Introduction
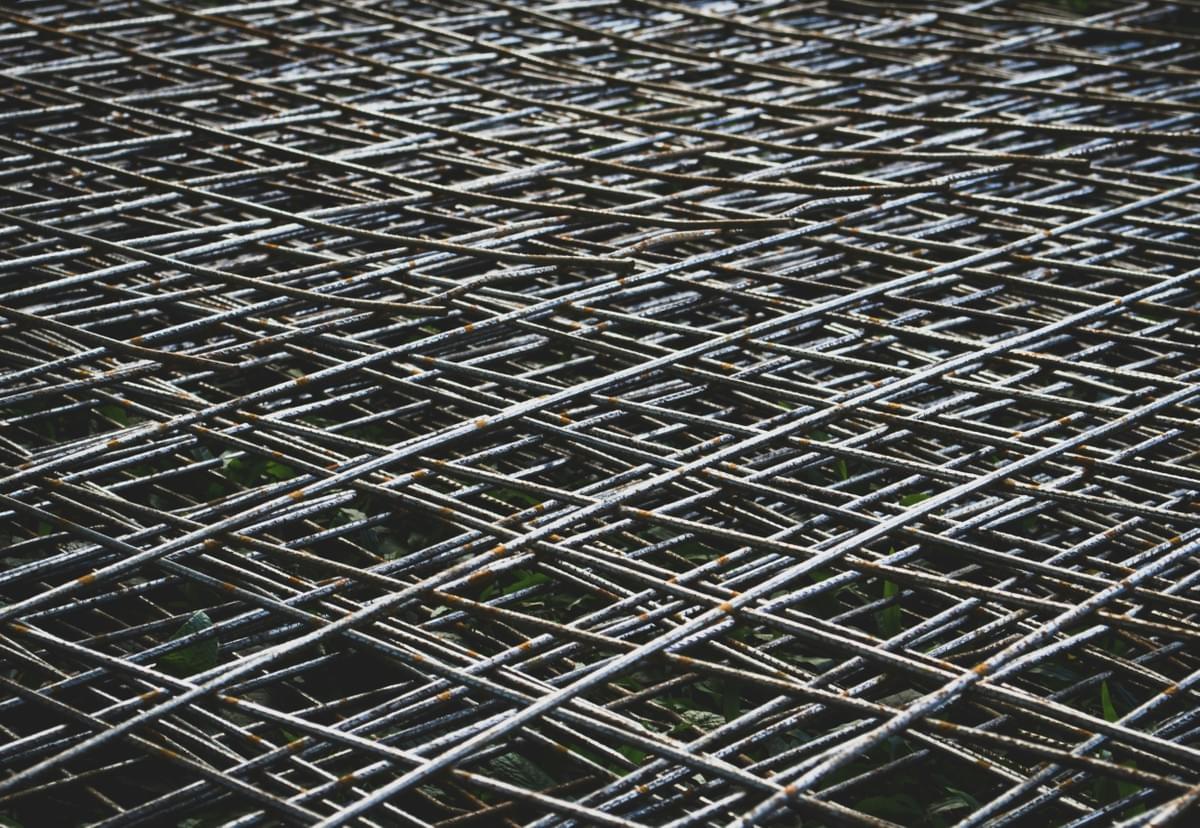
Nitinol stent manufacturing has revolutionized the medical industry, offering innovative solutions for cardiovascular diseases. With the rise of nitinol manufacturing companies, the production of these life-saving devices has become more accessible and efficient. Understanding how nitinol is made is crucial to appreciating its unique properties and applications.
Understanding Nitinol Stent Manufacturing
Nitinol stents, known for their ability to expand within narrowed arteries, are a marvel of medical technology. Their creation involves a fascinating process that combines material science and engineering expertise:
- Shape Memory Alloy: Nitinol, a nickel-titanium alloy, possesses unique shape memory properties. When formed into a stent shape, it can be compressed for delivery and regain its original form upon reaching body temperature, effectively opening the blocked artery.
- Precision Engineering: Manufacturing nitinol stents requires precise techniques like laser cutting and machining to create intricate designs that ensure optimal expansion and artery support.
- Advanced Metallurgy: Heat treatment is crucial in defining the stent's final shape memory and mechanical properties, ensuring its functionality and long-term durability within the body.
By combining these elements, nitinol stent manufacturing offers a minimally invasive and effective solution for treating arterial blockages.
