Introduction
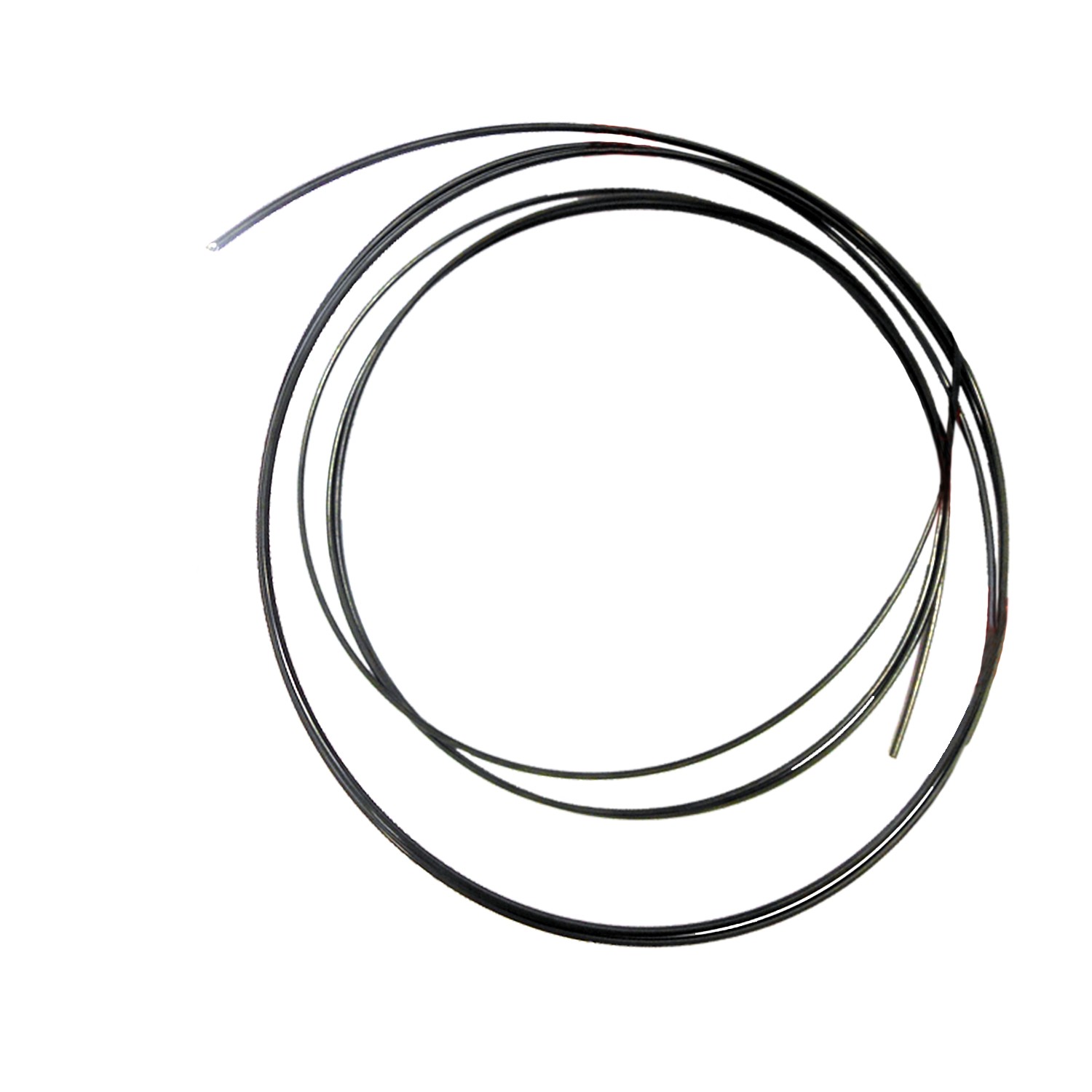
In the world of micro manufacturing, understanding Nitinol components is crucial for creating high-quality products. From Nitinol Braiding for Implantable Devices to Nitinol Micro Laser Cutting and Ultra-fine Nitinol Wires, the versatility of this shape memory alloy opens up a world of possibilities for innovative designs and precision engineering.
