Introduction
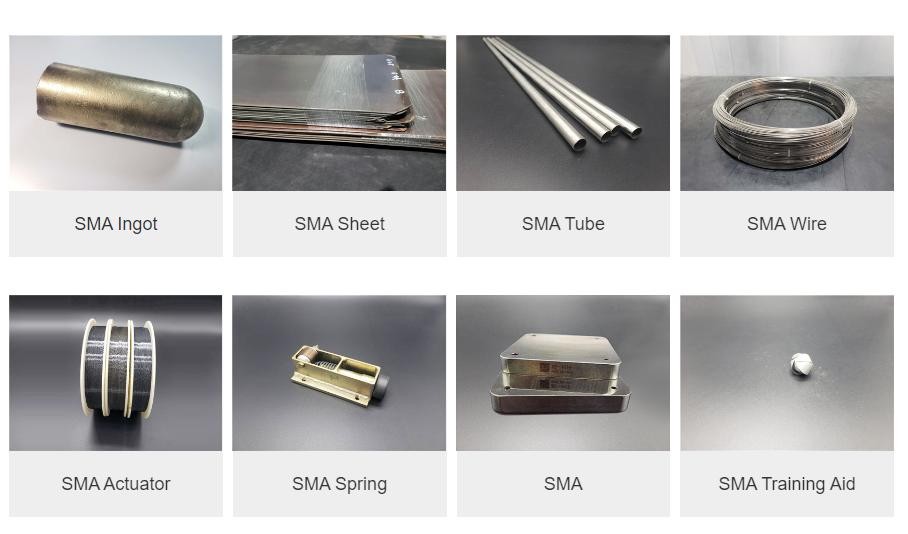
Regarding innovative materials, Nitinol 60 is a game-changer in various industries. This unique alloy, comprised of nickel and titanium, possesses exceptional mechanical and physical properties that make it highly sought after for various applications. From medical devices to aerospace components, Tensile Nitinol 60's versatility makes it a top choice for crafting high-quality materials and components.
What is Nitinol 60?
Nitinol 60 is a nickel-titanium alloy renowned for its remarkable shape memory and superelasticity. Because it can return to its original shape after being deformed, this material has revolutionized the design and functionality of numerous products across different sectors.
Applications of Tensile Nitinol 60
Tensile Nitinol 60's applications are diverse and far-reaching. This versatile material is crucial in enhancing performance and reliability, from intricate medical devices such as stents and guidewires to critical aerospace components like actuators and springs.
The Mechanical and Physical Properties of Nitinol-60
The mechanical and physical properties of Nitinol-60 are truly impressive. Its corrosion, fatigue, and wear resistance make it ideal for demanding environments where durability is paramount.
Understanding Nitinol 60
Nitinol 60, or Tensile Nitinol 60, is a unique alloy of nickel and titanium. This remarkable material exhibits shape memory and superelasticity, making it highly sought after in various industries for its exceptional mechanical and physical properties.
Definition and Composition
Nitinol 60 is a nickel-titanium alloy containing approximately 60% nickel. This composition allows it to return to its original shape after deformation, making it ideal for applications requiring precise and controlled movement. The unique combination of these two metals gives Nitinol 60 its distinctive properties, setting it apart from other materials.
History and Development
The history of Nitinol dates back to the early 1960s when researchers at the Naval Ordnance Laboratory discovered its unique properties by accident. Since then, extensive research and development have led to the widespread use of Nitinol in various fields, such as medicine, aerospace, and consumer goods. Its versatility has made it an indispensable material in modern manufacturing.
Since its accidental discovery, Nitinol has become a go-to material for various industries due to its unique shape memory and superelasticity. In medicine, Nitinol is used in stents, guide wires, and orthodontic wires due to its ability to return to its original shape after deformation. In aerospace, Nitinol is used in actuators and landing gear components for its lightweight and durable properties. Additionally, consumer goods such as eyeglass frames and mobile phone antennas also benefit from the flexibility and resilience of Nitinol.