The Rise of Nitinol Manufacturing Companies
In recent years, there has been a significant increase in nitinol manufacturing companies, driven by the growing demand for medical devices made from this superelastic material. These companies have played a pivotal role in advancing production processes and expanding the range of nitinol-based products available.
How Nitinol Is Made
Nitinol is a nickel-titanium alloy that exhibits unique shape memory and superelastic properties. Its production involves carefully controlling its composition, heat treatment, and mechanical processing to achieve the desired characteristics for medical applications.
Now, you have an engaging introduction that sets the stage for exploring all aspects of nitinol stent manufacturing while seamlessly incorporating relevant keywords.
The History of Nitinol
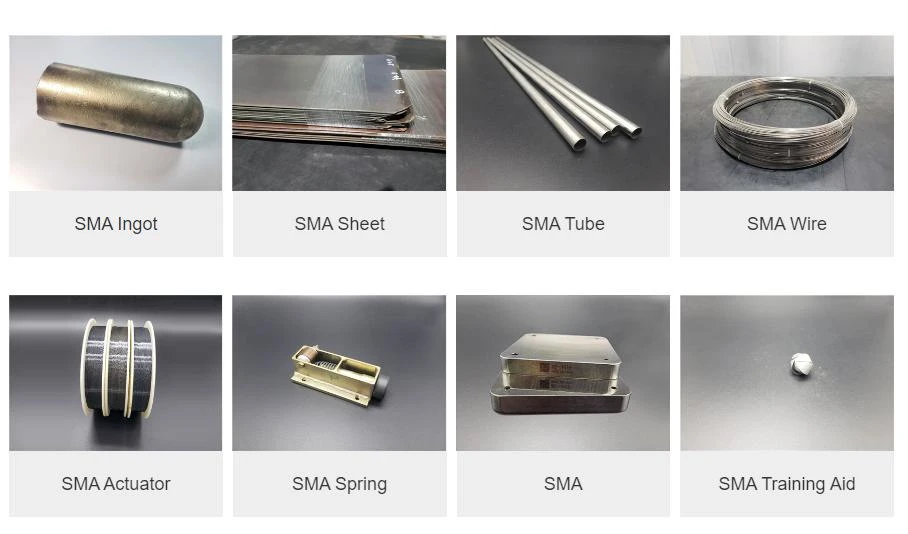
Nitinol, a unique alloy of nickel and titanium, was discovered in 1961 by the U.S. Naval Ordnance Laboratory. Nitinol derives from its composition and place of discovery: Nickel Titanium Naval Ordnance Laboratory. Initially, due to its shape memory properties, nitinol was used in orthodontic wires, but it quickly evolved into various applications, including medical devices like stents.
The Discovery of Nitinol
The discovery of Nitinol happened serendipitously when scientists observed the unusual behavior of a sample that returned to its original shape after being deformed at high temperatures. This phenomenon led to further research and understanding of nitinol's unique shape memory and superelastic properties, making it a valuable material for various industries, including healthcare.
The discovery of Nitinol's unique shape memory and superelastic properties revolutionized the manufacturing industry, developing new processes and techniques for working with this remarkable material. Engineers and scientists have since been able to manipulate Nitinol's properties to create products that can withstand extreme conditions, making it an ideal choice for aerospace, automotive, and consumer goods applications. As a result, Nitinol has become an essential component in producing high-performance devices and equipment across a wide range of industries.
Nitinol's Evolution in Manufacturing
As the potential applications of Nitinol became apparent, manufacturing techniques evolved to meet the demand for this versatile material. With advancements in metallurgy and fabrication methods, Nitinol manufacturing companies emerged to produce high-quality alloys with precise shape memory properties suitable for medical devices such as stents.
As the potential applications of Nitinol became apparent, manufacturing techniques evolved to meet the demand for this versatile material. With advancements in metallurgy and fabrication methods, Nitinol manufacturing companies emerged to produce high-quality alloys with precise shape memory properties suitable for medical devices such as stents. As the demand for Nitinol grew, research and development efforts focused on expanding its applications beyond medical devices. This led to the creation of Nitinol components used in aerospace, automotive, and consumer electronics, showcasing its adaptability and reliability in various fields.
Applications of Nitinol Shape Memory Alloys
The exceptional properties of Nitinol shape memory alloys have led to their widespread use in various fields ranging from aerospace engineering to biomedical applications. In the medical field, Nitinol stents have become indispensable for treating cardiovascular diseases due to their ability to self-expand within blood vessels while maintaining flexibility and strength.