Understanding Nitinol Components
Nitinol components are known for their unique ability to return to a predetermined shape when exposed to heat or pressure, making them ideal for intricate medical devices and other precision applications. Whether it's the flexibility of Nitinol Braiding for Implantable Devices or the precision of Ultra-fine Nitinol Wires, these components offer unparalleled performance in various industries.
The Importance of Best Practices for Micro Manufacturers
For micro manufacturers, adhering to best practices in Nitinol manufacturing is essential to ensure consistency, quality, and reliability in every component produced. From material selection to production processes, following industry standards and guidelines is crucial in delivering top-notch products that meet the highest standards.
Exploring the World of Nitinol Manufacturing
The world of Nitinol manufacturing encompasses cutting-edge technologies such as Micro 3D Metal Manufacturing and advanced techniques like Nitinol-Edgetech Industries' innovative processes. This exploration into the realm of shape memory alloys offers a glimpse into the future of micro manufacturing and its potential impact on various industries.
The Versatility of Nitinol Components
Nitinol, a shape memory alloy, offers a wide range of applications for micro manufacturers. Nitinol braiding for implantable devices provides flexibility and durability in medical implants, ensuring patient comfort and longevity. Additionally, nitinol micro laser cutting allows for precise shaping of components, enabling intricate designs for various industries. Ultra-fine nitinol wires further showcase the versatility of this material, offering strength and resilience in micro manufacturing processes.
Nitinol Braiding for Implantable Devices
Nitinol braiding is a crucial technique in the production of implantable medical devices. This process involves weaving nitinol wires to create flexible yet sturdy structures that are ideal for use in cardiovascular stents and other biomedical implants. The unique properties of nitinol allow these braided components to adapt to changes in temperature and pressure within the body, making them invaluable in the field of medical technology.
Nitinol Micro Laser Cutting
Micro laser cutting with nitinol enables manufacturers to achieve precision and intricacy in their component designs. This advanced manufacturing process allows for the creation of intricate patterns and shapes that are essential for various applications such as aerospace engineering and electronics. The ability to cut nitinol at a microscopic level ensures that manufacturers can produce high-quality components with unmatched precision.
Ultra-fine Nitinol Wires
Ultra-fine nitinol wires offer exceptional strength and flexibility, making them ideal for use in micro manufacturing processes across industries. These thin wires can be manipulated into complex shapes while retaining their shape memory properties, allowing for the creation of intricate components used in medical devices, automotive technologies, and more.
Precision Engineering with Nitinol
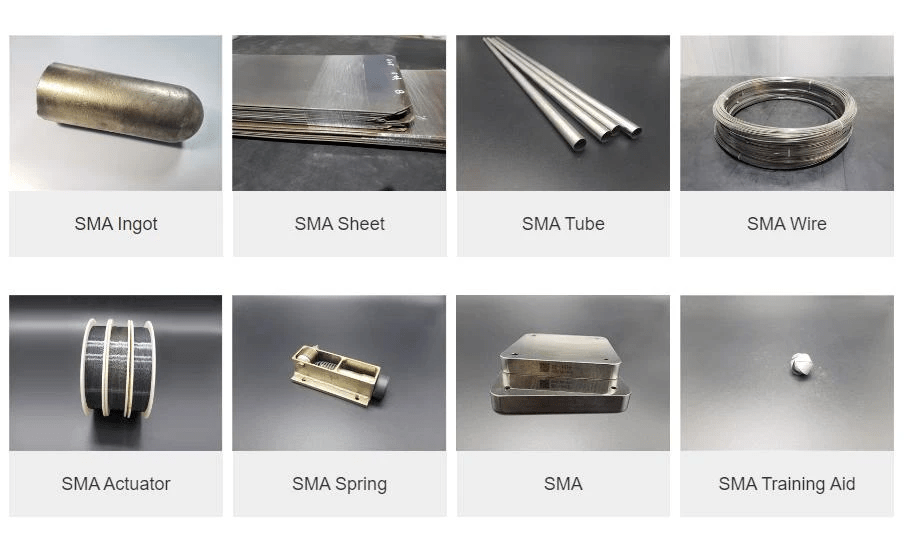
When it comes to precision engineering with Nitinol, micro manufacturers are at the forefront of creating innovative solutions. Nitinol micro-springs are a prime example of this, offering unparalleled flexibility and resilience in medical devices and other applications. These tiny springs, crafted with precision by expert micro manufacturers, play a crucial role in ensuring optimal performance and longevity in various industries.
