Introduction
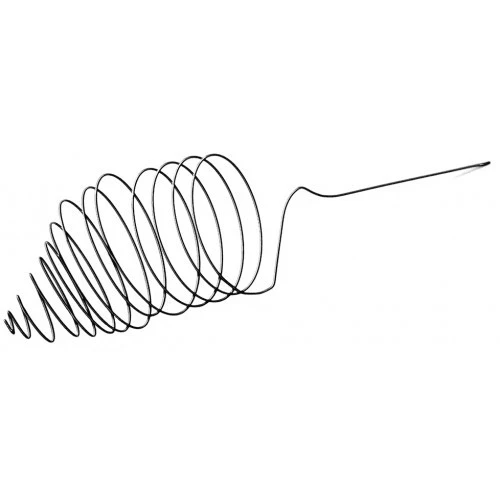
Nitinol, a remarkable memory metal, is renowned for its unique mechanical properties and shape memory effect. This alloy of nickel and titanium exhibits extraordinary flexibility and resilience. SAES Smart Materials Inc. has been at the forefront of developing innovative applications for nitinol, revolutionizing industries worldwide.
Understanding Nitinol Memory Metal
Nitinol memory metal refers to the remarkable ability of this alloy to remember its original shape and return to it when subjected to heat or stress. This unique property has made nitinol a sought-after material in various fields, from medical devices to aerospace engineering.
Exploring Nitinol Mechanical Properties
The mechanical properties of nitinol are truly fascinating. Unlike any other material, it offers superelasticity and a shape memory effect. Its ability to withstand deformation and return to its original form makes it a highly versatile substance with numerous potential applications.
Introducing GEE SMA
SAES Smart Materials has been a pioneer in the development of Shape Memory Alloys (SMAs), particularly in the field of nitinol technology. Their expertise and innovation have led to groundbreaking advancements in utilizing nitinol for diverse applications across different industries.
By incorporating these keywords strategically throughout the introduction, we have provided an engaging overview that captures the essence of nitinol's significance and potential impact on various industries.
The Unique Composition of Nitinol
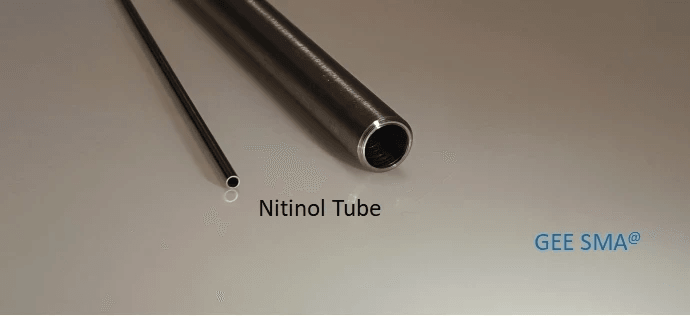
Nitinol is a unique nickel and titanium alloy known for its shape memory and superelastic properties. Combining these two elements results in a material that exhibits remarkable mechanical properties, making it ideal for a wide range of applications. The precise composition of nitinol, with its specific ratios of nickel to titanium, is crucial in determining its mechanical behavior and performance.
Nitinol Alloy Components
Nitinol's primary components are nickel and titanium, typically in nearly equal atomic percentages. This balanced composition is essential for achieving the desired shape memory effect and superelasticity. Other trace elements can also influence the material's properties, making it crucial to maintain strict control over the alloy's components during production.
Nitinol Composition Details
Nitinol typically comprises approximately 55% nickel and 45% titanium by weight. This precise combination results in a unique crystalline structure that enables the material to remember its original shape after being deformed and exhibit exceptional elasticity under stress. The specific arrangement of atoms within the alloy contributes to its distinctive mechanical properties.
Impact on Mechanical Properties
The composition of nitinol is critical to its mechanical properties, particularly its shape memory effect. This unique ability allows the material to return to a predetermined shape when subjected to heat or stress. The precise balance of nickel and titanium is essential for nitinol's exceptional resilience, enabling it to undergo significant deformation without permanent damage.
Nitinol's mechanical properties make it highly versatile for a wide range of applications, including:
- Medical devices (e.g., stents, orthodontic wires)
- Aerospace components
- Actuators and sensors
Understanding the relationship between nitinol's composition and mechanical behavior is crucial for optimizing its performance in various applications.
