Introduction
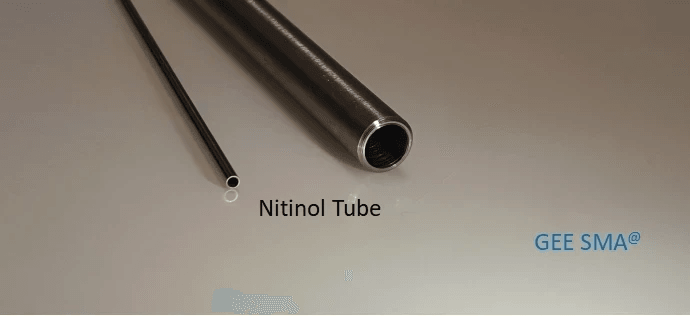
In materials engineering, the superelastic nitinol tube has emerged as a game-changer, revolutionizing various industries with its remarkable properties. From biomedical devices to aerospace and automotive applications, the versatility of nitinol alloys knows no bounds. Unleashing the potential of nitinol shape memory alloys has opened up a world of possibilities for innovative solutions and cutting-edge technologies.
Understanding Superelastic Nitinol Tube Applications
Superelastic nitinol tubes have found widespread applications in the medical field. Their unique ability to return to their original shape after deformation makes them ideal for minimally invasive surgical procedures. Their flexibility and biocompatibility make them suitable for various medical device applications.
Exploring the Versatility of Nitinol Alloys
Nitinol alloys, known for their shape memory and superelasticity, are indispensable in various industrial applications. Their ability to withstand high strain levels while returning to their original shape sets them apart from traditional materials, making them an attractive choice for engineers and designers across different sectors.
Unleashing the Potential of Nitinol Shape Memory Alloys
The unique properties of nitinol shape memory alloys have paved the way for groundbreaking product design and development innovations. From intricate nitinol wire components to metal nitinol fabrication, these alloys offer unparalleled performance and reliability in demanding environments.
The Science Behind Superelastic Nitinol Tubes
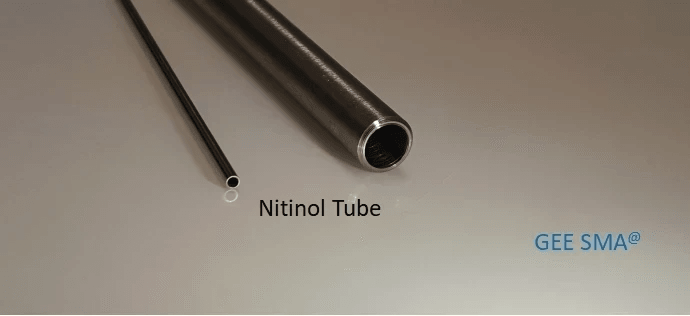
GEE SMA's Expertise in Crafting Nitinol Shape Memory Alloys
GEE SMA's team utilizes advanced metallurgical techniques and state-of-the-art equipment to craft nitinol shape memory alloys with unparalleled precision. Their dedication to quality control ensures that every superelastic nitinol tube meets strict specifications for performance and reliability.
In addition to their precision crafting techniques, GEE SMA's team also focuses on optimizing the composition of nitinol shape memory alloys to enhance their superelastic properties. By carefully controlling the ratio of nickel to titanium in the alloy, they can fine-tune the material's response to temperature and stress, resulting in tubes that can undergo significant deformation and return to their original shape with minimal energy loss. This level of control over the alloy's composition sets GEE SMA apart in the industry, allowing them to produce nitinol tubes with unmatched resilience and durability.
How Nitinol Alloys Enable Superelasticity
Nitinol alloys exhibit a phenomenon known as superelasticity, which allows them to undergo substantial deformation without permanent damage and then return to their original shape when the external force is removed. This unique property makes them highly sought after for various engineering applications.