Nitinol Micro-Springs
Nitinol micro-springs are meticulously designed and manufactured by skilled artisans to meet the exacting standards of modern technology. Their small size and exceptional memory properties make them ideal for use in intricate medical devices, where precision is paramount. Micro manufacturers leverage advanced techniques to create these springs, ensuring that they exhibit the desired shape memory effect and superelasticity required for their intended applications.
Furthermore, Nitinol micro-springs are designed to withstand the harsh conditions within the human body, ensuring longevity and reliability in medical devices. The intricate design and manufacturing process involve precise control over the composition and structure of the material, resulting in springs that can endure repeated use without degradation. This level of durability is essential for medical applications where the performance of these tiny components can have a significant impact on patient outcomes.
Nitinol Stent & Nitinol Medical Devices Shape Setting
In the realm of medical devices, Nitinol stents and shape-set components have revolutionized minimally invasive procedures. Micro manufacturers play a pivotal role in shaping these devices to precise specifications, enabling them to adapt to physiological changes within the body seamlessly. The expertise of micro manufacturers is evident in the flawless execution of shape-setting processes that ensure optimal performance and patient safety.
The art of Nitinol manufacturing lies in the ability to create intricate shapes and structures that can withstand the dynamic environment of the human body. Micro manufacturers leverage advanced technology and expertise to ensure that Nitinol stents and shape-set components are designed with precision and accuracy. This attention to detail is crucial in enabling these devices to seamlessly adapt to physiological changes, ultimately enhancing patient outcomes and safety.
GEE SMA and the Art of Nitinol Manufacturing
GEE SMA (Shape Memory Alloys) represents an advanced approach to Nitinol manufacturing that requires finesse and expertise from micro manufacturers. This cutting-edge technology allows for intricate designs and complex shapes to be achieved with precision, opening up new possibilities for innovative applications across various industries. With GEE SMA techniques mastered by skilled micro manufacturers, the art of Nitinol manufacturing reaches new heights.
GEE SMA has revolutionized the Nitinol manufacturing process by enabling intricate designs and complex shapes to be achieved with unparalleled precision. This level of precision opens up new possibilities for innovative applications across various industries, from medical devices to aerospace engineering. Skilled micro manufacturers who have mastered GEE SMA techniques are able to push the boundaries of what is possible in Nitinol manufacturing, allowing for greater customization and creativity in product design.