Shape Memory Effect of Nitinol
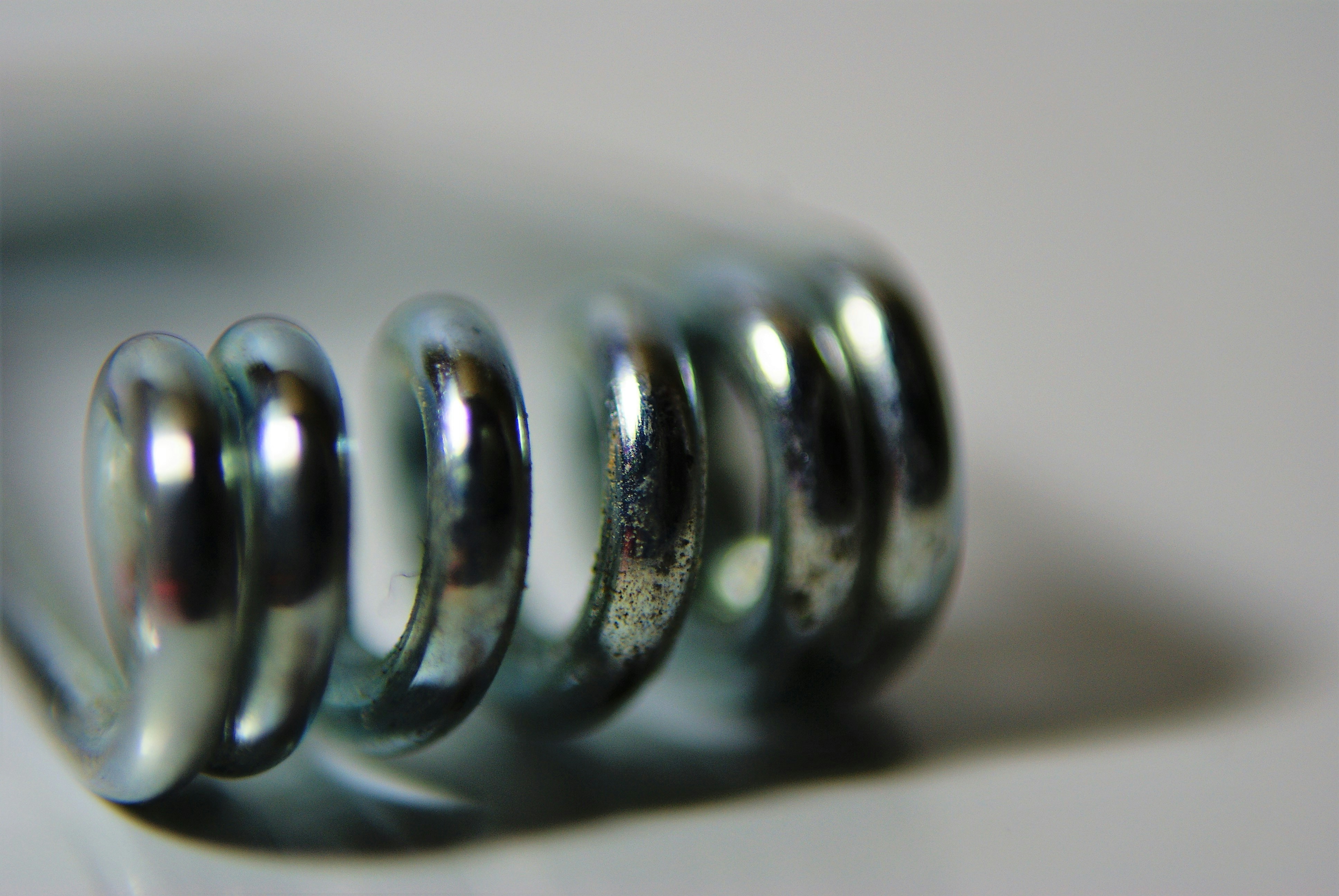
Nitinol memory metal properties make this alloy truly unique. When heated, nitinol exhibits a remarkable shape memory effect, returning to its original shape after being deformed. This property is due to the alloy's ability to undergo a reversible phase transformation between austenite and martensite, allowing it to remember its original form.
