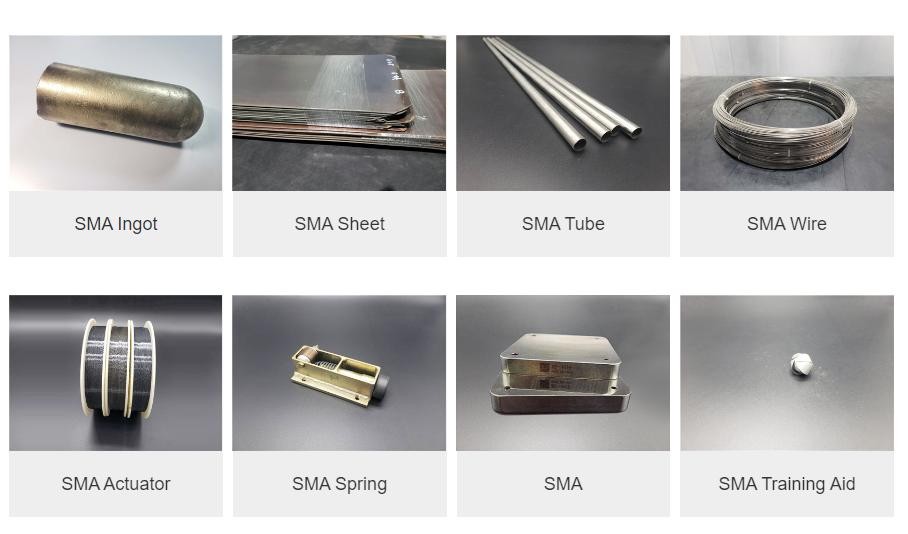
Shape memory alloy linear actuators are revolutionizing the field of robotics with their unique properties and applications. These devices utilize materials that can remember their original shape when subjected to specific thermal conditions, allowing for precise movement and control. The integration of Shape Memory Actuators, particularly Nitinol linear actuators, has transformed traditional robotic mechanisms into more efficient and lightweight systems.
How Shape Memory Works
At the heart of shape memory alloy technology lies a fascinating phenomenon known as shape memory effect (SME). When a shape memory alloy wire is heated above its transformation temperature, it undergoes a phase change that allows it to return to its pre-deformed shape. This unique characteristic enables the creation of muscle wire actuators that can contract or expand in response to temperature changes, making them ideal for applications requiring rapid actuation.
The mechanics behind this process involve two distinct phases: the martensitic phase, which is stable at lower temperatures and allows deformation, and the austenitic phase, which is stable at higher temperatures where the material returns to its original form. This dual-phase behavior is what makes a shape memory alloy actuator so versatile in various robotic applications. By carefully controlling temperature variations through electrical or thermal means, engineers can harness this effect for precise movements in robotic systems.
Benefits of Using Shape Memory Alloy
One of the standout benefits of using shape memory alloys in robotics is their lightweight nature compared to traditional actuators. This reduction in weight not only enhances energy efficiency but also improves overall system performance by allowing robots to operate faster and more effectively. Additionally, SMA actuators provide significant design flexibility; they can be easily integrated into compact spaces where conventional motors may not fit.
Another advantage lies in their low power consumption; Nitinol linear actuators require minimal energy input while delivering impressive force output. This efficiency makes them particularly appealing for battery-operated devices or applications requiring prolonged operation without frequent recharging or maintenance. Furthermore, these actuators exhibit high durability due to their fatigue-resistant properties, ensuring long-lasting performance even under repeated use.
Key Players in SMA Technology
The landscape of shape memory alloy technology features several key players who are pushing the boundaries of innovation within this field. Companies specializing in SMA technology have emerged as leaders by developing advanced materials and solutions tailored specifically for robotics and automation industries. Notable names include GEE SMA, which focuses on pioneering Nitinol actuator designs that cater to diverse industrial needs.
In addition to GEE SMA, other companies like Dynalloy and Smart Material Solutions are also contributing significantly by offering cutting-edge products such as muscle wire actuators and custom-shaped SMA components designed for specific applications. These organizations emphasize quality control and customer satisfaction while continuously striving for technological advancements that enhance performance metrics across various sectors utilizing shape memory alloys.