Nitinol alloys are particularly popular in the biomedical field due to their superelasticity. This unique property allows Nitinol tubes to be used in various medical devices, such as stents and guidewires. The ability to withstand substantial deformation without permanent damage makes Nitinol ideal for applications where flexibility and resilience are crucial, such as in minimally invasive surgical procedures.
Applications of Superelastic Nitinol Tubes in Biomedical Devices
Superelastic nitinol tubes are a cornerstone in modern medicine due to their exceptional biocompatibility and mechanical properties. These unique characteristics have led to widespread application in various critical medical devices.
- Stents: Expandable structures to open blocked arteries.
- Guidewires: Flexible tools to navigate through blood vessels.
- Orthodontic wires: Shape and align teeth with gentle force.
- Surgical instruments: Precise and adaptable tools for minimally invasive procedures.
Nitinol tubes empower healthcare professionals to perform complex procedures with minimal invasiveness while ensuring patient safety and optimal outcomes.
Engineering Marvel: Nitinol Wire and Metal Nitinol
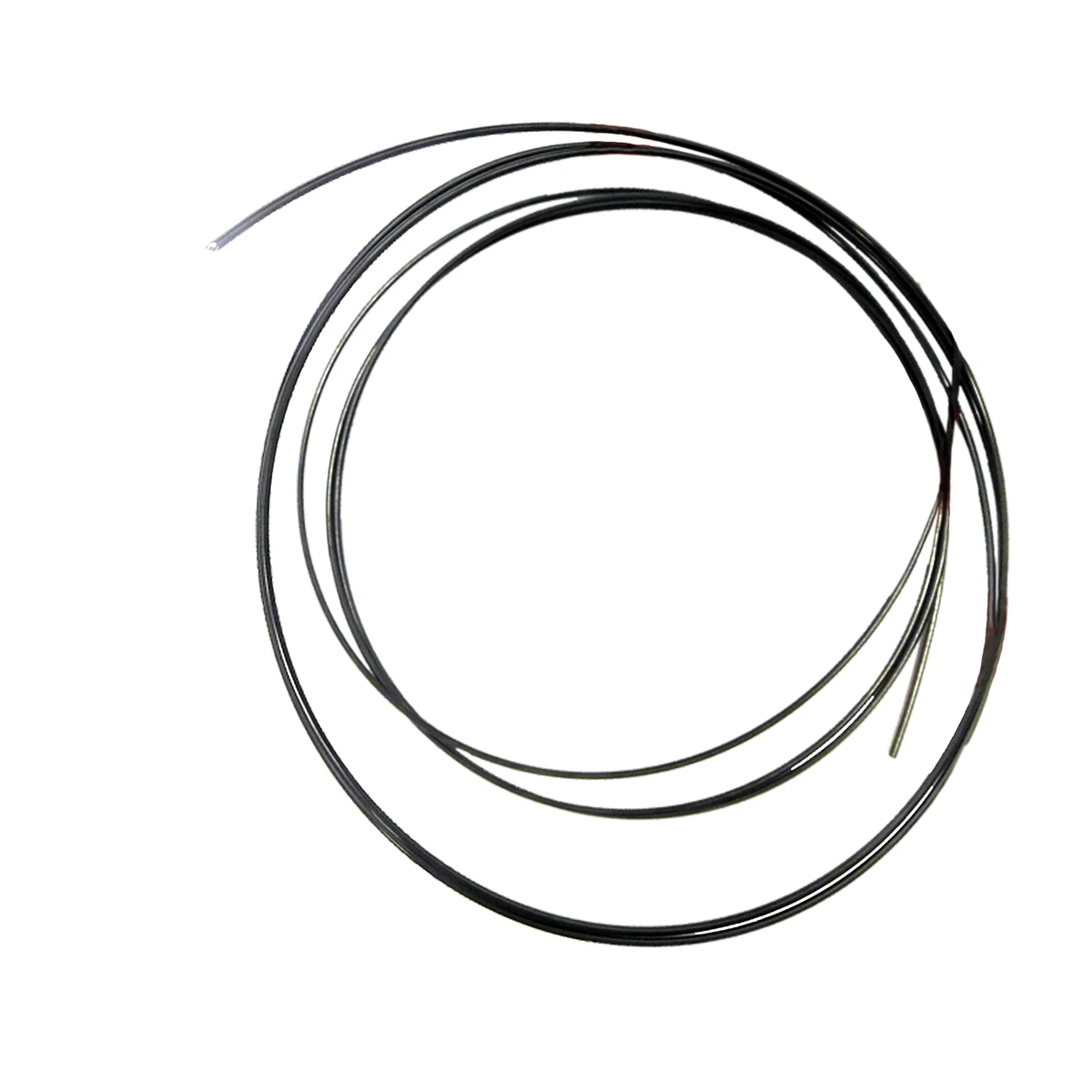
Nitinol wire is a game-changer in industrial applications, offering unparalleled flexibility and resilience. Its superelasticity and shape memory properties make it ideal for intricate mechanisms in robotics and machinery, providing durability and precision in manufacturing processes.