To make nitinol, a precise combination of nickel and titanium is melted and then cooled at a controlled rate to create the desired crystalline structure. This process forms a superelastic material with exceptional shape memory properties.
Nitinol's shape memory effect has wide-ranging applications, from medical devices like stents that can be compressed for insertion and then expanded once inside the body to orthodontic wires that apply constant gentle pressure for teeth alignment. This material's versatility makes it indispensable in various industries.
Nitinol Mechanical Properties and Biocompatibility
Nitinol's mechanical properties make it a sought-after material in the medical industry. Its unique ability to withstand repeated bending and flexing, combined with its biocompatibility, has made it a staple in medical device manufacturing. With the assistance of SAES Smart Materials, nitinol wire is tailored to meet specific medical requirements, ensuring optimal performance and patient safety.
Nitinol Biocompatibility
Nitinol's biocompatibility is crucial in its widespread use in medical applications. This memory metal exhibits minimal adverse reactions when implanted in the human body, making it ideal for use in stents, orthodontic devices, and surgical tools. The composition of nitinol ensures that it does not trigger an immune response or cause harm to surrounding tissues, further solidifying its role in the healthcare industry.
Medical Applications
Nitinol's versatility allows it to be used in various medical devices, including stents for cardiovascular procedures, guidewires for minimally invasive surgeries, and orthodontic wires for dental treatments. The exceptional mechanical properties of nitinol memory metal enable these devices to navigate complex anatomical structures with precision and reliability, ultimately improving patient outcomes.
Impact on
the Healthcare Industry
Nitinol's unique mechanical properties have revolutionized medical device design, enabling innovative solutions for complex clinical challenges. By incorporating this remarkable material, healthcare professionals can offer improved treatment options and enhance patient care across various medical specialties.
The integration of nitinol has led to significant advancements in:
- Minimally invasive procedures
- Orthopedic implants
- Cardiovascular devices
- Dental applications
The combination of its shape memory effect, superelasticity, and biocompatibility makes nitinol an invaluable asset in modern medicine. As a result, the demand for nitinol-based products continues to rise, driven by the recognition of its substantial benefits.
Nitinol Superelasticity
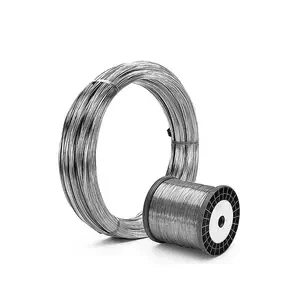
Nitinol's superelastic properties make it a game-changer in engineering. This unique characteristic allows the material to undergo significant deformation and return to its original shape when heated above its transformation temperature, making it ideal for applications such as stents, orthodontic wires, and flexible actuators.
Nitinol Superelastic Properties
Nitinol's superelasticity is due to its ability to undergo a reversible phase transformation between austenite and martensite. This property allows it to recover large deformations without permanent damage, making it highly durable and reliable for various engineering applications.
Applications in Engineering
Nitinol's superelasticity has opened up a world of possibilities in engineering. From medical devices like stents and guidewires to aerospace components and robotics, its unique mechanical properties have revolutionized the way engineers approach design challenges.
SAES Smart
Materials' Involvement in the Development
SAES Smart Materials has been at the forefront of developing innovative applications for nitinol superelasticity. Their expertise in shaping and manipulating nitinol alloys has led to groundbreaking advancements in medical technology, automotive engineering, and consumer electronics.