As we delve deeper into understanding these remarkable technologies within robotics, it's clear that shape memory alloys hold immense potential for future innovations driven by creativity and engineering excellence.
The Role of Nitinol Linear Actuators
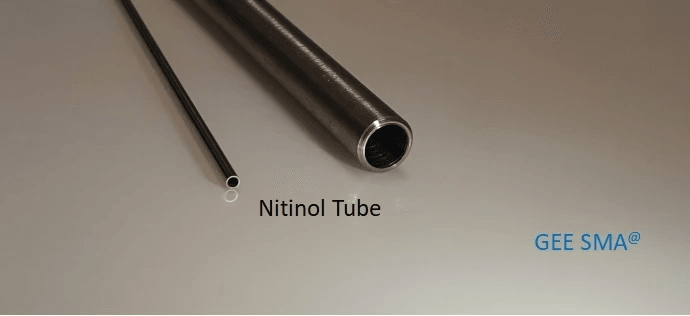
Nitinol linear actuators are revolutionizing the landscape of robotics, providing unique capabilities that traditional actuators simply can’t match. These devices utilize shape memory alloys (SMAs) like Nitinol to create movement through temperature changes, enabling precise control in a compact form factor. With their lightweight design and inherent flexibility, Nitinol linear actuators are becoming indispensable in various applications across industries.
Features of Nitinol Linear Actuators
One standout feature of Nitinol linear actuators is their ability to undergo significant deformation while maintaining a high strength-to-weight ratio. This means they can exert considerable force without adding bulk, making them ideal for applications where space is at a premium. Additionally, the shape memory alloy wire used in these actuators allows for rapid response times and excellent durability, further enhancing their appeal in robotic systems.
Another remarkable characteristic is the self-heating property of the nitinol actuator, which enables it to transition from one shape to another when electrical current is applied. This feature allows for seamless integration into various robotic designs where traditional motors might struggle with size or weight constraints. Furthermore, their resilience against fatigue makes shape memory alloy actuators reliable over extended periods of use.
Comparison with Traditional Actuators
When comparing nitinol linear actuators to traditional electric or pneumatic actuators, several key differences emerge that highlight the advantages of SMA technology. Traditional actuators often require bulky components and complex gear systems to achieve movement, which can lead to increased weight and maintenance challenges. In contrast, shape memory alloy linear actuators offer a more streamlined design with fewer moving parts, reducing both complexity and potential points of failure.
Moreover, while traditional systems may consume more energy due to constant power requirements for maintaining position or torque output, nitinol actuators only require power during actuation phases. This results in improved energy efficiency—an essential factor for battery-powered robotic applications where longevity is crucial. Additionally, the smooth operation and precise control afforded by muscle wire actuator technology allow for delicate tasks that would be difficult with conventional methods.
Real-World Applications
The versatility of Nitinol linear actuators has led to their adoption in numerous real-world applications across diverse fields such as medical devices and aerospace engineering. For instance, surgical robots utilize shape memory alloy actuators for minimally invasive procedures due to their compact size and ability to provide fine motor control without damaging surrounding tissues. This precision enhances patient outcomes while also streamlining surgical workflows.
In aerospace applications, nitinol actuators are employed in adaptive structures that respond dynamically to changing conditions during flight operations—think wings that morph based on aerodynamic needs! Such innovations showcase how shape memory alloy technology can enhance performance while reducing overall weight—a critical consideration in aircraft design where every gram counts.
Additionally, industries like automotive manufacturing are beginning to explore the use of SMA technology for smart seat adjustments or active suspension systems that adaptively respond to road conditions—further demonstrating how nitinol linear actuator capabilities can transform conventional approaches into cutting-edge solutions.
