Introduction
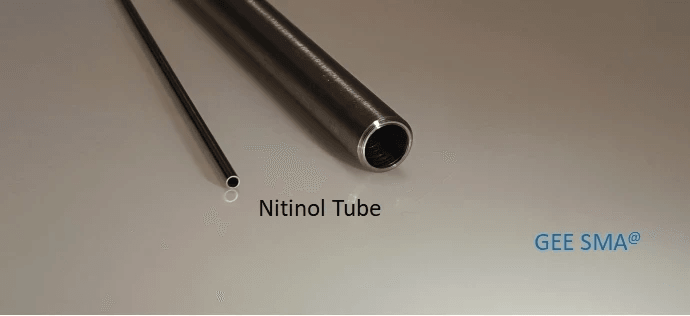
Nitinol, a unique alloy of nickel and titanium, is renowned for its extraordinary superelasticity and shape memory properties. Its remarkable mechanical properties make it popular in various industries, from medical devices to aerospace engineering. The versatility of nitinol material properties allows for tailored solutions to meet diverse needs.
Understanding the Superelasticity of Nitinol
Nitinol's superelasticity refers to its ability to undergo substantial deformation and return to its original shape when the external force is removed. This remarkable property makes it ideal for applications where flexibility and resilience are crucial, such as medical stents and braces.
Exploring Nitinol Mechanical Properties
Nitinol's mechanical properties are truly fascinating, as it exhibits high strength, excellent fatigue resistance, and biocompatibility. These characteristics make it a sought-after material for critical applications in healthcare, automotive engineering, and consumer electronics.
The Versatility of Nitinol Material Properties
The versatility of nitinol material properties is evident in its ability to be manufactured into various forms, including wires, tubes, sheets, and complex components with intricate shapes. This adaptability allows for creating innovative solutions across a wide range of industries.
The History of Nitinol
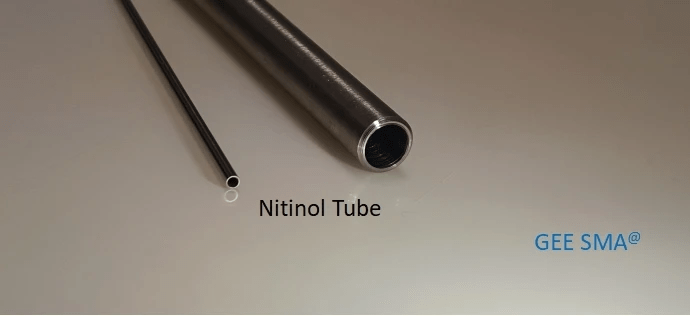
In the 1950s, researchers Buehler and Wang stumbled upon the remarkable superelasticity of nitinol, a nickel-titanium alloy. This discovery led to excitement in the scientific community, opening up a world of possibilities for innovative applications in various industries.
Nitinol's unique properties were quickly recognized by industrial pioneers, leading to its commercialization and widespread adoption in diverse applications such as medical devices, aerospace engineering, and consumer products. The material's ability to exhibit shape memory and superelasticity made it an attractive choice for engineers and designers looking to push what was possible.
Over the years, significant advancements have been made in nitinol wire properties, allowing for greater control over its mechanical behavior and performance. These developments have further expanded the range of applications for nitinol, making it an increasingly sought-after material for cutting-edge technologies.
Remember to keep using keywords like nitinol mechanical properties, nitinol properties, superelastic tube, nitinol material properties, nitinol material properties, and nitinol wire properties throughout your content!
Superelastic Nitinol Alloys
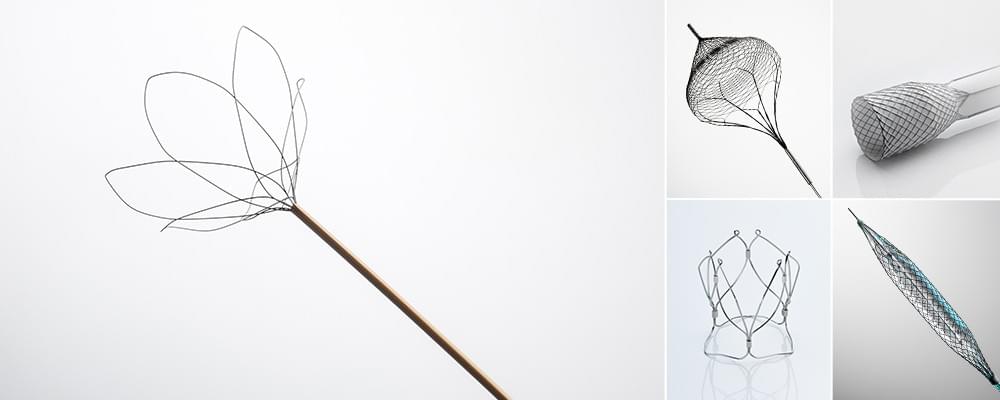
Characteristics and Composition
Nitinol alloys offer a unique blend of properties that make them invaluable in various applications. These alloys are composed of nickel and titanium, which exhibit remarkable superelasticity and shape memory capabilities, allowing them to deform significantly and return to their original shape.