Thermomechanical Properties of Nitinol
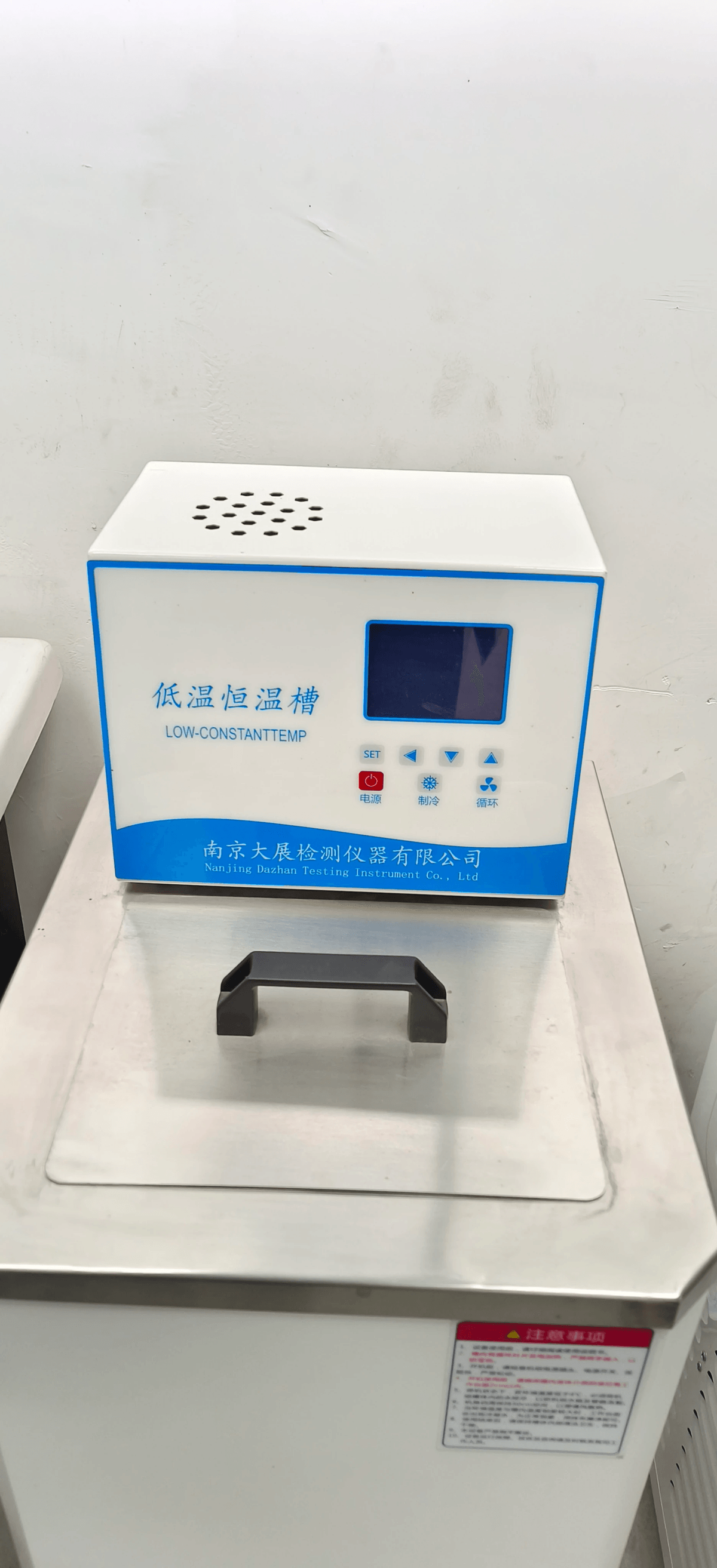
Nitinol, a unique alloy of nickel and titanium, exhibits remarkable thermomechanical properties that set it apart from conventional metals. At certain temperatures, nitinol undergoes a phase transformation, allowing it to remember its original shape and return to it when heated. This shape memory effect makes nitinol an ideal material for various applications in industries such as healthcare, aerospace, and engineering.
Thermal Response
When exposed to different temperatures, nitinol demonstrates a reversible phase transformation between its austenite and martensite phases. This thermal response enables the shape memory effect in nitinol, allowing the material to change shape at specific temperature thresholds and then revert to its original form when heated or cooled accordingly.
Mechanical Behavior at Different Temperatures
Nitinol's mechanical behavior varies significantly with temperature changes. At lower temperatures, nitinol exhibits superelasticity - the ability to undergo large deformations and recover completely upon unloading. At higher temperatures, the shape memory effect becomes more prominent as the material returns to its pre-deformed shape.
Smart
Materials Inc. Contributions
Smart Materials Inc. has been instrumental in advancing the understanding and application of nitinol's thermomechanical properties. Through research and development initiatives, they have contributed to uncovering the intricacies of nitinol's thermal response and mechanical behavior at different temperatures. Their work has paved the way for innovative uses of nitinol in various industries.