Muscle Wire Actuators: The Future of Robotics
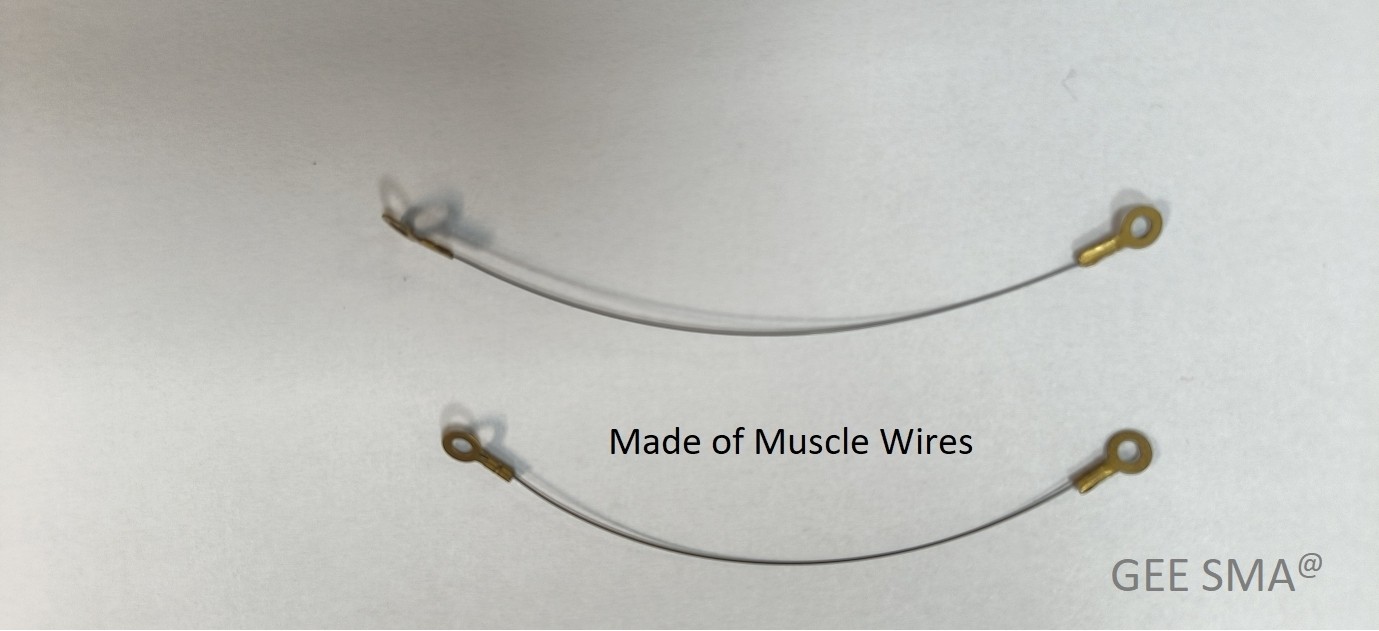
Muscle wire actuators, often referred to as shape memory alloy (SMA) wires, are revolutionizing the way we think about robotics. These ingenious devices leverage the unique properties of shape memory alloys to create motion in a compact and efficient manner. As we delve into the world of muscle wire actuators, it becomes clear that they represent a significant leap forward in actuator technology.
What is Muscle Wire?
Muscle wire is essentially a type of shape memory alloy wire that contracts when heated and returns to its original shape upon cooling. This behavior mimics natural muscle movement, making it an ideal candidate for applications requiring precise control and flexibility. The most commonly used material for muscle wires is Nitinol, a nickel-titanium alloy known for its remarkable ability to undergo phase changes under varying temperatures.
In the realm of robotics, muscle wire actuators are emerging as a game-changer due to their lightweight nature and ease of integration into complex designs. Unlike traditional actuators that can be bulky and cumbersome, muscle wires offer a streamlined alternative that fits seamlessly into various robotic architectures. Their compact size combined with their powerful actuation capability makes them particularly appealing for innovative robotic applications.
Advantages of Muscle Wire Actuators
One of the standout advantages of muscle wire actuators is their energy efficiency; they consume power only when performing work, unlike many traditional actuators that require continuous energy input. This efficiency not only extends battery life in portable robotic systems but also reduces overall operational costs associated with powering these devices. Additionally, shape memory alloy linear actuators can achieve high precision in movement thanks to their inherent responsiveness and control capabilities.
Another significant benefit lies in their design flexibility; muscle wires can be easily shaped or integrated into various configurations without compromising functionality. This adaptability allows engineers and designers to create more sophisticated robotic mechanisms tailored to specific tasks or environments. With advancements in SMA technology, including improved thermal response times, these actuation solutions are becoming even more viable for intricate designs.
