Introduction
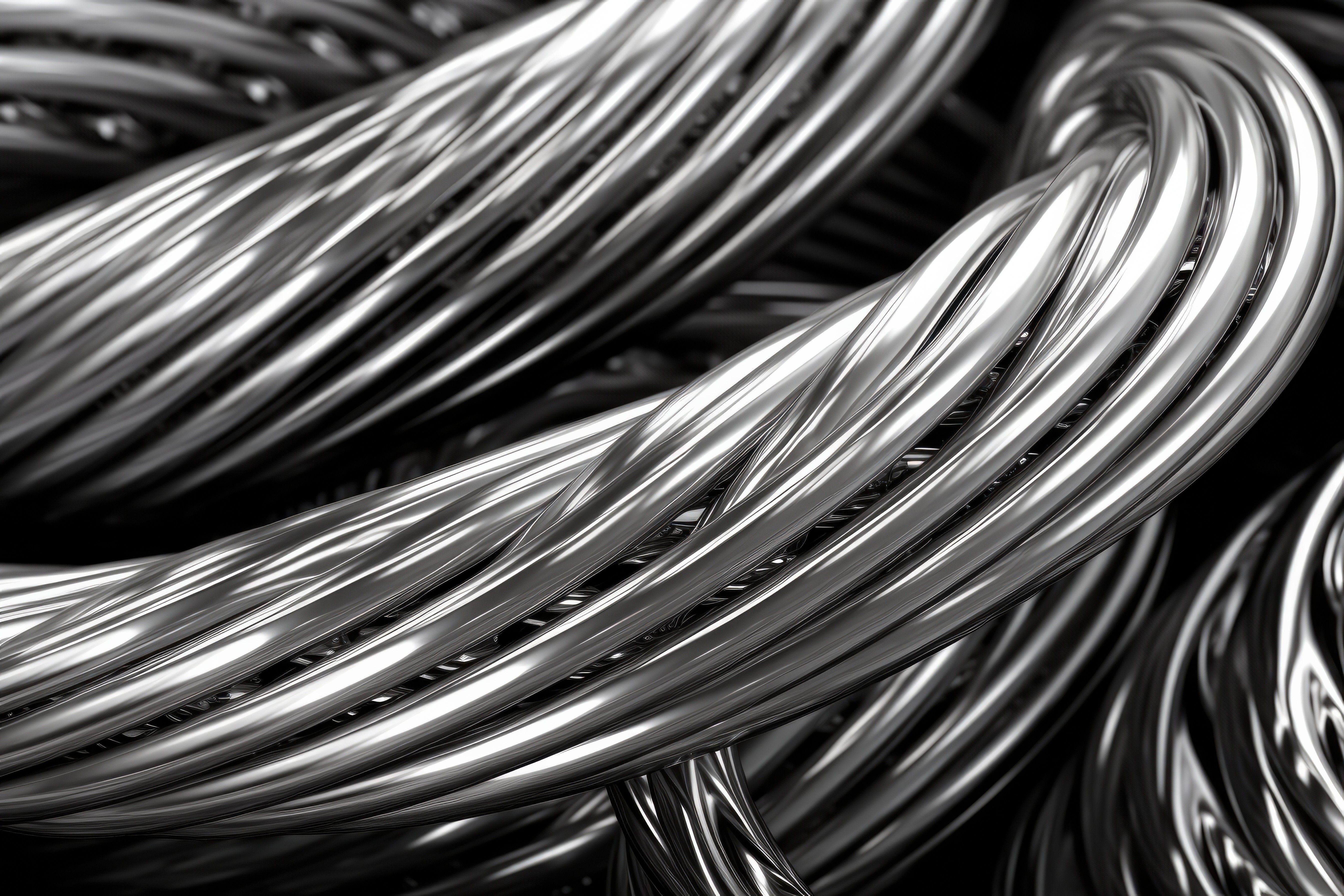
Nitinol, a remarkable nickel-titanium alloy, has gained widespread attention in mechanical engineering due to its extraordinary properties. From shape memory effect to super elasticity, nitinol offers a wide range of unique characteristics that make it an invaluable material for various applications.
Understanding the Importance of Nitinol Mechanical Properties
The mechanical properties of nitinol, such as super elasticity and shape memory effect, play a crucial role in its versatility and functionality. These properties enable nitinol to return to its original shape after deformation, making it ideal for applications where flexibility and resilience are essential.