Cutting-edge Innovations in Nitinol Manufacturing
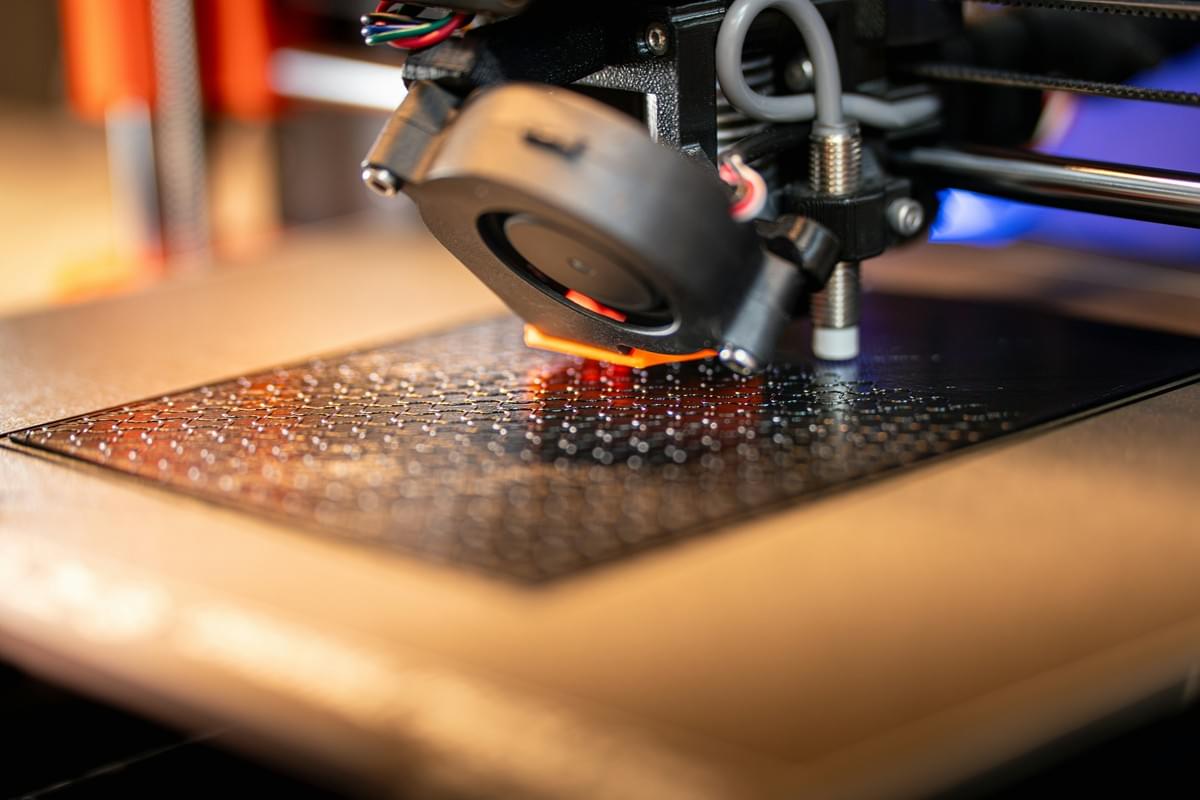
Nitinol-Edgetech Industries is at the forefront of cutting-edge innovations in Nitinol manufacturing, specializing in the production of high-quality Nitinol components for a wide range of applications. With a focus on precision engineering and advanced technology, they have revolutionized the industry by offering customized solutions for micro manufacturers looking to incorporate Nitinol components into their products.
Nitinol-Edgetech Industries
Nitinol-Edgetech Industries utilizes state-of-the-art equipment and expertise to produce Nitinol components such as Nitinol Braiding for Implantable Devices, Nitinol Micro Laser Cutting, and Ultra-fine Nitinol Wires. Their commitment to quality and innovation has made them a trusted partner for micro manufacturers seeking reliable and efficient solutions for their specialized needs.
Nitinol-Edgetech Industries has a proven track record of delivering high-quality Nitinol components that meet the unique requirements of micro manufacturers. Their advanced equipment and skilled team enable them to offer precise Nitinol Braiding for Implantable Devices, Nitinol Micro Laser Cutting, and Ultra-fine Nitinol Wires that are essential for the success of specialized projects. By consistently staying at the forefront of innovation, they continue to be the go-to partner for those seeking reliable and efficient solutions in the micro manufacturing industry.
Micro 3D Metal Manufacturing
Micro 3D Metal Manufacturing has emerged as a game-changer in the field of Nitinol manufacturing, allowing for the creation of intricate and complex designs with unparalleled precision. This technology opens up new possibilities for micro manufacturers looking to push the boundaries of what is possible with Nitinol components, offering endless potential for customization and innovation. With Micro 3D Metal Manufacturing, manufacturers can now produce Nitinol components that were previously thought to be too intricate or delicate to manufacture, opening up a world of new design possibilities. Additionally, this technology allows for the production of smaller and more lightweight Nitinol components, making it ideal for industries such as medical devices and aerospace where weight and size are critical factors.
The Future of Nitinol Components
As the demand for miniaturized devices continues to grow across industries, the future of Nitinol components looks promising. With ongoing advancements in materials science and manufacturing techniques, we can expect to see even smaller and more intricate designs that offer enhanced performance and reliability. The future holds endless opportunities for micro manufacturers to leverage the unique properties of Nitinol in creating cutting-edge products that meet the evolving needs of various industries.