Advantages of Utilizing Nitinol Wire in Industrial Applications
Nitinol wire's versatility extends to a wide range of industrial uses, from actuators and sensors to orthodontic instruments. Its ability to return to its original shape after deformation ensures consistent performance, making it a top choice for complex engineering projects that demand reliability and longevity.
In addition to its shape memory and superelasticity, nitinol wire offers excellent corrosion resistance, making it suitable for use in harsh industrial environments. This durability ensures that nitinol components can withstand exposure to chemicals, moisture, and extreme temperatures without compromising performance. As a result, industries such as aerospace, automotive, and medical devices rely on nitinol wire to deliver consistent results in demanding applications.
Innovations in Metal Nitinol Fabrication
Innovative techniques in metal nitinol fabrication have paved the way for more intricate designs and custom solutions across various industries. From micro-scale components to large-scale structures, metal nitinol's adaptability allows for precise shaping and forming, opening up new possibilities for cutting-edge applications.
Nitinol Alloy Properties and Unique Characteristics
Nitinol alloys' exceptional properties, including biocompatibility, corrosion resistance, and thermal conductivity, make them an unparalleled material choice. These characteristics make them indispensable in fields such as medical devices, aerospace engineering, automotive technology, and beyond.
Nitinol alloys are also known for their shape memory and superelasticity, allowing them to return to their original shape after deformation. This unique property makes nitinol tubes ideal for applications in the aerospace and automotive industries, where components are subjected to extreme conditions. Whether in aircraft engines or automobile suspension systems, the superelasticity of nitinol tubes ensures durability and reliability in demanding environments.