Key characteristics of nitinol alloys include:
- Versatility: Their composition can be tailored to achieve specific material properties.
- Biocompatibility: Ideal for medical devices as they do not cause adverse reactions in the body.
- Superelasticity and Shape Memory: Enable remarkable flexibility and recovery.
These properties make nitinol alloys indispensable in the medical field, where they are used in stents, guidewires, and orthodontic appliances.
Applications in Medical Devices
Nitinol's superelasticity and biocompatibility make it ideal for medical devices such as stents, guidewires, and orthodontic wires. Its ability to withstand repeated bending without permanent deformation is crucial in these applications, ensuring reliable performance within the human body. Nitinol's unique properties also make it suitable for minimally invasive surgical procedures, contributing to advancements in medical technology.
Nitinol Superelastic Tube Advantages
Due to their exceptional mechanical properties, nitinol superelastic tubes offer several advantages in engineering applications. These tubes can undergo large deformations while maintaining high recoverable strains, making them ideal for actuators, sensors, and other precision devices. The combination of strength and flexibility in nitinol tubes provides designers with a versatile material tailored to meet specific performance requirements.
Nitinol superelastic tubes are also highly corrosion resistant, making them suitable for harsh environments where other materials may degrade over time. This corrosion resistance adds to the longevity and durability of nitinol tubes, making them a cost-effective choice for engineering applications. Additionally, the biocompatibility of nitinol makes it an excellent option for medical devices and implants, further expanding its potential uses across different industries.
With its remarkable superelasticity and shape memory capabilities, nitinol continues revolutionizing various industries by offering unparalleled mechanical properties that cater to diverse needs.
GEE SMA's Role in Nitinol Production
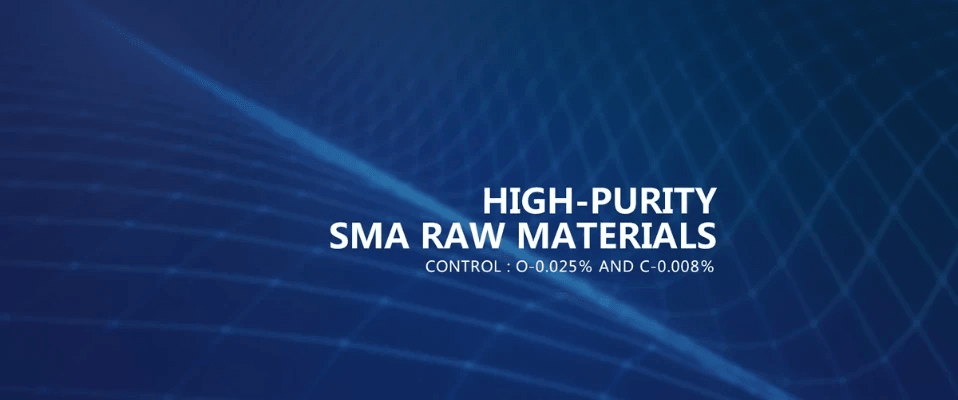
GEE Shape Memory Alloys (SMA) are crucial in producing Nitinol and crafting high-quality materials exhibiting exceptional mechanical properties. Focusing on tailoring nitinol components to meet specific requirements, GEE SMA ensures that the superelastic tube and nitinol wire properties are optimized for various applications. By addressing customer needs and delivering customized solutions, GEE SMA stands out as a leader in producing Nitinol materials.
Crafting High-Quality Materials
GEE SMA is dedicated to crafting high-quality Nitinol materials with superior nitinol properties. Through precise manufacturing processes and stringent quality control measures, GEE SMA ensures that nitinol's mechanical properties meet the highest standards. This commitment to excellence results in Nitinol materials exhibiting remarkable superelasticity and shape memory characteristics, making them ideal for various industries and applications.
