Introduction
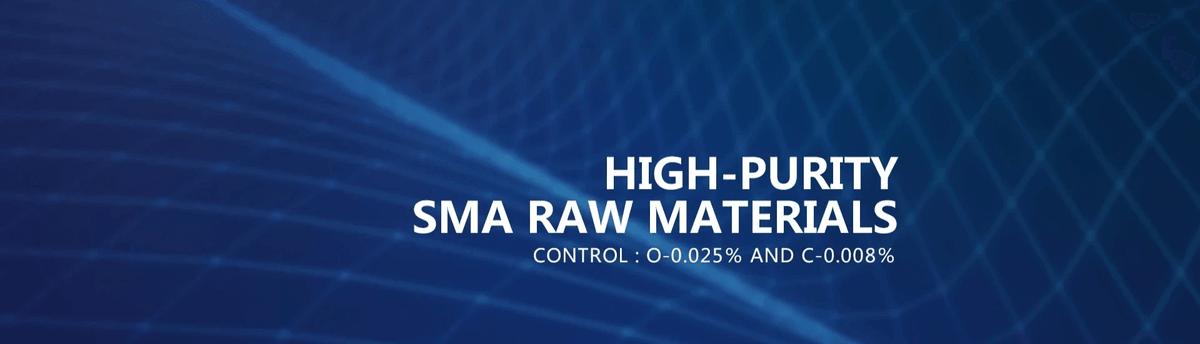
In the ever-evolving world of medical device manufacturing, nitinol laser cutting has become a crucial process for creating intricate components. As the demand for smaller, more precise devices grows, exploring the latest nitinol laser-cutting techniques becomes paramount. With advancements in technology and materials, the future of nitinol cutting techniques holds great promise for innovation and efficiency.
Exploring the Latest Nitinol Laser Cutting Techniques
The latest nitinol laser cutting techniques are revolutionizing medical device manufacturing. By harnessing the power of advanced laser technology, manufacturers can achieve unparalleled precision and intricacy in their nitinol components. These cutting-edge techniques allow for intricate designs and complex geometries to be achieved with remarkable accuracy.
Advancements in Nitinol Laser Cutting
Nitinol laser cutting has undergone remarkable advancements, revolutionizing the manufacturing of nitinol components. Here are some key improvements:
- Increased Precision: State-of-the-art laser cutting technology ensures exceptional accuracy and repeatability in nitinol component production.
- Enhanced Efficiency: Advanced laser cutting systems streamline manufacturing, leading to faster production times and reduced costs.
- Improved Quality: Nitinol laser cutting minimizes defects and imperfections, resulting in higher-quality components with superior performance.
- Expanded Applications: The advancements in nitinol laser cutting have created more complex and innovative medical device designs.
These advancements in nitinol laser cutting have significantly expanded the possibilities for medical device design and functionality. With the ability to efficiently produce precise, high-quality nitinol components, manufacturers can now develop innovative solutions that address critical healthcare needs.
The Future of Nitinol Cutting Techniques
The future of nitinol-cutting techniques is poised for continued innovation and advancement. As technology continues to evolve, so will the capabilities of nitinol laser-cutting processes. The potential for even greater precision, efficiency, and versatility in manufacturing nitinol components holds exciting prospects for the future of medical device development.