Superelastic Nitinol Tube Applications in Aerospace and Automotive Industries
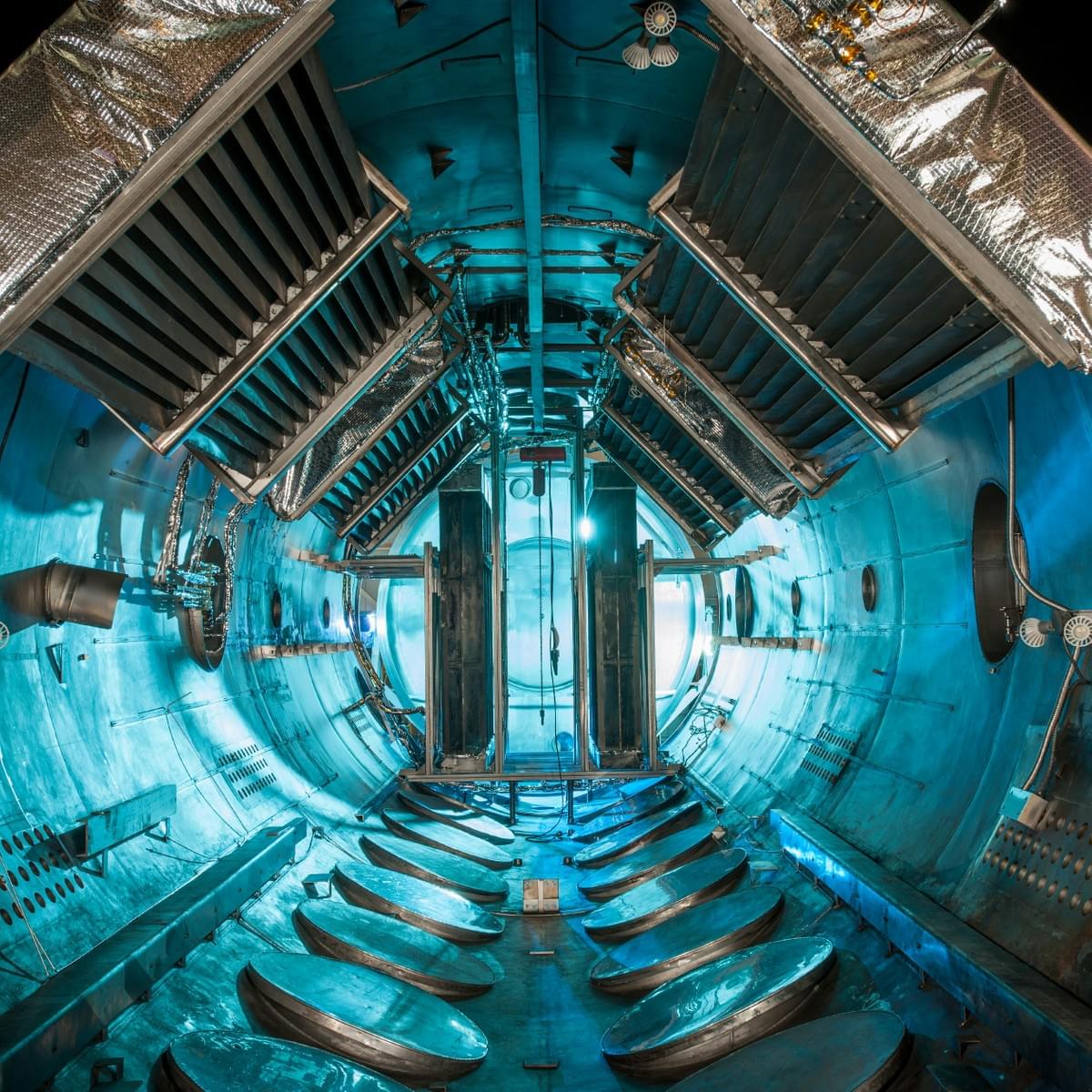
As a leader in advanced materials, GEE SMA has significantly contributed to aerospace and automotive advancements by utilizing superelastic nitinol tubes. These innovative tubes have been integrated into various components, enhancing critical systems' overall performance and reliability.
GEE SMA's Contribution to Aerospace and Automotive Advancements
GEE SMA's expertise in developing high-quality superelastic nitinol tubes has revolutionized aerospace and automotive engineering. GEE SMA has played a pivotal role in improving fuel efficiency, reducing emissions, and increasing the lifespan of aircraft and vehicles by providing lightweight, durable, and corrosion-resistant solutions. Furthermore, using nitinol tubes has allowed for more intricate and efficient design possibilities in both industries, leading to enhanced performance and safety standards. The unique properties of nitinol also contribute to greater precision and reliability in critical components, ensuring a higher level of operational excellence for aerospace and automotive applications. As a result, GEE SMA's contributions have advanced technology and elevated industry standards for quality and innovation.
Harnessing the Flexibility of Nitinol Springs
Nitinol springs are remarkable materials with exceptional properties that make them invaluable across various industries. Their unique flexibility and resilience enable them to excel in demanding environments.
Nitinol springs offer numerous advantages, including:
- Exceptional durability: Withstanding extreme conditions without compromising performance.