Exploring the Versatility of Nitinol Alloys
Nitinol alloys exhibit exceptional properties that make them suitable for diverse engineering applications. Whether in wires or components, nitinol's versatility allows it to be utilized in aerospace and biomedical engineering fields.
Unleashing the Potential of Nitinol in Mechanical Engineering
Nitinol alloys offer a wealth of possibilities for mechanical engineers. Their unique properties have the potential to revolutionize the field. Specifically, nitinol's characteristics can be leveraged to:
- Develop advanced medical implants with enhanced biocompatibility and functionality.
- Create innovative actuators and sensors for robotics and automation.
- Design high-performance structural components for aerospace and automotive industries.
By fully understanding and exploiting nitinol's capabilities, researchers can unlock new frontiers in mechanical engineering and create groundbreaking solutions to complex challenges.
Super Elasticity
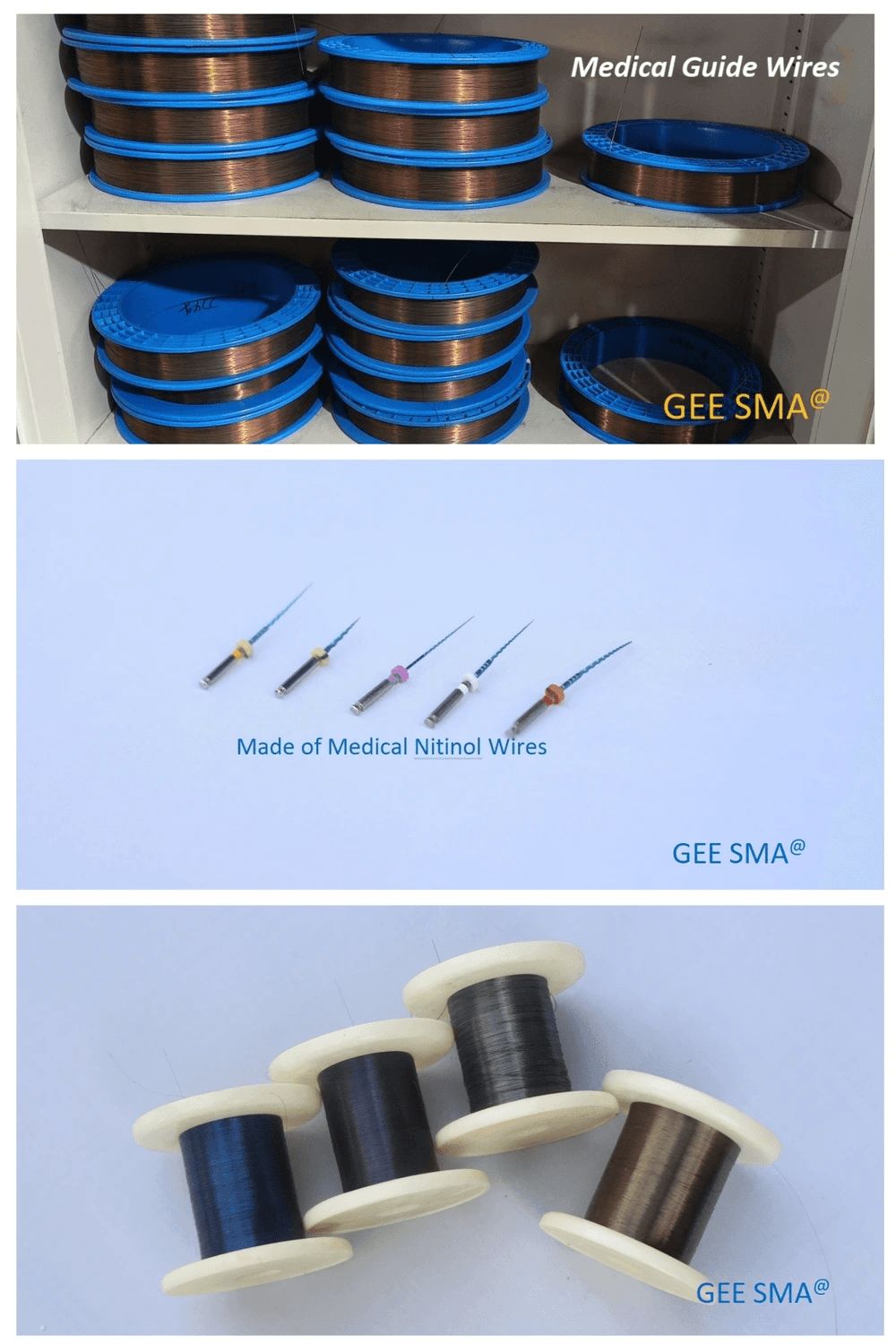
Nitinol's Unique Super Elastic Behavior
Nitinol's superelasticity is a remarkable mechanical property that allows the alloy to recover its original shape after significant deformation. This unique characteristic makes nitinol an ideal material for various applications requiring flexibility and resilience, such as medical devices, aerospace components, and consumer electronics.