Nitinol Braid Cutting
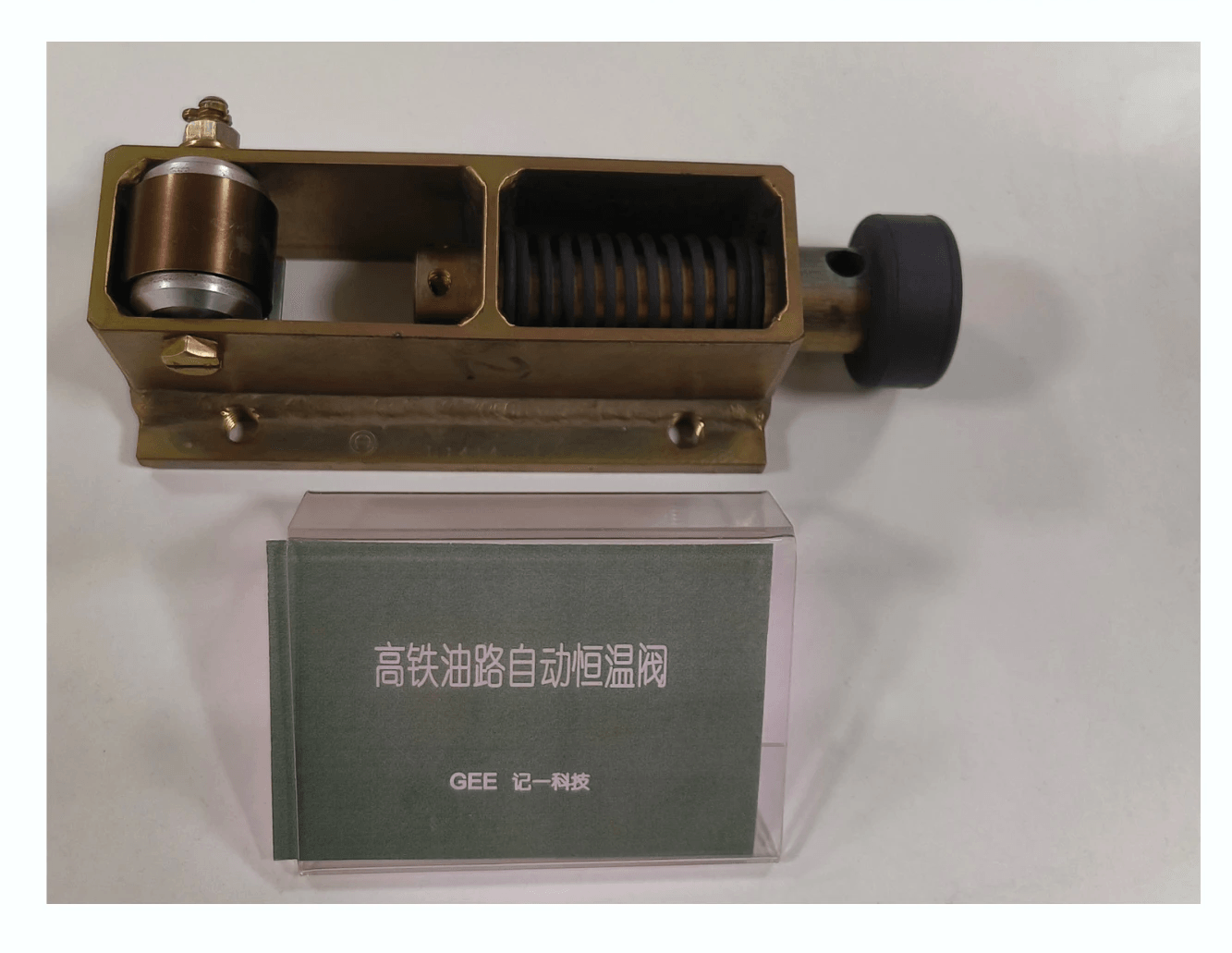
Nitinol braid cutting has seen significant advancements in recent years, with precision techniques crucial in achieving superior results. By utilizing specialized laser cutting methods, manufacturers can ensure clean and accurate cuts on intricate nitinol braid structures, enhancing the overall quality of the final product.
Precision Techniques for Nitinol Braid Cutting
In the realm of nitinol braid cutting, precision is key to achieving optimal results. Advanced laser cutting technologies allow for meticulous control over the cutting process, ensuring that each strand of nitinol braid is precisely cut to the desired specifications. This level of precision is essential for maintaining the structural integrity and functionality of nitinol-based medical devices and other intricate applications.
In addition to precision, efficiency is a crucial factor in nitinol braid cutting. Advanced laser cutting technologies provide meticulous control over the cutting process and offer faster and more streamlined production. This enhanced efficiency increases throughput and reduces lead times, benefiting manufacturers and end-users. By maximizing the speed and accuracy of nitinol braid cutting, these advanced techniques contribute to improved productivity and cost-effectiveness in producing medical devices and other intricate applications.
Enhancing Efficiency in Nitinol Braid Cutting
Efficiency is pivotal in modern manufacturing processes, and nitinol braid cutting is no exception. Manufacturers can streamline their production workflows with innovative automation and optimization techniques, reducing lead times and minimizing material waste. These efficiency enhancements contribute to cost savings while maintaining high-quality standards in nitinol braid-cutting operations.