- Shape memory: Returning to their original form after deformation, ensuring reliability.
- Biocompatibility: Safe for use in medical applications, expanding their potential.
These characteristics make nitinol springs ideal for critical components in aerospace, automotive, and medical applications, such as landing gear assemblies, suspension systems, stents, and orthodontic wires. As technology advances, nitinol springs are poised to play an even greater role in shaping the future.
Enhancing Performance with Nitinol Shape Memory Components
The integration of nitinol shape memory components has significantly enhanced the performance of aerospace and automotive systems. These components can adapt to changing environmental conditions, improving operational efficiency and safety. Whether used in actuation systems or control mechanisms, nitinol shape memory components offer unparalleled reliability.
The versatility of nitinol shape memory components also allows for greater design flexibility in aerospace and automotive applications. This means that engineers can create more innovative and efficient systems that were previously impossible with traditional materials. The ability of nitinol components to withstand extreme temperatures and harsh environments further expands the possibilities for their use in critical systems, providing a level of durability that is unmatched by other materials. As a result, integrating nitinol shape memory components opens up new avenues for technological advancement in these industries.
Remember that our commitment to quality extends beyond words - it's evident in our actions!
Revolutionizing Medical Devices with Nitinol Shape Memory Alloys
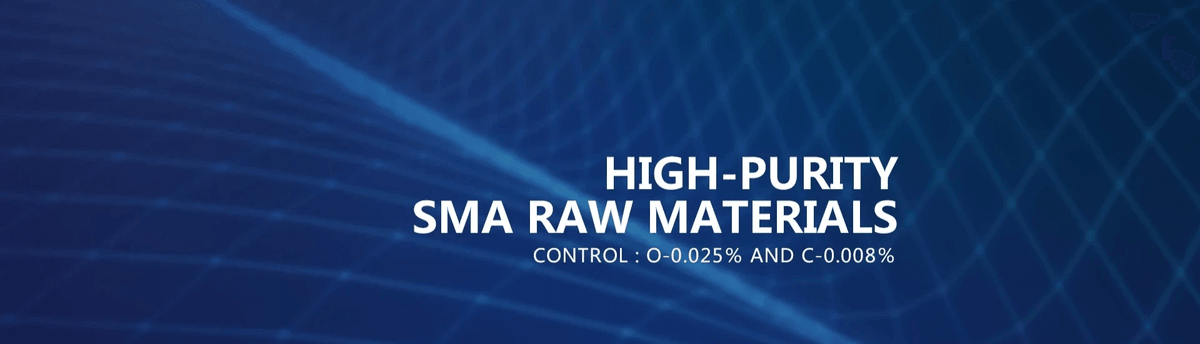
GEE SMA's Custom Solutions for Medical Device Manufacturers
GEE SMA is at the forefront of providing tailored solutions for medical device manufacturers, leveraging the unique properties of shape memory alloys (SMAs) like superelastic nitinol tubes. Our expertise in crafting custom nitinol components ensures that medical devices meet the specific requirements of each application, from cardiovascular implants to orthopedic instruments.
Nitinol's Role in Minimally Invasive Surgical Procedures
Nitinol shape memory alloys play a crucial role in advancing minimally invasive surgical procedures by enabling the development of intricate and flexible medical devices. From guidewires to stents, these SMAs provide the flexibility and resilience required to navigate intricate anatomical structures, ultimately improving patient outcomes and reducing recovery times.
Improving Patient Care through Nitinol-enabled Medical Devices
Nitinol has revolutionized the medical device industry. This remarkable alloy's unique properties have enabled the development of a new generation of medical devices that deliver superior patient care.
Nitinol-based medical devices offer several key advantages:
- Enhanced precision: Nitinol's shape memory and superelasticity allow for devices that can be precisely deployed and adjusted, minimizing invasiveness.
- Improved durability: The material's exceptional strength and resistance to fatigue ensure long-lasting performance and reliability.