Applications of Super Elastic Nitinol Wire
Super elastic nitinol wire is extensively used in minimally invasive medical procedures, where its ability to undergo large deformations without permanent damage is crucial. From stents and guidewires to orthodontic archwires and surgical instruments, the versatility of superelastic nitinol wire has revolutionized the field of medical device technology.
Key Factors Influencing Super Elasticity in Nitinol Alloys
Factors such as composition, heat treatment, and processing techniques influence the superelastic behavior of nitinol alloys. The precise control of these parameters enables engineers to tailor the superelastic properties of nitinol to meet specific application requirements, ensuring optimal performance and reliability.
Shape Memory Effect
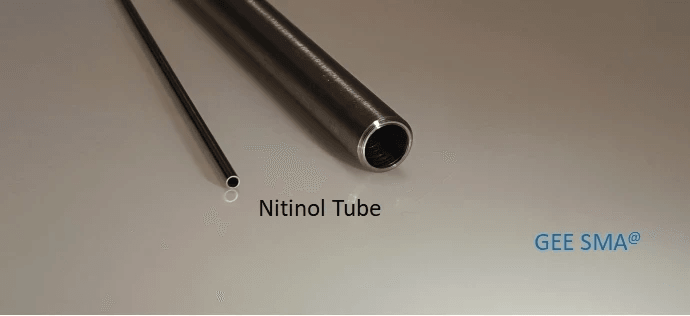
Nitinol alloys are renowned for their remarkable shape memory properties, which allow them to return to a predetermined shape after deformation. This unique characteristic has revolutionized various industries, from biomedical devices to aerospace engineering. Nitinol's ability to remember its original shape makes it an invaluable material for applications requiring precise and reliable shape recovery.
Harnessing the Shape Memory Properties of Nitinol
Nitinol's shape memory effect is harnessed through a process called thermal cycling, where the material undergoes a reversible phase transformation between the austenite and martensite phases. This enables nitinol to exhibit extraordinary flexibility and resilience, making it ideal for minimally invasive medical devices such as stents and guidewires.
Nitinol Nickel Titanium: A Shape Memory Alloy
Nitinol is often referred to as nitinol nickel titanium due to its composition of nickel and titanium, which gives rise to its exceptional shape memory behavior. This unique combination of elements allows nitinol alloys to undergo reversible phase transformations under specific temperature conditions, making them highly sought-after in manufacturing smart materials and actuators.
Innovations in Nitinol Shape Memory Technology
Recent advancements in nitinol shape memory technology have led to the development of sophisticated medical implants that can adapt to the body's natural movements. From self-expanding stents that conform to blood vessels' contours to orthodontic wires that apply gentle, continuous force to teeth, these innovations showcase the endless possibilities of leveraging nitinol's shape memory properties.
Tensile Strength
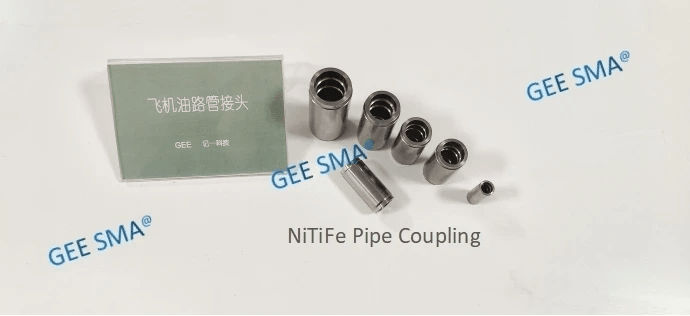
When evaluating the tensile strength of Nitinol wire, it's crucial to consider its unique mechanical properties. As a shape memory alloy, Nitinol nickel-titanium exhibits remarkable tensile strength, making it ideal for various applications in engineering and biomedical devices. The tensile properties of Nitinol alloys are influenced by factors such as composition, processing methods, and heat treatment, all of which play a significant role in determining its performance in practical use.