Lastly, muscle wire actuators boast low maintenance requirements compared to traditional mechanical systems which often involve wear-and-tear components needing regular servicing or replacement. By minimizing mechanical complexity while maximizing performance reliability, SMA actuators pave the way for longer-lasting robotic systems that can operate efficiently over extended periods.
Innovative Uses in Robotic Design
The versatility of muscle wire actuators has led to groundbreaking applications across various fields within robotics—from soft robotics to prosthetic limbs and beyond. In soft robotics specifically, these shape memory alloy wires enable smoother movements that mimic natural biological functions—think squishy robots capable of navigating through tight spaces or gently interacting with fragile objects without causing damage!
Moreover, Nitinol linear actuators have found their niche within prosthetics by providing users with enhanced mobility options through lightweight yet powerful actuation solutions tailored specifically for individual needs. This customization not only improves user experience but also promotes greater independence among those relying on assistive technologies.
Innovative uses extend further into areas like micro-robotics where precise movements at small scales are crucial; here, SMA actuator technology allows for micro-manipulation tasks such as targeted drug delivery systems or minimally invasive surgical tools—applications poised to reshape medicine as we know it! As research continues on optimizing these fascinating devices’ performance characteristics, one thing remains clear: muscle wire actuators are indeed paving the way towards an exciting future in robotics.
SMA Actuator and Its Impact on Robotics
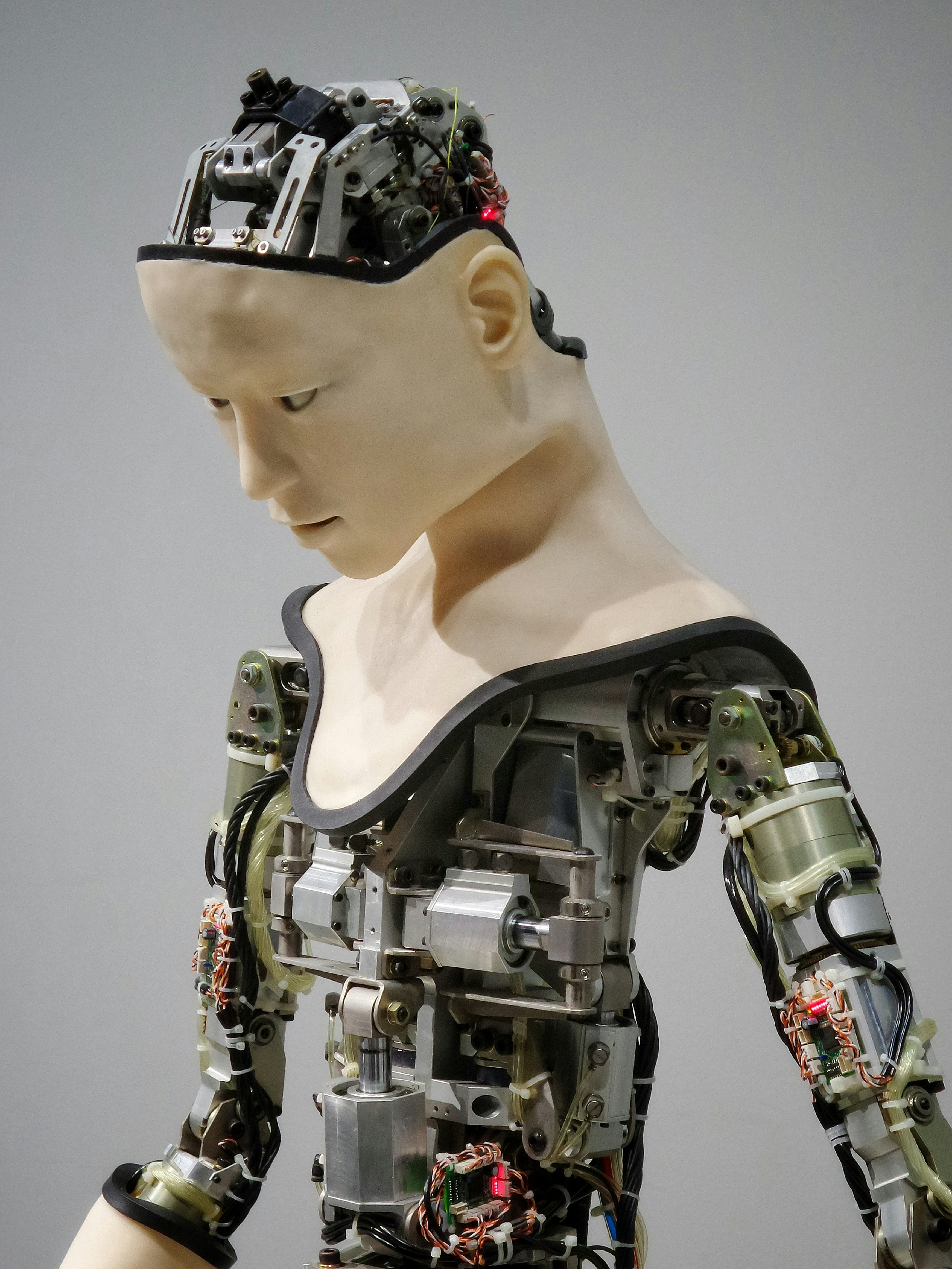
The integration of shape memory alloy (SMA) actuators into robotic systems has revolutionized design paradigms, offering unprecedented flexibility and lightweight solutions. These shape memory alloy linear actuators are not just compact; they also provide remarkable performance characteristics that traditional actuators simply cannot match. With their ability to change shape in response to heat, these devices enable engineers to innovate without being constrained by weight or size limitations.
Design Flexibility and Lightweight Solutions
One of the most significant advantages of using shape memory alloy actuators is their design flexibility. Unlike conventional actuators, which often require bulky mechanisms to function, the nimble nature of SMA technology allows for more intricate designs that can fit into tight spaces. This is particularly beneficial in applications such as drones or medical devices, where every gram counts and space is at a premium.