In addition to their use in stents, Nitinol shape memory alloys are employed in orthodontic wires and dental braces. Nitinol's unique ability to return to its original shape after deformation makes it an ideal material for these applications, as it allows for constant pressure on the teeth, resulting in more effective and efficient orthodontic treatment. Furthermore, the biocompatibility of Nitinol makes it safe for prolonged contact with bodily tissues, making it a preferred choice in dentistry.
Nitinol Stent Manufacturing Process
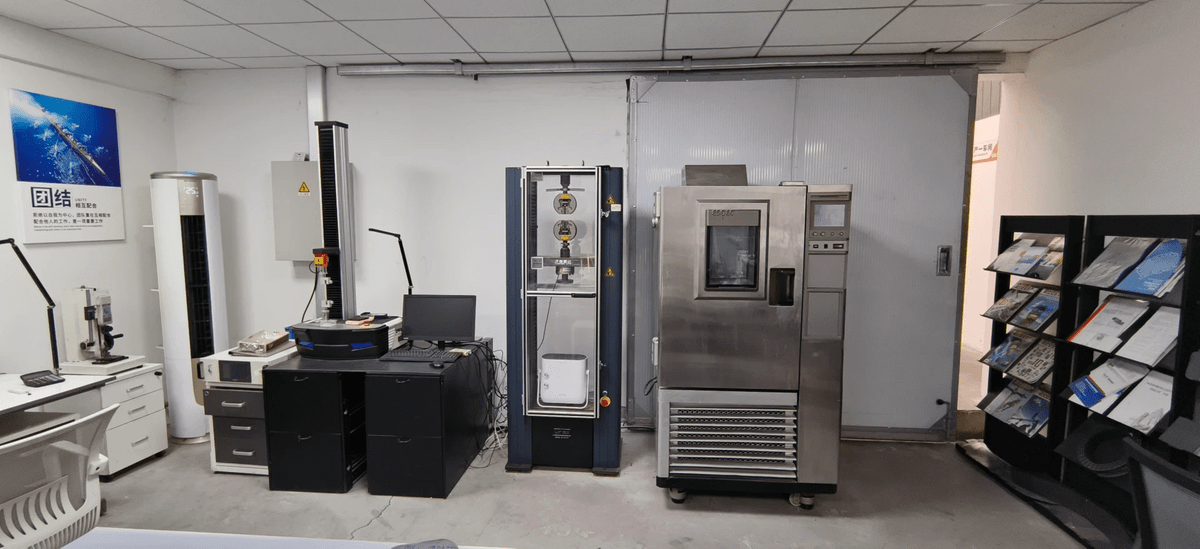
Nitinol stent manufacturing involves a meticulous process to ensure the quality and performance of the final product. The first step in the process is determining the nitinol alloy composition, which typically consists of nickel and titanium in varying proportions. This composition is critical as it directly affects the stent's mechanical properties, such as flexibility and shape memory.
Nitinol Alloy Composition
The nitinol alloy composition is carefully selected based on the stent's specific requirements, such as its intended application and desired properties. Different ratios of nickel and titanium result in varying levels of superelasticity and shape memory effect, allowing for customization according to patient needs. This crucial step sets the foundation for the subsequent fabrication techniques for creating nitinol stents.
After the nitinol alloy composition is carefully selected, the next step in creating nitinol stents involves using fabrication techniques specifically tailored to this unique material. These techniques may include laser cutting, electrochemical polishing, and shape setting, all designed to manipulate the nitinol alloy into the precise shape and size required for the stent. The expertise and precision involved in these fabrication techniques are essential in ensuring that the final product meets the necessary standards for medical devices.
Nitinol Fabrication Techniques
Once the nitinol alloy composition is determined, various fabrication techniques shape the material into stents. These techniques may include laser cutting, wire forming, and heat treatment processes that enable precise control over the stent's dimensions and mechanical characteristics. The intricacy of these techniques reflects the complexity involved in nitinol manufacturing but ultimately ensures high-quality stents with exceptional performance.
Quality Control in Nitinol Stent Production
Quality control is pivotal throughout nitinol stent production to guarantee reliability and safety. Stringent testing procedures are implemented at each manufacturing stage to assess dimensional accuracy, surface finish, and mechanical behavior. This meticulous approach ensures that every nitinol stent meets regulatory standards and delivers optimal performance when deployed in patients.