Stay ahead of the curve by embracing these cutting-edge innovations in Nitinol manufacturing! As a micro manufacturer, leveraging these advancements will allow you to create high-quality products that stand out in today's competitive market.
Best Practices for Micro Manufacturers
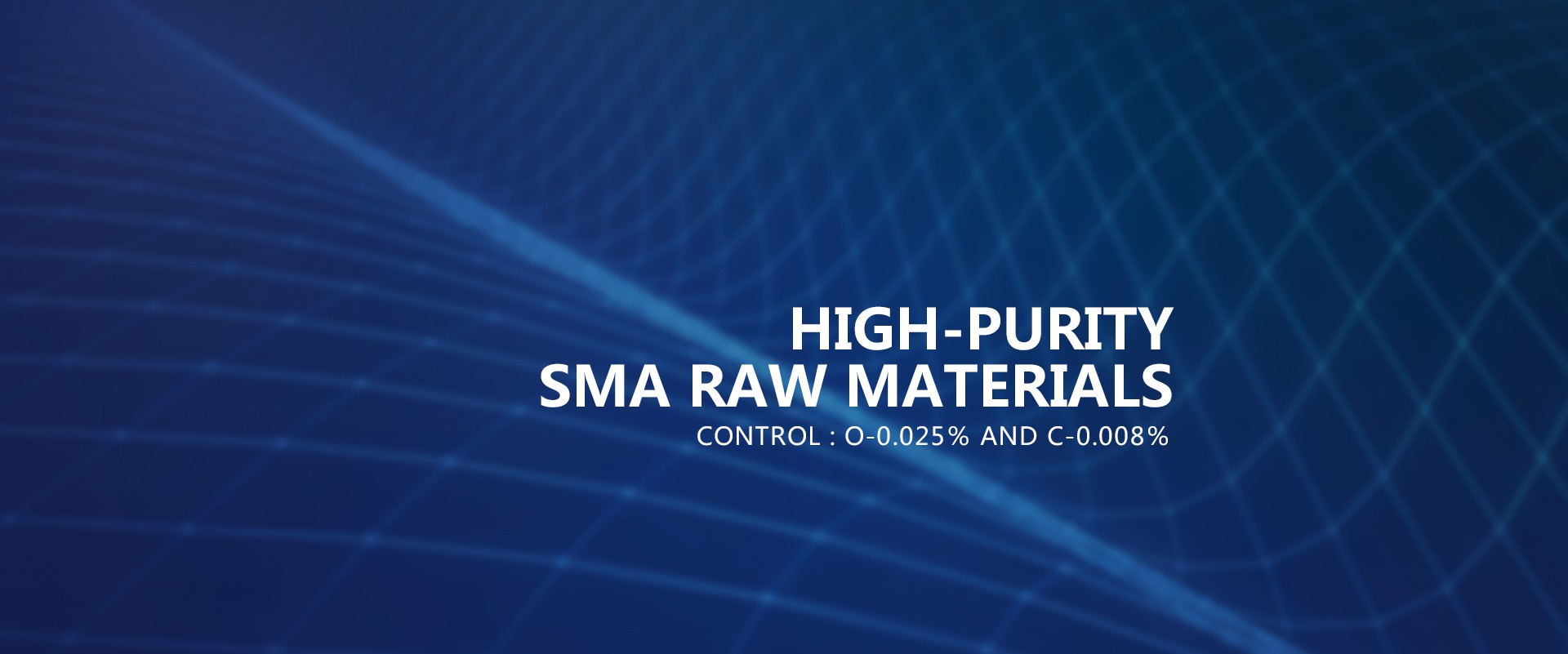
Micro manufacturers play a crucial role in the production of Nitinol components, ensuring quality and precision in every step of the manufacturing process. Quality control is paramount in Nitinol component production, with stringent measures in place to guarantee the reliability and performance of each component.