Moreover, Nitinol linear actuators exemplify this lightweight solution; they can be integrated seamlessly into various robotic architectures without adding unnecessary weight. The unique properties of shape memory alloy wire allow for a variety of configurations that enhance both aesthetic appeal and functional capability in robotics. As a result, engineers are increasingly turning to muscle wire actuators for projects where traditional options would fall short.
Enhanced Precision in Robotics
Precision is paramount in robotics, especially when it comes to tasks requiring delicate movements or accurate positioning. Shape memory alloy actuators excel in this area due to their fine control capabilities; they can respond quickly and accurately to electrical stimuli, making them ideal for applications like robotic surgery or automated assembly lines. The inherent ability of these nitinol actuators to produce consistent force with minimal backlash gives them an edge over traditional systems.
Furthermore, the responsiveness of shape memory alloys enables real-time adjustments during operation—this adaptability ensures that robots can perform with exceptional accuracy even under varying conditions or loads. The versatility offered by shape memory alloy linear actuators contributes significantly to enhancing the overall performance and reliability of robotic systems across diverse industries.
Case Studies of Successful Implementations
Several pioneering projects have showcased the transformative impact of SMA technology on robotics through successful implementations across various fields. For instance, a leading medical device company utilized shape memory alloy actuator technology in surgical robots, allowing for minimally invasive procedures with unprecedented precision and control—demonstrating how essential these innovations are in healthcare settings.
Another compelling example involves aerospace engineering; researchers have developed advanced drones powered by muscle wire actuators that optimize flight efficiency while maintaining stability even at high speeds. These case studies illustrate not only the practicality but also the potential for future developments using Nitinol linear actuator technology—paving the way for smarter robots capable of tackling complex challenges.
In summary, the adoption of SMA actuation solutions has set new benchmarks in design flexibility, precision control, and innovative applications within robotics—a trend likely to continue as technologies evolve further.