In addition to the rigorous testing procedures, quality control in nitinol stent production also involves continuous monitoring of the manufacturing environment to ensure that all materials and processes meet the highest standards. This includes regular equipment inspections, machinery calibration, and adherence to strict cleanliness protocols. By maintaining a controlled production environment, manufacturers can minimize the risk of contamination and ensure the quality of every nitinol stent produced.
Understanding the intricate process involved in nitinol stent manufacturing can help one appreciate the level of expertise required to produce these life-saving medical devices.
Advantages of Nitinol Stents
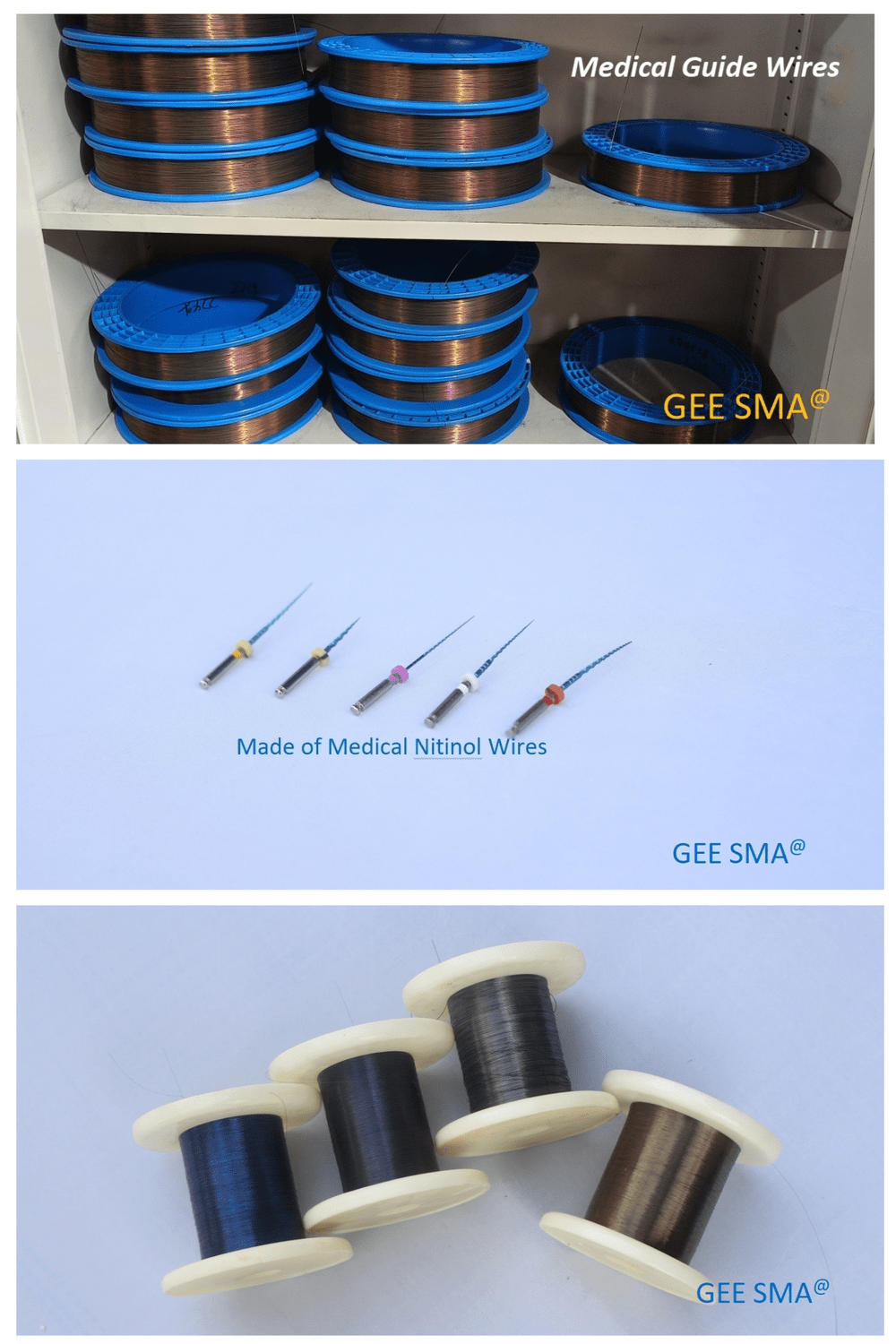
Flexibility and Durability
Nitinol stents offer several advantages over traditional stents, making them a popular choice for improving blood flow:
- Enhanced Flexibility: Nitinol allows easier insertion into the body's delicate vascular system, minimizing the risk of damage during placement.