Advantages and Limitations
One of the key advantages of Nitinol 60 is its ability to exhibit shape memory and superelasticity at different temperatures, allowing for a wide range of applications across diverse industries. However, limitations include potential challenges in processing due to its unique properties, requiring specialized techniques for manufacturing high-quality components.
One drawback of Nitinol 60 is its relatively high cost compared to other materials, which may limit its widespread use in certain industries. Additionally, the complex manufacturing process and specialized equipment required for working with Nitinol 60 can pose logistical and financial challenges for companies seeking to incorporate this alloy into their products. Despite these limitations, the unique properties of Nitinol 60 make it an attractive option for applications where shape memory and superelasticity are essential, such as in medical devices and aerospace components.
Tensile Nitinol 60 for Multiple Products
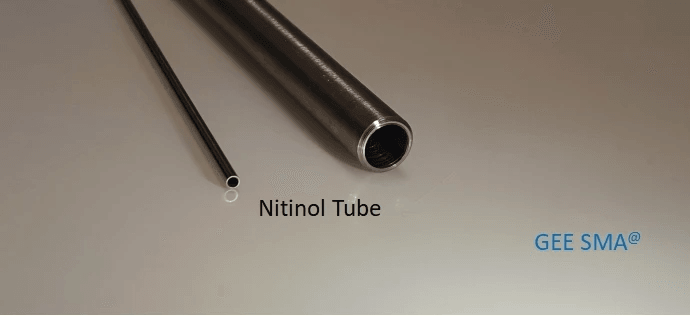
Tensile Nitinol 60 is a versatile material with applications in various industries, including medical devices, aerospace components, and consumer goods. Due to its biocompatibility and shape memory properties, nitinol 60 is used to create stents, guidewires, and other implantable devices in the medical field. In aerospace, it is utilized for lightweight and durable components such as actuators and landing gear. Additionally, consumer goods like eyeglass frames and watch springs benefit from the unique mechanical and physical properties of nitinol-60.
Medical Devices
Tensile Nitinol 60 in medical devices has revolutionized the industry by providing innovative solutions for minimally invasive procedures. Its superelasticity allows easy insertion into the body while retaining its original shape once deployed. This makes it an ideal material for stents that need to expand and contract within blood vessels without causing damage or discomfort to the patient.
Aerospace Components
Nitinol 60 is a valuable material in the aerospace industry due to its exceptional mechanical properties.
- High strength-to-weight ratio: Enables lighter aircraft structures for improved fuel efficiency.
- Excellent fatigue and wear resistance: Ensures the reliability of critical components in demanding environments.
- Suitability for critical components: Ideal for actuators in aircraft wings and landing gear assemblies.
Engineers can enhance performance and safety by incorporating Nitinol 60 into aircraft design.
Consumer Goods
Consumer goods also benefit from Tensile Nitinol 60's unique properties. Eyeglass frames made from this material offer flexibility and durability, reducing the risk of breakage while providing a comfortable fit for users. Similarly, watch springs crafted from nitinol-60 exhibit excellent fatigue resistance, ensuring long-lasting timepiece performance.
By understanding the diverse applications of Tensile Nitinol 60 in medical devices, aerospace components, and consumer goods, it's evident that this material plays a pivotal role in driving innovation across multiple industries while offering superior mechanical and physical properties essential for advanced product development.
Mechanical and Physical Properties of Nitinol-60
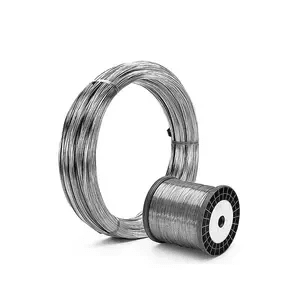
Shape Memory and Superelasticity
One of the most remarkable features of nitinol 60 is its shape memory and superelasticity. This means the material can be deformed at low temperatures and will return to its original shape when heated, making it ideal for applications requiring precise control over shape.
Corrosion Resistance
Nitinol 60 offers exceptional corrosion resistance, making it a reliable choice for products exposed to harsh environments or corrosive substances. This property ensures the longevity and durability of components made from this material, reducing maintenance needs and costs.