Evaluating the Tensile Strength of Nitinol Wire
Nitinol wire is known for its exceptional tensile strength, which allows it to withstand high levels of stress and strain without permanent deformation. This makes it an excellent choice for applications requiring resilience and durability, such as medical implants and orthodontic devices. Evaluating Nitinol wire's tensile strength involves rigorous testing under different conditions to ensure its reliability and performance in real-world scenarios.
Factors Affecting the Tensile Properties of Nitinol Alloys
Various factors, including the ratio of nickel to titanium, heat treatment processes, and impurities, influence Nitinol alloys' tensile properties. These factors can significantly impact the material's ability to resist deformation under tension and determine its suitability for specific engineering or biomedical applications. Understanding these factors is crucial for optimizing the mechanical properties of Nitinol alloys based on their intended use.
Implications of Tensile Strength in Nitinol Applications
The impressive tensile strength of Nitinol has far-reaching implications for its applications across different industries. From aerospace components to minimally invasive medical devices, the ability of Nitinol alloys to maintain their structural integrity under tension opens up new possibilities for innovative designs and advanced technologies. As engineers continue to push the boundaries of what is possible with materials science, the exceptional tensile strength of Nitinol will undoubtedly play a pivotal role in shaping the future.
Fatigue Resistance
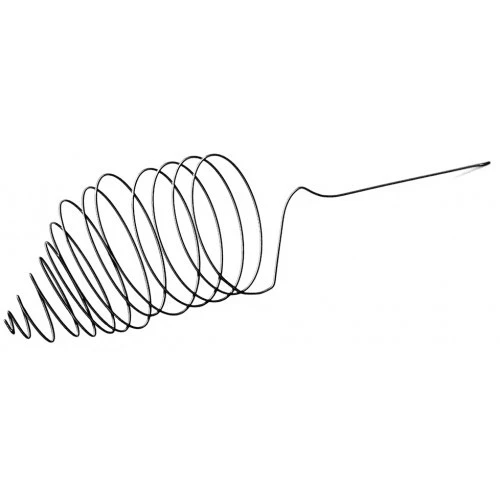
Nitinol alloys exhibit remarkable fatigue resistance, making them ideal for long-term applications in various industries. The unique ability of nitinol nickel titanium to withstand cyclic loading without degradation has revolutionized the design of medical devices, aerospace components, and consumer products.
Nitinol Alloys' Remarkable Fatigue Resistance
Nitinol properties include exceptional fatigue resistance, allowing for extended use without compromising performance. This makes nitinol alloys highly sought after in critical applications where durability is paramount.
Enhancing Fatigue Life in Nitinol Components
Engineers are constantly exploring ways to enhance the fatigue life of nitinol components through innovative design and advanced manufacturing techniques. By optimizing material properties and geometrical features, they can significantly extend the operational lifespan of nitinol-based products.
Advancements in Fatigue Testing of Nitinol Materials
Advancements in fatigue testing methods have enabled researchers to gain deeper insights into the behavior of nitinol under cyclic loading conditions. This knowledge has led to developing new alloy compositions and heat treatment processes that further improve fatigue resistance.
Corrosion Resistance
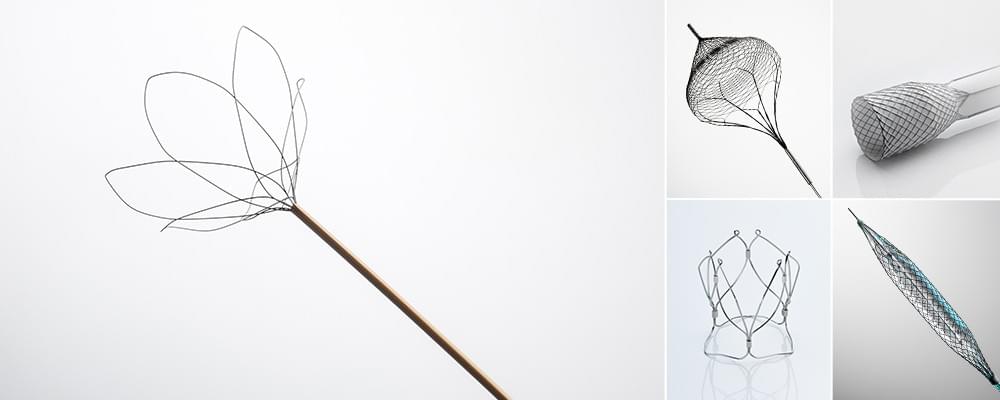
Nitinol's Impressive Corrosion Resistance
Nitinol alloys are renowned for their exceptional corrosion resistance, making them ideal for various applications in aggressive environments. Whether used in medical implants or aerospace components, nitinol's ability to withstand corrosion ensures longevity and reliability in critical systems.