In addition to automation and optimization techniques, manufacturers can also explore the use of advanced cutting tools and technologies to enhance efficiency in nitinol braid cutting further. Utilizing state-of-the-art laser or water jet cutting systems can significantly improve precision and consistency in the cutting process, resulting in higher-quality end products. These advanced technologies also offer greater flexibility in design and pattern options, allowing manufacturers to easily meet a wider range of customer requirements.
Innovative Approaches to Nitinol Braid Cutting
Nitinol braid-cutting technology has been rapidly evolving, with recent advancements focusing on improving speed, accuracy, and minimizing thermal damage. Here are some notable developments in this field:
- Advanced Robotics: Integrating robotic arms with laser-cutting technology has significantly enhanced precision and efficiency in nitinol braid cutting. This allows for complex and intricate designs to be cut with exceptional accuracy.
- Laser Technology Innovations: New laser technologies, such as ultrafast lasers, offer improved cutting speeds and reduced thermal impact on the nitinol material.
- Motion Control Systems: Advanced motion control systems ensure precise and repeatable cutting movements, contributing to accuracy and quality.
As the field of nitinol processing advances, we expect to see even more innovative solutions for cutting nitinol braid. By leveraging these technologies, manufacturers can produce high-quality nitinol products with greater efficiency and precision.
Nitinol Flat Wire Cutting
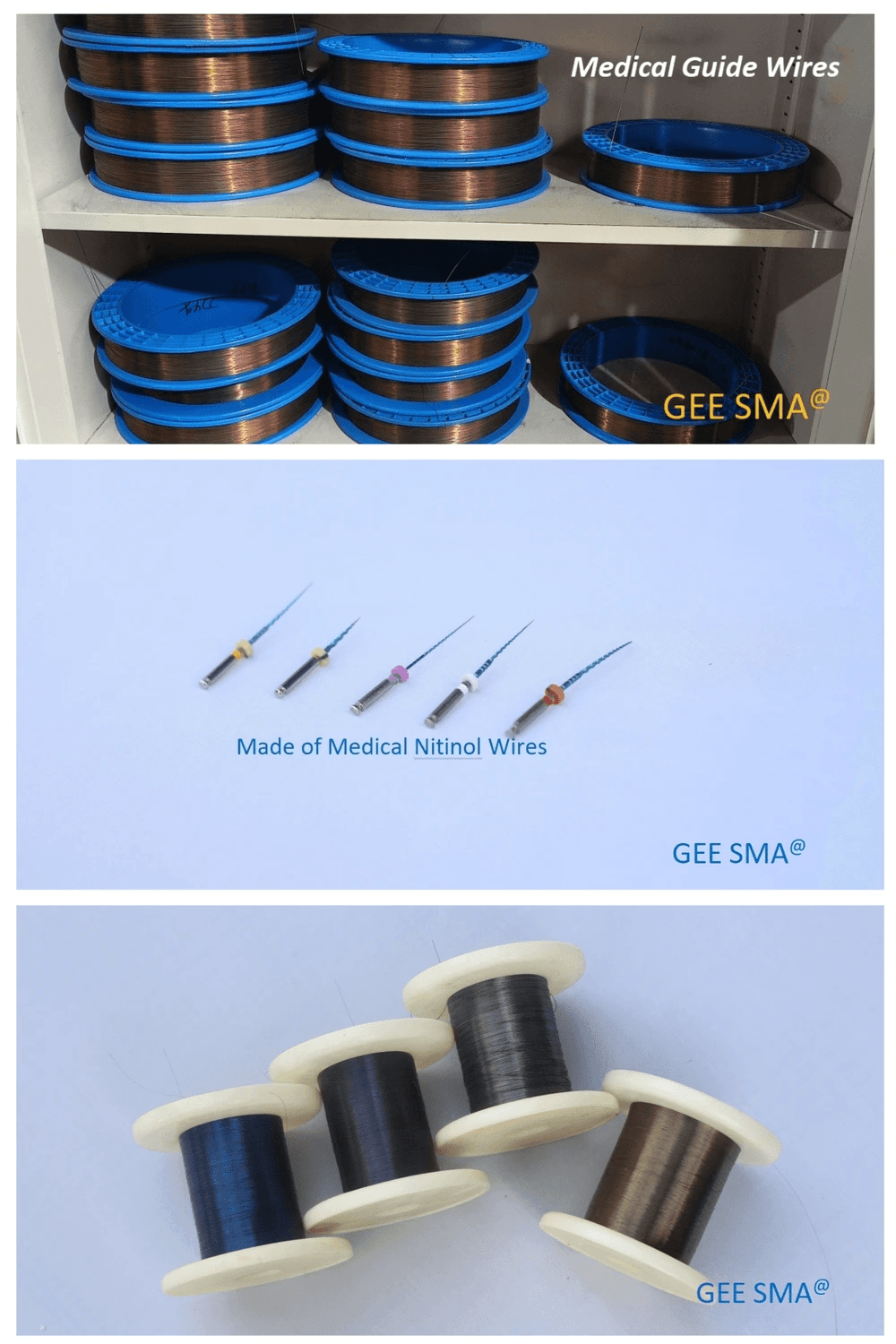
Nitinol flat wire cutting has seen remarkable advancements recently, with cutting-edge methods revolutionizing the industry. From innovative laser cutting techniques to state-of-the-art machinery, the precision and efficiency of nitinol flat wire cutting have reached new heights. Manufacturers can now maximize quality while streamlining processes, resulting in superior nitinol flat-wire products that meet the highest standards of excellence.