Fatigue and Wear Resistance
With its high fatigue and wear resistance, nitinol 60 can withstand repeated stress without experiencing permanent deformation or failure. This makes it suitable for use in products that undergo constant movement or mechanical stress, ensuring longevity and reliability.
Crafting High-Quality Materials and Components
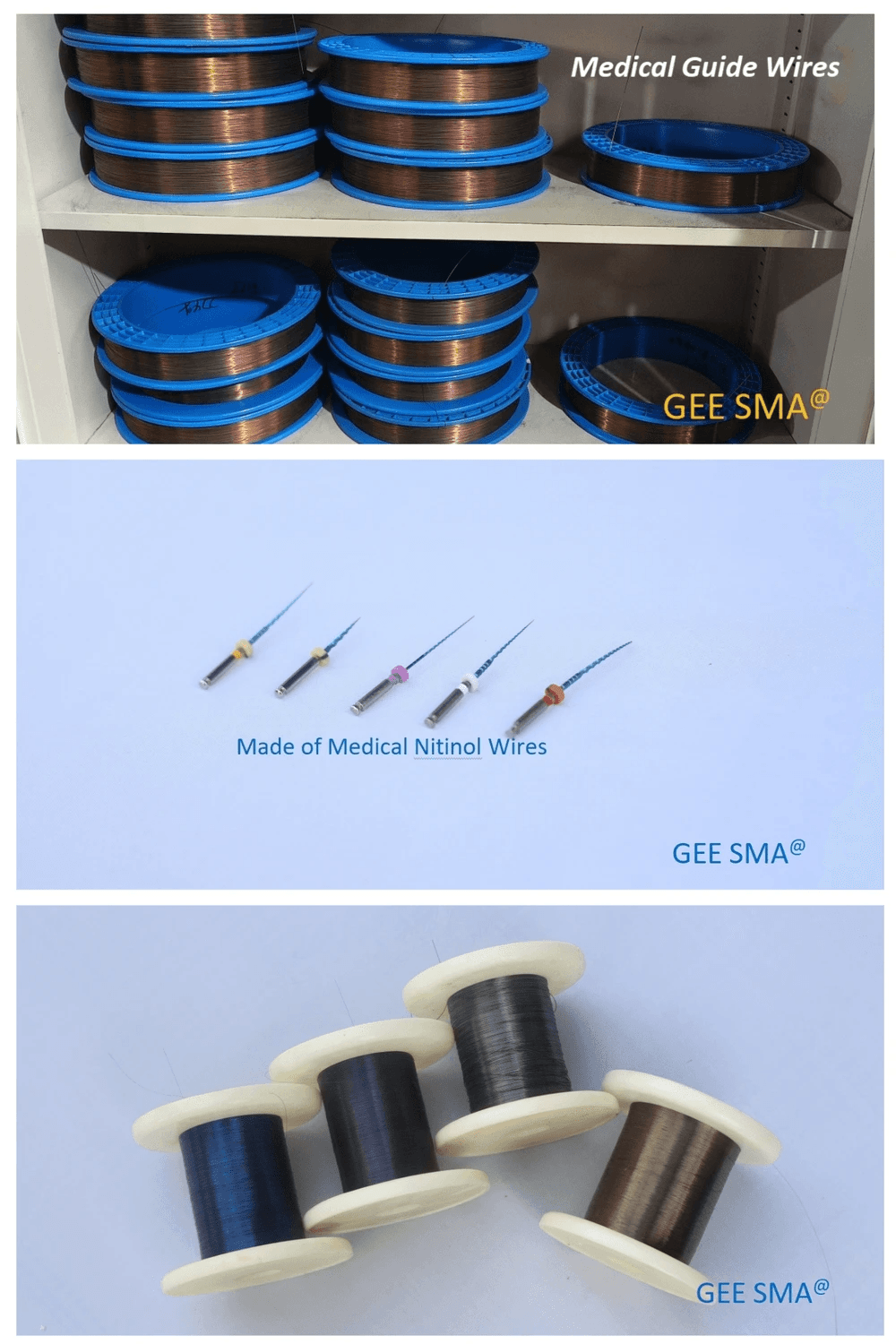
GEE SMA is a leading manufacturer of Nitinol 60. It utilizes state-of-the-art technology and precision engineering to produce high-quality materials and components. With a focus on innovation and expertise, GEE SMA ensures that every product meets the highest industry standards of excellence.