Nitinol Alloys in Biomedical Devices
In biomedical engineering, nitinol alloys have revolutionized the design and performance of medical devices. From stents to orthodontic wires, nitinol's corrosion resistance ensures biocompatibility and long-term functionality within the human body, making it a material of choice for life-saving applications.
Strategies for Optimizing Corrosion Performance in Nitinol
Engineers and materials scientists continue to develop innovative strategies for optimizing the corrosion performance of nitinol alloys. Through advanced surface treatments and alloy modifications, nitinol's inherent corrosion resistance can be further enhanced, opening up new possibilities for its use in demanding environments.
Thermal Conductivity
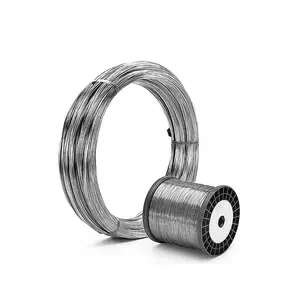
Nitinol alloys are renowned for their exceptional thermal conductivity, making them ideal for use in various mechanical systems where heat transfer is crucial. Nitinol's high thermal conductivity allows for efficient energy transfer and temperature regulation, enhancing the overall performance of mechanical components.
Thermal Conductivity of Nitinol in Mechanical Systems
In mechanical systems, nitinol's impressive thermal conductivity effectively dissipates heat, preventing overheating and maintaining optimal operating conditions. This property is particularly valuable in applications such as heat exchangers, where efficient thermal management is essential for maximizing energy efficiency and system reliability.
Nitinol in Thermal Actuators and Sensors
Nitinol's superior thermal conductivity makes it well-suited for use in thermal actuators and sensors, where precise temperature control and responsiveness are critical. Nitinol's ability to rapidly conduct heat enables these devices to accurately sense and respond to changes in temperature, making them invaluable in a wide range of mechanical and electronic systems.
Manipulating Thermal Conductivity in Nitinol Design
Engineers have developed innovative techniques to manipulate the thermal conductivity of nitinol alloys through careful design and material processing. By tailoring the microstructure and composition of nitinol, they can optimize its thermal properties to meet specific application requirements, opening up new possibilities for advanced thermal management solutions.
Young's Modulus
Nitinol's unique mechanical properties, including its Young's Modulus, are crucial in widespread applications. Understanding Young's Modulus in Nitinol is essential for engineers and designers to utilize this shape memory alloy effectively in various industries. By tailoring Young's Modulus for specific applications, such as biomedical devices or aerospace components, engineers can optimize the performance of Nitinol materials. Balancing Young's Modulus and flexibility in Nitinol components is a delicate yet vital task that requires careful consideration of design and material properties.
Understanding Young's Modulus in Nitinol
Young's Modulus, also known as the modulus of elasticity, is a fundamental property of materials that quantifies their stiffness. In essence, it measures a material's resistance to deformation under stress. For Nitinol (nickel-titanium), Young's Modulus is crucial for understanding how the alloy will behave in various applications.
Key factors influenced by Young's Modulus in Nitinol include:
- Deformation under stress: Predict how much Nitinol will stretch or compress when subjected to force.
- Design optimization: Selecting appropriate alloy compositions and processing techniques for desired mechanical properties.
- Performance prediction: Evaluating the suitability of Nitinol for specific applications based on its stiffness characteristics.
Determining Young's Modulus is essential for effectively utilizing Nitinol's unique properties in engineering and medical devices.
Tailoring Young's Modulus for Specific Applications
Innovations in materials science have enabled researchers to tailor the Young's Modulus of Nitinol alloys to meet specific application requirements. By adjusting factors such as alloy composition, heat treatment, and processing methods, engineers can customize the mechanical properties of Nitinol to suit diverse needs across industries. This flexibility makes Nitinol an attractive choice for a wide range of applications where precise control over material behavior is essential.
Balancing Young's Modulus and Flexibility in Nitinol Components
Finding the right balance between Young's Modulus and flexibility is crucial when designing components with Nitinol alloys. While a higher modulus provides greater stiffness, it may also reduce flexibility, limiting certain applications. Engineers must carefully consider these trade-offs to ensure that Nitinol components meet both structural requirements and functional needs without compromising overall performance.