Cutting-edge Methods for Nitinol Flat Wire Cutting
The latest nitinol laser cutting methods have transformed how flat wires are cut, allowing for unparalleled precision and accuracy. Advanced laser technology enables intricate designs and complex shapes to be cut with remarkable detail, giving manufacturers unprecedented flexibility in their production processes. This cutting-edge approach has elevated the quality of nitinol flat wire components, setting a new standard for excellence in the industry.
The precision and accuracy achieved through nitinol laser cutting methods have revolutionized the manufacturing process for flat wire components. This advanced technology allows for creating intricate designs and complex shapes with unprecedented detail, allowing manufacturers to push the boundaries of what is possible in their production processes. As a result, the quality of nitinol flat wire components has been elevated to new heights, setting a standard for previously unattainable excellence.
Maximizing Quality in Nitinol Flat Wire Cutting
The production of nitinol flat wire requires precise cutting techniques to ensure optimal performance and quality. Manufacturers have implemented various strategies to streamline this process and deliver superior products.
- Rigorous Quality Control: Manufacturers prioritize quality throughout the entire production process. This includes meticulous material selection, careful monitoring of cutting operations, and thorough final inspection.
- Advanced Cutting Technologies: Investing in state-of-the-art cutting equipment enables manufacturers to achieve greater precision, efficiency, and consistency in the nitinol flat wire cutting process.
- Continuous Improvement: By regularly evaluating and refining their processes, manufacturers can identify areas for optimization and maintain their competitive edge.
Through a combination of rigorous quality control, advanced technologies, and a commitment to continuous improvement, manufacturers are able to produce high-quality nitinol flat wire that meets the demanding requirements of various industries.
Streamlining Nitinol Flat Wire Cutting Processes
Streamlining nitinol flat wire cutting processes has become a key priority for manufacturers seeking to enhance efficiency and productivity. Through innovative automation and advanced machinery, production timelines have been significantly reduced while maintaining uncompromising quality standards. This streamlined approach benefits manufacturers by optimizing their operations and ensures that customers receive their orders promptly without sacrificing product quality.
By leveraging cutting-edge methods, maximizing quality control measures, and streamlining production processes, the future of nitinol flat wire cutting looks brighter than ever before!