- Adaptable to Movement: This flexibility also enables the stent to adapt to natural body movements, reducing the chance of fractures or dislodgment.
- Long-Term Durability: Nitinol's inherent strength ensures the stent maintains its shape and integrity over time, providing lasting support to weakened blood vessels.
- Biocompatible and Corrosion-Resistant: Nitinol is well-tolerated by the body, minimizing the risk of rejection or adverse reactions. Additionally, its corrosion resistance ensures the stent remains intact and free from degradation, even when exposed to bodily fluids for extended periods.
Nitinol stents combine flexibility, durability, and biocompatibility, making them a valuable tool for maintaining healthy blood flow and improving patient outcomes.
Biocompatibility and Corrosion Resistance
One of the key advantages of nitinol stents is their biocompatibility, meaning they are well-tolerated by the body and do not trigger adverse reactions. This property reduces the risk of inflammation or rejection, making nitinol stents a preferred choice for patients. Additionally, nitinol exhibits exceptional corrosion resistance, ensuring that the stent remains structurally sound within the harsh environment of the human body.
Customization for Patient Needs
Nitinol's unique shape memory properties allow for the customization of stents to meet specific patient requirements. This personalized approach ensures that each stent is tailored to fit individual anatomies and address diverse medical conditions. As a result, patients benefit from improved treatment outcomes and reduced complications due to better-fitting nitinol stents.
Challenges in Nitinol Stent Manufacturing
Nitinol stent manufacturing presents several challenges, including complex manufacturing techniques, regulatory compliance, and production cost considerations. The intricate process of shaping and fabricating nitinol alloys requires specialized equipment and skilled technicians to ensure the stents meet stringent quality standards.
Complex Manufacturing Techniques
The production of nitinol stents involves intricate processes such as shape setting, superelasticity treatment, and laser cutting. These techniques demand precision and expertise to achieve the desired mechanical properties and dimensional accuracy required for medical devices. Manufacturers must invest in state-of-the-art machinery and continuous training to master these complex manufacturing methods.
Regulatory Compliance
Nitinol stent manufacturing is subject to rigorous regulatory standards imposed by health authorities worldwide. Companies must adhere to strict guidelines set forth by organizations such as the FDA and CE Mark to ensure the safety and efficacy of their products. Compliance with these regulations adds a layer of complexity to the manufacturing process, requiring meticulous documentation and quality control measures.
Cost Considerations in Production
Due to the specialized materials, equipment, and labor involved, producing nitinol stents can be cost-intensive. Manufacturers face challenges in optimizing production processes to minimize wastage while maintaining high-quality standards. Balancing cost-efficiency with superior product performance is a constant challenge in nitinol stent manufacturing.
Manufacturers are exploring innovative production techniques and materials to address the cost challenges in nitinol stent manufacturing. For example, advancements in additive manufacturing technology have enabled the production of complex nitinol stent designs with reduced material wastage. Additionally, using automated equipment and robotics in manufacturing can help streamline production and reduce labor costs, contributing to overall cost-efficiency.