By studying nitinol's thermomechanical properties, we gain a deeper appreciation for this remarkable alloy's versatility and potential across diverse fields.
Nitinol Fatigue and Fracture Resistance
Nitinol's fatigue properties are a key aspect of its mechanical behavior. The material is known for its ability to withstand repeated stress without deformation. This unique property makes it ideal for applications in industries such as aerospace and healthcare, where durability is crucial. Nitinol's fatigue resistance allows for long-term use without compromising performance.
Fracture resistance is another important factor in determining the reliability of nitinol's mechanical properties. The material's ability to resist fracture under high-stress conditions ensures the longevity of its components and devices, making it a sought-after choice for critical applications where failure is not an option.
The impact of nitinol fatigue and fracture resistance on durability and longevity cannot be overstated. Whether used in medical implants or structural components in aerospace engineering, nitinol's ability to maintain its integrity over time is essential for ensuring safety and reliability.
Nitinol Corrosion Resistance
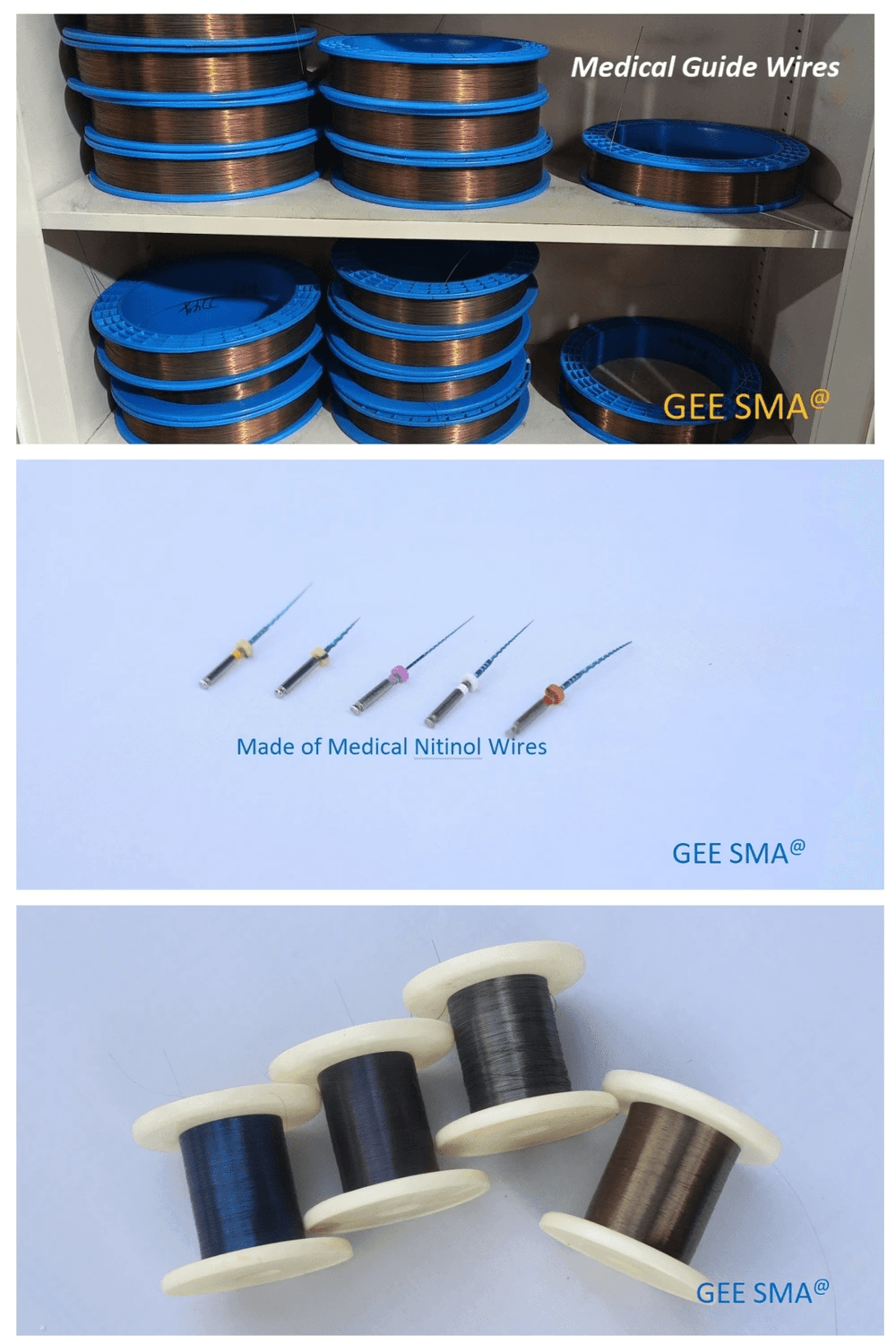
Nitinol is renowned for its impressive corrosion resistance, making it an ideal material for various industries. Its unique composition of nickel and titanium contributes to its exceptional resistance to corrosion in harsh environments. This property makes nitinol an excellent choice for medical devices, aerospace engineering, and marine equipment applications.