- Optimal patient outcomes: Nitinol devices combine precision and durability to contribute to better clinical results and enhanced patient satisfaction.
From minimally invasive catheters to complex neurovascular implants, nitinol is at the forefront of medical innovation.
Future Prospects and Innovations in Nitinol Applications
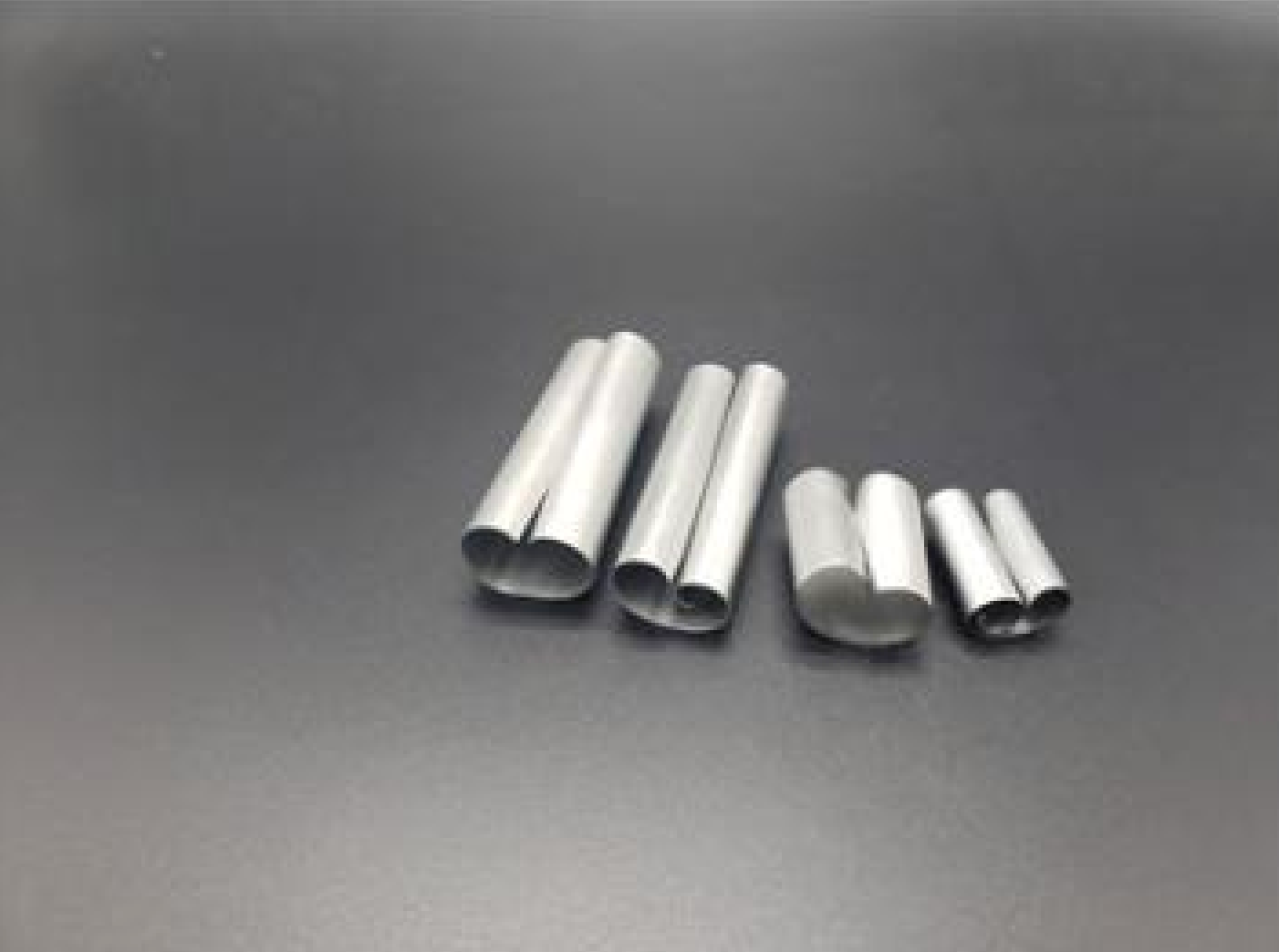
GEE SMA continues to spearhead groundbreaking research and development in Nitinol technology, aiming to push the boundaries of what's possible with shape memory alloys. Our team is dedicated to exploring new frontiers with Nitinol functional materials, seeking innovative ways to leverage its unique properties for various applications. As we look ahead, we anticipate exciting breakthroughs in Nitinol shape memory applications that will revolutionize industries and propel material engineering into the future.