Furthermore, GEE SMA prides itself on its ability to tailor Nitinol components to meet the specific needs of each industry and application. By working closely with clients to understand their unique requirements, GEE SMA can create customized Nitinol materials that deliver optimal performance and reliability. This personalized approach sets GEE SMA apart from other manufacturers, as the company is dedicated to providing tailored solutions that exceed expectations.
Tailoring Nitinol Components
At GEE SMA, the focus is on tailoring nitinol components to suit specific requirements and applications. Whether it's shaping Nitinol wires for medical devices or producing superelastic tubes for industrial use, GEE SMA leverages its expertise to customize Nitinol materials according to precise specifications. This tailored approach ensures that the unique material properties of Nitinol are optimized for each application, leading to enhanced performance and reliability.
Moreover, GEE SMA's team of skilled engineers and technicians is dedicated to collaborating closely with customers to understand their specific needs and challenges. By working in partnership with clients, GEE SMA ensures that the tailored Nitinol components not only meet technical requirements but also align with the overall goals and objectives of the project. This customer-centric approach fosters trust and transparency, ultimately leading to successful outcomes for all parties involved.
Addressing Customer Requirements
GEE SMA emphasizes understanding and addressing customer requirements regarding Nitinol production. By collaborating closely with clients, GEE SMA can develop tailored solutions that align with specific project needs and objectives. Whether fine-tuning Nitinol's mechanical properties or customizing material dimensions, GEE SMA's customer-centric approach ensures that every aspect of the production process is geared towards delivering optimal results for its clients.
Furthermore, GEE SMA's dedication to meeting customer requirements extends to testing and analyzing Nitinol's mechanical properties. Through rigorous quality control measures and advanced testing equipment, the company ensures that the Nitinol produced meets the specifications the client outlined. This commitment to precision and accuracy is a testament to GEE SMA's unwavering focus on delivering top-notch customer results.
Testing and Analyzing Nitinol Mechanical Properties
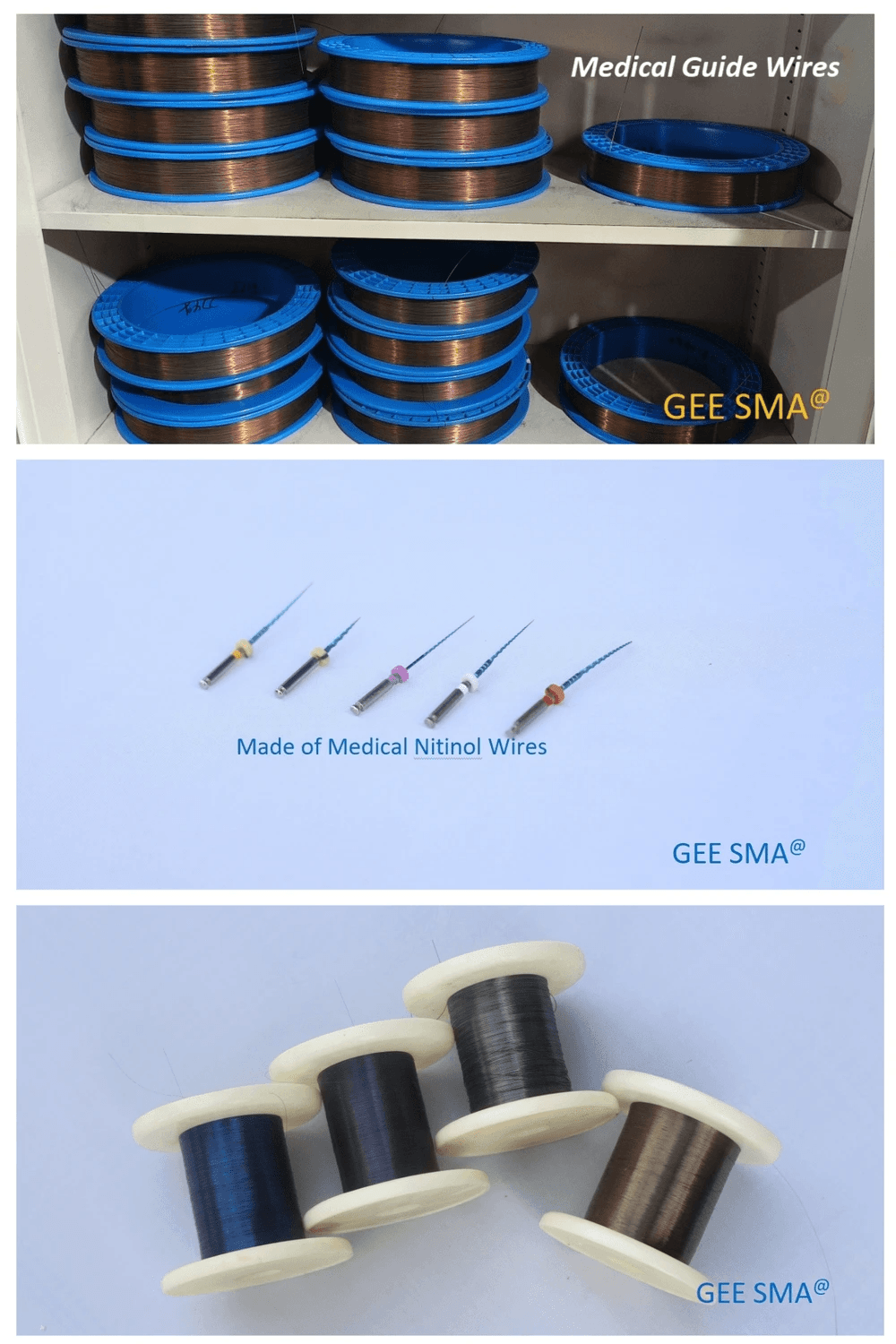
Mechanical Testing Methods