Quality Control in Nitinol Component Production
Quality control in Nitinol component production involves meticulous inspection and testing to ensure that each component meets industry standards. From the initial material selection to the final product, every stage undergoes rigorous quality checks to identify any defects or inconsistencies. This attention to detail ensures that Nitinol components are reliable and meet the highest standards for medical and industrial applications.
After the initial material selection, the Nitinol components are carefully shaped and formed to meet the specific requirements of medical and industrial applications. This customization process involves precision engineering and advanced manufacturing techniques to ensure that each component is tailored to the unique needs of the end user. By taking into account factors such as size, shape, and performance requirements, Nitinol components can be optimized for a wide range of uses, from surgical instruments to aerospace technology.
Customizing Nitinol Components to Meet Industry Needs
Micro manufacturers specialize in customizing Nitinol components to meet specific industry requirements. Whether it's Nitinol braiding for implantable devices, micro laser cutting, or ultra-fine Nitinol wires, these manufacturers have the expertise to tailor solutions that align with the unique needs of various industries. Their ability to customize Nitinol components ensures that they can be seamlessly integrated into a wide range of applications.
The Role of GEE SMA in Advancing Nitinol Manufacturing
GEE SMA plays a pivotal role in advancing Nitinol manufacturing by leveraging cutting-edge technologies and innovative techniques. As a leader in micro manufacturing, GEE SMA is at the forefront of developing new methods for shaping and processing Nitinol components with unparalleled precision and efficiency. Their contributions are instrumental in pushing the boundaries of what is possible with Nitinol, driving advancements across multiple industries.
With an emphasis on quality control, customization, and innovation, micro manufacturers are essential partners for industries relying on advanced materials like Nitinol. Their expertise ensures that businesses can access high-quality components tailored to their specific needs while driving continuous advancements within the field of nitinol manufacturing.
Industry Applications and Advances in Nitinol
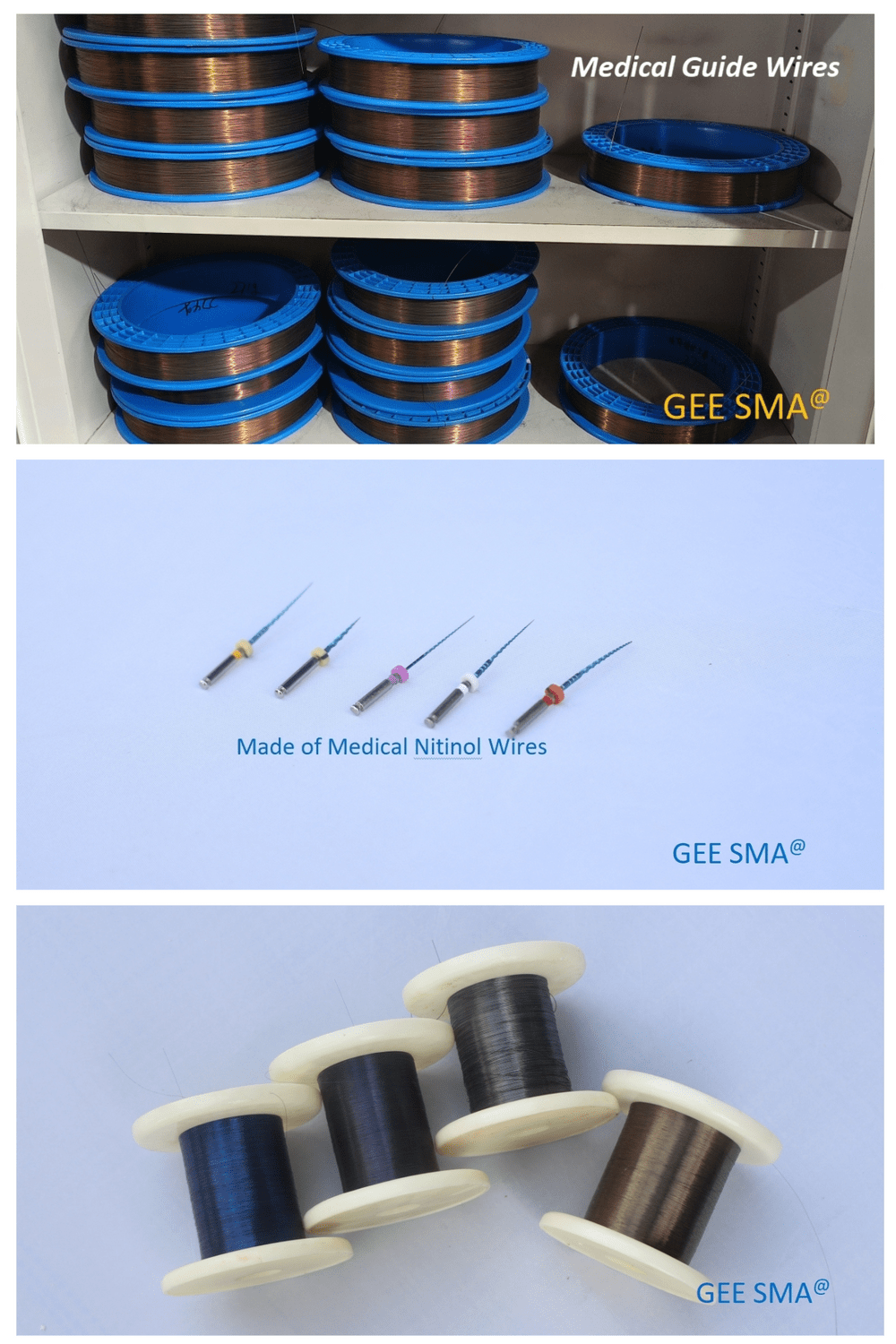
Nitinol in Biomedical Devices
Nitinol has revolutionized the biomedical industry with its use in creating innovative implantable devices such as stents, guidewires, and orthodontic wires. These components are crucial for minimally invasive surgeries and have significantly improved patient outcomes. The flexibility and shape memory of Nitinol make it an ideal material for biomedical applications.