GEE SMA's Ongoing Research and Development in Nitinol Technology
Our ongoing commitment to advancing Nitinol technology is evident through our extensive research initiatives, which aim to uncover new possibilities for this remarkable material. Focusing on enhancing its superelasticity and shape memory capabilities, we are continually refining our understanding of Nitinol alloys to unlock their full potential across various sectors. Through rigorous testing and experimentation, we are paving the way for next-generation applications that harness the power of Nitinol in unprecedented ways.
Exploring New Frontiers with Nitinol Functional Materials
At GEE SMA, we are venturing into uncharted territory by exploring using Nitinol functional materials in novel applications that transcend traditional uses. From adaptive structures to smart actuators, our team is at the forefront of redefining how Nitinol can be integrated into cutting-edge technologies that demand exceptional performance and reliability. By pushing the boundaries of what's achievable with this versatile material, we are poised to revolutionize industries across the board.
Anticipated Breakthroughs in Nitinol Shape Memory Applications
As we look toward the future, we foresee remarkable breakthroughs in Nitinol shape memory applications that will reshape entire industries. From advanced medical devices that adapt seamlessly to patient needs to aerospace components that respond dynamically to changing conditions, the potential for leveraging Nitinol's shape memory properties is limitless. With ongoing advancements in material science and engineering, GEE SMA is primed to take charge of realizing these anticipated breakthroughs.
Embrace the Future of Materials Engineering with Nitinol Technology
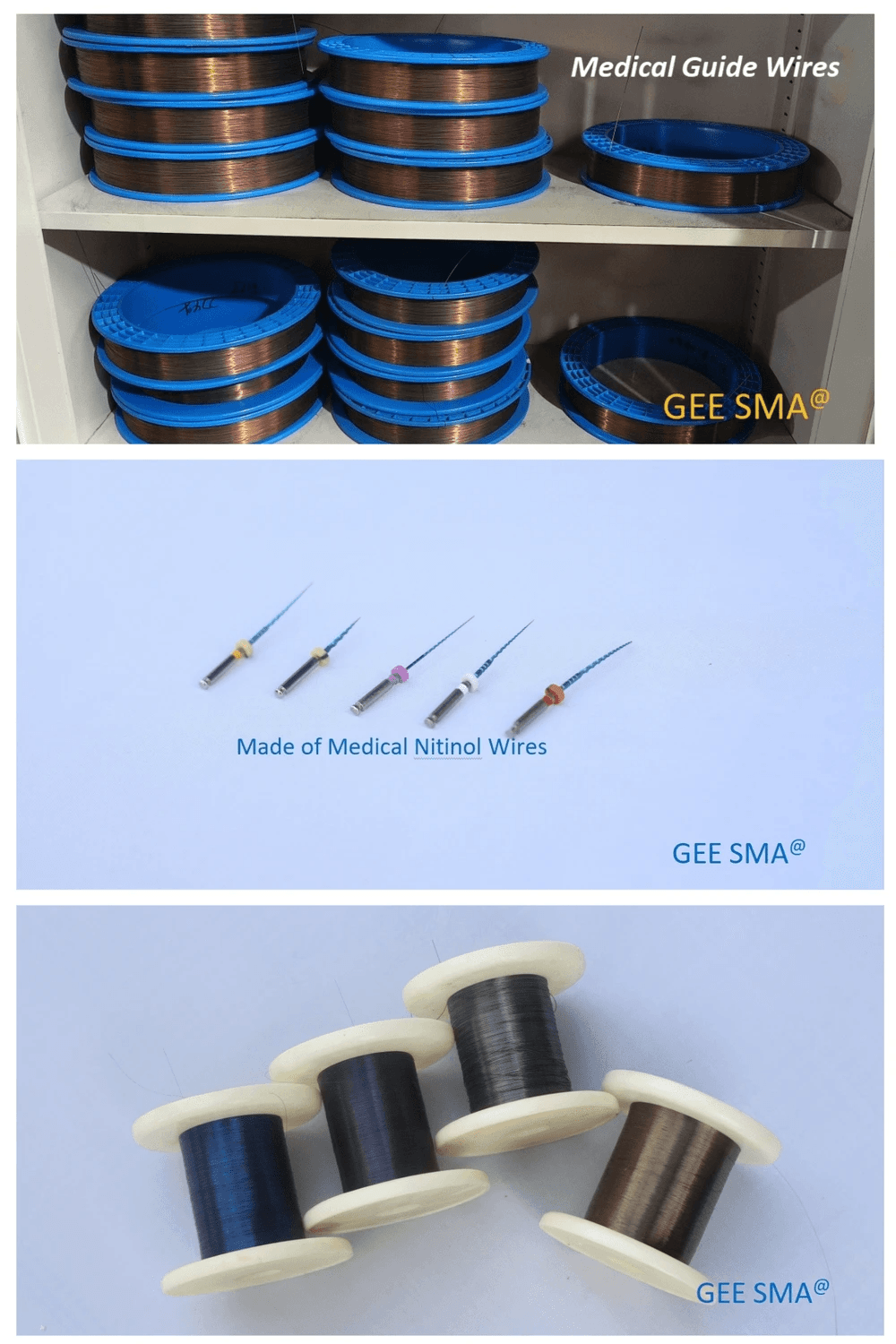
Nitinol shape memory alloys have revolutionized various industries, offering endless possibilities for innovation and advancement. With superelastic nitinol tubes, shape memory alloys, and nitinol wire at our disposal, the potential for enhanced product performance is limitless. Embracing the future of materials engineering with nitinol technology will undoubtedly lead to groundbreaking developments and transformative solutions.