GEE SMA: Pioneers in Nitinol Technology
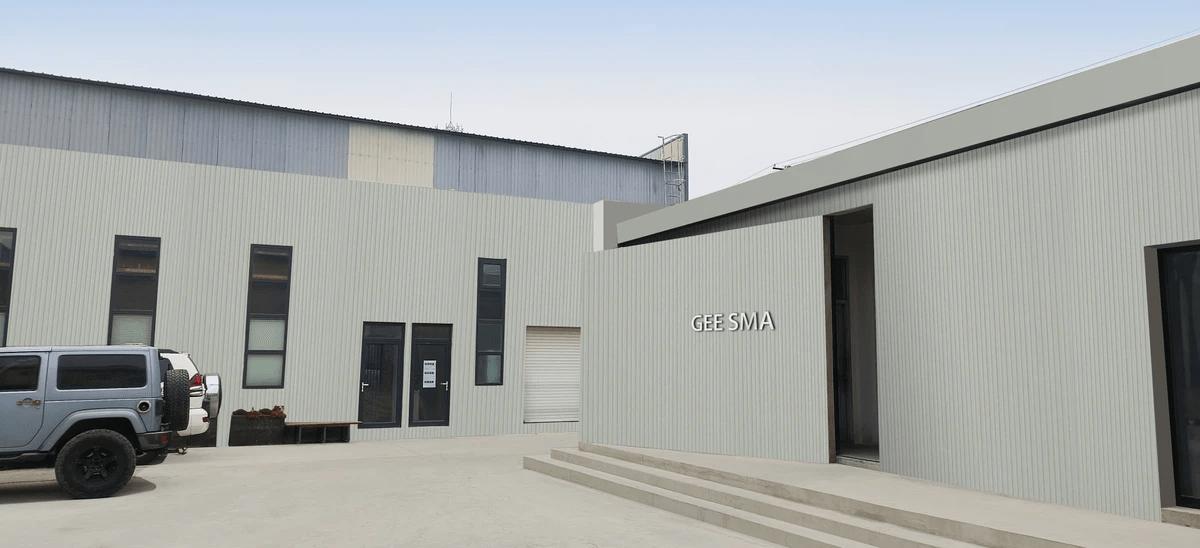
GEE SMA has emerged as a front-runner in the development and application of Nitinol technology, particularly in the realm of shape memory alloys. Their innovations have propelled the capabilities of shape memory actuators, offering remarkable enhancements that cater to various industries. By focusing on cutting-edge research and practical implementations, GEE SMA is redefining what’s possible with shape memory alloy linear actuators.
Overview of GEE SMA’s Innovations
GEE SMA has consistently pushed the boundaries of what's achievable with Nitinol linear actuators. Their research has led to breakthroughs that improve efficiency and functionality, making their shape memory alloy actuator solutions a go-to for engineers and designers alike. With a keen eye on both performance and reliability, GEE SMA’s innovations ensure that each shape memory actuator can withstand the rigors of real-world applications while maintaining precision.
Tailored Solutions for Diverse Needs
Understanding that no two projects are alike, GEE SMA excels at providing tailored solutions to meet diverse needs across various sectors. Whether it’s a muscle wire actuator for robotics or specialized applications requiring unique specifications, their team works closely with clients to develop custom designs using shape memory alloy wire. This level of personalization not only enhances performance but also fosters innovation in how shape memory actuators are utilized across different fields.
Commitment to Quality and Customer Satisfaction
At the heart of GEE SMA's operations lies an unwavering commitment to quality and customer satisfaction. They employ rigorous testing protocols to ensure every nitinol actuator meets high standards before it reaches clients’ hands. By prioritizing customer feedback and continuously refining their products, GEE SMA solidifies its reputation as a trusted provider in the world of shape memory alloy linear actuators.