Nitinol Electropolishing
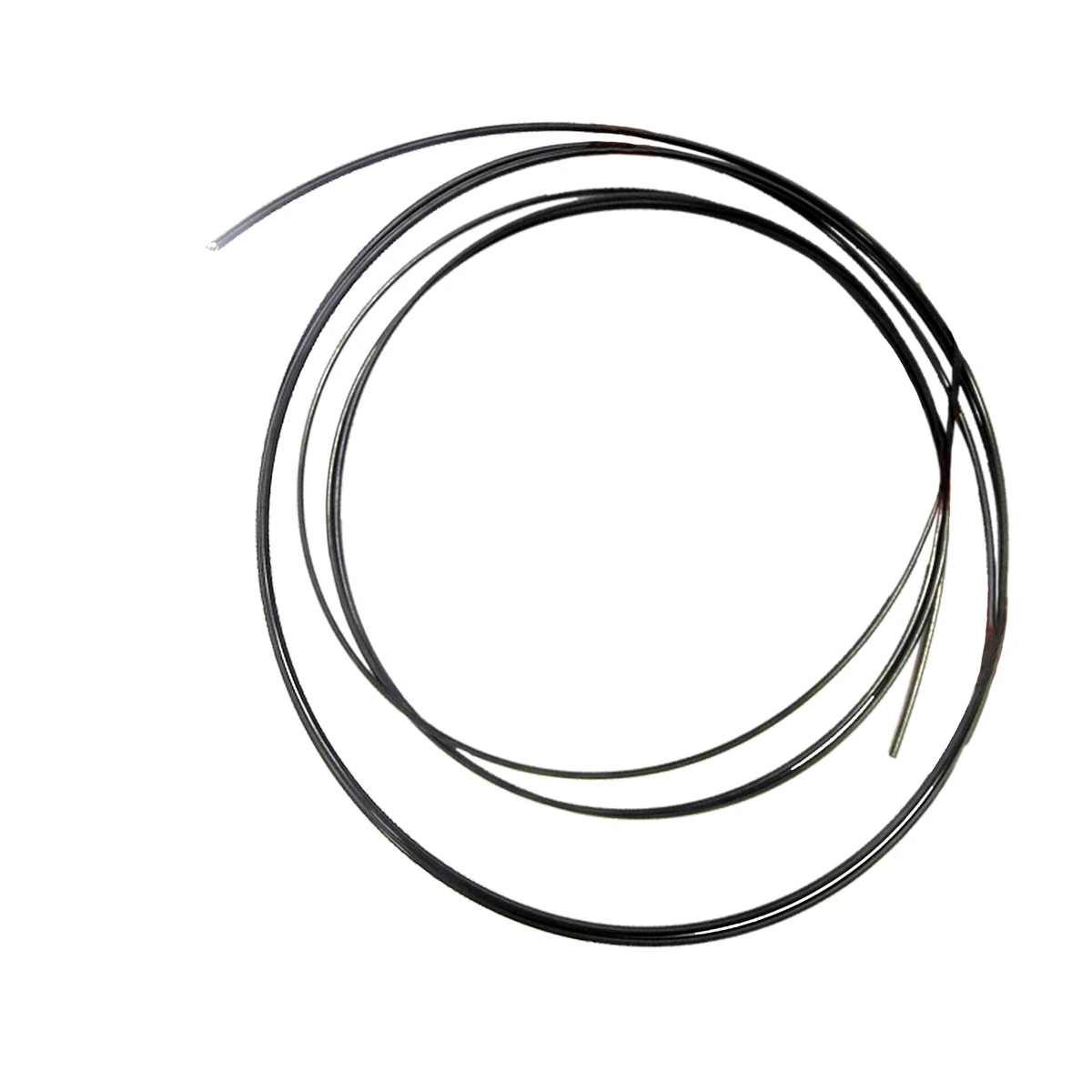
Nitinol electropolishing is a crucial step in manufacturing, ensuring a flawless finish for nitinol components. By perfecting nitinol electropolishing techniques, manufacturers can achieve a smooth and uniform surface, free from any imperfections that could compromise the final product's functionality. This process involves carefully controlling the electrochemical parameters to achieve the desired surface smoothness and brightness level.
Perfecting Nitinol Electropolishing Techniques
Perfecting nitinol electropolishing techniques requires a deep understanding of the material's properties and how it responds to different electrochemical conditions. By optimizing parameters such as current density, temperature, and electrolyte composition, manufacturers can achieve consistent results and minimize variations in surface finish. This precision is essential for meeting the stringent quality standards for medical devices and other critical applications.
Achieving Superior Finish with Nitinol Electropolishing
Nitinol electropolishing offers a superior finish to mechanical polishing methods, as it can reach intricate geometries and internal surfaces that are inaccessible through traditional means. The result is a pristine surface that enhances biocompatibility and corrosion resistance while maintaining the material's unique shape memory properties. This level of finish is particularly important for medical implants where any surface irregularities could lead to tissue irritation or other complications.
Enhancing Surface Quality through Nitinol Electropolishing
Nitinol electropolishing is a crucial process for enhancing the surface quality of nitinol components. This technique offers several key benefits:
- Improved Aesthetics: Electropolishing produces a smooth, mirror-like finish that enhances the visual appeal of nitinol products.