Nitinol Corrosion Properties
Nitinol's corrosion properties are attributed to its passive oxide film, which forms on the surface when exposed to oxygen. This film protects the material from chemical reactions that would otherwise lead to corrosion. As a result, nitinol is highly resistant to rust and degradation in aggressive environments, ensuring longevity and reliability in various applications.
Environmental Impact
Nitinol's corrosion resistance has a positive environmental impact by reducing the need for frequent replacements and repairs due to degradation. This results in less waste and lower resource consumption over time, contributing to sustainable practices in industries where nitinol is utilized.
Implications for Various Industries
Nitinol's exceptional corrosion resistance makes it a prime choice for various industries. Its applications are particularly significant in:
- Healthcare: Ensuring the longevity and reliability of medical implants and devices within the human body.
- Aerospace: Providing robust and durable components for aircraft and spacecraft.
- Marine Engineering: Offering corrosion protection in the harsh saltwater environment.
Nitinol's unique properties make it an invaluable asset in these sectors, contributing to improved performance and extended product life.
Nitinol Workability and Fabrication
Nitinol, a unique memory metal, comes in various forms and shapes, such as wires, tubes, and sheets, allowing for versatile applications in different industries. Fabrication techniques for nitinol include laser cutting, EDM machining, and shape setting to achieve desired shapes and sizes. Smart Materials Inc. specializes in tailoring nitinol materials to specific applications through precise fabrication processes.
Nitinol Forms and Shapes
Nitinol wire is commonly used in medical devices due to its flexibility and shape memory properties. Nitinol tubes are utilized in aerospace engineering for their lightweight yet strong characteristics. Nitinol sheets are often employed in manufacturing components for their superelasticity and fatigue resistance.
Fabrication Techniques
The process of making nitinol involves melting nickel and titanium together at high temperatures before cooling rapidly to form the desired alloy composition. To achieve the desired mechanical properties, nitinol is fabricated through intricate processes such as heat treatment, cold working, and shape setting.
Tailoring Materials for Specific Applications
Smart Materials Inc. specializes in tailoring nitinol materials for specific applications by customizing the alloy composition, heat treatment processes, and fabrication techniques to meet the unique requirements of diverse industries such as healthcare, aerospace, and engineering.