Understanding nitinol's mechanical properties is essential for its effective application. Several testing methods are employed to characterize this unique material.
- Tensile, compression, and bending tests: These standard tests evaluate nitinol's strength, elasticity, and flexibility.
- Fatigue testing: assesses the material's resistance to repeated loading and unloading, which is crucial for medical and aerospace applications.
- Torsion testing: determines nitinol's behavior under twisting forces, which is valuable for automotive and robotics components.
By combining these testing methods, engineers and researchers can comprehensively understand nitinol's mechanical behavior and optimize its use in various industries.
Understanding Stress and Strain
Stress and strain play a crucial role in analyzing nitinol properties. By subjecting the material to controlled loads and measuring its response, engineers can gain valuable insights into how nitinol behaves under different levels of stress and strain. This data is essential for designing components with specific performance requirements.
Stress and strain testing also allows engineers to identify potential weaknesses in nitinol materials, helping refine the manufacturing process and improve product quality. By understanding how stress and strain impact the material's behavior, engineers can make informed decisions about the best methods for shaping and treating nitinol to achieve desired performance characteristics. This knowledge is crucial for ensuring that nitinol components meet the rigorous demands of various applications, from medical devices to aerospace technology.
Nitinol Material Performance Metrics
A range of metrics are used to assess factors such as fatigue resistance, shape memory behavior, and superelasticity to quantify the performance of nitinol materials. These metrics provide valuable information for engineers looking to optimize the use of nitinol in various applications. Understanding the fatigue resistance of nitinol is crucial for applications where the material will undergo repeated stress cycles, such as in medical stents or orthodontic wires. Shape memory behavior is another key metric, allowing nitinol to return to its original shape after being deformed, making it ideal for minimally invasive medical procedures and other innovative applications.
By carefully analyzing the mechanical properties of nitinol through various testing methods, researchers and engineers can unlock new possibilities for this remarkable material in fields such as aerospace, medical devices, and consumer products.