- Enhanced Functional Performance: Electropolishing removes surface imperfections, reducing the risk of stress concentrations and fatigue failure, leading to improved component reliability and durability.
- Reduced Risk of Corrosion: The smooth surface created by electropolishing minimizes the surface area available for corrosion, enhancing the component's resistance to environmental degradation.
- Improved Biocompatibility: In medical applications, electropolishing can help create a smoother surface that is less likely to cause irritation or rejection by the body.
Industries such as aerospace, automotive, and healthcare can produce high-quality components that meet stringent performance standards by incorporating nitinol electropolishing into their manufacturing processes.
Machining Nitinol
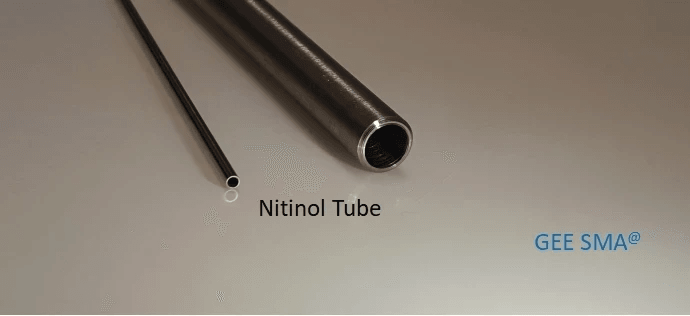
Advanced methods are crucial for achieving precise results when machining nitinol. Manufacturers can ensure the highest accuracy and consistency in shaping nitinol components by utilizing state-of-the-art CNC machines and specialized cutting tools. By incorporating advanced software for programming and simulation, machining processes can be optimized to minimize material waste and reduce production time.
Advanced Methods for Machining Nitinol
Advanced methods for machining nitinol involve using high-speed cutting tools and innovative cooling techniques to maintain dimensional stability and prevent material deformation. Additionally, the integration of multi-axis machining capabilities allows for complex geometries to be achieved with unparalleled precision, meeting the exact specifications required for nitinol components used in medical devices and other critical applications.
Furthermore, using advanced CAD/CAM software allows for the precise programming of machining operations, ensuring that nitinol components are manufactured with the highest accuracy. This level of precision is crucial in the medical field, where nitinol components are used in devices such as stents and guidewires, where even the smallest deviation from specifications can have serious consequences. By employing these advanced methods for machining nitinol, manufacturers can guarantee that their products meet the stringent quality standards required for critical applications.
Precision Machining for Nitinol Components
Precision machining for nitinol components demands meticulous attention to detail throughout manufacturing. Each step must be carefully executed, from initial material preparation to final finishing operations, to ensure that the desired tolerances and surface quality are consistently met. Focusing on achieving tight dimensional control and superior surface finishes, precision machining is essential for producing high-quality nitinol parts.
Precision machining for nitinol components demands meticulous attention to detail throughout manufacturing. Each step must be carefully executed, from initial material preparation to final finishing operations, to ensure that the desired tolerances and surface quality are consistently met. Focusing on achieving tight dimensional control and superior surface finishes, precision machining is essential for producing high-quality nitinol parts.
Optimizing Nitinol Machining Processes
Optimizing nitinol machining processes involves continuous improvement efforts to enhance efficiency, reduce costs, and increase overall productivity. By implementing lean manufacturing principles and utilizing advanced metrology equipment for quality control, manufacturers can streamline their operations while maintaining the highest standards of precision and accuracy. Through ongoing research and development, new techniques are continually being developed to optimize nitinol machining processes further.
Nitinol Tubes Cutting
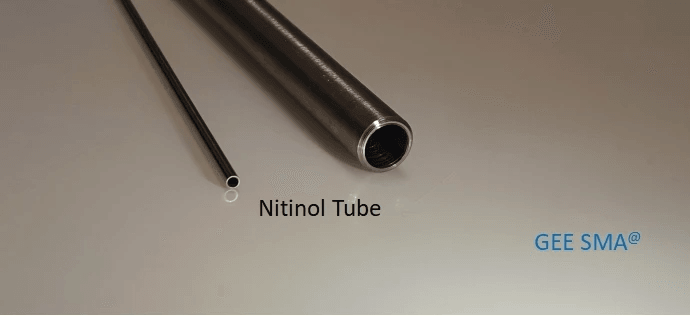
Innovative Approaches to Nitinol Tubes Cutting
Innovative approaches to nitinol tube cutting have revolutionized the medical device industry, allowing for the creation of intricate and precise components. Utilizing advanced laser cutting technology, manufacturers can now achieve unparalleled precision and consistency in cutting nitinol tubes. These innovative techniques have opened up new possibilities for developing next-generation medical implants and devices.