Unlocking Endless Possibilities with Nitinol Shape Memory Alloys
The remarkable properties of superelastic nitinol tubes and shape memory alloys have unlocked a world of possibilities in engineering and manufacturing. From biomedical devices to aerospace applications, the versatility of nitinol has paved the way for cutting-edge advancements that were once unimaginable.
The unique combination of flexibility and shape memory in nitinol alloys has revolutionized the design and performance of various products. Nitinol's ability to return to its original shape after deformation makes it an ideal material for creating self-expanding stents used in medical procedures. Additionally, its superelasticity allows for developing durable and resilient components for aerospace engineering, enabling safer and more efficient aircraft designs.
Leveraging Nitinol Alloys for Enhanced Product Performance
By using nitinol alloys, industries can also improve the durability and longevity of their products. Nitinol's high fatigue and corrosion resistance make it an ideal choice for applications that require long-term reliability, such as medical devices, aerospace components, and automotive parts. This increased durability enhances product performance and reduces maintenance costs and downtime, providing a competitive edge in the market.
As we embrace the future of materials engineering, it's clear that nitinol technology will continue to play a pivotal role in driving innovation forward. With ongoing research and development in nitinol applications, we can anticipate groundbreaking breakthroughs that will redefine the boundaries of what is possible in materials science. One area where nitinol technology is poised to impact significantly is the medical field, where its unique properties make it ideal for use in minimally invasive surgical procedures. The flexibility and shape memory of nitinol allows for innovative medical devices that can adapt to the body's natural contours, leading to improved patient outcomes and recovery times.