Innovations and Future Applications
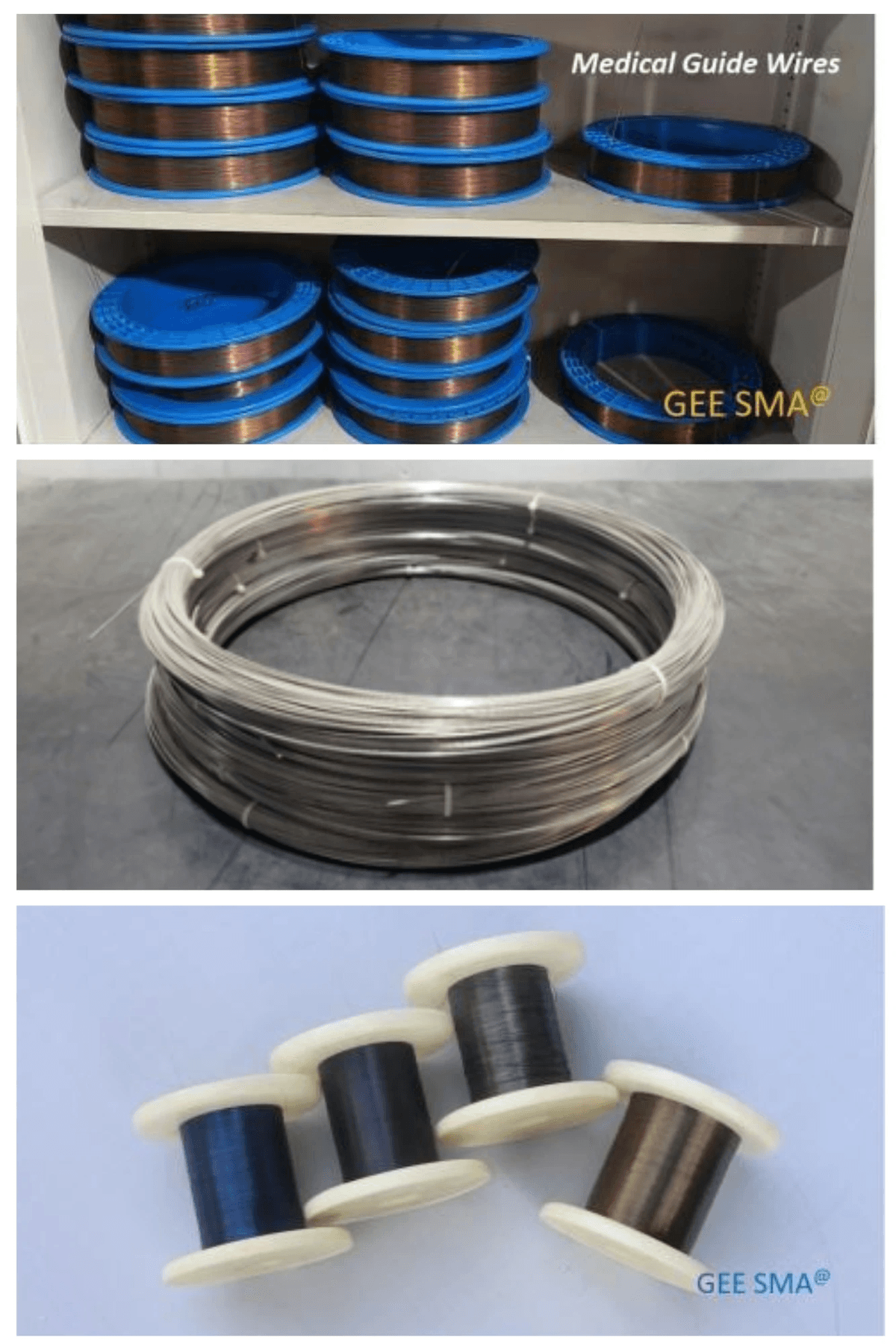
Emerging Technologies
In materials science, emerging technologies constantly push the boundaries of what's possible with Nitinol. From advancements in manufacturing processes to innovative applications in aerospace and automotive industries, Nitinol's unique superelastic and shape memory properties continue to inspire breakthroughs.
Potential for Shape Memory Alloys
The potential for shape memory alloys like Nitinol is truly remarkable. With the ability to remember their original shape and return to it when heated, these alloys can revolutionize fields such as robotics, smart materials, and consumer electronics. The adaptability of Nitinol's properties makes it an exciting prospect for future technological developments.
Nitinol's Role in Biomedical Engineering
Nitinol is a remarkable material with unique properties, making it exceptionally well-suited for biomedical engineering. Its ability to transform between shapes based on temperature has led to groundbreaking applications in various medical devices.
- Stents: Nitinol stents can expand and contract within the body, providing critical support for blood vessels and airways.
- Orthodontic wires: Gentle, continuous force is applied to teeth using Nitinol wires, correcting misalignment effectively.
- Biocompatibility and durability: Nitinol's compatibility with the human body and its resistance to wear makes it an ideal choice for long-term implants.
By harnessing the potential of Nitinol through continued research and development, we can anticipate even more innovative medical solutions in the future. This versatile material is undoubtedly a cornerstone of modern biomedical engineering.