Precision Techniques for Nitinol Tubes Cutting
Precision techniques for nitinol tube cutting involve using state-of-the-art laser cutting systems that can accurately shape and trim nitinol tubes to specifications. By employing advanced software algorithms and real-time monitoring, manufacturers can ensure that each cut is made with utmost precision, resulting in high-quality nitinol components with minimal material waste. These precision techniques are crucial in meeting the stringent quality standards for medical applications.
Advancements in Nitinol Tubes Cutting
Advancements in nitinol tube cutting have led to increased efficiency and cost-effectiveness in manufacturing processes. With faster laser cutting machines and improved cooling systems, manufacturers can now produce more nitinol tube components without compromising quality. Furthermore, advancements in automation have streamlined production workflows, reducing lead times and enhancing overall productivity.
By incorporating innovative approaches, precision techniques, and advancements in nitinol tube cutting, manufacturers are poised to elevate medical device manufacturing standards while driving forward technological advancements in the industry.
GEE SMA: Your Partner for High-Quality Nitinol Solutions
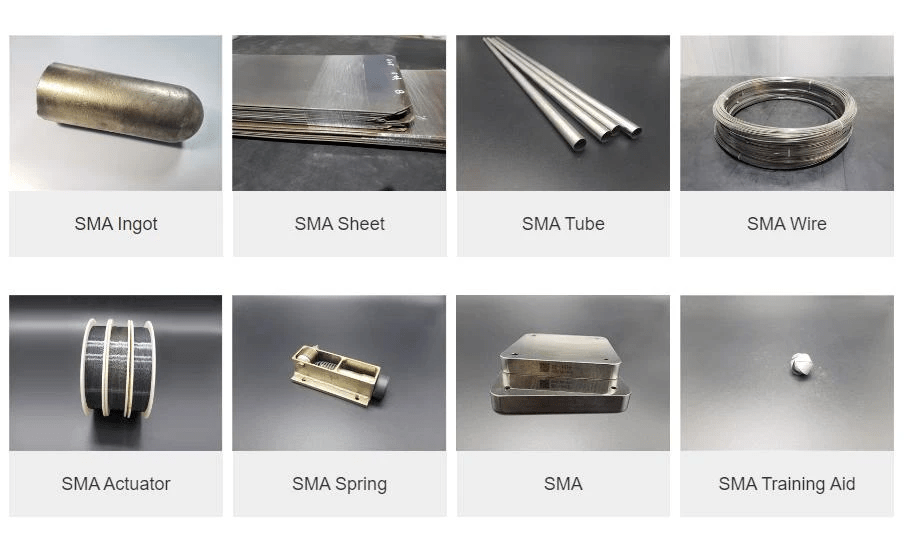
In conclusion, the latest nitinol-cutting techniques have revolutionized the industry, elevating standards and setting the stage for future trends. Nitinol laser cutting has paved the way for precision and efficiency in braid, flat wire, tube cutting, electropolishing, and machining processes. As demand for high-quality nitinol solutions grows, GEE SMA remains your trusted partner for innovative and reliable nitinol products.
Elevating Nitinol Cutting Standards
The advancements in nitinol cutting techniques have undeniably elevated industry standards, allowing for unparalleled precision and quality. With innovative approaches to braid, flat wire, and tube cutting, as well as electropolishing and machining processes, manufacturers can now easily achieve superior results. The future of nitinol cutting is bright, promising even greater advancements in efficiency and accuracy.
Future Trends in Nitinol Laser Cutting
As technology continues to evolve, future trends in nitinol laser cutting are expected to focus on further enhancing precision and speed while minimizing waste. From refining existing techniques to exploring new application methods, the industry is poised for continuous improvement in meeting customer demands for high-quality nitinol products.
At GEE SMA, we understand the importance of delivering top-notch nitinol solutions that meet the highest quality and performance standards. Our commitment to innovation and excellence ensures that our customers receive the best-in-class products tailored to their needs. With a focus on collaboration and customer satisfaction, we are dedicated to being your preferred partner for all your nitinol requirements.