GEE SMA's Approach to Manufacturing Nitinol 60
GEE SMA's approach to manufacturing Nitinol 60 involves a meticulous process that begins with sourcing the finest raw materials and continues through advanced manufacturing techniques. The company's commitment to quality and reliability ensures that each product is crafted with precision and expertise, meeting the diverse needs of various industries.
In addition to the rigorous manufacturing process, GEE SMA utilizes state-of-the-art testing and inspection equipment to ensure that each Nitinol 60 product meets the highest quality standards. This commitment to thorough quality control guarantees that customers receive reliable and consistent products that perform as expected in their specific applications. GEE SMA demonstrates its dedication to delivering superior Nitinol 60 products that exceed industry expectations by adhering to strict quality control protocols.
Quality Control Measures
Quality control is paramount at GEE SMA, with stringent measures in place to guarantee that the mechanical and physical properties of Nitinol-60 meet or exceed industry standards. From rigorous testing protocols to comprehensive inspection procedures, every step is taken to ensure that only the highest-quality materials and components are delivered to customers.
Customization Options for Specific Applications
Recognizing the unique requirements of different industries, GEE SMA offers customization options for specific applications of Tensile Nitinol 60. Whether it's medical devices, aerospace components, or consumer goods, the company works closely with clients to tailor materials and components to their specifications, ensuring optimal performance and functionality.
In addition to customizing materials and components, GEE SMA offers comprehensive testing and validation services to ensure that the tailored products meet industry standards and regulations. By working closely with clients throughout the process, the company can address any specific challenges or requirements, resulting in a final product exceeding expectations. This collaborative approach ensures optimal performance and functionality and fosters long-term partnerships built on trust and mutual success.
Meeting Unique Customer Needs
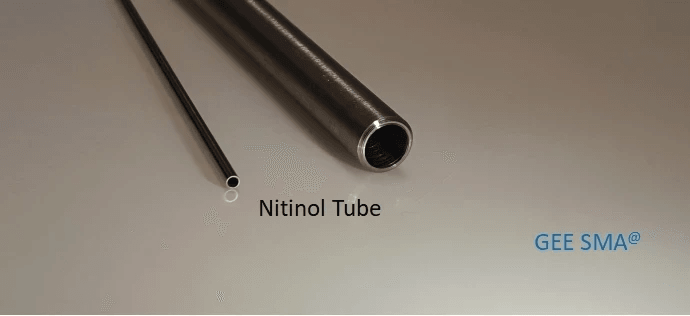
As the demand for innovative materials like Nitinol 60 continues to grow, GEE SMA prioritizes collaborative product development to meet our customers' specific requirements. By working closely with clients, we can tailor the properties of Tensile Nitinol 60 to suit their unique applications, ultimately leading to more effective and efficient end products.
Collaborative Product Development
Our team at GEE SMA understands the importance of collaboration when developing high-quality materials and components. By involving our clients in product development, we can gain valuable insights into their needs and preferences, allowing us to create customized solutions that meet or exceed their expectations.
By working closely with our clients, we can ensure that the materials and components we develop are perfectly tailored to their specific needs. This collaborative approach allows us to address potential issues or concerns early in development, ultimately saving time and resources. We aim to create functional materials that meet and exceed our client's expectations, and collaboration is key to achieving this.
Tailoring Nitinol Functional Materials
With a deep understanding of Nitinol-60's mechanical and physical properties, we have the expertise to tailor its functional materials according to specific requirements. Whether it's adjusting shape memory characteristics for medical devices or enhancing fatigue resistance for aerospace components, we can customize Tensile Nitinol 60 for a wide range of applications.
With our in-depth knowledge of Nitinol-60, we can modify its superelasticity to meet the requirements of various industrial applications. Whether designing components for robotics or creating specialized tools for the automotive industry, our tailored Tensile Nitinol 60 can provide the necessary flexibility and resilience. By understanding our customers' specific needs, we can customize the material to deliver optimal performance in a wide range of dynamic environments.