Ductility
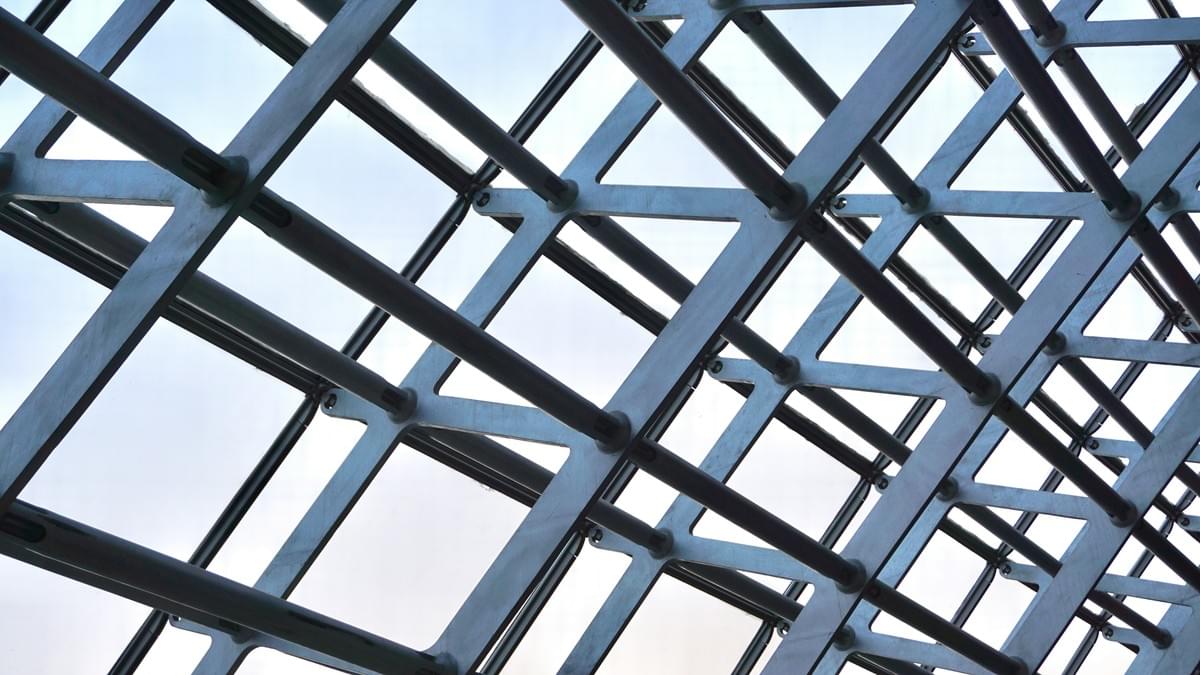
Nitinol is renowned for its exceptional ductility properties, allowing it to be easily drawn and formed into various shapes without sacrificing its structural integrity. This unique characteristic makes nitinol wire ideal for intricate components in mechanical engineering applications.
Nitinol's Exceptional Ductility Properties
Nitinol alloys' flexibility enables them to undergo significant deformation without breaking, making them highly malleable and easy to work with. This property is essential in ensuring that nitinol components can withstand the rigorous shaping processes involved in manufacturing.
Ductility in Nitinol Wire Drawing and Forming
Nitinol's impressive flexibility is crucial in wire drawing and forming processes, allowing manufacturers to create intricate designs with precision and accuracy. This capability makes nitinol wire preferred for producing complex structures such as medical stents and actuators.
Maximizing Ductility for Nitinol Component Manufacturing
Nitinol's ductility is critical for engineers and designers to consider when developing new products or devices. By carefully selecting and utilizing this property, manufacturers can optimize component performance and meet the stringent demands of various industries.
To fully leverage nitinol's flexibility, consider the following:
- Material Composition: Fine-tune the nitinol alloy to achieve the desired ductility level.
- Manufacturing Processes: Employing techniques that preserve flexibility, such as superelastic forming or shape memory heat treatment.
- Component Design: Optimize component geometry to minimize stress concentrations and enhance flexibility.
By following these guidelines, manufacturers can produce high-quality nitinol components with exceptional performance and reliability.