Nitinol Mechanical Properties in Aerospace
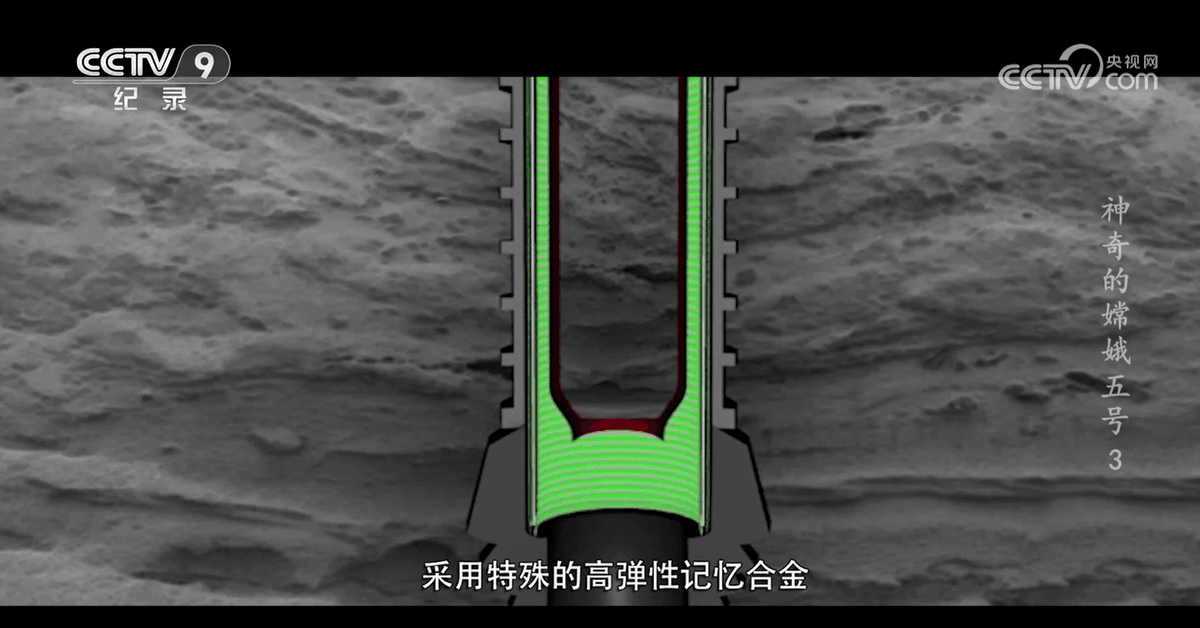
Nitinol memory metal has revolutionized aerospace engineering with its unique combination of nitinol mechanical properties. The superelasticity and shape memory effect of nitinol wire has made it an invaluable material for various aerospace applications, from actuators and sensors to components for aircraft engines. Its ability to withstand extreme temperatures and high-stress environments has significantly impacted the design and functionality of aerospace technology.
Nitinol in Aerospace Engineering
Nitinol wire is widely used in aerospace engineering for its exceptional mechanical properties, such as superelasticity and shape memory effect. These properties make it an ideal material for actuators, essential components in aircraft wings, landing gear, and other moving parts. Nitinol's ability to return to its original shape after deformation allows for precise control and adjustment in critical aerospace systems.
Impact on Design and Functionality
The incorporation of nitinol memory metal in aerospace design has led to enhanced functionality and performance. Its unique properties enable the development of lightweight, compact, and durable components that contribute to improved fuel efficiency, reduced maintenance costs, and increased safety standards in aircraft operations.
Meeting Industry Standards and Requirements
As the aerospace industry continues to push the boundaries of innovation, meeting stringent industry standards and requirements is essential. Nitinol's exceptional mechanical properties have allowed it to meet these rigorous demands by providing reliability, durability, and high performance in extreme conditions.
The Future of Nitinol Mechanical Properties
As the demand for advanced materials continues to grow, so does the need for advancements in nitinol technology. With ongoing research and development, experts are exploring new ways to enhance the mechanical properties of nitinol memory metal, making it even more versatile and adaptable for various applications.
Advancements in Nitinol Technology
Researchers and engineers constantly push the boundaries of nitinol composition and processing techniques to optimize its mechanical properties further. By fine-tuning the alloy components and fabrication methods, they aim to improve its shape memory effect, superelasticity, and fatigue resistance, opening up new possibilities for innovative healthcare, aerospace, and beyond applications.
Potential Applications and Innovations
The future of nitinol mechanical properties holds promise for groundbreaking applications across industries. The potential uses for improved nitinol materials are virtually limitless, from advanced medical devices with enhanced biocompatibility to aerospace components with superior durability and performance. As researchers continue to unlock its full potential, we expect to see innovative products that leverage these enhanced properties.
Tailored Materials for Unique Customer Needs
With a deeper understanding of nitinol composition and processing techniques, manufacturers can now tailor materials to meet specific customer requirements. Whether creating custom shapes or adjusting thermal response characteristics, the ability to customize nitinol alloys opens up opportunities for unique solutions in various fields. This tailored approach ensures end-users receive high-performance materials that align perfectly with their needs.