Swift Response to Customer Requirements
GEE SMA is a leading provider of high-quality Nitinol 60 products, renowned for our exceptional customer service and responsiveness.
Our commitment to meeting customer needs is evident in our:
- Agile approach: Quickly adapting to changing requirements.
- Collaborative product development: Working closely with clients to create tailored solutions.
- Swift response times: Delivering efficient and timely service.
By offering these key advantages, GEE SMA is a trusted partner for businesses seeking top-tier Nitinol 60 solutions.
The Future of Mechanical and Physical Properties of Nitinol-60
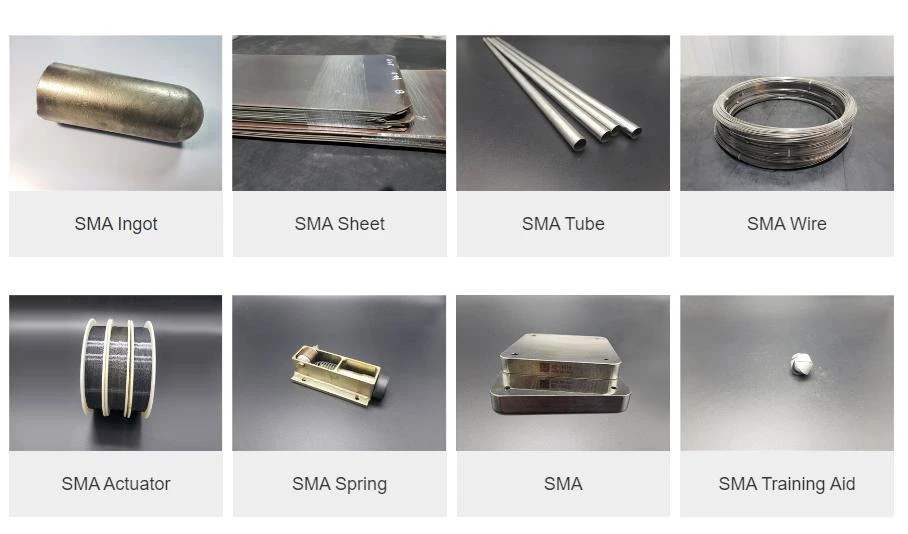
Thanks to its versatility and unique properties, Nitinol 60 has truly revolutionized various industries. Its applications are endless, from medical devices to aerospace components, making it a game-changer in the materials industry. With its impressive mechanical and physical properties, the future of Nitinol-60 looks promising for even more innovative advancements.
The Versatility of Nitinol 60 in Various Industries
Nitinol 60 is a remarkable material known for its exceptional adaptability and performance. Its unique properties make it a valuable asset across various industries.
Nitinol 60 excels in numerous applications due to its:
- Shape memory effect: allowing for self-adjusting components
- Superelasticity: enabling flexibility and durability
- Corrosion resistance: ensuring long-lasting performance
These characteristics make Nitinol 60 a sought-after material for healthcare and aerospace industries, solidifying its position as a versatile and high-performance option.
Why Tensile Nitinol 60 is a Game-Changer
The introduction of tensile Nitinol 60 has truly disrupted traditional material options with its superior performance and reliability. Its remarkable mechanical and physical properties have set new standards for product development, making it an undeniable game-changer in the industry.
Tensile Nitinol 60 has revolutionized the industry by offering a unique combination of high strength, superelasticity, and shape memory properties. This allows for the creation of previously impossible or impractical products to manufacture using traditional materials. Additionally, its resistance to corrosion and fatigue makes it a highly durable and long-lasting option for a wide range of applications. As a result, Nitinol 60 has opened up new possibilities for product design and innovation, making it an essential material for forward-thinking companies.
As technology advances, so does the potential for further enhancements in the mechanical and physical properties of Nitinol-60. Ongoing research and development efforts are focused on improving the fatigue resistance and durability of Nitinol-60, making it even more suitable for demanding applications in aerospace, automotive, and medical devices. With these advancements, we can expect Nitinol-60 to become an even more versatile and reliable material for various engineering and manufacturing needs.