Work Hardening
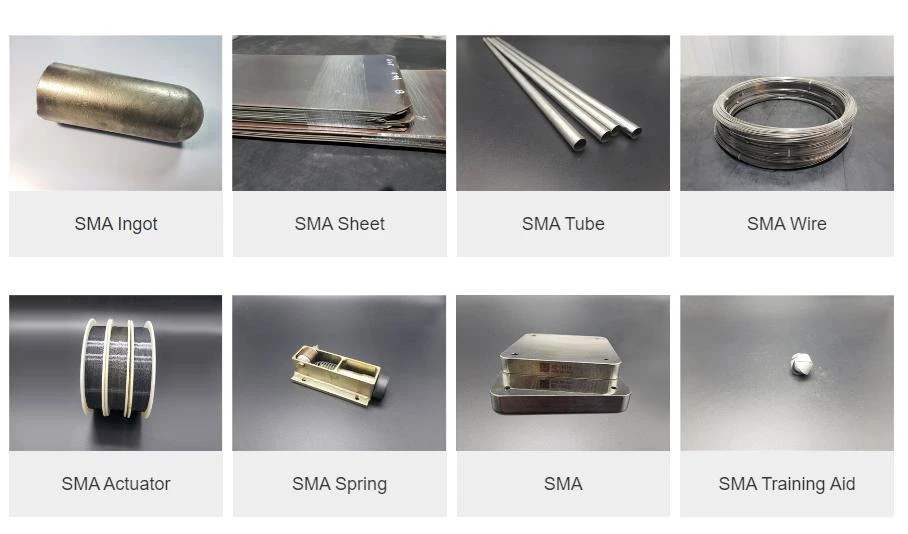
Nitinol alloys exhibit unique work hardening behavior, where the material becomes stronger and more resistant to deformation as it is deformed. This phenomenon allows for the shaping and forming of nitinol components with improved mechanical properties over time, making it a highly desirable feature in various engineering applications.
Work Hardening Behavior of Nitinol Alloys
Nitinol's work-hardening behavior results from its phase transformation from austenite to martensite during deformation, leading to an increase in strength and hardness. This characteristic makes nitinol ideal for applications requiring repeated bending or shaping, such as medical devices and actuators.
Impact of Work Hardening on Nitinol Performance
The work hardening process in nitinol results in enhanced mechanical properties, including increased strength and flexibility, improving performance and reliability in engineering applications. This unique behavior allows nitinol components to withstand greater loads and maintain their shape under repetitive stress.
Strategies for Controlling Work Hardening in Nitinol Processing
Controlling the degree of work hardening is crucial in optimizing the mechanical properties of nitinol components. Through careful processing techniques such as heat treatment and cold working, engineers can tailor the level of work hardening to achieve specific performance requirements, ensuring consistent quality and reliability in nitinol products.
Thermal Shape Setting

Nitinol's remarkable thermal shape setting capability allows for creating intricate components with precise shape memory properties. By subjecting nitinol components to specific thermal treatments, engineers can program them to revert to their original shape when exposed to heat, making them ideal for self-expanding stents and other biomedical devices.
Thermal Shape Setting of Nitinol Components
Thermal shape setting is a process that involves heating nitinol components above their transition temperature and then cooling them in a specific configuration, effectively programming their shape memory properties. This allows for creating complex shapes that can be triggered to return to their original form when exposed to heat, making nitinol an invaluable material in various engineering applications. One such application is in producing self-expanding stents used in medical procedures. These stents are designed to expand and hold open narrowed or weakened arteries. Nitinol's shape memory properties allow it to be easily inserted into the body before expanding to its desired shape. Once deployed, these stents can be compressed for insertion into blood vessels or other tubular structures and then expand back to their original shape shape-setting.
Nitinol's thermal shape setting properties have revolutionized the design of self-expanding stents used in medical procedures. These stents can be compressed for insertion into blood vessels or other tubular structures and then expand back to their original shape once deployed, providing crucial support and maintaining vessel patency. This innovative technology has greatly improved patient outcomes by reducing the need for invasive surgeries and allowing for less traumatic procedures. Additionally, the flexibility and durability of Nitinol make it an ideal material for these stents, ensuring long-term effectiveness and patient comfort.