By staying at the forefront of advancements in nitinol technology, companies like SAES Smart Materials are driving innovation and shaping the future of the smart materials industry. As these developments continue to unfold, we can anticipate an exciting era of transformative applications that harness the full potential of nitinol's mechanical properties.
The Versatility of Nitinol Mechanical Properties
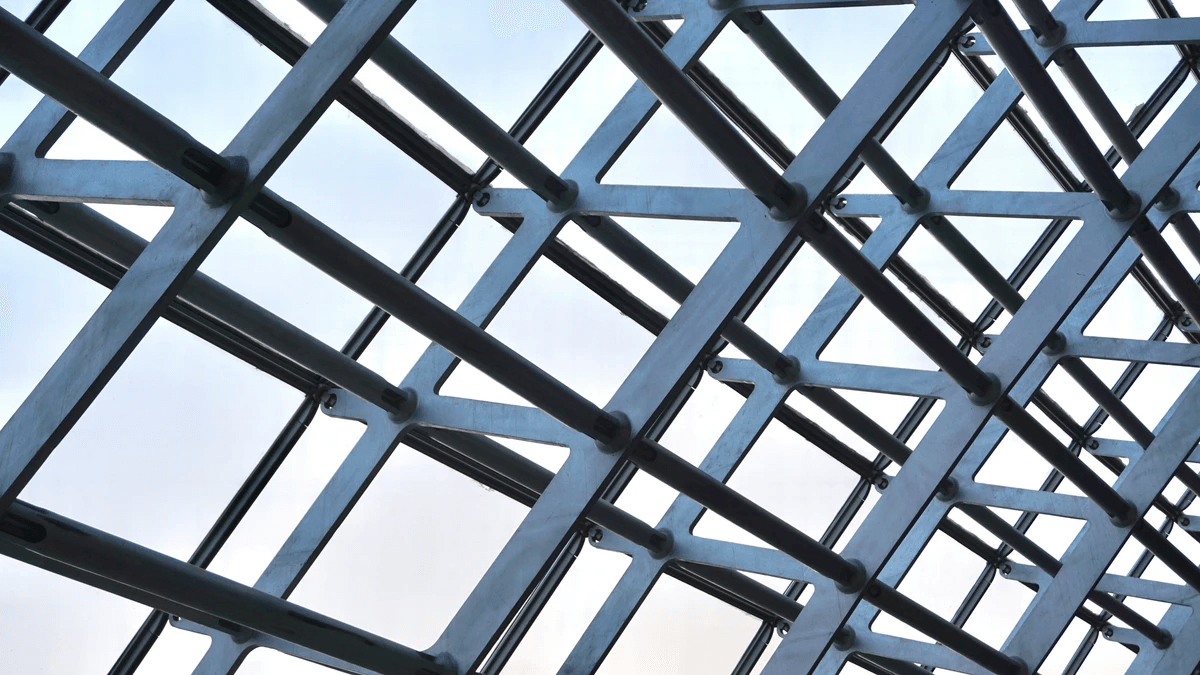
Nitinol's mechanical properties offer various applications, from aerospace engineering to medical devices. The partnership with SAES Smart Materials has led to groundbreaking innovations in nitinol memory metal technology, creating new opportunities for tailored materials that meet unique customer needs. By harnessing the potential of nitinol for diverse applications, the future looks promising for this remarkable smart material.
The versatility of nitinol's mechanical properties is truly remarkable. Its unique shape memory effect and superelasticity make it an ideal material for a wide range of industries. From biomedical implants to actuators in robotics, nitinol's ability to return to its original shape after deformation opens up endless possibilities for innovation and design.
Partnerships with SAES Smart Materials
The collaboration between nitinol experts and SAES Smart Materials has resulted in cutting-edge advancements in smart materials technology. Combining expertise in nitinol composition and fabrication with SAES's innovative approach, new applications and materials tailored to specific industry needs are constantly being developed.
Harnessing the Potential of Nitinol for Diverse Applications
As the demand for smart materials continues to grow, nitinol's potential is being harnessed for diverse applications across various industries. From automotive engineering to consumer electronics, its unique mechanical properties are paving the way for groundbreaking innovations that were once thought impossible.