Conclusion
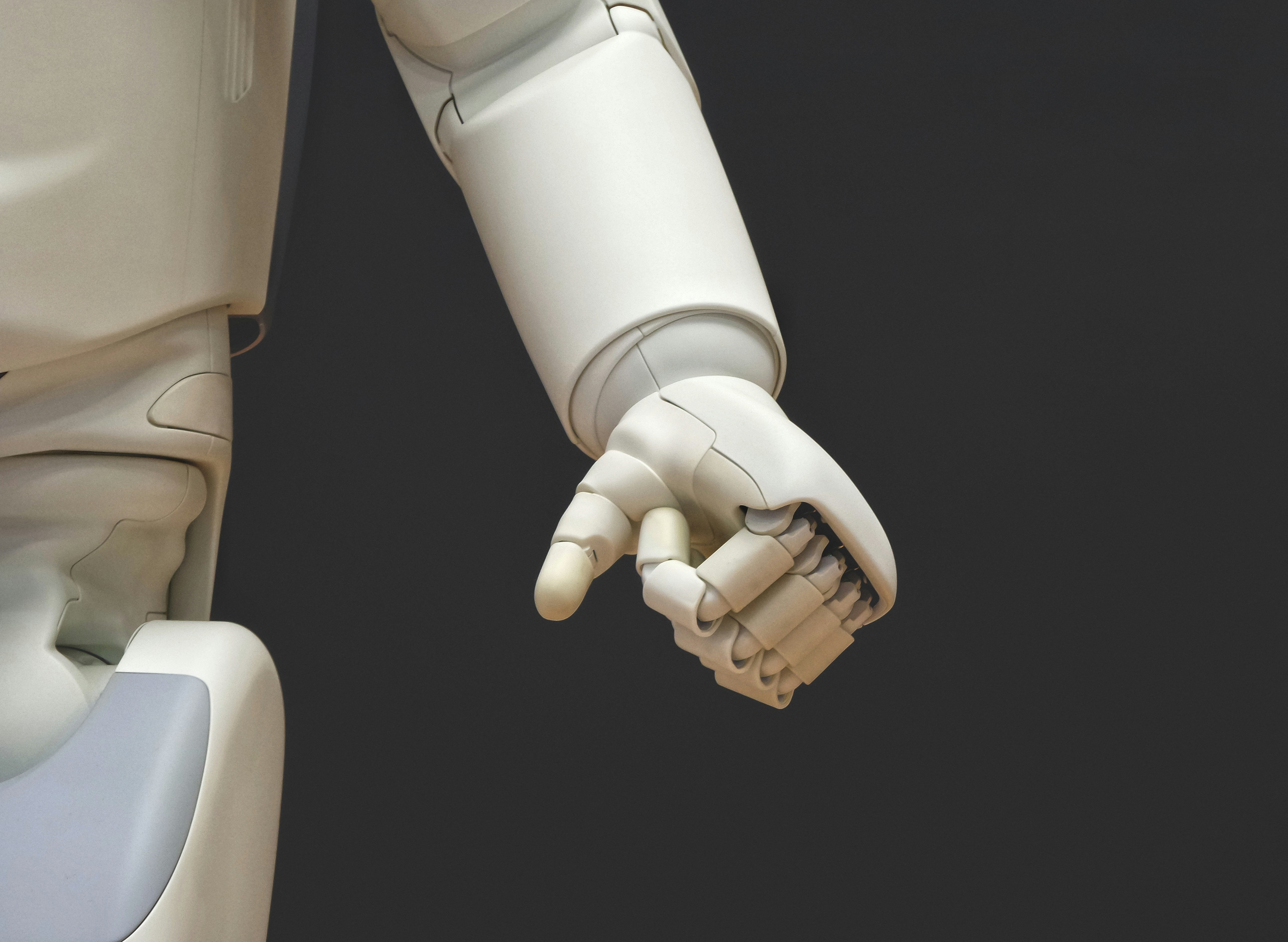
As we stand on the brink of a new era in robotics, the role of shape memory alloy linear actuators is becoming increasingly significant. These innovative devices, powered by the unique properties of shape memory alloys, are not just enhancing existing technologies but also paving the way for entirely new applications. With advancements in materials science and engineering, Shape Memory Actuators are set to redefine what robots can achieve.
The Future of Shape Memory Alloy in Robotics
The future of robotics is bright with the integration of shape memory alloy technology. As we continue to explore the capabilities of shape memory alloy actuators, industries ranging from healthcare to manufacturing will benefit from their lightweight and compact designs. The adaptability and efficiency offered by Nitinol linear actuators will drive innovations that were once thought impossible.
Transforming Robotics with Nitinol Technology
Nitinol technology is at the forefront of this transformation, providing unique features that traditional actuators simply cannot match. By utilizing nitinol actuators, engineers can create systems that respond quickly and efficiently to stimuli, mimicking natural movements more closely than ever before. This level of precision not only enhances robotic performance but also opens doors for real-world applications that require delicate handling and responsiveness.
Embracing Innovation in Actuation Solutions
Embracing innovation means recognizing the potential impact of muscle wire actuators and other SMA technologies on future designs. With a focus on creating smarter, more efficient robots, we can expect a surge in creative solutions that leverage shape memory alloy wire for actuation purposes. As industries adapt to these advancements, it’s clear that the journey toward integrating shape memory alloys into everyday robotics has only just begun.