Optimizing Thermal Shape Setting Techniques for Nitinol Devices
Engineers are constantly refining the thermal shape setting techniques used for nitinol devices, seeking to enhance precision and repeatability while minimizing any potential degradation of mechanical properties during the process. This ongoing optimization ensures that nitinol components maintain their exceptional performance characteristics even after undergoing thermal shaping treatments. One key area of focus is the development of advanced heating and cooling methods that allow for more precise control over the transformation temperatures of nitinol, resulting in improved shape memory and superelasticity. Additionally, researchers are exploring innovative surface treatments to minimize the risk of oxidation and improve the fatigue resistance of nitinol components, further enhancing their long-term reliability in applications.
Embrace Innovation in Nitinol Alloys
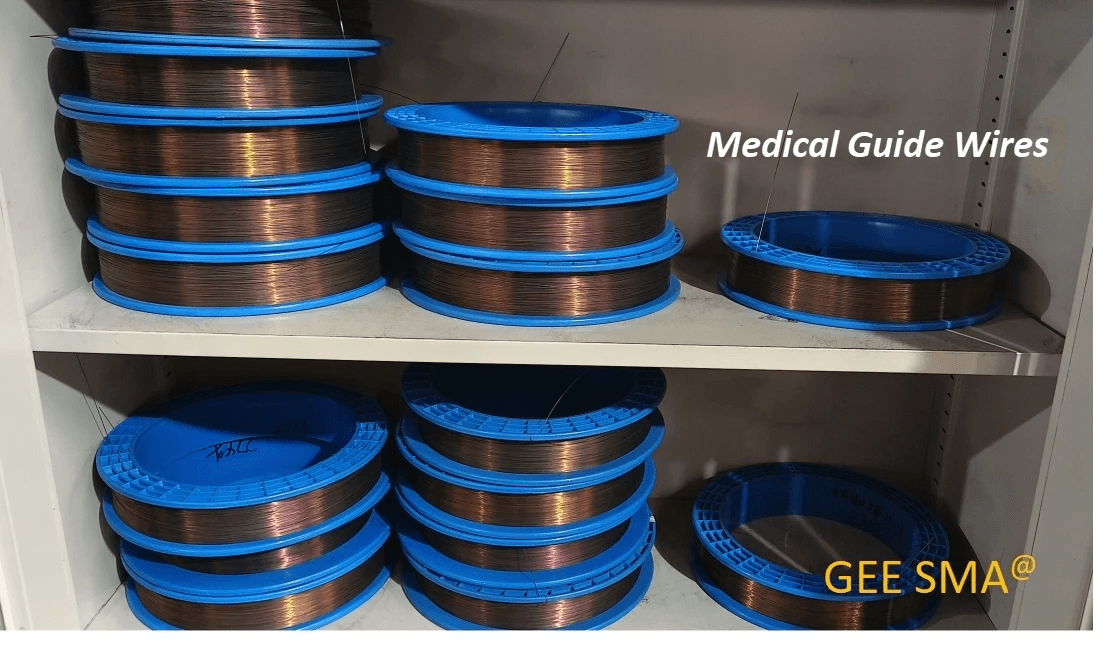
In conclusion, the potential of nitinol's mechanical properties is truly remarkable, with its unique superelastic behavior and shape memory effect setting it apart from traditional materials. Embracing innovation in nitinol alloys will continue to drive advancements in various fields, from medical devices to aerospace engineering. The future of nitinol engineering holds endless possibilities for creating groundbreaking solutions that push the boundaries of what is possible.
Unlocking the Potential of Nitinol Mechanical Properties
Nitinol nickel-titanium is a remarkable shape memory alloy with unparalleled properties, making it an ideal material for various applications. From super elastic nitinol wire to its exceptional corrosion resistance, nitinol alloys offer a level of versatility and reliability that is unmatched in the industry. Understanding and harnessing these unique properties can unlock endless opportunities for innovation and advancement in various fields.
As industries continue to explore the potential of nitinol alloys, embracing innovation becomes crucial for pushing the boundaries of what is achievable with this remarkable material. Whether it's developing new applications for super elastic nitinol wire or optimizing thermal shape-setting techniques for medical devices, there is no limit to the innovative solutions that can be created using nitinol alloys. Embracing new ideas and approaches will lead to groundbreaking developments that revolutionize mechanical engineering.
Realizing the Future of Nitinol Engineering
The future of nitinol engineering holds immense promise as researchers and engineers continue to push the boundaries of what can be achieved with this remarkable material. With ongoing advancements in understanding and manipulating nitinol properties, we are on the brink of realizing groundbreaking innovations across various industries. As we look ahead, it's clear that nitinol engineering will play a pivotal role in shaping the future of materials science and mechanical design.