Nitinol in Aerospace and Automotive Industries
In the aerospace and automotive industries, Nitinol's unique properties are harnessed to create components that require high strength, flexibility, and resistance to corrosion. From actuators to sensors, Nitinol plays a vital role in improving the performance and reliability of critical systems in these sectors.
Advantages and Challenges of Using Nitinol Components
The advantages of using Nitinol components are abundant, including its superelasticity, biocompatibility, and durability. However, challenges such as precise manufacturing requirements and cost considerations need to be carefully managed by micro manufacturers to ensure the successful integration of Nitinol components into various applications.
By leveraging the versatility of Nitinol components across different industries, micro manufacturers can continue to drive innovation while overcoming challenges associated with their production and integration.
Conclusion

As we wrap up our exploration of Nitinol manufacturing, it's crucial for micro manufacturers to prioritize quality control and customization to meet industry demands. The impact of Nitinol components in various industries, from biomedical devices to aerospace and automotive, is undeniable. Embracing best practices for Nitinol manufacturing is key to driving innovation and meeting the ever-evolving needs of the market.
Key Considerations for Nitinol Component Manufacturing
Micro manufacturers must prioritize precision engineering and cutting-edge innovations to ensure the highest quality Nitinol components. From ultra-fine Nitinol wires to micro-springs, attention to detail is paramount in every step of the manufacturing process. Quality control measures must be implemented at every stage to guarantee the reliability and performance of Nitinol components.
The Impact of Nitinol Components in Various Industries
Nitinol components play a pivotal role in revolutionizing industries such as healthcare, aerospace, and automotive. From Nitinol braiding for implantable devices to micro laser cutting techniques, the versatility of these components continues to drive advancements across various sectors. The impact of Nitinol components extends far beyond their small size, making them indispensable in modern engineering.
Embracing Best Practices for Nitinol Manufacturing
Micro manufacturers must embrace best practices in Nitinol manufacturing by leveraging cutting-edge innovations such as those offered by companies like Nitinol-Edgetech Industries and Micro 3D Metal Manufacturing. By staying ahead of industry trends and continuously improving production processes, manufacturers can ensure that they deliver top-notch customized solutions that meet the ever-evolving demands of their clients.