Leverage Nitinol for Innovative Solutions
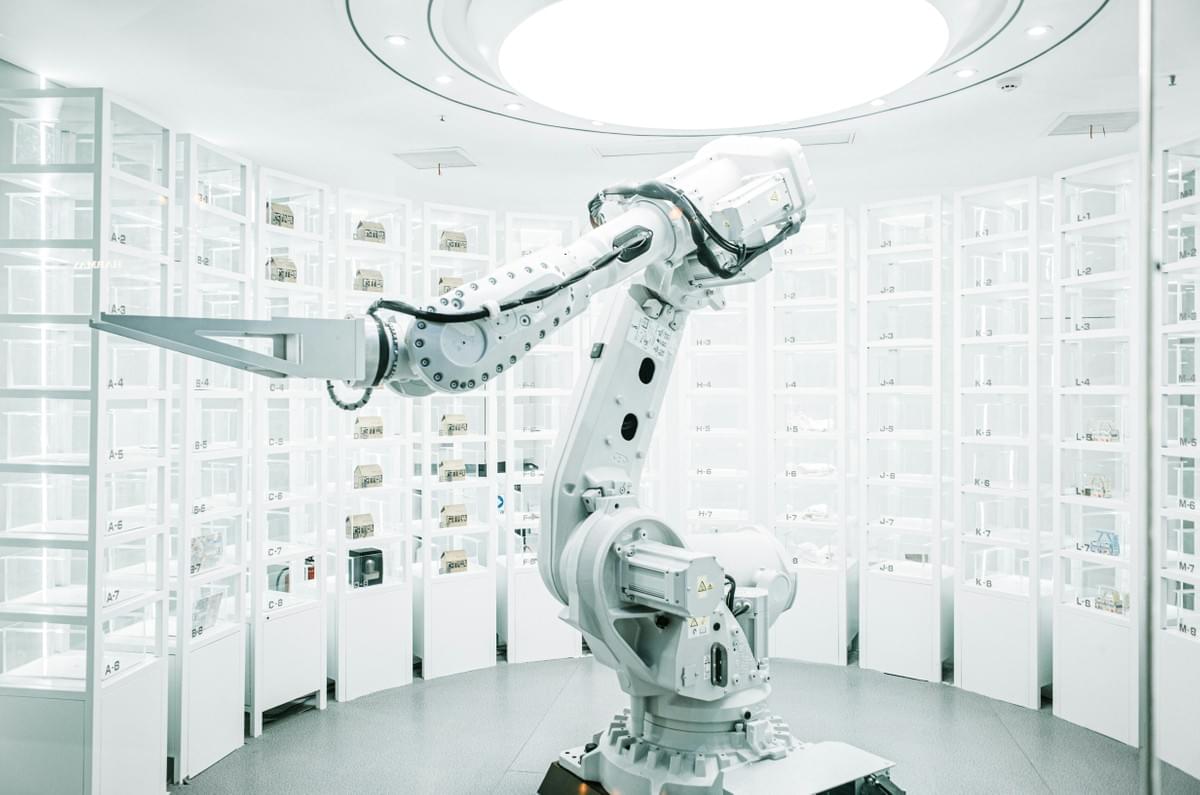
Nitinol's remarkable superelasticity and unique mechanical properties make it an ideal material for innovative solutions in various industries. From aerospace to medical devices, the versatility of nitinol properties allows for groundbreaking advancements and cutting-edge technologies.
Harnessing Nitinol's Superelastic Properties
The superelastic tube made from nitinol is a game-changer in medicine, offering unparalleled flexibility and resilience. Its ability to return to its original shape after deformation makes it invaluable in minimally invasive surgical procedures, leading to improved patient outcomes and faster recovery times.
Nitinol's superelastic properties make it a versatile material that can be adapted to meet diverse medical needs. Whether used in stents, guidewires, or other medical devices, nitinol's unique flexibility and resilience allow precise navigation through the body's intricate pathways. This adaptability is crucial in addressing the specific requirements of different surgical procedures, ultimately contributing to more successful patient outcomes.
Adapting Nitinol Material Properties for Diverse Needs
As industries continue to evolve, the adaptability of nitinol material properties proves crucial in meeting diverse needs. Whether crafting intricate components for automotive applications or developing advanced orthodontic devices, nitinol's unique characteristics empower engineers and designers to push the boundaries of what's possible.
Furthermore, nitinol's shape memory and superelasticity properties make it an ideal material for various applications, from medical devices to aerospace components. Its ability to return to its original shape after deformation and withstand high levels of strain without permanent damage makes it a versatile option for industries looking to innovate and improve performance. This adaptability ensures that nitinol will continue to play a pivotal role in driving technological advancements in the years to come.
With its rich history, unparalleled characteristics, and endless possibilities for innovation, nitinol continues to be at the forefront of material science, driving progress across multiple industries. As we look towards the future, the potential for further advancements and applications using this remarkable alloy is truly limitless.