Future Innovations in Nitinol Manufacturing
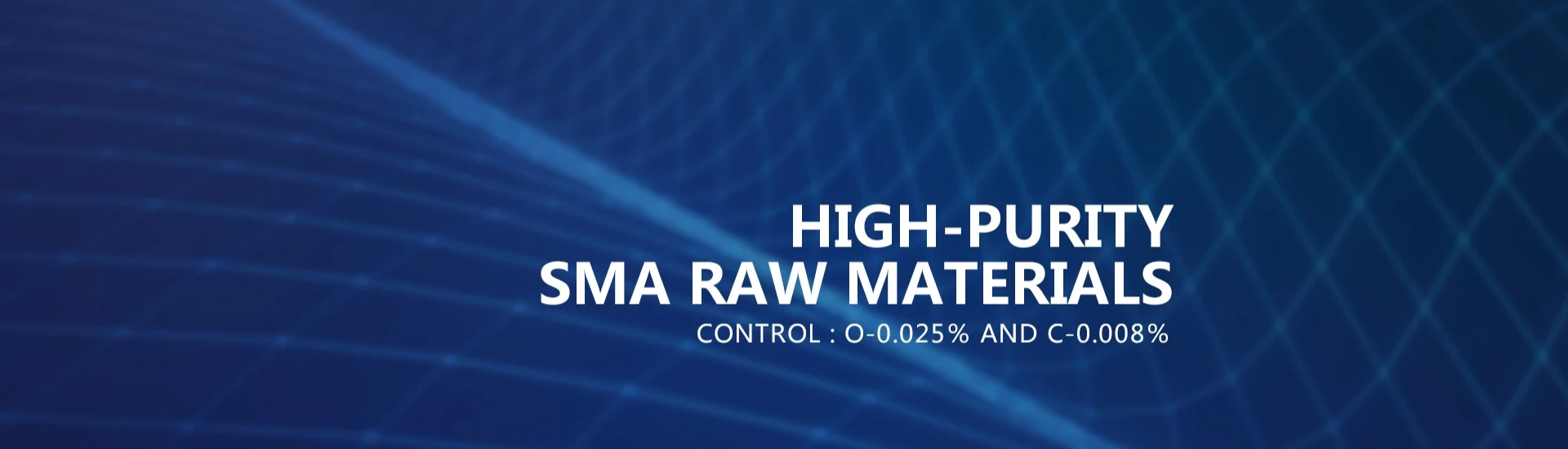
As the demand for nitinol stents continues to grow, advancements in nitinol material science are crucial for improving the performance and longevity of these medical devices. Researchers are focusing on developing new nitinol alloys with enhanced properties, such as improved fatigue resistance and higher tensile strength, to meet the evolving needs of patients and healthcare providers.
Advancements in Nitinol Material Science
In addition to refining the composition of nitinol alloys, there is a strong emphasis on integrating cutting-edge technology into the manufacturing process. This includes utilizing advanced modeling and simulation techniques to optimize the design and fabrication of nitinol stents and implementing innovative heat treatment methods to achieve precise shape memory characteristics and superelastic behavior.
Integration of Technology in Manufacturing
Furthermore, the integration of additive manufacturing technologies, such as 3D printing, is revolutionizing the production of nitinol stents by enabling complex geometries and customized designs previously unattainable with traditional manufacturing methods. This shift towards additive manufacturing enhances production efficiency and facilitates rapid prototyping and customization for individual patient requirements.
Market Trends and Opportunities
In response to growing market trends, manufacturers are exploring opportunities to expand their product offerings beyond traditional vascular stents. This includes developing novel applications for nitinol shape memory alloys in other medical devices, such as orthopedic implants and neurovascular devices. This opens up new avenues for innovation and growth within the nitinol manufacturing industry.
The Future of Nitinol Stent Manufacturing
As the demand for nitinol stent manufacturing continues to grow, the future looks promising for this innovative industry. With advancements in material science and technology, the potential for even more durable and customizable nitinol stents is on the horizon. The commitment to quality and innovation will drive the evolution of nitinol manufacturing in the future.
With ongoing research and development, the future of nitinol stent manufacturing holds great promise. As new techniques and materials are discovered, we can expect to produce even more advanced and effective stents, improving patient outcomes and quality of life.
The Importance of Quality in Nitinol Manufacturing
Nitinol's unique properties make it ideal for medical devices, particularly stents. However, ensuring patient safety and device functionality requires strict quality control measures. Here's why:
- Material Composition: Slight variations in nitinol's nickel and titanium content can significantly impact its shape memory and mechanical properties. Rigorous checks ensure the material meets precise specifications.
- Manufacturing Processes: Each stage significantly affects the final product from melting to forming. Quality control monitors these processes to guarantee consistent and reliable stent production.
- Dimensional Accuracy: Precise dimensions are critical for proper stent deployment and functionality. Quality control measures ensure stents meet the exact size and shape requirements.
- Surface Quality: Surface imperfections can compromise biocompatibility and increase the risk of infection. Stringent quality checks guarantee a smooth and flawless surface finish.
- Performance Testing: Every stent undergoes rigorous testing to verify its shape memory, mechanical strength, and fatigue resistance, ensuring it performs as intended within the body.
Nitinol manufacturers can deliver safe, reliable, and high-performing stents by implementing comprehensive quality control measures, fostering trust with healthcare providers, and ultimately improving patient outcomes.
GEE SMA's Commitment to Nitinol Innovation
At GEE SMA, our dedication to nitinol innovation drives us to push boundaries and explore new possibilities in stent manufacturing. By staying at the forefront of technological advancements and market trends, we are committed to delivering cutting-edge solutions that enhance patient care.